Гипермир » Антикоррозийная обработка автомобиля
Антикоррозийное покрытие используется для защиты поверхностей автомобиля от разъедания ржавчиной. Оно продлевает сохранность металла и внешнего вида автомобиля. Процедуру обработки следует делать хотя бы раз в 3 года.
Какие существуют виды обработки.
Есть два вида средств, используемых для этой цели. Выбор их зависит от места нанесения покрытия. Битумной мастикой, изготовленной из синтетических смол, пользуются для защиты металла от ударов и других повреждений. Антикоррозийными средствами являются также материалы, основой которых являются каучук и ПВХ. Они более долговечны, но применяют их в основном на машиностроительных заводах.
Внутренние поверхности автомобиля обрабатываются антикоррозийными составами, которые изготовлены на масляной основе, а также на основе воска. После обработки такими средствами остается тонкая пленка, которая защищает от попадания влаги и коррозии.
Выбор материалов и средств для антикоррозийной обработки автомобиля.
Для покрытия днища берется выбранное антикоррозийное средство, добавляется пушечная смазка (сто граммов на один литр средства) и пластилин (одна упаковка на пять литров), все перемешивается и нагревается на водяной бане.

Для обработки внутренних плоскостей кузова используются баллончики с антикоррозийным препаратом.
В салоне машины средство наносится только на пол из – за большей уязвимости к коррозии. Перед покраской машины обязательно нужно обработать антикоррозийной смесью всю ее поверхность хотя бы в один слой.
Переодически подвергая автомобиль такой обработке, авто прослужит вам несколько десятилетий.
В магазине Гипермир вы можете купить средства от коррозии.
Антикоррозионное покрытие
RUST STOP – средство, предназначенное для борьбы с коррозией. Антикор выпускает компания «A.M.T. Inc.» (Канада).
Область применения
«РАСТ СТОП» используется во многих сферах, к основным можно отнести следующие:
- Защита днища транспорта и кузова.
- Покрытие внутренней и внешней части резервуаров, предназначенных для хранения нефтепродуктов.
- Формирование слоя на трубопроводах и контейнерах.
- Защита мостов, градирен и насосов от коррозии.
- Защита конструкций из стали, оборудования и железнодорожных путей.
- Формирование вторичной оболочки на поверхностях из стали и бетона.
- Предотвращение абразивного разрушения. Можно использовать на путепроводах и воронках, а также на коленчатых патрубках и трубах.
- Покрытие кровли из бетона, стали и дерева. Антикор можно наносить как на несущую поверхность, так и на изоляцию.
Преимущества
Существует несколько продуктов, которые выпускают под маркой «РАСТ СТОП». Одни предназначены специально для обработки труднодоступных мест. Если сравнивать с обычными адгезионными средствами, оно всегда полужидкое, не затвердевает. Кроме того, отличается следующими достоинствами:
- Заполняет даже мельчайшие дефекты. Запечатывает небольшие трещины и сглаживает царапины.
- Не оказывает негативного воздействия на детали, выполненные из масло- и бензостойкой резины.
В продаже также есть продукция, предназначенная для днища транспорта. В обычном состоянии имеет гелеобразный вид, а при воздействии на поверхность переходит в текучее состояние. Обладает следующими преимуществами:
- Это свойство направлено на обеспечение самовосстановления. Антикор вытесняет влагу, проникая в кристаллическую решетку, при этом образуется полимолекулярный слой. Ингибиторы коррозии, из которых он состоит, подавляют коррозионный процесс.
- Если сравнивать антикоррозионный эффект от применения «РАСТ СТОП» с эффектом от воздействия мастик, то он не зависит от того, соблюдался ли режим полимеризации.
- Перед нанесением не нужно проводить подготовительные работы. Вам не придется тратить средства и время на стандартную очистку поверхности, ее обезжиривание и сушку.
- Материал безопасен для человека и окружающей среды.
Перечисленные выше преимущества позволяют максимально упростить процесс обработки, снизить трудозатраты.
Как наносить антикоррозийное покрытие
При работе нужно помнить о технике безопасности, вам понадобятся перчатки и другая индивидуальная защита. Следите за тем, чтобы при обработке машины средство не скапливалось на полу. Дело в том, что оно имеет масляную основу, поэтому вы можете поскользнуться.
Обрабатывайте машину в помещении, которое хорошо проветривается. Темпера воздуха должна быть не меньше +10 С. Нанося покрытие, не переворачивайте аэрозольный баллончик. Предохраняйте его от ударов.
Перед нанесением антикора на автомобиль сделайте следующее:
- Уберите все из багажника.
- Если собираетесь обрабатывать кузов, то поставьте машину на подъемник и снимите колеса.
- Снимите подкрылки, аналогично поступите с защитными щитками в арках. Уберите шумоизоляцию и утеплитель. Снимите щетки дворников.
- Осмотрите дренажные отверстия, они должны быть чистыми. Уделите внимание и кузову автомобиля, удалите пыль и грязь.
- Пласты ржавчины сковырните отверткой, вспучившуюся краску удалите.
- Помойте машину, капли воды тщательно вытрите. Скрытые полости нужно продуть сжатым воздухом. Высушите пороги.
- Сидения закройте накидками. На педали наденьте чехлы или обмотайте их полиэтиленом. Аналогично закройте тормозные диски, не забудьте про колодки. Следите, чтобы и на них не попал антикор.
Нанося его на труднодоступные места, используйте технологические отверстия, которые были сделаны на заводе. Лишних отверстий сверлить не нужно.
Нанесите антикоррозийку на открытую поверхность при помощи малярной кисти, но лучше всего использовать специальное оборудование. Используя аэрозоль в баллоне, периодически встряхивайте его.
Работая со скрытыми полостями, вводите насадку до упора. Аэрозоль следует распылять непрерывно, орошая так, чтобы после обработки выкапывалось от 3 до 5 капель.
Если капель нет, это указывает на то, что полость орошена недостаточно хорошо. В этом случае обработку необходимо повторить. С помощью специальной насадки вы нанесете материал на самые труднодоступные участки. На высыхание днища и кузова отведите 48 часов.
Свойства
«РАСТ СТОП» отличается тем, что не только защищает изделия из металла, но и останавливает уже начавшуюся коррозию. Он преобразует ржавчину и вытесняет ее. Обработав металл, вы гарантированно предотвратите появление сквозной ржавчины.
Покрытие имеет отличные изолирующие свойства. Сам препарат имеет приятный запах. При нанесении он не изменяет цвет.
Те машины, которые ранее были обработаны другими антикоррозийными материалами, могут быть без ограничений обработаны «Раст Стоп». Перед нанесением материала предварительная подготовка не требуется.
Антикор делать ли
Правильный вечный антикор — DRIVE2
Не раз уже писал, что зачастую здесь у меня сохранены интересные для меня «рецепты» и интересующие меня вещи. Данный пост был заимствован у sscdimon отсюда так что все попросы к нему.
На тему антикоррозийной обработки уже очень много сказано-пересказано и сломано копий о головы друг друга.

Ладно, шучу конечно. Наверняка вы тоже уже начитались множество статей, где люди варят адовые смеси из мастики-солярки-негрола-пушсала-отработки-пластилина-парафиновых свечек и крыльев златоглазок. Возможно они неплохи, но вот необходимость и эффективность каждого компонента, а главное долговечность, обычно остаются туманны. На вопрос «как оно через 10 лет» обычно отвечают что машина продана, а эффективность можно оценить только через 7-8 лет после обоработки. Это не говоря про вонизм и вред для здоровья. Я же расскажу вам про свой вариант антикоррозийной обработки своими руками, доказательством эффективности которого послужит четвёрка. Сейчас ей 28 лет, но нет ни одного пятнышка ржавчины. Не надо думать, что она хранится в гараже в сферическом вакууме, ей тоже неплохо достаётся и дождиков, и грязевых ванн. И гаража у неё нет, обычно она хранится на даче под открытым небом, а иногда на улице в Москве прямо среди хлоридов натрия, магния, кальция и чёрта лысого.
Вот так происходит самое бережное в мире хранение почти антикварного автомобиля. Фото в разгаре процесса.
Полный размер
Вот так происходит самое бережное в мире хранение почти антикварного автомобиля. Фото в разгаре процесса.
Антикор по этому рецепту был сделан ей более десяти лет назад, в 2004 году и ни разу не обновлялся. Затем эта технология неоднократно повторялась на огромном количестве разных машин с отличным результатом. Почему не отдать в антикор-центр? Я не жлоб, и человек не совсем бедный, но! Я пока ни разу не видел, чтобы кто-то, за любые вообще деньги, качественно антикорил чужую машину. Тем более, правильными препаратами.
Как обычно, сначала немного теории. Как гниёт машина? Очень просто — изнутри. Меня очень умиляют люди, усердно намазывающие по низу кузова мастику и антигравий, думая, что теперь-то двери и пороги уж точно не заржавеют. Если поцарапать краску до металла снаружи, ждать дырку надо лет десять. Но изнутри, например в пороге, достаточно всего одного маленького очага коррозии. Если он там появится, через 3 года у вас гарантирована сквозная дыра: раствор воды и реагентов быстро сделает своё дело. Если вы переварили те же пороги, то без обработки хватит их ровно на 2 года. По сравнению со внешней, развивающаяся внутри полостей коррозия почти всегда более обширна. К моменту вылезания наружу она захватывает внутри большу́ю площадь. Поэтому, если вы увидели на пороге пузырёк вздувшейся краски, с большой вероятностью это уже дыра с палец толщиной.
Механизм действия абсолютно любых средств на основе восков и мастик один — покрыть плёнкой металл. Ингибиторы в их составе — это маркетинговый ход, после высыхания плёнки они уже никакой роли не играют. Поэтому плёнка антикора — единственный барьер перед коррозией. Так почему же машины, обработанные тектилами/мовилями/мастиками всё равно гниют? Со временем парафиновое покрытие теряет эластичность, трескается и в нём появляются микропоры, через которые влага попадает к металлу. То же касается и мастики на днище. Многие видели, как старая мастика сползает, стоит только чем-нибудь её поддеть.
Вот что происходит под мастикой на примере моей бывшей восьмёрки. Всё это сделал всего лишь конденсат, подкрылки на ней стояли с самого начала. Влага напрямую никогда туда не попадала! Заметьте полоску от заводского скотча на отверстии для проводов повторителя поворота, под ней нет ржи. Всё потому, что мастика пропускает под себя влагу, а скотч нет.
Вот что происходит под мастикой на примере моей бывшей восьмёрки. Всё это сделал всего лишь конденсат, подкрылки на ней стояли с самого начала. Влага напрямую никогда туда не попадала! Заметьте полоску от заводского скотча на отверстии для проводов повторителя поворота, под ней нет ржи. Всё потому, что мастика пропускает под себя влагу, а скотч нет.
Внутри с мовилями картина аналогичная, просто этого не видно. Вернее, видно, когда уже поздно 🙂 Пара примеров. Нексия, 2006 год. Была обработана обычным парафиновым антикором типа TECTYL или WAXOYL. Весь низ добротно обработан, никаких непрокрасов нет. Диагноз — замена порогов, двери и кучи ещё всего. Как же так?
Дверь нексии, обработанная 10 лет назад восковым антикором типа тектила / ваксойла. Внутри на панели и брусе безопасности отчётливо виден след обработки. Снизу изнутри также всё было отлично обработано.
Полный размер
Дверь нексии, обработанная 10 лет назад восковым антикором типа тектила / ваксойла. Внутри на панели и брусе безопасности отчётливо виден след обработки. Снизу изнутри также всё было отлично обработано.
Результат антикоррозийной обработки выглядит впечатляюще, что-то явно пошло не так.
Полный размер
Результат антикоррозийной обработки выглядит впечатляюще, что-то явно пошло не так.
Второй пример — шестёрка 1999 года выпуска, тоже обработана восковым антикором. Обработана жирненько, смачно! Судя по потёкам, даже не один раз.
Крыло, Мовиль. XX век, неизвестный мастер.
Полный размер
Крыло, Мовиль. XX век, неизвестный мастер.
При желании, можно найти множество примеров прямо здесь, на драйв2. Причина всё та же — высыхание и растрескивание покрытия. Стоит ещё добавить, что парафиновый состав нельзя наносить на грязную поверхность. В инструкции к препарату обычно сказано «очистить и обезжирить». А вы видели изнутри порог машины, которой всего-то пара лет? Так что разрезаем порог болгаркой, очищаем-обезжириваем и завариваем на место. И лишь потом обрабатываем, только так будет правильно по инструкции. И то, сварной шов изнутри так же должен быть зачищен и обезжирен.
Исходя из всего вышесказанного, я сделал выводы, что правильный вечный антикор должен:
1) не высыхать,
2) содержать ингибиторы коррозии,
3) сам расползаться по внутренним полостям с помощью капиллярного эффекта,
4) пропитывать всю грязь внутри и не требовать подготовки поверхности.
Таким условиям может соответствовать только антикор на масляной основе. Но 90% продукции ML — это боди, тектилы, динитролы и всевозможные «мовили» на восковой основе, которая рано или поздно высыхает. На масляной основе я видел всего два антикора: канадский RUST STOP и Noxudol 700. Я очень давно использую RUST STOP, репутация у него безупречная. Но как обычно есть нюансы, которые перечеркивают все плюсы. РАСТ-СТОП А для скрытых полостей слишком жидкий и со временем весь вытекает. Обработку придётся повторять раз в год-два. РАСТ-СТОП Б для днища нормально ничем нельзя разбавить, поэтому внутрь так просто его не загнать. Если использовать его по назначению, на днище, то он не образует плёнку. Так и останется мазнёй типа вазелина. Со временем пропитает заводскую мастику и она станет такой мягкой, что её можно будет стереть пальцем. Спору нет, ржаветь не будет, но мне не нравится такая липкая мягкость на днище. Да и дороговато, 800р за литр.
Раст-стоп А для внутренних полостей
Раст-стоп А для внутренних полостей
Тут настало самое время упомянуть совершенно обособленный вид антикора, так называемое «пушечное сало». Этот велосипед изобрели ещё в союзе. Читаем состав: пушечное сало — не что иное, как… загущенное масло! Именно в этом секрет его легендарной стойкости к коррозии. Правда, при упоминании пушсала в дискуссии на тему антикоррозийной обработки, обычно начинается «сейчас есть в сто раз лучше», «это когда ничего другого не было», «купи нормальный современный препарат» и прочее. Ну-ну, на современные препараты я уже насмотрелся.
Только продаваемое сейчас пушсало — «совсем не торт» и часто содержит больше парафина, чем масла. Но мы обратим этот факт себе в пользу и допилим с помощью RUST STOP’а. Раст-стоп нужен пушечному салу для лучшего расползания, уменьшения вязкости (чрезмерное увеличение вязкости — главная причина растрескивания) и придания ему лучших антикоррозийных свойств.
Пушечное сало необходимо найти двух разных видов. Твердое, с большим количеством парафина — для днища, и мягкое, как литол24 — для внутренних полостей. Состав легко проверить на ощупь: твердое «пушасло» с парафином не будет липнуть к рукам. Я брал двух от разных фирм: OIL RIGHT и БиКар.
Ойлрайтовское пушечное сало не образует плёнку, оно всегда мягкое. Примерно как литол-24 и больше всего похоже на классическое пушсало из СССР. Его я использую для внутренних полостей, разбавленным раст-стопом 3 к 1. Т.е. на одну банку пушсала 2кг требуется 650мл раст-стопа.
пушсало ОЙЛРАЙТ, использовал для внутренних полостей
пушсало ОЙЛРАЙТ, использовал для внутренних полостей
БиКаровское пушечное сало твёрдое, т.к. содержит парафин, а вот самой сути — масла — в нём, как мне кажется, очень мало. Его, разбавленным раст-стопом 4 к 1, я наношу на днище. Т.е. на одну банку 2кг требуется 500мл раст-стопа. Каким видом раст-стопа (для внутренних полостей или днища) разбавлять пушечное сало, значения не имеет. Они отличаются только наличием тиксотропного загустителя у раст-стопа Б и розовым красителем у раст-стопа А. Действующих веществ в них одинаковое количество. Я рекомендую разбавлять только раст-стопом Б для днища. И в случае необходимости, его можно использовать в чистом виде для устранения непрокрасов (например, внутри двери или арки колеса) без нагревания.
пушсало Бикар, использовал для днища
пушсало Бикар, использовал для днища
Летом этот антикор разогревается на солнце и начинаются волшебные метаморфозы. Благодаря капиллярному эффекту он ползёт по всем поверхностям, даже вверх, пропитывая каждую трещинку. Это будет происходить каждый год, и с каждым годом антикоррозийная защита будет только усиливаться, а не трескаться. Что самое приятное, не надо с этим морочиться регулярно — достаточно одной обработки на весь срок службы машины.
