Измерение толщины металла через красочное покрытие
Применение: Измерение остаточной толщины стенок металлических труб, цистерн, обшивки корпусов судов и других конструкций через лакокрасочное покрытие.
Проблематика: В нефтехимической промышленности, приходится часто измерять остаточную толщину корродированных металлов, через одно или несколько слоев покрытия (чаще всего неметаллического). При использовании стандартных ультразвуковых толщиномеров, наличие краски или другого покрытия создает многочисленные погрешности в измерениях, часто увеличивая значение толщины металла на величину более чем в два раза превосходящую толщину красочного покрытия; это вызвано относительно малой скоростью распространения звука в краске. Есть два решения данной проблемы: измерение толщины в режиме Эхо-эхо и измерение в режиме THRU-COAT.
Оборудование: Режимы Эхо-эхо и THRU-COAT доступны в двух коррозионных толщиномерах Olympus: 38DL PLUS и 45MG.
Раздельно-совмещенные преобразователи на протяжении долгого времени являются отраслевым стандартом для измерения толщины корродированных объектов, подходят для работы на грубых поверхностях и при наличии питтинговой коррозии. Одноэлементные преобразователи можно рекомендовать для измерения металлических изделий с гладкой окрашенной поверхностью, где требуется высокая точность измерения.
Теория: Скорость распространения продольных ультразвуковых волн в стали обычно составляет 5,900 м/м, тогда как скорость звука в красочном (или аналогичном) покрытии – обычно менее 2,500 м/с. При измерении общей толщины окрашенных стальных изделий с помощью стандартного ультразвукового толщиномера, прибор ошибочно измеряет толщину покрытия со скоростью распространения звука в стали; это означает, что толщина красочного покрытия будет как минимум в 2,35 раза больше реального значения (соотношение двух скоростей звука). В случае с толстым покрытием и малыми допустимыми отклонениями, ошибка, допущенная при измерении красочного покрытия, может составлять значительную часть общего измерения. Для решения данной проблемы, следует полностью исключить красочное покрытие при расчете или измерении толщины изделия.
Суть метода Эхо-эхо заключается в измерении временного интервала между двумя последующими донными эхо-сигналами, представляющими траекторию звуковой волны «туда-обратно» через тестируемый материал. При измерении окрашенных металлических изделий, эти многочисленные донные эхо-сигналы возникают только в металле, не в покрытии, поэтому интервал между любой парой сигналов (донными эхо-сигналами 1 и 2, донными эхо-сигналами 2 и 3, и т.д.) представляет толщину металла, без учета толщины красочного покрытия.
Запатентованная технология THRU-COAT позволяет определить время прохождения звука туда-обратно в покрытии. Этот временной интервал используется для расчета и отображения толщины покрытия, а при вычислении этого интервала из общего значения толщины, прибор отображает толщину металла.
Каждый из представленных методов измерения имеет свои недостатки и преимущества. Выбирайте наиболее подходящий метод для конкретного приложения:
Преимущества Эхо-эхо:
• Работает с широким спектром стандартных преобразователей.
• Измерения можно выполнять при высоких температурах (до 500 C) с помощью специальных преобразователей.
Недостатки Эхо-эхо:
• Требует многочисленных донных эхо-сигналов, которые могут отсутствовать в сильно корродированных металлах.
• Диапазон измеряемых толщин может быть более ограничен, по сравнению с Thru-Coat.
Преимущества THRU-COAT:
• Широкий диапазон измеряемых толщин, обычно от 1 мм до более 50 мм в стали.
• Требуется только один донный эхо-сигнал.
• Может более точно измерять минимальную остаточную толщину металла в случае питтинговой коррозии.
Недостатки THRU-COAT:
• Покрытие должно быть неметаллическим, толщиной не менее 0,125 мм.
• Поверхность покрытия должна быть относительно ровной и гладкой.
• Требует использования одного из двух специализированных преобразователей.
• Максимальная температура поверхности должна быть приблизительно 50 C.