Технология обработки несложная, но мутроная и грязная. К этому сразу нужно быть морально готовым и запастись терпением. Нужна плитка, кисточки, медицинские шприцы (проще всего достать 30мл, штук 5) и обязательно строительный фен. Сначала пушсало разогревается на плитке до жидкого состояния. Когда оно полностью станет жидким, в него добавляется раст-стоп и смесь перемешивается. Не надо перегревать и кипятить сало, чтобы оно меняло цвет! Потом шприцем разогретый жидкий состав загоняется во все внутренние полости по технологической карте обработки конкретного автомобиля, с одновременным прогревом целевой поверхности строительным феном или плиткой. Пороги я предварительно прогревал той же электроплиткой, в которой растапливал сало. Затем кистью смесь из твёрдого пушсала и раст-стопа наносится днище, предварительно разогретое электроплиткой или строительным феном — тогда пушсало ложится просто идеально и отлично впитывается. Днище обрабатывается по квадратам, по размеру нагревательной способности плитки/фена.
Благодаря гнилой шестёрке у меня имеется бесценная схема ключевых гниющих мест на классике 🙂 Особое внимание нужно уделить стойкам лобового стекла, столбам передней подвески (из-под капота 2 отверстия), усилителям брызговика (треугольники с 2мя отверстиями справа от бардачка и слева панели приборов), верху задних дверей около ручки, солдату, чашкам пружин, задней и передней панелям под бамперами. Я не говорю про лонжероны-пороги-крылья, это само собой.
Так изнутри должна выглядеть обработанная дверь
Так изнутри должна выглядеть обработанная дверь
Обработанное днище
Полный размер
Обработанное днище
И под конец блиц-опрос. Отвечу на самые часто задаваемые вопросы из комментариев и лички:
Геморно? Да! Грязно? Очень! Но оно того стоит. Конечно, проще и быстрее компрессорным пистолетом загнать жидкий не гор
www.drive2.ru
* Можно ли делать антикор зимой?
Один из распространенных мифов об антикор обработке это то, что её нужно делать летом.Попробуем внести ясность в этот вопрос!
Представляется, что миф идет из прошлых времен, когда не было хороших материалов для антикор обработки и это делалось подручными средствами — пушсалом, отработкой, нигролом и т. д. Классическая рекомендация мастеров тех времен: после обработки покатайся по пыли! Поставь на солнце! Надежней будет!
С тех времен прошли многие годы, сейчас большинство цивилизованных антикор-центров используют в работе современные специализированные материалы, которые не требуют выполнения подобных рекомендаций!
Современные составы для обработки днища вполне самодостаточны, им не нужна пыль для отвердения! Если их правильно нанести на сухую чистую поверхность, то они будут долгие годы надежно защищать автомобиль. Материалы для скрытых полостей (МЛ-составы) так же полностью адаптированы к обычным методам нанесения без постановки на солнце и т. д., более того локальный перегрев сразу после нанесения может даже сделать более тонким защитный слой на вертикальных поверхностях, так как материалы разрабатываются с учетом нанесения при средних температурах.
Еще одна причина заблуждений идет из времен, когда не было возможности сделать качественную подготовку (отмыть, просушить поверхность), поэтому выбирали меньшее из зол: пусть чуть грязноватая поверхность, зато сухая.
Сейчас в антикор-центрах с организованным процессом подготовки, в любом случае днище сначала моется (намокает), затем продувается воздухом, сушится тепловыми пушками. Поэтому не имеет значения, сухая машина приехала на обработку или мокрая.
Производители материалов обычно рекомендуют 15-20 часов щадящего режима после нанесения, пока материал не пришел в конечное состояние. Свежие покрытия не боятся ни влаги, ни температуры, они боятся механических воздействий. Но в этом случае более опасны высокие температуры. Когда на улице холодно, машина выезжает из цеха, материал твердеет и не так важен становится щадящий режим эксплуатации. Хуже, когда на улице +30, материал мягкий и его легко повредить в первые сутки.
Поэтому зима, в некотором смысле, даже более благоприятное время для нанесения покрытий.
22.11.2016
Посетите наш канал
xn--80aqgkhmk.xn--p1ai
Ремонт и Доработка» на DRIVE2
В начале этого года встал вопрос восстанавливать мою старую машину или менять на что то посвежее, было решено взятся за старое и вылечить все болячки, чем покупать авто подороже с новыми косяками…
Разобрав машину вылезла неприятная картина
Машина 2005 года( и так сгнила, прежние владельци походу плохо следили за ней…
После удаления заводского антикора, все зачищал карцовкой, до сох пор в ушах звенит как вспомню что целый день с болгаркой плясал возле нее)
Затем все хорошо матуем и обезжириваем и наносим кислотный грунт, когда он подсохнет наносим шовный герметик, везде где есть стыки метала или сварочные швы…
Дав герметику подсохнуть наносим на него акриловый грунт
Делал кстати в 2 этапа, чтобы голый метал долго не оставался без защиты… Сначала зачищал и грунтовал и красил переднюю часть, а на следующий день заднюю, т. к за день это сложно сделать
Затем когда краска высыхает, хорошенечко ее матуем скочь брайтом и обезжириваем, чтобы зацепился антикор получше и наносим горячий антикор
Мой рецепт антикора позаимствованый у одного человека тут на драйве…
В суп идет мастика и пуш сало в пропорции 1 к 1
Все это дело варится на костре
У меня ушло 2 банки мастики и 2 банки пуш сала, нанес я 4-5 слоев…
Надеюсь после такого машина гнить не будет…
www.drive2.ru
FAQ антикор
зависит от Ваших планов на автомобиль, на иномарке среднего класса, при средних пробегах (20000-30000 км в год) 3-4 года видимых следов ржавчины, как правило, нет, потом постепенно, начинают появляться рыжие пятна вдоль швов… до сквозной коррозии обычно проходит еще 2-3 года. Впрочем все это очень приблизительно. Производители автомобилей сейчас не ставят целью производить долговечные кузова.
В любом случае, производя дополнительную антикоррозионную обработку Вы закладываете более долгую жизнь кузову!
НЕ СУЩЕСТВУЕТ однозначного определения, что такое АНТИКОР!
Любой производитель в той или иной степени заботится об обработке автомобиля, некоторые машины имеют высокую степень защиты (качественный металл кузовного листа, покрытие цинком, полимерные покрытия, воски), другие меньшую, но любой специалист в области антикоррозионной защиты скажет что максимальная защита стального листа обеспечивается цинкованием, качественной окраской и покрытием поверх органическими материалами.
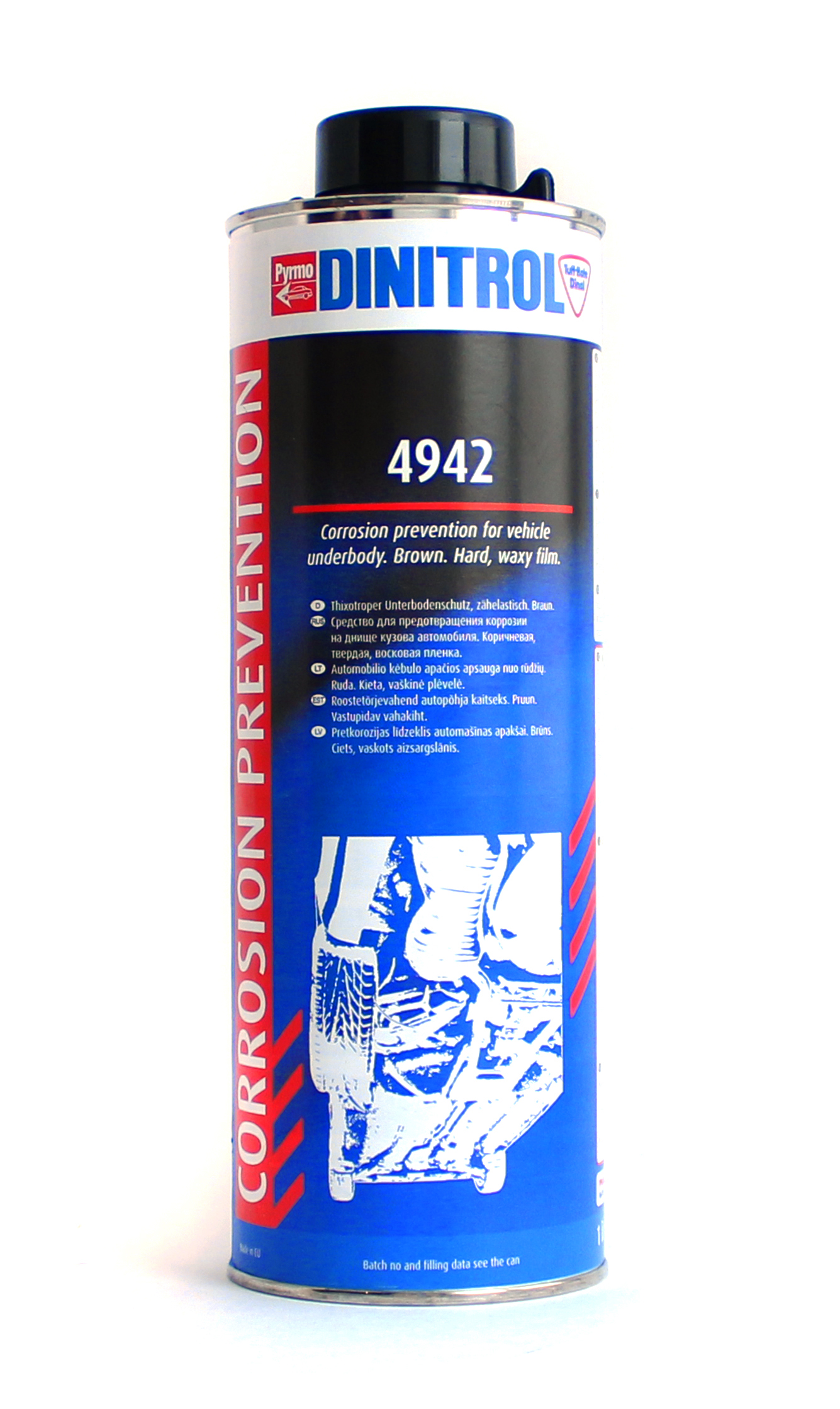
если не планируется покрытие полимерными составами типа «антигравий», то ржавчину достаточно очистить до состояния, что бы она не сыпалась и не слоилась. После зачистки, если ржавчина остается, она грунтуется МЛ составами, а затем, желательна обработка не высыхающими мастиками на восковой основе. В случае, когда коррозионные повреждения уже достаточно сильные (перфорированная, сквозная коррозия), то рекомендуется обработка МЛ материалами на масляной основе и скрытых полостей и внешних поверхностей.
старое покрытие нужно удалять, если оно отслаивается, потрескалось и т. д., чаще всего в этом нет необходимости, достаточно очистить его в местах где оно отслаивается.
мы применяем антикоррозионные материалы только известных и проверенных производителей, это материалы верхнего эшелона качества.
Материалы разных производителей могут по каким-то позициям проигрывать, по каким-то выигрывать друг у друга, но все материалы из первой пятерки на 100% выполнят свои задачи. Еще важно понимать что при обработке машины важен не только материал, но и технология обработки: кузов должен быть промыт, просушен и материалы нанесены в соответствии с назначением и в нужные места.
при повторных обработках, как правило, нет проблем химической несовместимости материалов, вопрос лежит в области физических свойств, чаще всего стоит придерживаться правила не наносить более твердые покрытия поверх более мягких. Например битумные покрытия поверх масляных или восковых…

Разница между комплексами в материале для покрытия днища и колесных арок. Это могут быть МЛ — составы, защитные покрытия на битумной и восковой основах или противоизносные пасты, так называемые «жидкие подкрылки».
«жидкие подкрылки» это не подкрылки, как таковые. Это покрытие, резино-битумная композиция, материал, имеющий повышенную механическую прочность, износостойкость, позволяющую покрытию эффективно сопротивляться абразивному воздействию в колесных арках. После нанесения мастики образуется резиноподобный слой, толщиной 2-4 мм. Применяется в случае, когда нет пластиковых подкрылок, с целью защиты от износа и повышения защиты от шума от колес.
да, можно.
Часто такие покрытия делаются на машины, которые эксплуатируются в тяжелых условиях (бездорожье, гравийные дороги) с целью усиленной защиты.
Или с целью дополнительной шумоизоляции.
полимерные материалы, «антигравий» подразумевают подготовку поверхности «как под покраску» и подготовить днище, арки машины, бывшей в эксплуатации крайне трудно, чаще применяют специализированные материалы для обработки арок — «жидкие подкрылки».
это зависит от конструкции конкретной модели, штатного и дополнительного подкрылка. Установка подкрылка диктуется конструкцией дополнительного подкрылка, некоторые крепятся саморезами в кромку крыла. В последнее время более распространены подкрылки, которые устанавливаются без саморезов, с использованием штатных элементов крепления.
антикоррозионную обработку можно производить в любое время года. Зима, в некотором роде, даже более благоприятный период, так как когда автомобиль после обработки выезжает на улицу, материал остывая, твердеет, уменьшается риск повреждения свежего покрытия.
полная обработка автомобиля в нашем центре занимает около 7-10 часов, в зависимости от модели, состояния кузова, из которых основное время уходит на подготовку (промыть, просушить кузов)
все зависит от применяемых материалов, при обработке материалами содержащими уайт-спирит испарения и запах неизбежны, качественные импортные материалы обычно имеют нерезкий запах в течении нескольких дней, (много зависит от температуры и конструкции автомобиля), если применяются материалы не содержащие растворителей, то запаха нет вообще…
обработка скрытых полостей, днища (материалами для днища) практически никакого эффекта не дает (толщина пленки очень невысока). Эффект шумоизоляции появляется при нанесении резино-битумных мастик, материалов типа «жидкие подкрылки». Покрытие 2-3 мм. толщиной в той или иной степени снижает вибронагрузки и шум.
можно ехать сразу, но желательно некоторое время (20-30 часов), избегать механических воздействий (не буксовать, ездить с невысокими скоростями, не мыть машину…)
машина выглядит чистой, на лакокрасочном покрытии не должно быть следов антикора, потеков и т. д., возможна некоторая «жирность» покрытия на ощупь, которая смоется на любой мойке.
гарантия означает, что в течении гарантийного срока, не должно появиться ни малейших следов ржавчины, (если ее не было до обработки, что определяется и фиксируется в процессе осмотра), если появляются отслоения, следы ржавчины то это гарантийный случай и повод предъявить претензию.
Наши условия сохранения гарантии подробно описаны в гарантийном сертификате.
Оплатить Вы можете любым, удобным Вам способом. Наличными деньгами, банковским платежом, пластиковой картой , Яндекс деньгами, Вебмани
Существуют скидки при повторных обращениях, для клубов партнеров,…различные варианты снижения цены Вы можете посмотреть здесь: http://антикор.рф/discounts/
материалы применяемые в нашем центре достаточно долговечны и не теряют свойств при эксплуатации в условиях Москвы, при обычной эксплуатации, минимум 6-7 лет, важно только чтобы они лежали на кузове…
Повторная обработка нужна ТОЛЬКО в случае, если покрытие утрачено (ободрано, стерто…) или потеряло свойства (ссохлось, потрескалось,…)

по закону, Вы не лишитесь гарантии на автомобиль, если какие-то работы производите в сертифицированных центрах. Впрочем, в любом случае стоит позвонить Вашему дилеру и узнать его мнение по данному вопросу. У наших центров есть все необходимые сертификаты для выполнения работ по антикоррозионной защите и шумоизоляции.
Вы можете их найти на странице Нормативные документы
xn--80aqgkhmk.xn--p1ai
Два новых антикор материала от Valvoline | TECTYL BIOCLEANER & TECTYL TPC-INVISIBLE
В начале октября 2015 года, Европейское отделение компании VALVOLINE сообщило о выпуске 2-x новых продуктов:
TECTYL BIOCLEANER и TECTYL TPC-INVISIBLE.
Это яркий пример, того, когда спрос рождает предложение. Расширена и дополнена линейка водорастворимых антикор продуктов. Водорастворимые антикоррозионные материалы, являются материалами 4-го поколения антикоров ТЕКТИЛ. Экологические требования Евросоюза все более ужесточают требования к охране окружающей среды. Здесь мы приводим материалы, которые работают в парах с материалами на восковой основе такие как ТЕКТИЛ 506, 502, 846 и ТЕКТИЛ 511-М на масляной основе.
Много функциональный антикор состав TECTYL BIOCLEANER.
Этот антикоррозионный состав применяется для удаления антикор материала с металлических частей механизмов или конструкций после хранения и перед использованием. Для удаления: синтетических, животных, растительных и минеральных масел, смазок и покрытий. Удаляет антикоррозионные материалы TECTYL.
Это комплексное дополнение к решениям по защите от коррозии, которые мы предлагаем для наших клиентов, когда есть необходимость удалить временный защитный слой антикора (например, TECTYL 506 или 846 на восковой основе, или TECTYL 511 – на масляной основе).
TECTYL BIOCLEANER. Концентрат вещества TECTYL BIOCLEANER можно разбавить обычной водопроводной водой. Соотношение: 25% TECTYL BIOCLEANER к 75% обычной воды. Далее можно использовать раствор разными способами, от распыления под давлением, до работы со щеткой. Главное, что готовый раствор TECTYL BIOCLEANER справляется с задачей в считаные секунды. Защитная пленка антикора растворяется в растворе данного материала.
Второе дополнение к линейке антикор продуктов — это новый водорастворимый материал TECTYL TPC-INVISIBLE.
Этот антикоррозионный состав применяется для временной защиты металлических частей механизмов или конструкций от коррозии во время хранения в помещении и на открытом воздухе.
Продукт рекомендуется(!) использовать для очистки конструкций и механизмов, когда очистка водой или напором воды под давлением, несет угрозу возникновения очагов коррозии. Чтобы, избежать возникновения коррозии на металлических поверхностях после обработки водой, в водопроводную воду добавляют концентрат материла TECTYL TPC-INVISIBLE в объеме 3% — 5%. Полученный антикор раствор может наносится распылением или погружением детали в него.
Поставляется с оригинальной надписью VALVOLINE
Варианты фасовки:
Артикул 862979 TECTYL BIOCLEANER — 20 л ведро
Артикул 854414 TECTYL TPC-INVISIBLE — 25 кг ведро
Особенности и преимущества
TECTYL BIOCLEANER
• На водной основе
• Биоразлагаемый
• 25% водный раствор
Особенности и преимущества
TECTYL TPC-INVISIBLE
• На водной основе
• Очень экономичный с толщиной слоя 0,5 мкм
• Только 3-5% концентрата в водном растворе
• Нет необходимости для очистки металлических частей перед использованием
• Может быть окрашено поверху
• Невидимое невооруженным глазом
Соответствующая техническая информация ниже:
PI_Tectyl-Biocleaner_TE040-01
PI_Tectyl_TPC_Invisible_TE074-01
Как выбрать спрей-антикор — виды спреев и особенности каждой группы
Если вы задумались о покупке спрея-антикора, то ответьте себе на простой вопрос – для чего он вам? Ответ на этот вопрос подскажет, чем нужно руководствоваться для правильного выбора антикоррозийного средства в аэрозоли.
Большинство спреев-антикоров – универсальны, то есть один баллончик можно использовать для разных целей, однако, существует условное разделение:
- Технические;
- Автомобильные.
Технические спреи применяются для устранения дефектов оцинкованных изделий, для ремонта поврежденных цинковых покрытий, дополнительной защиты после сварки деталей, защитной обработки трубопроводов и другого металлического оборудования, а так же в качестве грунта, под покраску металлических поверхностей.
Автомобильные спреи применяются для защиты от ржавчины различных автомобилей. Они в свою очередь подразделяются на спреи для внешних и внутренних (скрытых) поверхностей кузова.
То есть, выбор спрея в первую очередь происходит исходя из его назначения. Так же спреи можно разделить по составу, методу воздействия, по узким областям применения или по очередности нанесения.
По составу
По составу можно выделить цинковые спреи, алюминиевые, с нержавеющей сталью, хромом, никелем, медью, латунью, бронзой и другими металлами. Они производятся на основе алкидных, стирольных, природных и синтетических смол, каучука, битума, полимерных связующих, воска, органических растворителей и прочих компонентов.
В общем, больше важен не состав, а эффект, который это состав вам даст. Самым распространенным, потому что самым эффективным компонентом в борьбе с ржавчиной является цинк.
Цинк более активен по сравнению с железом и покрыт оксидной пленкой. Металлы покрываются слоем цинка (в составе спрея-антикора) и при контакте с влагой, в местах царапин и повреждений покрытия возникает гальваническая пара. Катод в данном случае — железо, а анод — цинк. Электроны движутся от цинка к железу, где связываются молекулами кислорода. В результате, цинк потихонечку растворяется, а железо остается неповрежденным коррозией.
Такая защита действует до 15-25 лет, пока слой цинкового покрытия не разрушится. Ярким примером такого средства является — Цинкор-спрей с высоким содержанием цинкового порошка до 95%.
Спреи с содержанием других металлов, обычно обходятся дороже цинковых, но дают дополнительные преимущества: особый цвет, блеск, защита от высоких температур и прочие.
По методу воздействия
По методу воздействия спреи, как и другие антикоры, делятся на 2 вида. Антикоры, действующие пассивным (барьерным) методом и активным (катодным).
Большинство спреев, не содержащих металлические частицы, работают как барьер от внешних воздействий и не дают коррозии образовываться. Обычно, такой защиты хватает на несколько лет, при бережном использовании.
Спреи, содержащие металлические частицы, так же защищают барьерным методом, но действуют дольше, до 10 лет.
Спреи, содержащие цинк и алюминий защищают металлы сразу двумя способами — барьерным и катодным (также называемым активным, протекторным или электрохимическим).
Катодная защита подразумевает, что цинк при нанесении на железо образует с ним гальваническую пару, в которой железо — менее активный металл, а цинк — более
активный. При контакте с влагой и кислородом цинк-анод вступает в реакцию первым, жертвует свои электроны на борьбу с коррозией, а железо — катод принимает электроны, защищается и остается практически не тронутым ржавчиной. Защитный процесс продолжается до полного истощения слоя цинка.1 слоя в 40-60 мкм хватает на 10-25 лет.
Сразу 2 способа защиты, которые сменяют друг друга, очень пригождаются металлам с первого дня эксплуатации. Дело в том, что любое покрытие составом не герметично на 100%, а имеет дефекты и поры. Цинковое покрытие также может пропускать некоторое количество кислорода на начальном этапе использования. Именно тогда оно защищает металлы от ржавчины протекторным или электрохимическим способом. В процессе эксплуатации происходит уплотнение структуры покрытия, полное растворение цинковых соединений и вступает в силу барьерная защита, как при горячем цинковании. Если целостность покрытия будет нарушена (царапины, механические повреждения, разъедание химикатами), то за работу снова возьмется катодная защита.
По областям применения
Спреи-антикорры универсальны, их наносят на любые металлические поверхности. Поэтому вы вряд ли найдете антикоррозийный спрей «специально для забора» или «для нанесения на трубы». Автомобильная область является исключением, здесь вы встретите спрей «для днища» или «для порогов». Это делается как раз для удобства покупателей-автолюбителей. Хотя для этих целей подойдет практически любой антикоррозийный спрей с характеристиками стойкости к коррозии и хорошей адгезией.
Однако некоторые спреи-антикоры больше подойдут для той или иной области применения. Так для металлических поверхностей, постоянно подвергающихся механическим воздействиям, лучше выбирать спреи на основе каучуковых, битумных смол или полимеров, с хорошей эластичностью, позволяющие нанесение толстым слоем. Например, для днища автомобиля.
Так же стоит тщательнее выбирать спрей для внутренних полостей и труднодоступных мест. Здесь пригодятся спреи на масляной или на восковой основе, с проникающей способностью, влагоотталкивающими и даже влаговытесняющими свойствами. Необходимо позаботиться о способе доставки спреев в труднодоступные места – специальные тонкие трубки и насадки.
По очередности нанесения
Спреи, как и прочие антикоррозийные покрытия, используются как грунт, промежуточное или финишное покрытие, а так же могут быть универсальными. Большинство спреев, представленных на нашем сайте – универсальны и станут любым из слоев. Вам просто стоит определиться – для чего вам спрей? В качестве какого слоя вы хотите его использовать? Планируете ли вы наносить покрытие поверх спрея? И прочитать в описании – подойдет ли выбранное вами средство для этих целей.
СВЯЖИТЕСЬ С НАМИ ПРЯМО СЕЙЧАС И УЗНАЙТЕ О САМЫХ ВЫГОДНЫХ ПРЕДЛОЖЕНИЯХ, СКИДКАХ И АКЦИЯХ!
телефон: 8 (800) 707-53-17
e-mail: info@tdspray. ru
Для вас мы работаем: пн-пт 9:00-18:00
С уважением, коллектив магазина TDSPRAY.ru
Аэрозоль Mercasol 3 / 3 AL (Меркасол 3 / 3 АЛ)
ОБЛАСТЬ ПРИМЕНЕНИЯ
Mercasol 3 / 3 AL является разновидностью одного материала, отличающаяся цветом, предназначен для индивидуальной антикоррозионной обработки в гаражах или мастерских. Используется для внутренних полостей, порогов и соединений на автомобилях для защиты от гравия и коррозии. Mercasol 3 / 3 AL может использоваться вместе с препаратами Mercasol 1, нанесенным ранее. Mercasol купить и нанести можно самому не прибегая к услугам автосервисов.
ХАРАКТЕРИСТИКИ
Mercasol 3 / 3 AL — черного и бронзового цвета соответственно. Mercasol 3 / 3 AL является хорошим проникающим антикор. средством с содержанием растворителя (алифатические нафтены) на воско-масляной основе. Обладает хорошими антикор. свойствами в течение длительного периода времени. Создает пленку для защиты от гравия. Препарат был протестирован на совместимость с наиболее распространенными антикор. системами на рынке и одобрен для применения на большей части различных марок автомобилей.
ПОДГОТОВКА ПОВЕРХНОСТИ
Обрабатываемая поверхность должна быть сухой и очищенной от грязи, соли и масел. Возможно использование Меркасола 1 перед нанесением Mercasol 3 / 3 AL.
НАНЕСЕНИЕ
Нанесение должно производиться в помещении при температуре от +15ºС — +40ºС. Mercasol 3 / 3 AL должен наноситься безвоздушным методом или воздушным методом с использованием оборудования Гевеко.
Аэрозоль Mercasol 3 / 3 AL можно также наносить распылением через установленный на баллоне носик.
РЕКОМЕНДУЕМАЯ ТОЛЩИНА СЛОЯ
200 мкм толщина влажного слоя дает толщину 90 мкм сухого слоя. Возможно повторное нанесение для получения более толстой пленки.
РАСХОД МАТЕРИАЛА
0,40 лтр/м²
ОЧИСТКА
Очистка оборудования проводится алифатическим растворителем. Излишки материала предпочтительнее удалять препаратом Mercasol Cleaner или алифатическим растворителем.
ВРЕМЯ ВЫСЫХАНИЯ
Время высыхания зависит от температуры и влажности, при температуре +23ºС и относительной влажности 50% время высыхания составляет приблизительно 4 часа.
ХРАНЕНИЕ
Срок хранения – 12 месяцев, при соблюдении соответствующей инструкции.
ТЕХНИЧЕСКИЕ ДАННЫЕ
- Слой Восковой
- Проникающая Способность >70 мм в полости 50 мкм
- Адгезия при Отсутствие трещин и низкой температуре отслаивания при температуре -20ºС
- Растворитель Алифатические нафтены < 0,1% ароматический в-в
- Точка вспышки ~ +40ºС
- Содержание сухого в-ва в весов.% ~ 51%
- в-ва в объем.% ~ 45%
- Вязкость ~ 52мПас
- Плотность ~ 0,86 г/см³
Вышеуказанная техническая информация описывает основные параметры. Она не описывает точные параметры и предельные значения выше/ниже. Целью данной информации является общее описание технические качеств препарата. Информация не является гарантией в отношении специальные характеристик или годности препарата для применения в определенных областях. Поскольку Гевеко Индастри АБ не контролирует условия хранения препарата после его отгрузки, компания несет ответственность только за техническое качество препарата в соответствии с «Общими условиями продаж и отгрузки» компании, которые можно получать у Гевеко Индастри АБ.
Цвет: черный.
Упаковка: 1 литр.
Как обработать мовилью автомобиль
Понравилась статья? Следите за новыми идеями полезных авто советов в нашем канале. Подписывайтесь на нас в Яндекс.Дзене. Подписаться.«Мовиль» является антикоррозийным составом, которые используются в ремонтно-кузовных работах в автомастерских для защиты кузова и металлических элементах авто от ржавчины. «Мовиль» прост в использовании, но для создания максимально надежного защитного слоя, который будет максимально долго защищать кузов, следует помнить об основных правилах нанесения этого средства.
Самостоятельная обработка автомобиля «Мовилем»
В отличие от элементов трансмиссии и двигателя, которые после капитального ремонта по внешнему виду практически не отличаются от новых, кузов может сохранить многие скрытые дефекты, которые после закрашивания могут быть не видны, но от этого их опасность не уменьшается. Речь идет об очагах коррозии, которые при непрофессиональном подходе трудно и порой невозможно полностью нейтрализовать.
В результате приходится либо латать образующиеся сквозные отверстия от коррозии, либо проводить более основательные работы вплоть до полной замены поврежденных элементов кузова. Избежать этого можно, применяя антикоррозийный состав «Мовиль», который является отличным профилактическим средством от ржавчины. Существует несколько видов этого антикоррозийного состава, и каждый из них решает определенные проблемы. Вне зависимости от этого при нанесении следует придерживаться общих основных правил.
Как правильно наносить «Мовиль»
Все виды средства «Мовиль» наносятся с помощью специального устройства в виде пистолета для распыления. Такой способ обработки способствует наиболее глубокому проникновению средства в поврежденные участки и его равномерному распределению по поверхности кузова. Если кузов был предварительно обработан любым видом синтетической мастики – нанесение «Мовиля» не рекомендуется. Но средство можно использовать, если кузов обрабатывался перед этим битумной мастикой. Через образованный ею слой антикор все равно будет проникать к металлической поверхности детали.
Другие основные правила нанесения «Мовиля» заключаются в следующем:
- Состав не следует наносить на резиновые прокладки и заглушки, так как активные вещества «Мовиля» могут разъедать резину.
- Перед нанесением средства обрабатываемую поверхность необходимо зачистить от ржавчины и загрязнений и обезжирить с помощью растворителя или других специальных средств.
- Оптимальная температура для распыления «Мовиля» варьируется в пределах +10-+30 градусов, поэтому такие работы лучше проводить в закрытых мастерских или отапливаемых боксах.
- Перед тем, как основательно обрабатывать поверхность кузова, рекомендуется распылить небольшое количество «Мовиля», чтобы увидеть, с какой интенсивностью производить нанесение для оптимального растекания по поверхностям.
- В среднем расход средства при учете его нанесения одним слоем составляет около 400 граммов на квадратный метр. При нанесении второго и последующего слоев расход следует рассчитывать индивидуально.
Окончательное высыхание «Мовиля» происходит за два часа, после чего исправить недостатки покраски уже невозможно, поэтому во время проведения работ следует распылять средство аккуратно и сразу обирать ее излишки и устранять образующиеся подтеки.
На тему антикоррозийной обработки уже очень много сказано-пересказано и сломано копий о головы друг друга. Это почти как религия. Это почти как «тосол» и антифриз. Это точно так же, как выбор масла. 🙂 Я просто поделюсь с вами единственно верным вариантом антикоррозийной обработки своими руками…
Ладно, шучу конечно. Наверняка вы тоже уже начитались множество статей, где люди варят адовые смеси из мовиля-мастики-солярки-негрола-пушсала-отработки-пластилина-парафиновых свечек и крыльев златоглазок. Возможно они неплохи, но вот необходимость и эффективность каждого компонента, а главное долговечность, обычно остаются туманны. На вопрос «как оно через 10 лет» обычно отвечают что машина продана, а эффективность можно оценить только через 7-8 лет после обоработки. Это не говоря про вонизм и вред для здоровья. Я же расскажу вам про свой вариант антикоррозийной обработки своими руками, доказательством эффективности которого послужит четвёрка. Сейчас ей уже 30 лет, но нет ни одного пятнышка ржавчины. Не надо думать, что она хранится в гараже в сферическом вакууме. Ей тоже неплохо достаётся и дождиков, и грязевых ванн. Гаража у неё нет, обычно она хранится на даче под открытым небом или в Москве прямо на улице среди хлоридов натрия, магния, кальция и чёрта лысого.
Антикор по этому рецепту был сделан ей пятнадцать лет назад, в 2004 году и с тех пор ни разу не обновлялся. Затем эта технология неоднократно повторялась на огромном количестве разных машин с отличным результатом. Почему бы не отдать в антикор-центр? Я не жлоб, и человек не совсем бедный, но! Я пока ни разу не видел, чтобы кто-то, за любые вообще деньги, качественно антикорил чужую машину. Тем более, правильными препаратами.