Процедура: Процедуры активации и выполнения измерений в режимах Эхо-эхо и THRU-COAT с помощью толщиномеров 38DL/45MG и соответствующих преобразователей подробно описываются в руководствах по эксплуатации данных приборов. Руководства по эксплуатации также включают подробное описание процедуры калибровки скорости звука, настройки усиления и игнорирования сигнала (где это необходимо).
Диапазонизмерений Thru-Coat: Функция THRU-COAT с преобразователями D7906-SM или D7908 используется только для измерения металлических покрытий (краска, эпоксидная смола) толщиной 0,12 мм и более. Если, при измерении стальных изделий с покрытием, величина покрытия не отображается, это значит, что толщина покрытия находится ниже минимального предельного значения толщины, измеряемого в режиме THRU-COAT, или не может быть измерена данной функцией.
Диапазон измеряемых толщин (металлов) в режиме THRU-COAT находится в пределах от 1 мм до более 50 мм, в зависимости от акустических свойств металла и состояния внутренней поверхности.
Диапазон измерений Эхо-эхо: В режиме Эхо-эхо, диапазон измеряемых толщин зависит от выбора преобразователя и типа толщиномера, а также от акустических свойств измеряемого металла и состояния поверхности. Поскольку в режиме измерения Эхо-эхо требуется как минимум два донных эхо-сигнала, в некоторых случаях данный режим не работает, – например, при измерении сильно корродированных металлических изделий с неровной поверхностью, или материалов с высокой степенью рассеяния или ослабления ультразвука, где второй эхо-сигнал может не проявиться. В таких случаях, следует использовать технологию THRU-COAT.
При использовании толщиномеров 38DL и 45MG типичный диапазон измерения в режиме Эхо-эхо составляет:
Тип преобразователя | Диапазон измеряемых толщин* | |
D798 | от 1,5 до 7,50 мм | |
D790/D791 | от 2,0 до 50 мм | |
D797 | от 12,5 до 125 мм | |
М201 | от 1,25 до 12,5 мм |
Измерение толщины резиновых лент и покрытий
Назад к ресурсамТолщину резиновых лент и резиновых покрытий бывает сложно измерить с помощью традиционных механических средств. Имейте в виду, что измерение толщины резинового покрытия на некоторых материалах может потребовать специальных настроек прибора для обеспечения точности показаний. Оборудование: Для измерения толщины резиновых лент/покрытий мы рекомендуем использовать прецизионные толщиномеры 38DL PLUS и 45MG с ПО для одноэлементных ПЭП. Эти портативные толщиномеры, в комбинации с соответствующими преобразователями (частота от 2,25 до 20 МГц), способны измерять резиновые материалы в диапазоне толщин от 0,2 до 6 мм. |
Продукты, используемые для этой цели
Ультразвуковой портативный толщиномер 45MG оснащен всеми необходимыми функциями и программными опциями. Этот уникальный прибор совместим со всеми одноэлементными и раздельно-совмещенными преобразователями Olympus и способен решить любые задачи толщинометрии.
38DL PLUS — усовершенствованный ультразвуковой толщиномер. Использует раздельно-совмещенный ПЭП для выявления внутренней коррозии, и работает в режимах THRU-COAT (измерения через покрытие) и Эхо-эхо. Используется с одноэлементными ПЭП для высокоточного измерения толщины тонких, слишком толстых или многослойных материалов.
Magna-Mike представляет собой портативный толщиномер, использующий простой магнитный метод для высокоточного измерения толщины немагнитных и тонких материалов (пластиковые бутылки).
Sorry, this page is not available in your country
No related products
Sorry, this page is not available in your countryLet us know what you’re looking for by filling out the form below.