Как обычно, сначала немного теории. Как гниёт машина? Очень просто — изнутри. Меня крайне умиляют люди, усердно намазывающие по низу кузова мастику и антигравий, думая, что теперь-то двери и пороги уж точно не заржавеют. Если поцарапать краску до металла снаружи, ждать дырку надо лет десять. Но изнутри, например в пороге, достаточно всего одного маленького очага коррозии. Если он там появится, примерно через 3 года гарантирована сквозная дыра: раствор воды и реагентов быстро сделает своё дело. Если вы переварили те же пороги, то без обработки хватит их ровно на 2 года. По сравнению со внешней, развивающаяся внутри полостей коррозия почти всегда более обширна. К моменту вылезания наружу она захватывает внутри большу́ю площадь. Поэтому, если вы увидели на пороге пузырь вздувшейся краски, с большой вероятностью это уже дыра с палец толщиной.
Механизм действия абсолютно любых средств на основе воска или мастики — это защитная плёнка на металле. Ингибиторы в их составе — это маркетинговый ход, после высыхания плёнки они уже никакой роли не играют. Поэтому плёнка антикора — единственный барьер перед коррозией. Почему же машины, обработанные тектилами/мовилями/мастиками всё равно гниют? Со временем парафиновое покрытие теряет эластичность, трескается и в нём появляются микропоры, через которые влага попадает к металлу. То же касается и мастики на днище. Многие видели, как старая мастика сползает, стоит только чем-нибудь её поддеть.
Внутри с мовилями картина аналогичная, просто этого не видно. Вернее, видно, когда уже поздно 🙂 Пара примеров. Нексия, 2006 год. Была обработана обычным парафиновым антикором типа TECTYL или WAXOYL. Весь низ добротно обработан, никаких непрокрасов нет. Диагноз — замена порогов, дверей и кучи ещё всего. Как же так?
Второй пример — шестёрка 1999 года выпуска, была обработана очередным «мовилем». Обработана жирненько, смачно! Судя по потёкам, даже не один раз.
При желании, можно найти множество примеров прямо здесь, на драйв2: пример 1, пример 2. Причина всё та же — высыхание и растрескивание покрытия. Стоит ещё добавить, что парафиновый состав нельзя наносить на грязную поверхность. В инструкции к препарату обычно сказано «очистить и обезжирить». А вы видели изнутри порог машины, которой всего-то пара лет? Так что разрезаем порог болгаркой, очищаем-обезжириваем и завариваем на место. И лишь потом обрабатываем, только так будет правильно по инструкции. И то, сварной шов изнутри так же должен быть как-то зачищен и обезжирен )))
Исходя из всего вышесказанного, я сделал выводы, что правильный вечный антикор должен:
1) не высыхать,
2) содержать ингибиторы коррозии,
3) сам расползаться по внутренним полостям с помощью капиллярного эффекта,
4) пропитывать всю грязь внутри и не требовать подготовки поверхности.
Таким условиям может соответствовать только антикор на масляной основе. Но 90% продукции ML, все эти боди, тектилы, динитролы и всевозможные «мовили» на восковой основе, которая рано или поздно высыхает. На масляной основе я видел всего два антикора: канадский RUST STOP и Noxudol 700. Лично я очень давно использую RUST STOP, репутация у него безупречная. Но как обычно есть нюансы, которые перечеркивают все плюсы. РАСТ-СТОП А для скрытых полостей слишком жидкий и со временем весь вытекает. Обработку придётся повторять раз в год-два. РАСТ-СТОП Б для днища нормально ничем нельзя разбавить, поэтому внутрь так просто его не загнать. Если использовать его по назначению, на днище, то он не образует плёнку. Так и останется мазнёй типа вазелина. Со временем пропитает заводскую мастику и она станет такой мягкой, что её можно будет стереть пальцем. Спору нет, ржаветь не будет, но мне не нравится такая липкая мягкость на днище. Да и дороговато, 800р за литр.
Тут настало самое время упомянуть совершенно обособленный вид антикора, так называемое «пушечное сало». Этот велосипед изобрели ещё в союзе. Читаем состав: пушечное сало — не что иное, как… загущенное масло! Именно в этом секрет его легендарной стойкости к коррозии. Правда, при упоминании пушсала в дискуссии на тему антикоррозийной обработки, обычно начинается «сейчас есть в сто раз лучше», «это когда ничего другого не было», «купи нормальный современный препарат» и прочее. Ну-ну, на современные препараты я уже насмотрелся.
Только продаваемое сейчас пушсало — «совсем не торт» и часто содержит больше парафина, чем масла. Но мы обратим этот факт себе в пользу и допилим его с помощью RUST STOP’а. Раст-стоп нужен пушечному салу для лучшего расползания, уменьшения вязкости (её чрезмерное увеличение — главная причина растрескивания) и придания ему лучших антикоррозийных свойств.
Пушечное сало необходимо найти двух разных видов. Твердое, с большим количеством парафина — для днища, и мягкое, как литол — для внутренних полостей. Состав легко проверить на ощупь: твердое «пушасло» с парафином не будет липнуть к рукам. Выбирайте сало любой фирмы, принципиальной разницы нет. Я брал двух от разных фирм: OIL RIGHT и БиКар.
Ойлрайтовское пушечное сало не образует плёнку, оно всегда мягкое. Примерно как литол-24 и больше всего похоже на классическое пушсало из СССР. Его я использую для внутренних полостей, разбавленным раст-стопом 3 к 1. Т.е. на одну банку пушсала 2кг требуется 650мл раст-стопа.
БиКаровское пушечное сало твёрдое, т.к. содержит парафин, а вот самой сути — масла — в нём, как мне кажется, очень мало. Его, разбавленным раст-стопом 4 к 1, я наношу на днище. Т.е. на одну банку 2кг требуется 500мл раст-стопа. Раст-стоп А и Б отличаются только наличием тиксотропного загустителя у раст-стопа Б и розовым красителем у раст-стопа А. Действующих веществ в них одинаковое количество. Я рекомендую разбавлять только раст-стопом Б для днища, т. к. на тиксотропный загуститель не действует высокая температура и летом в случае чрезмерного нагрева на солнце это придаст составу чуть большую стабильность. И в случае необходимости, его можно использовать в чистом виде для устранения непрокрасов (например, внутри двери или арки колеса) без нагревания. Раст-стоп Б очень неохотно растворяется в жидком пушсале, т.к. температура на тиксотропный загуститель не действует. Так что терпение, мой друг, и ещё раз терпение.
Летом этот антикор разогревается на солнце и начинаются волшебные метаморфозы. Благодаря капиллярному эффекту он ползёт по всем поверхностям, даже вверх, пропитывая каждую трещинку. Это будет происходить каждый год, и с каждым годом антикоррозийная защита будет только усиливаться, а не трескаться. Что самое приятное, не надо с этим морочиться регулярно — достаточно одной обработки на весь срок службы машины.
Технология обработки несложная, но мутроная и грязная. К этому сразу нужно быть морально готовым и запастись терпением. Нужна плитка, кисточки, медицинские шприцы (проще всего достать 30мл, штук 5) и обязательно строительный фен. Сначала пушсало разогревается на плитке до жидкого состояния. Когда оно полностью станет жидким, в него добавляется раст-стоп и смесь перемешивается. Не надо перегревать и кипятить сало, чтобы оно меняло цвет! Потом шприцем разогретый жидкий состав загоняется во все внутренние полости по технологической карте обработки конкретного автомобиля, с одновременным прогревом целевой поверхности строительным феном или плиткой. Пороги я предварительно прогревал той же электроплиткой, в которой растапливал сало. Затем кистью смесь из твёрдого пушсала и раст-стопа наносится на днище, предварительно разогретое электроплиткой или строительным феном — тогда пушсало ложится просто идеально и отлично впитывается. Днище обрабатывается по квадратам, по размеру нагревательной способности плитки/фена.
Благодаря гнилой шестёрке у меня имеется бесценная схема ключевых гниющих мест на классике 🙂 Особое внимание нужно уделить стойкам лобового стекла, столбам передней подвески (из-под капота 2 отверстия), усилителям брызговика (треугольники с 2мя отверстиями справа от бардачка и слева панели приборов), верху задних дверей около ручки, солдату, чашкам пружин, задней и передней панелям под бамперами. Я не говорю про лонжероны-пороги-крылья, это само собой.
И под конец блиц-опрос. Отвечу на самые часто задаваемые вопросы из комментариев и лички:
Геморно? Да! Грязно? Очень! Но оно того стоит. Конечно, проще и быстрее компрессорным пистолетом загнать жидкий не горячий состав, но вечного антикора из этого не получится.
Обрабатывал ли я пол салона? Нет. Я считаю, что сухость в салоне — лучший и единственный известный мне рабочий рецепт для исключения коррозии. Если будет болото, хоть ведро сала вылей — результат так или иначе станет плачевным. Вот тут человек через это прошёл: www.drive2.ru/l/533807123922944113/
Чем ещё разбавить, если жалко денег/не нашёл раст-стопа? Консервационное масло К-17, рекомендацию с трансмиссионкой и сухим горючим убираю после результатов эксперимента этого человека. Лучше раст-стопа всё равно ничего нет.
А можно я разбавлю мовилем вместо раст-стопа? Мовиль-мовиль, хочу мовиль, люблю мовиль!11 То, что вы называете мовилем, а особо продвинутые ещё и по какой-то дикой нелепости мовилью — в женском роде — делают непонятно кто и где. Настоящий тру-мовиль, который, кстати сказать, не поверите, делался на основе масла, кончился вместе с СССР и больше не появится никогда, смиритесь. Но пробуйте на здоровье, если лень учиться на чужих ошибках.
Можно ли наносить на голый металл? Конечно можно, хотя я рекомендую всегда сначала грунтовать эпоксидным грунтом. Здесь же приведу рецепт феншуйного ЛКП: металл зачищается от ржавчины → травится преобразователем (или наносится кислотный грунт) → акриловый грунт (изолятор) → эпоксидный грунт → акриловая краска (либо акриловый грунт → база → лак). Но когда я варил шестёрку, мазал на голый металл. Всё прекрасно держится, только слой получается тоньше.
Как клеить шумоизоляцию? Сначала вы клеите шумоизоляцию, потом наносится антикор по контуру и швам. Это верно для любого антикора. На сало сверху не приклеится ничего.
А можно наносить по заводской мастике? Можно и нужно, хоть по заводской мастике, хоть чему угодно, включая уже начинающуюся ржавчину. Только зачистить от отваливающихся частей и грязи, чтобы не было полостей под многослойной ржавчиной. Хотя в таких случаях обычно уже пора варить. Зачищать можно без фанатизма, без обезжиривания, без болгарки. Просто чтобы был виден слой прежнего антикора или неотваливающейся ржавчины.
Хочу облегчить ацкий труд, как насчёт распыления мовильником/антигравийным пистолетом? У меня лично ничего хорошего из этих экспериментов не вышло. Смесь в полёте застывает и на поверхности получается консистенция «воздушный творожок чудо». Кто не видел — купите, заодно попробуйте, вкусно. Всё в пузырьках, а поверхность не пропитана. Актуально только если греть, и втирать кисточкой, но тогда и облегчения никакого особо нет. К тому же приходится постоянно греть сам инструмент, очень быстро забивается.
Говорят можно разбавлять уайт-спиритом или бензином, чтобы не греть, но я так не делал из соображений безопасности.
На сколько хватит такого антикора? Вопрос хороший. Процесс полимеризации масла и испарения лёгких фракций состава всё равно идёт, а именно они отвечают за эластичность и адгезию. Поэтому я вас обманул, это не вечный антикор и хватит его примерно лет на 50. На четвёрке за 15 лет состав стал чуть твёрже, чем свежак. Весьма вероятно, что ещё лет через 40 он всё-таки затвердеет так, что начнёт отваливаться. Тогда моим внукам придётся повторить.
Нахрен надо, иномарки не гниют! Гниют. Особенно в москве, с особым рвением. «Вы просто поверьте, а поймёте потом».
А можно ли намазать мастику, хоть куда-нибудь, хоть зачем-нибудь. Нет, мастика — это абсолютное зло. С чем бы её ни смешай.
Какое количество нужно на легковую машину? При аккуратном равномерном нанесении хватит 2кг + 2кг сала разных видов + 1л раст-стопа Б. Версию А покупать вообще не надо, только Б. Если заливать «по уши» и вообще отнестись с фанатизмом, берите 4+4+2. Но это очень проблематично впихнуть, да и польза вряд ли будет больше от количества. Единственное, на днище можно мазать побольше.
А как же потом её варить? Свою шестёрку я сначала всю гнилую отантикорил, а потом варил. Все же так делают, правда? 🙂 Первый способ — стравить пушсало нафиг с помощью того же фена. Нагрел — всё стекло — вари. Второй способ — забить. Да, будет капать, гореть, но горение сало не поддерживает, тухнет как только остынет. За время сварки я два раза палил шестёрку. Первый раз загорелась шумка, второй раз — проводка подкапотки при проварке столба. Сало не сильно мешало.
И ещё одно неоспоримое преимущество моего рецепта — он безвреден для здоровья и не воняет. Особенно это касается любителей отработки, отработанное масло является довольно сильным канцерогеном.
- Мовиль для авто: как пользоваться?
- Что такое Мовиль
- Подготовка автомобиля перед обработкой
- Как наносить Мовиль правильно
- Какой Мовиль выбрать, богатство предложений на рынке
Ржавчина на кузове авто – это головная боль многих автомобилистов. Как с ней бороться, чтобы со временем машина не превратилась в кусок ржавого железа? Сегодня рынок автохимии предлагает разные активные средства защиты автомобиля от разрушающего действия коррозии. Среди них – «Мовиль» с преобразователем ржавчины. Что же такое «Мовиль» и как им правильно пользоваться?
Что такое Мовиль
«Мовиль» – это универсальный антикор для скрытых полостей автомобиля. Но кроме этого, «Мовиль» используют для обработки днища авто, особенно когда машину ставят на консервацию. В состав «Мовиля» входит машинное масло, растворитель, ингибитор коррозии и добавки, которые придают этому автоконсерванту свойства текучести и способность вытеснять остатки влаги с любых поверхностей: окрашенных и неокрашенных.
Чем хорош «Мовиль»? При нанесении автоконсерванта на поверхность образуется тонкая маслянистая пленка, которая предотвращает образование ржавчины. Таким образом, поверхность металла полностью изолируется от попадания влаги и воздуха – главных виновников коррозии. Если очаги ржавчины уже есть, то ингибитор в составе данного средства начинает сразу активно уничтожать ржавчину.
Что нужно знать об особенностях средства «Мовиль»:
• Наносится на любую металлическую поверхность: окрашенную или нет.
• Не нуждается в дополнительной сушке.
• Покрывает поверхность тонкой герметической пленкой, препятствующей попаданию влаги на незащищенный металл.
• Не агрессивный к краске и металлу.
• Агрессивный к резине.
• Несовместим с синтетическими мастиками.
• Прекрасно проникает в труднодоступные места авто.
Подготовка автомобиля перед обработкой
Перед обработкой антикором автомобиль надлежит обработать:
1. Помыть машину. Если обрабатывать нужно днище, то его моют на подъемнике: струей горячей воды с давлением 60-100 атмосфер.
2. Просушить поверхность.
3. Устранить дефекты на поверхности металла. Если есть рыхлая ржавчина – убрать ее.
4. Нанести антикор. Подсохшая пленка создаст защитный слой в 40-60 мкм.
Как наносить Мовиль правильно
Препарат «Мовиль» наносится при помощи специального пистолета. Распыление под давлением позволяет «Мовилю» проникнуть во все щели и углубления, которые могут быть подвержены коррозии. На открытых участках допускается нанесение препарата кисточкой.
«Мовиль» можно наносить на поверхность, ранее обработанную битумной мастикой: средство все равно проникнет во все поврежденные места и надежно законсервирует металл. Если на поверхность ранее была нанесена синтетическая мастика, то применять «Мовиль» категорически запрещено. Следите, чтобы «Мовиль» не повредил резиновые элементы авто.
Советы по нанесению средства «Мовиль»:
• Очистить поверхность от грязи и вздувшейся ржавчины.
• Рекомендуется обезжирить поверхность.
• Распылять «Мовиль» лучше при температуре от +10 до +30 градусов.
• Наносить «Мовиль» следует в 2-3 слоя.
• Наносить средство нужно равномерно. Внимание! Сначала нанесите препарат на багажник или дверь, и посмотрите, как он растекается. Тогда вам легче будет сориентироваться в методике распыления (вам важно, чтобы не лило).
• Расход препарата на 1 слой: 400 г на квадратный метр.
• Полное высыхание – через 2 часа.
Если «Мовиль» попадает на краску, то отмыть его потом крайне сложно. Если капли средства попали на краску, то убирайте подтеки сразу. Если на некоторых технологических отверстиях есть заглушки – снимите их: «Мовиль» сможет проникнуть в такие недоступные места через отверстия под заглушками.