№ 1 — Определение толщины сырого слоя | А. Калиброванная гребенка | — | Измерения дают приблизительное значение толщины сырого слоя |
В. Колесный толщиномер | Погрешность ±2,5% + 1 мкм | Метод можно использовать в лаборатории и на месте окрашивания | |
С. Взвешивание для измерения толщины сырого слоя на свежеокрашенной поверхности | Воспроизводимость ±15 мкм | Метод № 1С можно использовать также для определения толщины высушенного покрытия, но только в лаборатории | |
№ 2 — Определение толщины высушенного покрытия путем расчета соотношения между массой и площадью высушенного покрытия | Применяют для мягких покрытий, толщина которых не может быть измерена приборами с зажимными элементами или измерительным стержнем | Измерения дают неточные результаты | Обеспечивает проверку, когда значение толщины находится в заданных пределах.![]() |
№ 3 — Измерение толщины высушенного покрытия приборами, использующими механический контакт | А. Микрометрический метод. Применяют для измерений на практически плоских пластинах и окрашенных поверхностях | Погрешность ±2 мкм. Воспроизводимость ±30% — для тонких покрытий; ±20% — для толстых покрытий | Покрытие должно быть достаточно твердым, чтобы противостоять вдавливающему усилию при контакте с зажимами микрометра. Покрытие разрушается в процессе испытания. Если пленка не отделена от основания, толщина покрытия должна быть более 25 мкм |
В. Метод с применением многооборотного индикатора. Испытуемые пластины или окрашенные поверхности должны быть практически плоскими или иметь кривизну в одном направлении | Воспроизводимость ±10% с нижним пределом 2 мкм | Покрытие должно быть достаточно твердым, чтобы противостоять вдавливающему усилию при контакте с измерительным стержнем | |
№ 4 — Измерение толщины высушенного покрытия профилометрическим методом | Рекомендуется в качестве арбитражного метода для практически плоских окрашенных поверхностей | Воспроизводимость ±10% с нижним пределом 2 мкм | Покрытие должно быть достаточно твердым, чтобы противостоять вдавливающему усилию пера профилометра.![]() |
№ 5 — Измерение толщины высушенного покрытия с использованием микроскопа | А. Микроскопическое исследование поперечного сечения. Рекомендуется как арбитражный метод измерения для покрытий на основаниях со сложным профилем, например на поверхностях после дробеструйной обработки | Погрешность ± 2 мкм. Воспроизводимость ±10% | Участок окрашенного изделия вырезают и закрепляют на смоле. Покрытие разрушается в процессе испытания |
В. Метод вырезки клина. Метод не применяют к хрупким и рыхлым покрытиям. Методы А и В можно применять при определении толщины отдельных слоев в многослойном покрытии | Воспроизводимость ±10% с нижним пределом 2 мкм | Чтобы вырезать пленку, нужен специальный режущий инструмент или сверло. Покрытие в процессе измерения разрушается | |
С.![]() | Воспроизводимость ±10% | Для исследования профиля покрытия применяют специальный микроскоп (микроскоп светового сечения). Прозрачные покрытия не разрушаются | |
№ 6 — Магнитные методы | Для магнитных металлических оснований: | ||
А. Магнитоиндукционный принцип | Погрешность ±2% + 1 мкм. Воспроизводимость ±10% | Покрытие должно быть достаточно твердым, чтобы выдерживать давление датчика | |
В. Принцип отрыва постоянного магнита | Погрешность ±5% + 1 мкм | Измерения можно проводить на месте окрашивания | |
№ 7 — Метод вихревых токов | Для немагнитных металлических оснований | Погрешность ±2% + 1 мкм Воспроизводимость ±10% | Приборы действуют по принципу вихревых токов.![]() |
№ 8 — Неконтактные методы | Применяют, когда контакт инструмента с покрытием нежелателен. Применяют для измерений на практически плоских окрашенных поверхностях | Воспроизводимость ±10% | В приборах используют принцип обратного рассеяния b-частиц (метод № 8А) или явление рентгеновской флуоресцентности (метод № 8Б). Для получения точных результатов покрытия должны быть гомогенными |
№ 9 — Гравиметрический (растворения) метод | Применяют для измерения толщины покрытий на основаниях с неоднородным профилем (например стальные пластинки после дробеструйной обработки) и для покрытий на полимерных основаниях, если последние не подвержены действию лакокрасочных растворителей | — | Массу покрытия измеряют путем растворения покрытия без растворения основания.![]() |
№ 10 — Определение толщины высушенного покрытия на стальных основаниях, подвергнутых дробеструйной обработке | Для высушенных покрытий на магнитных металлических основаниях с шероховатой поверхностью (после дробеструйной обработки) | — | В приборах используют явление магнитной индукции. Измерения можно проводить на месте окрашивания. В некоторых случаях можно также применять метод № 5А или метод № 9 |
Примечание — Ряд из указанных в таблице методов можно использовать для измерения толщины свободных пленок. |
Акустические Контрольные Системы — Отчет по измерению толщины основного металла через лакокрасочные и компаундные покрытия с использованием ультразвукового толщиномера А1210
Отчет: Загрузить
Продукция: Ультразвуковой толщиномер А1210
Цель исследования: Оценка возможности измерений толщины металлов через покрытия, пропускающие ультразвук и имеющие хорошую адгезию с металлом.