Какой Мовиль выбрать, богатство предложений на рынке
Выбор марки «Мовиля» не влияет на качество защитной пленки на поверхности металла. Автоконсервант «Мовиль» может быть разливной и в баллонах (под давлением). Разливной «Мовиль» подходит для нанесения кисточкой и для заправки специального пистолета. «Мовиль» в баллонах сразу можно распылять. Если вы собираетесь проработать средством труднодоступные места, но у вас нет краскопульта, то покупайте «Мовиль» в форме аэрозоля.
Подписывайтесь на наши ленты в таких социальных сетях как, Facebook, Вконтакте, Instagram, Pinterest, Yandex Zen, Twitter и Telegram: все самые интересные автомобильные события собранные в одном месте.
Повышение физико-химических и антикоррозионных свойств полиуретанового покрытия на основе тунгового масла путем модификации ангидридами и неорганической кислотой
Реферат
Полиол на основе тунгового масла (ТО) синтезирован гидроксилированием и алкоголизом. Модификацию синтезированного полиола (очищенное алкоголизированное гидроксилированное тунговое масло (PAHTO)) проводили с использованием определенной пропорции фталевого ангидрида (PA), малеинового ангидрида (MA) и борной кислоты (BA), действующих как модификаторы, так и сшивающие агенты. Модифицированный полиуретан (PU) получали взаимодействием модифицированного полиола с толуолдиизоцианатом (TDI) в соотношении NCO / OH = 0,7. Спектроскопические исследования модифицированного ПУ подтвердили процесс модификации. Антикоррозионные свойства модифицированного ПУ на оцинкованной стали (GS) оказались лучше, чем у мягкой стали (MS) в водном (3,5 мас.%) Растворе NaCl. Полученные характеристики гидрофобности и шероховатости поверхности вместе с ее морфологией были проанализированы с использованием атомно-силовой микроскопии (АСМ) и краевого угла (СА).Свойства химической стойкости, а также физические свойства, такие как блеск, стойкость к царапинам, адгезия и ударопрочность, оценивались с использованием стандартных методов. Было обнаружено, что сшивающий фрагмент в основной цепи цепи PU проявляет лучшие физико-химические свойства по сравнению с немодифицированным PU. Термическая стабильность модифицированного полиуретанового покрытия была исследована с помощью дифференциальной сканирующей калориметрии (ДСК) и термогравиметрического анализа (ТГА), которые показали, что термические свойства, такие как разложение и стеклование материалов, увеличиваются с увеличением молярного соотношения ПА и БА.Исследование потенциодинамической и электрохимической импедансной спектроскопии (EIS) показало лучшую коррозионную стойкость PU с включением PA и BA, которые позволяют использовать его в нескольких промышленных и коммерческих целях.
Ключевые слова
Модифицированный полиуретан (PU)
Оцинкованная сталь (GS)
Низкоуглеродистая сталь (MS)
Модификатор
сшивающий агент
Поляризация
Коррозия
Спектральный анализ
Электрохимический импеданс (EIS4)
Характеристика поверхности
Рекомендуемые статьи Цитирующие статьи (0)
Полный текст© 2019 Elsevier B.V. Все права защищены.
Рекомендуемые статьи
Цитирующие статьи
(PDF) АНТИКОРРОЗИОННАЯ ДЕЯТЕЛЬНОСТЬ НЕКОТОРЫХ НОВЫХ ПАВ НА ОСНОВЕ РАСТИТЕЛЬНЫХ МАСЕЛ
Антикоррозионные ПАВ на основе растительных масел Раздел D-Research Paper
Eur. Chem. Бюлл., 2014, 3 (5), 437-440 437
АНТИКОРРОЗИОННАЯ ДЕЯТЕЛЬНОСТЬ НЕКОТОРЫХ НОВЕЙШИХ
ПАВ НА ОСНОВЕ РАСТИТЕЛЬНЫХ МАСЕЛ
Аббасов В. М., Исмайлов И. Т., [а, б] Хани М.Абд Эль-Латиф, [а, в] и С. Ф.
Ахмадбекова [а]
Ключевые слова: ингибирование коррозии; поверхностно-активные вещества; растительные масла; жирные кислоты; адсорбция; мягкая сталь
Ингибирование коррозии молекулами поверхностно-активного вещества связано со способностью поверхностно-активного вещества агрегироваться на границах раздела и в растворе. В этой статье
исследуется ингибирование адсорбции и коррозии ряда товарных поверхностно-активных веществ жирных кислот, синтезированных на основе растительных масел (подсолнечное,
, хлопковое, кукурузное и пальмовое масло), на низкоуглеродистой стали при 50 ºC в насыщенном CO2 рассоле.Эффективность ингибирования соединений teste
показала хорошее ингибирование и защиту углеродистой стали даже при низких концентрациях. Тенденция к ингибированию коррозии
коррелирует с химической структурой соединений.
Авторы, ответственные за переписку
E-mail: [email protected]
[a] Институт нефтехимических процессов им. Мамедалиева, Национальная
Академия наук Азербайджана, AZ1025 Баку,
Азербайджан
[b] Факультет Химия, Московский государственный университет имени М.В. Ломоносова,
119991, ГСП-1, Россия, Москва, Ленинские горы 1-3,
[c] Кафедра химии, факультет естественных наук, Университет Сохаг,
82524 Сохаг, Египет
Введение
Исследование коррозии CO2 началось несколько десятилетий назад, и
еще нельзя считать завершенным.Углеродистая сталь
широко используется в качестве насосно-компрессорных труб или трубопроводов в нефтегазовой промышленности
и обычно сильно эродируется, особенно когда коррозионный электролит
содержит CO2.1 В нефтедобывающей и обрабатывающей промышленности
ингибиторы имеют всегда был
считался первой линией защиты от коррозии.
Большинство ингибиторов, используемых в настоящее время в добывающих скважинах, представляют собой
органических азотистых соединений. В этом смысле использование поверхностно-активных веществ
в качестве ингибиторов является одним из наиболее известных методов защиты от коррозии
.2-4 Ингибирование коррозии молекулами поверхностно-активного вещества
связано со способностью поверхностно-активного вещества агрегировать на границах раздела
и в растворе.
В данной работе синтезированы новые поверхностно-активные вещества
, выделенные из растительных масел (подсолнечное (A), хлопковое (B), кукурузное (C) и пальмовое (D) масла
) и изучены их антикоррозионные свойства
. свойства в средах с углекислым газом при 50 ° C. Поверхностно-активные вещества
были приготовлены в различных композициях
(Схема 1) на основе растительных масел и диэтаноламина, как в
Ref.5 Структуры синтезированных ПАВ
подтверждены физико-химическими спектроскопическими методами.
Схема 1. Молекулярная структура синтезированных анионных ПАВ
, где M = Na + (Ингибитор I), K + (Ингибитор II), Nh5
+
(Ингибитор III), -NH-Ch3Ch3OH (Ингибитор IV), -N- (Ch3Ch3OH) 2
(Ингибитор V).
Эксперименты
Скорость коррозии стойкости к линейной поляризации (LPR)
(метод пузырьковых испытаний) включает оценку коррозии
данного металла в смоделированном рассоле, насыщенном CO2, при температуре
, эквивалентной температуре в полевых условиях.Во время теста в тестовый раствор непрерывно барботируется
CO2. Скорость коррозии
определяется мгновенно с помощью метода LPR
, в котором небольшое постоянное напряжение
прикладывается к паре идентичных электродов, и измеряется результирующий ток
. Ограничение метода пузырьковых испытаний состоит в том, что он
не дает информации о влиянии напряжения сдвига на
на характеристики данного ингибитора коррозии.
Результаты и обсуждение
Рисунок 1 показывает, что изменение скорости коррозии (CR)
со временем для низкоуглеродистой стали в 1% -ном растворе NaCl, насыщенном
с CO2, содержащим различные концентрации ингибитора формы
I при 50 ° C синтезирован на основе всех четырех масел. Ингибитор
был добавлен после 1 часа воздействия, потому что в это время потенциал коррозии
стал стабильным, что позволило измерить скорость коррозии (CR)
до введения ингибитора.
Исходный CR без ингибитора составил
между 3,45 и 5,03 мм / год. Из рисунка
видно, что CR в отсутствие ингибитора имеет тенденцию к увеличению со временем на
. Увеличение CR было связано с
гальваническим эффектом между фазой феррита и цементитом
(Fe3C), который является частью исходной стали в окисленном состоянии, отличном от
, и накапливается на поверхности после
предпочтительного растворение феррита (α-Fe) в Fe2 + [6].Известно, что Fe3C
менее активен, чем ферритная фаза.
Следовательно, происходит преимущественное растворение феррита
по сравнению с цементитом, при этом первый работает как анод, а
последний как катод, что способствует реакции выделяющегося водорода
(HER) в процессе коррозии 6,7
Параметры коррозии рассчитывались на основании теста LPR
. Эффективность ингибирования (IE) и степень покрытия поверхности
рассчитывали согласно следующим уравнениям
: 5
CH- (CH 2) 7-CN
OS
R- (Ch3) 8-
O
O
O
O
Ch3-Ch3-OH
Ch3-CH 2-OH
-M +
Этот сайт использует файлы cookie для повышения производительности.Если ваш браузер не принимает файлы cookie, вы не можете просматривать этот сайт.
Настройка вашего браузера для приема файлов cookie
Существует множество причин, по которым cookie не может быть установлен правильно. Ниже приведены наиболее частые причины:
- В вашем браузере отключены файлы cookie. Вам необходимо сбросить настройки своего браузера, чтобы он принимал файлы cookie, или чтобы спросить, хотите ли вы принимать файлы cookie.
- Ваш браузер спрашивает вас, хотите ли вы принимать файлы cookie, и вы отказались.Чтобы принять файлы cookie с этого сайта, используйте кнопку «Назад» и примите файлы cookie.
- Ваш браузер не поддерживает файлы cookie. Если вы подозреваете это, попробуйте другой браузер.
- Дата на вашем компьютере в прошлом. Если часы вашего компьютера показывают дату до 1 января 1970 г., браузер автоматически забудет файл cookie. Чтобы исправить это, установите правильное время и дату на своем компьютере.
- Вы установили приложение, которое отслеживает или блокирует установку файлов cookie.Вы должны отключить приложение при входе в систему или проконсультироваться с вашим системным администратором.
Почему этому сайту требуются файлы cookie?
Этот сайт использует файлы cookie для повышения производительности, запоминая, что вы вошли в систему, когда переходите со страницы на страницу. Чтобы предоставить доступ без файлов cookie потребует, чтобы сайт создавал новый сеанс для каждой посещаемой страницы, что замедляет работу системы до неприемлемого уровня.
Что сохраняется в файле cookie?
Этот сайт не хранит ничего, кроме автоматически сгенерированного идентификатора сеанса в cookie; никакая другая информация не фиксируется.
Как правило, в файлах cookie может храниться только информация, которую вы предоставляете, или выбор, который вы делаете при посещении веб-сайта. Например, сайт
не может определить ваше имя электронной почты, пока вы не введете его. Разрешение веб-сайту создавать файлы cookie не дает этому или любому другому сайту доступа к
остальной части вашего компьютера, и только сайт, который создал файл cookie, может его прочитать.
Повышение антикоррозионных и микроэлектрических свойств полиуретановых нанокомпозитов из зеленого масла Brassica nigra
Roiter Y, Minko S (2005) Одномолекулярные эксперименты в АСМ на границе твердое тело – жидкость: конформация адсорбированных гибких полиэлектролитных цепей in situ. J Am Chem Soc 127: 15688–15689
Статья CAS PubMed Google Scholar
Исикгора Ф.Х., Бесер С.Р. (2015) Лигноцеллюлозная биомасса: устойчивая платформа для производства химикатов и полимеров на биологической основе. Polym Chem 6: 4497–4559
Статья CAS Google Scholar
Хоутон К.А., Бурслем Г.М., Уилсон А.Дж. (2015) Разработка синтеза супрамолекулярных полиуретанов с водородной связью без использования растворителей. Chem Sci 6: 2382–2388
Статья CAS PubMed PubMed Central Google Scholar
Sadekar AG, Mahadik SS, Bang AN, Larimore ZJ, Wisner CA, Bertino MF, Kalkan AK, Mang JT, Sotiriou-Leventis C, Leventis N (2012) От «зеленых» аэрогелей до пористого графита путем эмульсии гелеобразование акрилонитрила.Chem Mater 24: 26–47
Статья CAS Google Scholar
Ray D, Das K, Ghosh SN, Bandyopadhyay NR, Sahoo S, Mohanty AK, Misra M (2010) Новые материалы из шелухи кунжута и ненасыщенной полиэфирной смолы. Ind Eng Chem 49: 6069–6074
Статья CAS Google Scholar
Hojabri L, Kong X, Narine SS (2009) Диизоцианат на основе жирных кислот и полиуретан на биологической основе, полученные из растительного масла: синтез, полимеризация и характеристика.Биомакромология 10: 884–891
Статья CAS Google Scholar
Liu W, Zheng Y, Li J, Liu L, Huang X, Zhang J, Kang X, Tang X (2012) Новые полиуретановые сетки на основе гибридного неорганического / органического фосфазена, содержащие нанотрубки с поверхностно-активными гидроксильными группами . Polym Adv Technol 23: 1–7
Статья CAS Google Scholar
Lligadas G, Ronda JC, Galia M, Cadiz V (2010) Растительные масла как платформенные химические вещества для синтеза полиуретана: современное состояние.Биомакромология 11: 2825–2835
Статья CAS Google Scholar
Silva WSD, Lapis AAM, Suarez PAZ, Neto BAD (2011) Ферментно-опосредованное эпоксидирование метилолеата, поддерживаемое ионными жидкостями на основе имидазолия. J Mol Catal B Enzym 68: 98–103
Статья CAS Google Scholar
Явни И., Петрович З.С., Гуо А., Фуллер Р. (2000) Термическая стабильность полиуретанов на основе растительных масел.J Appl Polym Sci 77: 1723–1734
Статья CAS Google Scholar
Кулкарни Р.Д., Дешпанде П.С., Махаджан С.У., Махуликар П.П. (2013) Эпоксидирование горчичного масла и раскрытия кольца 2-этилгексанолом для биосмазочных материалов с улучшенными термоокислительными характеристиками и текучестью комков. Ind Crops Prod 49: 586–592
Статья CAS Google Scholar
Vedtofte MS, Jakobsen MU, Lauritzen L, Heitmann BL (2012) Роль незаменимых жирных кислот в контроле ишемической болезни сердца.Curr Opin Clin Nutr Metab Care 6: 592–596
Артикул CAS Google Scholar
Guo A, Cho Y-J, Petrovic ZS (2000) Структура и свойства галогенированных и негалогенированных полиолов на основе сои. J Polym Sci Часть A Polym Chem 38: 3900–3910
Статья CAS Google Scholar
Петрович З.С., Чжан В., Явни И. (2005) Структура и свойства полиуретанов, полученных из триглицеридных полиолов озонолизом.Биомакромол 6: 713–719
Статья CAS Google Scholar

Fleischmann C, Lievenbrück M, Ritter H (2015) Полимеры и красители: разработки и применения. Полимеры 7: 717–746
Артикул CAS Google Scholar
Раджан Х., Раджалингам П., Радхакришнан Г. (1993) Синтез и свойства сегментированного полиуретана с использованием фенолфталеина в качестве удлинителей цепи.J Appl Polym Sci 48: 2095–2099
Статья CAS Google Scholar
Карнароглио Д., Мартина К., Пальмизано Г., Пенони А., Домини С., Кравотто Г. (2013) Последовательный синтез изоцианатов и производных мочевины в одном сосуде с помощью реакции Штаудингера-аза-Виттинга с помощью микроволн, Байльштейн. J Org Chem 9: 2378–2386
CAS Google Scholar
Kreye O, Mutlu H, Meier MAR (2013) Устойчивые пути к прекурсорам полиуретана.Green Chem 15: 1431–1455
Статья CAS Google Scholar
Zu Y, Tang J, Zhu W, Zhang M, Liu G, Liu Y, Zhang W., Jina M (2011) СаО-катализаторы, нанесенные на оксид графита, для переэтерификации соевого масла метанолом. Биоресур Технол 102: 8939–8944
Артикул CAS PubMed Google Scholar
Bykkam S, Rao KV, Chakra CHS, Thunugunta T (2013) Синтез и характеристика оксида графена и его антимикробная активность против Klebseilla и Staphylococcus.Int J Adv Biotechnol Res 4: 142–146
Google Scholar
Вадивел С., Ванита М., Мутукришнарадж А., Баласубраманян Н. (2014) Композитный материал оксид графена – BiOBr как высокоэффективный фотокатализатор для разложения красителей метиленовый синий и родамин – В. J Water Process Eng 1: 17–26
Статья Google Scholar
Прасанна Д. , Сельварадж В. (2017) Композит поли (сульфонилдифенол / циклофосфазен / бензидин) -графен, легированный платиной и медью, в качестве электродного материала для одноэлементных щелочных топливных элементов с прямым спиртовым соединением.RSC Adv 7: 34922–34932
Статья Google Scholar
Magal RT, Selvaraj V (2017) Сравнительное исследование электрокаталитического окисления спирта на наночастицах Pt-Au, нанесенных на композит с привитым сополимером оксида графена для применения в топливных элементах. Ионика 22: 1–12
Google Scholar
Yao RR, Zhao D-L, Bai L-Z, Yao N-N, Xuz L (2014) Простой синтез и электрохимические характеристики полых графемовых сфер в качестве анодных материалов для литий-ионных аккумуляторов.Nanoscale Res Lett 9: 368–373
Статья CAS PubMed PubMed Central Google Scholar
Хуанг Т., Синь И, Ли Т., Натт С., Зулианг Лай С. (2013) Модифицированный нанокомпозит графен / полиимид: усиливающие и трибологические эффекты. Интерфейсы Appl Mater 5: 4878–4891
Статья CAS Google Scholar
Wu G, He X, Xu L, Zhang H, Yan Y (2015) Синтез и характеристика биополиуретана / SiO 2 нанокомпозита из природного масла sapium sebiferum.RSC Adv 5: 27097–27106
Статья CAS Google Scholar
Chang C-H, Huang T-C, Peng C-W, Yeh T-C, Lu H-I, Hung W-I, Weng C-J, Yang T-I, Yeh J-M (2012) Новые антикоррозионные покрытия, полученные из композитов полианилин / графен. Carbon 50: 5044–5051
Артикул CAS Google Scholar
Желудкевич М.Л., Щукин Д.Г., Ясаков К.А., Мохвальд Х., Феррейра М.Г.С. (2007) Антикоррозионные покрытия с эффектом самовосстановления на основе наноконтейнеров, пропитанных ингибитором коррозии. Chem Mater 19: 402–411
Статья CAS Google Scholar
Pu NW, Shib GN, Liu YM, Sun X, Chang JK, Sun CL, Ger MD, Chen CY, Wang PC, Peng YY, Wu CH, Lawes S (2015) Графен, выращенный на нержавеющей стали как высокоэффективное и экологически чистое антикоррозионное покрытие для биполярных пластин топливных элементов с полимер-электролитной мембраной. J Power Sources 282: 248–256
Статья CAS Google Scholar
Шармин Э., Зафар Ф., Акрам Д., Алам М., Ахмад С. (2015) Последние достижения в области экологически чистых покрытий на основе растительных масел: обзор. Ind Crops Prod 76: 215–229
Статья CAS Google Scholar
Гауда О.Е., Махмуд С.Ф., Эль-Генди А.А., Хайба А.С. (2014) Улучшение диэлектрических свойств полиэтилена высокой плотности за счет включения глины-нанонаполнителя. World J Eng Technol 2: 289–297
Статья Google Scholar
Prateek VK Thakur, Gupta RK (2016) Последние достижения в области нанокомпозитов на основе сегнетоэлектрических полимеров для конденсаторов с высокой плотностью энергии: синтез, диэлектрические свойства и будущие аспекты. Chem Rev 116: 4260–4317
Артикул CAS PubMed Google Scholar
Khamsen N, Onwimol D, Teerakawanich N, Dechanupaprittha S, Kanokbannakorn W, Hongesombut K, Srisonphan S (2016) Стерилизация семян риса ( Oryza sativa L.) без повышения температуры прорастания в атмосфере с помощью плазменной стерилизации .ACS Appl Mater Interfaces 8: 19268–19275
Статья CAS PubMed Google Scholar
Чао-Лунг Х, Ле Ань-Туан Б., Чун-Цун С. (2011) Влияние золы рисовой шелухи на характеристики прочности и долговечности бетона. Constr Build Mater 25: 3768–3772
Статья Google Scholar
Wu C, Huang X, Wang G, Wu X, Yang K, Li S, Jiang P (2012) Функционализация графеновых листов сверхразветвленным полимером для улучшения механических и диэлектрических свойств полиуретановых композитов.J Mater Chem 22: 7010–7019
Статья CAS Google Scholar
Wu C, Huang X, Wu X, Xie L, Yang K, Jiang P (2013) Гибриды углеродных нанотрубок с инкапсулированным оксидом графена для получения нанокомпозитов с высокими диэлектрическими характеристиками и повышенной плотностью накопления энергии. Наномасштаб 5: 3847–3855
Артикул CAS PubMed Google Scholar
Ян Х., Ли Ф., Шан Ц., Хан Д., Чжан К., Ню Л., Иваск А. (2009) Ковалентная функционализация химически преобразованных графеновых листов с помощью силана и его усиления.J Mater Chem 19: 4632–4638
Статья CAS Google Scholar
Wu X, Zhang X, Yang S, Chen H, Wang D (2000) Исследование эпоксидированного рапсового масла, используемого в качестве потенциального биоразлагаемого смазочного материала. J Am Oil Chem Soc 77: 561–563
Статья CAS Google Scholar
Zhang C, Li Y, Chen R, Kessler MR (2014) Полиуретаны из полиолов на основе растительных масел, не содержащих растворителей.ACS Sustain Chem Eng 2: 2465–2476
Статья CAS Google Scholar
Daniel L, Ardiyanti AR, Schuur B., Manurung R, Broekhuis AA, Heeres HJ (2011) Синтез и свойства сильно разветвленных производных масла Jatropha curcas L. Eur J Lipid Sci Technol 113: 18–30
Статья CAS Google Scholar

Серешт Р.Дж., Джаханшахи М., Рашиди А.М., Горейши А.А. (2013) Синтез и характеристика термически восстановленного графена.Iran J Energy Environ 4: 53–59
Google Scholar
Zhang J, Tang JJ, Zhang JX (2015) Полиолы, полученные из эпоксидированного соевого масла с раскрывающимся кольцом с помощью жирного диола на основе касторового масла. Int J Polym Sci 22: 1–8
Статья CAS Google Scholar
Dai H, Yang L, Lin B, Wang C, Shi G (2009) Синтез и характеристика различных полиолов на основе сои путем раскрытия кольца эпоксидированного соевого масла с метанолом, 1,2-этандиолом и 1 , 2-пропандиол.J Am Oil Chem Soc 86: 261–267
Статья CAS Google Scholar
Шайк М.Р., Алам М., Аландис Н.М. (2015) Разработка экологически безопасных материалов на основе поли (уретанэфирамида) / Fe 2 O 3 нанокомпозитов в качестве материалов для антикоррозионных покрытий. J Polym Eng 35: 813–916
Статья CAS Google Scholar
Сауседо-Ривалькоба В., Мартинес-Эрнандес А.Л., Мартинес-Баррера Г., Веласко-Сантос С., Ривера Армента Дж.Л., Кастаньо В.М. (2011) Удаление шестивалентного хрома из воды с помощью полиуретан-кератиновых гибридных мембран.Вода, загрязнение воздуха и почвы 218: 557–571
Статья CAS Google Scholar
Шамси Р., Садеги GMM (2016) Новый полиэфирный диол, полученный из отходов ПЭТ, и его применение в синтезе композитов на основе полиуретана и углеродных нанотрубок: поведение при набухании и характерные свойства. RSC Adv 6: 38399–38415
Статья CAS Google Scholar
Zhang C, Madbouly SA, Kessler MR (2015) Полиуретаны на биологической основе, полученные из различных растительных масел. ACS Appl Mater Interfaces 7: 1226–1233
Статья CAS PubMed Google Scholar
Wang S-K, Sung CSP (2002) Спектроскопические характеристики модельной мочевины, уретанового соединения и диаминового наполнителя для полиуретан-мочевины. Макромолекулы 35: 877–882
Статья CAS Google Scholar
Zhang S, Ren Z, He S, Zhu Y, Zhu C (2007) FTIR-спектроскопические характеристики твердых сегментов модели полиуретан-мочевина (PUUMHS) на основе трех удлинителей диаминовой цепи. Spectrochim Acta Part A 66: 188–193
Статья CAS Google Scholar
Kima HS, Yeuma JH, Choib SW, Leec JY, Cheonga I.W (2009) Дисперсии урушиола / полиуретан-мочевины и их пленочные свойства. Prog Org Coat 65: 341–347
Артикул CAS Google Scholar
Li L, Wang X, Li Z, Bi W, Li Y, Qi Y, Dong Q (2016) Исследование кинетики синтеза и отверждения нового фторированного полиуретана с фторированными боковыми цепями, прикрепленными к мягким блокам. Новый J Chem 40: 596–605
Статья CAS Google Scholar
Paul D, Paul S, Roohpour N, Wilks M, Vadgama P (2013) Антимикробные, механические и термические исследования полиуретана, содержащего частицы серебра. J Funct Biomater 4: 358–375
Статья CAS PubMed PubMed Central Google Scholar
Байг У., Санаги М.М., Хан А.А. (2014) Получение органо-неорганического полиуретана-Al 2 O 3 анионообменный волокнистый композит и его применение в разработке мембранного электрода для определения хрома (VI) в воде. RSC Adv 4: 63831–63839
Статья CAS Google Scholar

Rostamizadeh S, Hemmasi A, Zekri N (2017) Магнитный амино-функционализированный оксид графена как новый и перерабатываемый бифункциональный нанокатализатор для синтеза пирано [3,2-c] производных пиридина без использования растворителей.Nanochem Res 2: 29–41
CAS Google Scholar
Liaw D-J (1997) Относительные физические и термические свойства полиуретановых эластомеров: влияние удлинителей цепи бисфенолов, диизоцианатов и структур полиолов. J Appl Polym Sci 66: 1251–1265
Статья CAS Google Scholar
Popescu LM, Rusti CF, Piticescu RM, Buruiana T, Valero T, Kintzios S (2013) Синтез и характеристика кислых композитов полиуретан – гидроксиапатит для биомедицинских применений.J Compos Mater 47: 603–612
Статья CAS Google Scholar
Sanchis MR, Calvo O, Fenollar O, Garcia D, Balart R (2008) Характеристика изменений поверхности и эффектов старения при обработке полиуретановой пленки азотной плазмой низкого давления. Polym Test 27: 75–83
Статья CAS Google Scholar
Лу Х., Фукс Б., Обенг Ю., Мачински С., Ричардсон К.А. (2002) Количественный анализ физических и химических изменений в поверхностях полиуретановых прокладок CMP.Mater Charact 49: 35–44
Статья CAS Google Scholar
Meera KMS, Sankar RM, Jaisankar SN, Mandal AB (2013) Физико-химические исследования сшитых полиуретановых / силоксановых пленок для гидрофобных поверхностей с помощью золь-гель процесса. J Phys Chem B 117: 2682–2694
Статья CAS Google Scholar
Чен X, Ву Л., Чжоу С., Ю Б. (2003) Полимеризация на месте и характеристика композитов полиуретан / нанокремнезема на основе полиэфира. Polym Int 52: 993–998
Статья CAS Google Scholar
Кумар Р.С., Арираман М., Алагар М. (2015) Исследования диэлектрических свойств армированных GO гибридов бисфенола- Z полибензоксазина. RSC Adv 5: 23787–23797
Статья CAS Google Scholar
Кришнадеви К., Селварадж В. (2017) Разработка эпоксидных композитов, содержащих циклофосфазен и золу рисовой шелухи, для высокоэффективных применений.Polym Bull 74: 1791–1815
Статья CAS Google Scholar
Wang Z, Nelson JK, Hillborg H, Zhao S, Schadler LS (2012) Нанокомпозит, наполненный оксидом графена, с новыми электрическими и диэлектрическими свойствами. Adv Mater 24: 3134–3137
Статья CAS PubMed Google Scholar
Pourhashem S, Vaezi MR, Rashidi A, Bagherzadeh MR (2017) Изучение антикоррозионных свойств нанокомпозитных покрытий на основе эпоксидно-графенового оксида на основе растворителя на мягкой стали.Corros Sci 115: 78–92
Статья CAS Google Scholar
Mo M, Zhao W, Chen Z, Yu Q, Zeng Z, Wu X, Xue Q (2015) Превосходные трибологические и антикоррозионные свойства полиуретановых композитных покрытий, армированных функционализированным графеном и нанолистами оксида графена. RSC Adv 5: 56486–56497
Статья CAS Google Scholar
Кришнадеви К., Селварадж В. (2016) Циклотрифосфазен и TiO 2 армированный нанокомпозит, нанесенный на пластины из мягкой стали для антибактериальной и коррозионной защиты.Appl Surf Sci 366: 148–157
Статья CAS Google Scholar
Sirajunnisa A, Fazal Mohamed MI, Subramania A, Venkatraman BR (2014) Ингибирующее действие экстракта листьев Ziziphus jujuba на щелочную коррозию алюминия. Eur J Appl Sci Technol 1: 23–31
Google Scholar
Органофункциональный силан на основе рапсового масла для защитных покрытий из нержавеющей стали
3.1. Физико-химический анализ и анализ морфологии поверхности.
a представляет СЭМ-изображение нержавеющей стали 304, обезжиренной ацетоном и химически активированной в растворе КОН. На изображении видны зерна и трещины на поверхности стали, типичные для аустенитной стали [29], что подтверждает частичное травление поверхности стали, происходящее при такой химической активации. Спектр EDS очищенной стали (а) показывает сигналы, относящиеся к железу, хрому и никелю, в то время как сигнал, относящийся к атомам углерода, очень слабый, подтверждая полное удаление органических примесей с поверхности стали.
Сканирующий электронный микроскоп (SEM Hitachi, SU3500) изображение нержавеющей стали ( a ) 304 после обработки ацетоном и горячим 10% раствором КОН; ( b ) образец R1; ( c ) образец R2; ( д ) образец R3; ( e ) образец R4; ( f ) образец R5 при увеличении 10k.
Результаты энергодисперсионной рентгеновской спектроскопии (EDS) нержавеющей стали ( a ) 304 после обработки ацетоном и горячим 10% раствором КОН; ( b ) образец R1; ( c ) образец R2; ( д ) образец R3; ( e ) образец R4; ( f ) образец R5.
Подготовленные таким образом стальные пластины использовались для испытаний антикоррозионных покрытий. Покрытия получали золь-гель методом из спиртовых растворов силана RPTMS. В результате процессов гидролиза и конденсации, протекающих в приготовленных золь-гель растворах, была получена развитая сцепленная сеть ковалентных связей Si-O-Si. Процесс конденсации между группами -ОН, происходящими на поверхности стали, и группами Si-OH и Si-O-CH 3 , присутствующими в растворе, приводит к образованию гидролитически стабильных ковалентных связей металл-O-Si, через которые покрытие прочно прикрепилось к поверхности. Более того, длинная алифатическая цепь (идущая от масла), связанная с атомом кремния, наделяла стальную поверхность гидрофобным характером.
b – f представляет собой СЭМ-изображения стальной поверхности, покрытой материалом на основе RPTMS. Эти изображения идентичны изображениям на СЭМ-изображениях голой стали (а). Образование защитных покрытий на стальной поверхности не привело к значительным изменениям поверхности стальных листов; Все исследованные образцы характеризовались растрескиванием поверхностных слоев. Только для нескольких стальных пластин с покрытием (см. D, f) изображение поверхности металла было размытым, что, скорее всего, было связано с частичным рассеиванием электронов силоксановым слоем, сформированным на поверхности металла.Образование дополнительного тонкого металлоорганического покрытия на поверхности стали было подтверждено спектрами EDS (b – f), показывающими дополнительные сигналы, исходящие от атомов углерода и кремния. Наибольшие интенсивности сигналов, отнесенных к кремнию, были зарегистрированы для покрытий, нанесенных из растворов, содержащих ТЭОС, при перемешивании в течение 72 ч (R3 и R5). Увеличение времени перемешивания растворов положительно сказалось на гидролизе и конденсации ТЭОС, в то время как покрытия, полученные в таких условиях, были богаче кремнием.К сожалению, продолжительное время перемешивания привело также к частичной конденсации RPTMS (полисилоксан отвечал за мутность раствора, и после прекращения перемешивания система становилась расслоенной), что ограничивало его вклад в образование покрытия на поверхности стали.
EDS-картирование было выполнено и проанализировано для проверки однородности распределения углерода и кремния в нанесенных покрытиях (результаты показаны в дополнительных материалах). Согласно картированию EDS, в покрытиях R1 – R4 элементы C и Si были равномерно распределены по поверхности металла (на изображениях не было темных участков или пятен, которые указывали бы на фрагменты стали, не покрытые покрытием). Только в отверстиях на поверхности стали наблюдалось скопление атомов C и Si (более светлые участки на изображениях). На изображениях EDS-картирования Si для покрытия R5 наблюдались единичные темные пятна, отмечающие области без этих атомов, что указывает на неоднородность покрытия.
Как уже упоминалось, для определения толщины нанесенных покрытий RPTMS стальные подложки царапались острой кромкой алюминиевого листа. Глубину царапин измеряли с помощью атомно-силового микроскопа (АСМ).Типичный результат с извлеченным профилем показан на. Наконец, были рассчитаны среднее значение и стандартное отклонение таких полученных значений высоты ступеньки. Результаты толщины таких проанализированных слоев представлены в.
( a ) Типичное изображение AFM поцарапанного слоя, ( b ) извлеченный профиль с подобранной ступенчатой кривой.
Таблица 2
Толщина слоев RPTMS.
Образец | Толщина слоя [нм] |
---|---|
R1 | 486 ± 31 |
R2 | 2030 ± 70 |
R503 | |
R503 | 613 ± 45 |
R5 | 800 ± 100 |
Наиболее толстое покрытие R2 получено из раствора, содержащего 20 мас.% RPTMS и TEOS, после перемешивания в течение 3 часов. Увеличение времени перемешивания раствора (покрытие R3) отрицательно сказалось на толщине покрытия. Наши предыдущие исследования [28] показали, что через 3 ч достигается наибольшая концентрация продуктов гидролиза РПТМС, после 72 ч перемешивания в растворе преобладают полисилоксаны. Кроме того, следует отметить, что в случае покрытия R2 использовалась более высокая концентрация RPTMS, что также может повлиять на толщину полученного покрытия.
Образцы стали со свежим покрытием, а также соответствующие образцы, выдержанные в течение 24 часов в дистиллированной воде, были подвергнуты FT-IR-анализу для оценки влияния состава растворов силана и времени процесса конденсации, применяемого перед их осаждением на поверхность стали, качество формируемых покрытий и их долговечность.Оценка стойкости сформированных покрытий была основана на сравнении интенсивностей характеристических полос, наблюдаемых в ИК-Фурье спектрах измеренных образцов до и после их кондиционирования в воде. Характерные полосы, наблюдаемые в спектрах всех испытанных образцов, подтверждают наличие ожидаемых функциональных групп на их поверхности. Наблюдаемые в спектрах широкие полосы с максимумами при 3300 или 3420 и, вероятно, в диапазоне 980–830 см –1 следует отнести к присутствию силанольных (Si-OH) групп в структуре сформированных покрытий.Полосы при 2928, 2850 и 1460 см -1 являются результатом валентных асимметричных, симметричных и ножничных колебаний, соответственно, связей C-H, присутствующих в метиленовых (-CH 2 -) остатках длинных алкильных цепей. Наличие карбонильных групп подтверждается наличием полосы при 1734 см -1 , характерной для валентных колебаний связи C = O. Широкая полоса в диапазоне 1250–1000 см –1 является результатом перекрывающихся колебаний, характерных для Si-O-Si, Si-OCH 3 и связей C-O.Образование связей Si-O-Si различной геометрии подтверждается также наличием полос с максимумами при 790 и 690 см -1 .
( a ) ИК-Фурье-спектры образцов стали с покрытием и ( b ) соответствующих образцов после кондиционирования в воде.
В случае обсуждаемых систем также ожидается наличие полос, характерных для связей M-O-Si. Литературные данные указывают на то, что появление полос этого типа можно ожидать в диапазоне 1000-900 см-1 [30].Точнее Seyedmonir et al. полоса при 925 см -1 отнесена к фрагменту Mo-O-Si [31], Naviroj et al. приписали слабые спектральные полосы около 963 и 950 см -1 связям Al-O-Si и Ti-O-Si соответственно [32], Миллер и Ишида приписали антисимметричное колебание валентного колебания около 965 см -1 Pb Связывание -O-Si в плюмбосилоксане [33]. Полосы около 960 см -1 также были приписаны связям Ni-O-Si и Ti-O-Si Саади и др.и Sayari et al. соответственно [34,35]. Цейтлер и Браун в своих гораздо более ранних исследованиях приписали полосы поглощения при 926 и 919 см -1 связям Ti-O-Si в тетракистрифенилсилокси- и тетракистриметилсилоксититановых производных соответственно [36].
В свете приведенных данных широкая полоса, наблюдаемая в спектрах измеряемого образца в диапазоне от 980 до 830 см −1 , может быть отнесена к колебаниям связей MO-Si, а не к колебаниям Si-OH. упоминалось выше.Тем не менее, учитывая характер образцов для измерений, метод их приготовления и специфику применяемой аналитической техники (FT-IR в режиме ATR) такое назначение было бы чрезмерной интерпретацией. Скорее всего, наличие этой полосы является результатом перекрывающихся колебаний связей Si-OH и M-O-Si.
Хорошо видно, что относительные интенсивности указанных выше полос существенно различаются в каждом спектре, что подтверждает, что состав растворов силана, а также период их гидролиза и конденсации сильно влияют на качество формируемых покрытий.Наибольшая интенсивность характеристических полос наблюдалась в спектре образца R2, что также подтверждает, что слой, сформированный на его поверхности, является наиболее толстым из всех измеренных образцов. Это связано с самой высокой концентрацией силанов в растворе, который используется для его приготовления. Интенсивность спектра, записанного для образца R3, приготовленного из раствора силана той же концентрации (см.), Но подвергнутого пролонгированному до 72 ч процессу гидролитической поликонденсации, значительно ниже.Это можно объяснить образованием плохо растворимых высокомолекулярных частиц во время длительного процесса поликонденсации, что приводит к неоднородности раствора и, как следствие, к снижению нагрузки на поверхность образца.
Сравнение интенсивностей спектров, записанных для свежих образцов (а) и подвергнутых старению в воде (б), также свидетельствует о наивысшем качестве покрытия, сформированного на поверхности образца R2. Интенсивность кондиционированного образца R2W (после погружения в воду) ниже, чем зафиксированная для образца R2, но все же самая высокая из всех замоченных образцов.Однако следует также отметить, что интенсивность спектра образца R3W после его погружения в воду практически не изменилась по сравнению с спектром образца R3, записанным до погружения в воду. Значительное уменьшение интенсивности полос, наблюдаемых в спектрах образцов R1W, R4W и R5W, а также изменение отношения относительных интенсивностей полос 2928 и 2850 см −1 к полосам 1250–1000 см −1 — результат выщелачивания RPTMS. Этот эффект наиболее выражен для образцов R1 и R1W, покрытых раствором, содержащим только RPTMS без добавления TEOS.Результаты анализа FT-IR предполагают, что нанесение раствора силана с более высокой концентрацией RPTMS и содержащего TEOS позволяет формировать более прочные (гидролитически стабильные) покрытия, возможно, с лучшими барьерными свойствами.
представляет значения углов смачивания водой (WCA) на очищенной голой и модифицированной поверхности из нержавеющей стали 304. Как следует из измеренных значений WCA, модифицированная поверхность из нержавеющей стали является гидрофильной, так как ее WCA ниже 90 °. Покрытия на основе силана, нанесенные на поверхность из нержавеющей стали 304, придают этой поверхности гидрофобный характер (R1, R2, R4).Гидрофобность поверхности объясняется влиянием длинных алифатических цепей силана RPTMS. Стальные поверхности, покрытые покрытиями R3 и R5, полученными из растворов, перемешиваемых в течение 72 часов, являются гидрофильными, поскольку их WCA ниже 90 °. Материалы на основе чистого ТЭОС (кремнезем, покрытия) гидрофильны [37,38]. Как упоминалось ранее, более длительное перемешивание растворов способствует реакции конденсации RPTMS; Вклад длинных алифатических цепей в полученное покрытие меньше, что может повлиять на более низкие значения WCA.
Таблица 3
Значения краевого угла смачивания водой (WCA) для нержавеющей стали 304 без покрытия и образцов R1–5.
Образец | WCA / Степень | |||
---|---|---|---|---|
Нержавеющая сталь 304 | 70 | |||
R1 | 96 | |||
R2 | ||||
R2 | R4 | 94 | ||
R5 | 82 |
3.
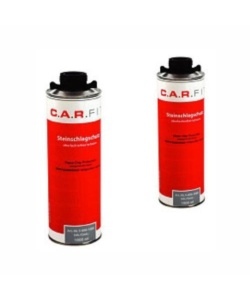
и показать результаты измерений EIS. Это графики Боде, то есть отношения фазового угла и модуля импеданса от частоты сигнала. Полученные результаты частично подтверждают физико-химический анализ и анализ морфологии поверхности. В диапазоне высокочастотных значений образец R2 показывает наименьший фазовый угол (θ), который равен почти –90 °. Это указывает на то, что покрытие, нанесенное на образец R2, является наиболее толстым и / или наиболее однородным, т.е.е., он показывает лучшие диэлектрические свойства [39,40,41,42,43,44]. Кроме того, в диапазоне низкочастотных значений фазовый угол для этой выборки самый высокий. Такая большая разница в θ, в зависимости от частоты, указывает на то, что две постоянные времени, описывающие силоксановое покрытие (первая постоянная времени) и электрохимические реакции на границе раздела пассивная оксидная пленка / электролит (вторая постоянная времени), очень хорошо разделены [39 , 40,41,43]. Это еще одно свидетельство, подтверждающее тезис о большей толщине и / или однородности покрытия, нанесенного на образец R2.Как следствие, значения модуля импеданса для этого образца самые высокие во всем диапазоне тестируемых частот (). Наличие прямой линии с наклоном (-1) () указывает на наличие постоянного параметра фазового элемента, а плато — на наличие резистивного элемента в тестируемой системе [39,40]. Как уже упоминалось, в случае покрытий с диэлектрическими свойствами, которые наносятся на металлические и стальные поверхности, фазовый угол и модуль импеданса зависят не только от толщины, но и от однородности покрытия.Если покрытие чрезвычайно пористое и способно впитывать большое количество раствора электролита, то внутри покрытия образуются проводящие пути, и значения фазового угла увеличиваются (высокочастотные значения). Однако в этом случае следует отметить некоторую сходимость между результатами испытаний EIS (тестов Боде) и результатами измерений толщины покрытия (AFM). Это относится к образцам R2, R3 и R5. Единственное исключение — образец R4, который также характеризуется низкими значениями фазового угла в высокочастотном диапазоне и фактически является одним из самых тонких.Это, вероятно, указывает на то, что это покрытие очень однородное, что также будет объяснено позже при описании результатов тестов потенциодинамической поляризации. В свою очередь, образец R5, покрытие которого было нанесено из раствора, содержащего самую низкую добавку RPTMS и самое продолжительное время перемешивания, показывает самые высокие значения фазового угла, что связано как с меньшей толщиной, так и с худшей однородностью. В случае нержавеющей стали 304 фазовый угол, а также модуль импеданса уменьшаются и увеличиваются, соответственно, при уменьшении значения частоты.Следовательно, в этом случае наблюдается одна постоянная времени, описывающая наличие электрохимической реакции [44]. Кроме того, отсутствие силоксанового покрытия означает, что в высокочастотном диапазоне появляется плато (). Это определение сопротивления электролита. На графиках Боде (−θ vs f), полученных для образца R4, наблюдается наличие трех петель (пиков), в том числе двух (едва заметных) в диапазоне высокочастотных значений (~ 100 кГц – 100 Гц). Это не обязательно указывает на наличие трех постоянных времени.Скорее всего, появление двух вышеупомянутых петель (высокочастотные значения) связано с самим силоксановым покрытием и их наличие является результатом структуры этого покрытия. Кроме того, для образца R5 характерна только одна петля (пик) в диапазоне высоких частот. Хотя значения θ в этом случае самые высокие. Как было сказано выше, слои на образцах R4 и R5 являются одними из самых тонких. Кроме того, на это явление влияют как время перемешивания раствора, так и количество добавки RPTMS.В каждом из этих образцов использовалось минимальное количество RPTMS. Следует отметить, что покрытия, нанесенные из растворов, в которых использовалось большее количество RPTMS, характеризуются наибольшими значениями модуля импеданса () в диапазоне наименьших значений частоты.
Графики Боде (угол сдвига фаз в зависимости от частоты) для нержавеющей стали 304 и образцов R1–5.
Графики Боде (модуль сопротивления в зависимости от частоты) нержавеющей стали 304 и образцов R1–5.
Электрохимический анализ импедансной спектроскопии позволяет согласовать электрические эквивалентные схемы (EEC) с тестируемыми электрохимическими системами [39,40].показывает графики Найквиста. Символами обозначены экспериментальные данные, а линиями — данные, полученные в результате подгонки EEC. Степень совпадения линий и экспериментальных точек говорит о правильности выбора ЭВП. a – c показаны EEC, которые были согласованы с результатами испытаний EIS для немодифицированной нержавеющей стали 304 и образцов R1–5. Элементами, составляющими представленные схемы, являются резисторы (R), параметры элемента постоянной фазы (Q) и элемент диффузии (): R s : некомпенсированное эквивалентное последовательное сопротивление раствора электролита, Q dl : параметр элемента постоянной фазы, описывающий двойной электрический слой, R ct : сопротивление переносу заряда, Q c : параметр элемента постоянной фазы, описывающий силоксановое покрытие, R c : сопротивление силоксанового покрытия и Ϻ: элемент, который представляет собой ограниченное линейное диффузионное явление.Следует отметить, что параметр элемента постоянной фазы (Q) заменяет конденсатор, в то время как полное сопротивление элемента постоянной фазы определяется выражением [39,40,45,46]:
где j, ω и α — мнимые числа, угловая частота и коэффициент, отражающий емкостную дисперсию, соответственно. Согласно уравнению (1), элемент постоянной фазы выражает неидеальное поведение конденсатора, то есть является отражением емкостной дисперсии на границе раздела электролит / электрод, и поэтому параметр Q больше не следует идентифицировать как емкость, когда α <1.Это связано, среди прочего, с химической неоднородностью тестируемой поверхности или даже с адсорбцией различных типов ионов. По данным Yuan et al. [45] и Hirschorn et al. [46], существует возможность оценить эффективную емкость покрытия, а также двойного электрического слоя на основе параметра постоянного фазового элемента и значений сопротивления. Однако в дальнейших частях рукописи значения эффективных емкостей не сравниваются, поэтому они не определялись.В этой ситуации только значения сопротивлений и α для конкретных параметров элемента с постоянной фазой являются релевантными для описания результатов испытаний EIS. Таким образом, значения Q представлены как F s (α − 1) , что согласуется с Yuan et al. [45] и Hirschorn et al. [46].
( a — d ) Графики Найквиста нержавеющей стали 304 и образцов R1–5. Исходные данные (символы) и подогнанные данные (сплошные линии).
Электрические эквивалентные схемы (EEC), соответствующие данным EIS для ( a ) нержавеющей стали 304 без покрытия, ( b ) образцов R1, R3, R4, R5 и ( c ) R2.
На поверхности нержавеющей стали 304, подвергнутой электрохимическим испытаниям, образовалась пассивная оксидная пленка. Согласно Барсукову и Макдональду [40], при выборе EEC для сталей или металлов, содержащих пассивные оксидные слои, следует учитывать постоянный параметр фазового элемента и сопротивление этих слоев, а также образование двойного электрического слоя в электролите / Пассивная оксидная пленка и пассивная оксидная пленка / элемент подложки. Kocijan et al.[47] описали четыре наиболее часто используемых типа ЭЭП с учетом двух постоянных времени и одной, которая характеризует присутствие оксидного слоя и двойного электрического слоя на границе раздела пассивная оксидная пленка / элемент подложки. Учитывая работу Барсукова и Макдональда [40], было решено использовать схему, содержащую элементы, описывающие формирование двойного электрического слоя на границе раздела электролит / пассивная оксидная пленка. Это получено из графика Найквиста, который указывает на наличие одной постоянной времени. Это должна быть первая возможная постоянная времени, видимая в высокочастотном диапазоне. В этом случае во всем частотном диапазоне видна только одна постоянная времени. Это связано с методикой подготовки стальной поверхности. При обработке стали не применялась механическая очистка. Кроме того, травление в щелочных растворах позволяет удалять загрязнения, сохраняя при этом пассивную оксидную пленку на поверхности стали. Поэтому уже в начале электрохимических испытаний на поверхности стального образца присутствовала пассивная оксидная пленка.Это также подтверждается результатами анализа EDS (наличие кислорода). Использование двух постоянных времени обычно касается ситуации, когда оксидный слой начинает формироваться в растворе электролита, в котором проводятся испытания [47]. Затем на графиках Найквиста в диапазоне высокочастотных значений появляется контур полукруга, а на графиках Боде, точнее на графиках, изображающих зависимость между фазовым углом и частотой, появляются две петли, т.е. диапазон значений высоких и низких частот.
EEC для модифицированных образцов содержит параметр постоянного фазового элемента (Q) и сопротивление (R) силоксановых покрытий и электрохимические явления на границе раздела электролит / пассивная оксидная пленка [44]. Силоксановые покрытия пористые, поэтому они способны абсорбировать определенное количество электролита. Следовательно, такой способ представления схемы имеет физический смысл. Элемент Ϻ представляет собой конкретное явление диффузии, то есть ограниченную линейную диффузию с отражающими граничными условиями [39,40,48,49,50,51]:
Z (jω) = Rdcoth (τdjω) τdjω
(2)
где R d и τ d — сопротивление диффузии и постоянная времени диффузии соответственно.τ d равно L 2 / D, где L и D представляют собой последовательность толщины диффузионного слоя и коэффициента диффузии. Обычно элемент импеданса Варбурга, который определяет полубесконечную линейную диффузию, используется для описания диффузионных явлений, происходящих в электрохимических системах. Использование этого элемента оправдано, если в определенном диапазоне частот точки на графике Найквиста образуют линию, наклон которой равен (–1). Если в исследуемой электрохимической системе происходят фарадеевские реакции, такая линия обычно появляется в среднем и низкочастотном диапазоне.Однако, помимо элемента импеданса Варбурга, существуют другие элементы, которые можно использовать для описания диффузии, включая элементы, описывающие ограниченную линейную диффузию (диффузия конечной длины). В случае результатов испытаний EIS элемент использовался для описания характера отдельных образцов с нанесенными покрытиями. Стоит отметить, что все образцы, на которые были нанесены покрытия, имеют лучше или хуже развитый полукруг в высокочастотном диапазоне. Тогда в диапазоне среднечастотных значений линия принимает диффузный характер, а в диапазоне низкочастотных значений описывает наличие постоянного параметра фазового элемента.Эта ситуация, помимо первой постоянной времени (высокочастотный диапазон), может быть описана наличием диффузионного элемента и параметра постоянных фазовых элементов. Следовательно, в этой ситуации наиболее подходящий выбор — это тот, который описывает ограниченную линейную диффузию. Характер графиков Найквиста и выбор элемента поддерживается, среди прочего, Ласией [39] и Бегуином и Фронковяком [48]. показывает значения всех компонентов выбранного EEC. Образец R2, содержащий самое толстое (AFM) силоксановое покрытие, характеризуется наивысшим значением сопротивления покрытия (R c ), что равносильно лучшим диэлектрическим свойствам.Полукруг в диапазоне высокочастотных значений показывает наибольший диаметр (а, б). Кроме того, параметр Q имеет наименьшее значение, а параметр α — наибольшее значение. В средне- и низкочастотном диапазоне имеется только прямая линия, наклон которой соответствует наличию постоянного параметра фазового элемента. Следовательно, элемент, описывающий диффузию массы, не нужен. В других случаях, то есть при более длительном перемешивании раствора (72 часа) и минимальном добавлении RPTMS, покрытия становятся более тонкими и менее однородными, поэтому возникают диффузионные явления, связанные с наличием большого количества плохо растворимого, высокомолекулярные коллоидные частицы.
Однако модель ограниченной линейной диффузии с отражающими граничными условиями в основном применяется к проводящим полимерам, тонким пассивным оксидным пленкам, системам, основанным на явлениях интеркаляции и внедрения, тонким пленкам раствора между электрохимически активным электродом и неактивными поверхностями [39,40,48,49, 50,51]. Подводя итог, ограниченная линейная диффузия с отражающими граничными условиями основана на предположении об отсутствии градиента концентрации, то есть при x = L градиент концентрации равен нулю.Образцы R1, 3, 4 и 5 показывают типичный диффузный характер на промежуточных частотах (). Форма кривых Найквиста ясно указывает на модель ограниченной линейной диффузии с отражающими граничными условиями. Это, безусловно, связано с нержавеющей сталью и наличием пассивной оксидной пленки. Как уже было сказано, нанесенные покрытия являются пористыми, поэтому процесс электрохимической коррозии протекает под покрытием. На поверхности пассивной оксидной пленки образуется слой продуктов коррозии.Со временем происходит отслоение покрытия [18]. Можно сказать, что оксидная пленка нарастает. Продуктом этих процессов является слой, состоящий из оксидов / гидроксидов металлов, ионов и раствора электролита. Это несколько пористый слой, заполненный раствором электролита. Прежде всего, это слой, проводящий электрический заряд. Конечно, модель ограниченной линейной диффузии (отражающие границы) не является идеальной моделью для этого типа электрохимической системы, однако в данный момент времени и на этой стадии деградации поверхности нержавеющей стали, покрытой этим типом покрытия. , эта модель может успешно использоваться и является наилучшим выбором.По мере реакции раствора электролита характеристики импеданса изменятся. Деградация покрытия продолжится. Под покрытием образуется гораздо больше продуктов коррозии. Покрытие будет заполнено большим количеством раствора электролита и большим количеством продуктов коррозии в виде ионов и оксидов / гидроксидов металлов.
Характеристика импеданса в диапазоне значений промежуточной частоты будет указывать на наличие диффузионных явлений, которые затем могут быть описаны с помощью элемента импеданса Варбурга или элемента импеданса для ограниченной линейной диффузии с пропускающими граничными условиями [39,40,48].По результатам можно сделать вывод, что слои продуктов коррозии (под покрытием) относительно тонкие. Об этом свидетельствует низкое значение постоянной времени диффузии τ d по сравнению с сопротивлением диффузии R d . Стоит отметить, что наибольшее значение R d указывает образец R4, то есть образец, который, вероятно, имеет чрезвычайно однородное покрытие. Однородность покрытия (R4) и его толщина (R2) влияют на количество и качество продуктов коррозии, образующихся под покрытием.Полученный слой изделий более плотный. Кроме того, меньше ионов и оксидов / гидроксидов металлов появляется в слое, а также в его окрестностях. Из-за этого процесс диффузии характеризуется высоким сопротивлением (R4) или его можно просто не учитывать (R2). Учитывая явление диффузии на границе раздела покрытие / пассивная оксидная пленка, значения α для параметра Q dl значительно отличаются от единицы. Постоянная времени элемента постоянной фазы рассредоточена, и Q dl не может быть определен как емкость.Также стоит отметить, что наибольшее значение α показывает параметр Q dl для образца R2, т.е. образца с достаточно толстым покрытием, поэтому нет необходимости учитывать использование ограниченной линейной диффузии. элемент Ϻ.
Таблица 4
Значения компонентов резистора (R), элемента с постоянной фазой (Q) и ограниченной линейной диффузии (R d , τ d ) различных электрических эквивалентных схем (EEC) соответствуют результатам EIS для 304 нержавеющая сталь и образцы Р1–5.
Образец | Q c · 10 −6 (F s (α − 1) ) | α | R c (кОм) | R d (Ом) | τ d (с) | Q dl · 10 −6 (F s (α − 1) ) | α | R ct (кОм) | Нержавеющая сталь 304 | — | — | — | — | — | 43.![]() | 0,92 | 10,390 | ||||
---|---|---|---|---|---|---|---|---|---|---|---|---|---|---|---|---|---|---|---|---|---|
R1 | 0,84 | 0,83 | 43,40 | 15,193 | 0,94 | 11,18 | 0,54 | 0,54 | — | — | 5,88 | 0,66 | — | ||||||||
R3 | 0,58 | 0,84 | 13,58 | 5205 | 0,40 875166 | 0,56 | — | ||||||||||||||
R4 | 0,39 | 0,81 | 17,20 | 70,124 | 6,54 | 24,53 | 0,56 | 0,56 | 0,56 | 6,92 | 0,001 | 130,40 | 0,58 | — |
показывает результаты испытаний потенциодинамической поляризации (PP), а также собирает значения потенциалов коррозии (E corr ) (плотности тока коррозии) j corr ), коэффициенты наклона катодных (–β c ) поляризационных кривых и потенциалов питтинга (E pitt ), полученных в результате этих испытаний. Полученные результаты частично подтверждают результаты измерений EIS, т.е. образец R2 показывает наибольшее значение E corr . Более того, все образцы, поверхности которых были модифицированы силоксановыми покрытиями, характеризуются более высокими значениями E corr , т.е. они более благородны по сравнению с немодифицированной нержавеющей сталью 304. Однако образцы с нанесенными силоксановыми покрытиями показывают более высокие значения j corr . Как упоминалось выше, пористые силоксановые покрытия способны абсорбировать раствор электролита, что подразумевает образование проводящих путей внутри этих покрытий.Поэтому, скорее всего, значения плотности тока коррозии высоки. Однако значения отдельных образцов настолько малы и похожи друг на друга, что трудно найти какую-либо разумную связь между методом приготовления золь-гель раствора и j corr данного образца. Единственная проявляющаяся закономерность — это то, что образец, на который нанесено наиболее толстое покрытие, показывает наименьшее значение j corr . В других образцах следует учитывать наличие крупных, плохо растворимых коллоидных частиц, которые делают покрытия более тонкими.Следовательно, значения плотности тока коррозии становятся выше. Это связано с более высоким отношением поглощенного количества электролита к толщине покрытия, а также с наличием / образованием слоя продуктов коррозии под покрытиями.
Потенциодинамические поляризационные кривые для нержавеющей стали 304 без покрытия и образцов R1–5.
Таблица 5
Потенциалы коррозии (E corr ), плотности тока коррозии (j corr ), наклон катодных (β c ) кривых поляризации и значения потенциалов питтинга (E pitt ) для чистой нержавеющей стали 304 сталь и образцы Р1–5.
Образец | E corr (мВ относительно SCE) | j corr (нА см −2 ) | −β c (мВ) | E мВ по сравнению с SCE) | ||||||
---|---|---|---|---|---|---|---|---|---|---|
Нержавеющая сталь 304 | −93 | 3,80 | 40 | 410 | ||||||
R1 | −26 | 5,00 | R2 | 32 | 4.![]() | 125 | 600 | |||
R3 | −65 | 6,00 | 59 | 495 | ||||||
R4 | −36 | 6,10 | 6,10 | −17 | 4,90 | 60 | 460 |
Как упоминалось ранее, значения фазового угла и модуля сопротивления в высокочастотном диапазоне зависят от толщины и однородности покрытия.Эту закономерность также можно отнести к наклону катодных поляризационных кривых. Учитывая, что эти покрытия являются пористыми, через их структуру происходит массоперенос (раствор электролита и кислород) [45]. Таким образом, можно сделать вывод, что эти покрытия не полностью изолируют стальную поверхность. Кроме того, тестируемые системы находятся не в активированном, а в диффузном контроле. Это относится к обеим поляризационным кривым. Катодная кривая иллюстрирует реакцию восстановления кислорода.Наклон этой кривой указывает степень ингибирования транспорта кислорода конкретным слоем. Следовательно, наклон кривой катодной поляризации является показателем толщины и однородности покрытия. Наибольшие значения наклона характерны для образцов R2 и R4, т.е. для самого толстого и одного из самых тонких (AFM) покрытий соответственно. Отсюда следует, что толщина и однородность покрытия одинаково влияют на наклон катодной поляризационной кривой. На основании этого можно сделать вывод, что покрытие на образце R4 чрезвычайно однородное, что подтверждается результатами EIS и потенциодинамических поляризационных испытаний.Немодифицированная сталь показывает наименьшее значение наклона кривой. Это соответствует ожиданиям и является отражением наличия пассивной оксидной пленки, которая намного тоньше, чем покрытия, содержащие RPTMS.
Тем не менее, самым большим преимуществом используемых защитных покрытий является ингибирование процессов окисления на поверхности нержавеющей стали 304. Явления электрохимической коррозии стали, а также металлических элементов включают сопряженные реакции окисления и восстановления (условия разомкнутой цепи).Оба процесса протекают на поверхности корродирующего материала и оба влияют на скорость всего явления. Хотя скорость электрохимической коррозии, выраженная величиной плотности тока коррозии как для модифицированных, так и для немодифицированных стальных образцов, радикально не отличается, при подавлении реакции окисления заметны значительные различия. А именно, для образцов, модифицированных силоксановыми покрытиями, коэффициенты наклона анодных (β a ) поляризационных кривых стремятся к бесконечности (β a → ∞), а коэффициент наклона β a для стали без покрытия равен ~ 1 В.Поэтому нет необходимости включать эти значения в [52]. Понятно, что анодный процесс и, следовательно, анодные поляризационные кривые находятся под диффузным контролем. Это диффузия массы, но в данном случае это касается компонентов стали (Fe, Cr, Ni) в виде ионов и гидроксидов, которые слабо связаны с поверхностью стали [45,53]. Подводя итог, это демонстрирует ингибирование реакции растворения поверхности из нержавеющей стали 304, модифицированной силоксановыми покрытиями. Это также подтверждается значениями потенциала питтинга (E pitt ).В случае нержавеющей стали 304 E pitt равен примерно 0,4 В относительно SCE, что согласуется с нашими предыдущими исследованиями [44]. Образец R1 является единственным образцом, который характеризуется более низким значением E Pitt по сравнению с немодифицированной сталью. Это образец с самым тонким покрытием. Наибольшее значение E pitt было получено для образца R2, который модифицирован наиболее толстым и, вероятно, относительно однородным покрытием. На это указывают все физико-химические, морфологические и электрохимические исследования, включая потенциодинамическую поляризацию.Хотя толщина этого покрытия не оспаривается, можно спорить о его однородности. Стоит отметить, что увеличение плотности тока происходит уже при потенциале ~ 0,35 В относительно нас. Однако полное неконтролируемое увеличение плотности тока, соответствующего потенциалу питтинга, происходит при потенциале 0,6 В, что является самым высоким значением среди всех испытанных образцов. Второе по величине значение E pitt обозначено образцом R4, который содержит одно из самых тонких покрытий.Однако можно предположить, что это довольно однородное покрытие, которое, помимо высокого значения E pitt и результатов испытаний EIS, также указывает на высокое | –β c | коэффициент наклона. Следует также отметить, что поляризационные испытания, направленные на определение значений потенциалов точечной коррозии, являются отличным показателем долговечности покрытия, т. Е. Моделируют ускоренное длительное испытание на долговечность покрытия в агрессивной водной среде.
Моделирование сверхразветвленного алкидного / сферического нанокомпозита ZnO на основе подсолнечного масла для механических и антикоррозионных применений
rsc.org/schema/rscart38″> Подходы к разработке усовершенствованных наноматериалов с гиперразветвленной архитектурой и отсутствием летучих органических соединений (ЛОС) привлекли значительное внимание.В этом исследовании экологически чистые сверхразветвленные алкидные смолы для механических и антикоррозионных покрытий с высоким содержанием твердых веществ были успешно синтезированы на основе подсолнечного масла (SFO) с использованием метода полиэтерификации . Эти смолы характеризуются энергоэффективным синтезом полимеров, отсутствием гелеобразования, высокой функциональностью и низкой вязкостью. Процесс химического осаждения был использован для изготовления сферических наноструктур оксида цинка (ZnO) с контролируемым диаметром и морфологией.С помощью метода ex situ была изготовлена серия конформных, новых, недорогих сверхразветвленных алкидных / сферических нанокомпозитов ZnO на основе SFO. Были распределены различные концентрации нанонаполнителя, чтобы установить синергетический эффект на характеристики материалов в микробинарном масштабе. Характеристики нанокомпозитов, включая молекулярную массу, кислотное и гидроксильное число приготовленных алкидных смол, одновременно оценивались с помощью различных стандартных тестов. Нанокомпозиты также были подвергнуты различным испытаниям для определения их поверхностной адгезии и механических свойств, таким как испытания на ударопрочность, Т-образный изгиб, поперечный разрез и сопротивление истиранию.Кроме того, были оценены физико-механические свойства, антикоррозийное поведение, термическая стабильность и клеточная цитотоксичность изготовленных материалов. Антикоррозионные свойства нанокомпозитов были исследованы путем испытаний в солевом тумане в 5 мас.% NaCl. Результаты показывают, что хорошо диспергированные наносферы ZnO (0,5%) внутри сверхразветвленной алкидной матрицы улучшают долговечность и антикоррозионные свойства композитов; таким образом, они потенциально могут применяться в экологически чистых покрытиях поверхностей.
Коричневая антикоррозионная краска на масляной основе, 250 рупий / квадратный фут Square 1 Worldwide Pvt. Ltd.
Коричневая антикоррозионная краска на масляной основе, 250 рупий / квадратный фут Square 1 Worldwide Pvt. ООО | ID: 20777638512Уведомление : преобразование массива в строку в /home/indiamart/public_html/prod-fcp/cgi/view/product_details.php в строке 290
Спецификация продукта
Цвет | Коричневый |
Тип грунтовки на основе | Масляная основа |
Форма | Жидкость |
Глянцевая поверхность | 9075 907 907 Глянцевая 9130
Описание продукта
Нацеленные на успешный рост в этой области, мы способствуем предложению превосходного качества Epoxy Metal Primer Paint .
Заинтересовал этот товар? Получите последнюю цену у продавца
Связаться с продавцом
Изображение продукта
О компании
Год основания 2008
Юридический статус компании с ограниченной ответственностью (Ltd.