Объект исследования: Сегмент стальной пластины с лакокрасочным покрытием, нанесённым с одной стороны, и компаундным – с другой.
Используемый инструмент для проведения исследования: Ультразвуковой толщиномер А1210 с рабочим режимом А-СКАН и раздельно-совмещенный преобразователь D1771 с рабочей частотой 4 МГц.
Вспомогательные материалы: Специализированный гель для проведения толщинометрии различных конструкционных материалов – «АКС-гель».
Проведение исследования
Проводя такие измерения, следует помнить, что граница покрытие/металл может давать сигнал, амплитуда которого может быть весьма значительна, и этот сигнал может быть принят за основной. Чтобы исключить ложные измерения и повысить точность измерений, применяется измерение между двумя максимумами сигнала, начиная со второго импульса.
Примечание: Первый импульс, определяемый покрытием, может быть очень мал и почти не различим.
1. Рассмотрим измерение толщины стальной пластины, имеющей основную толщину стенки 8 мм. С одной стороны пластины нанесено лакокрасочное покрытие толщиной 0,5 мм, с другой – компаундное толщиной от 2 до 3 мм (рис.1 и рис.2).
Рис.1. Сегмент стальной пластины с нанесённым лакокрасочным покрытием толщиной 0,5 мм.
Рис.2. Сегмент стальной пластины с нанесённым компаундным покрытием толщиной от 2,0 до 3,0 мм.
Измерения проводятся с помощью подключённого к электронному блоку толщиномера А1210 раздельно-совмещённого преобразователя D1771 с рабочей частотой 4 MГц. Подключение преобразователя осуществляется двойным кабелем LEMO-LEMO.
Для точного определения толщины стальной пластины необходимо провести измерения в местах без покрытия. Для этого край пластины с каждой стороны был зачищен.
Перед началом измерений в место установки преобразователя D1771 наносится специальный гель, который необходим для обеспечения акустического контакта, т.е. для передачи ультразвуковых колебаний из преобразователя в материал объекта контроля.
Включаем толщиномер, устанавливаем режим А-СКАН, выбираем из списка ПЭП преобразователь D1771. Перед началом измерений необходимо провести «тест» выбранного преобразователя, следуя указаниям на экране толщиномера.
Выбираем из списка материалов марку стали со скоростью продольной ультразвуковой волны 5 950 м/с.
Примечание: Если точная скорость прохождения ультразвука не известна, то её можно определить по образцу известной толщины (см. п.2.3.2.4. руководства по эксплуатации).
Перед началом измерений в режиме А-СКАН необходимо нажатием клавиши F3 выбрать способ измерения «между двумя максимума сигнала».
Далее измеряем толщину стальной пластины в местах без покрытия. Оценка измерений производится путём фиксации стробом (красный отрезок на экране прибора) получаемых импульсов, отражённых от внутренней стенки стальной пластины (первый и второй донные сигналы) (рис. 3).
Рис.3. Проведение измерения толщины стальной пластины в местах с удалённым покрытием в режиме А-СКАН.
Измеренное значение толщины пластины составило 7,95 мм.
2. Проведем измерение толщины стальной пластины через лакокрасочное покрытие толщиной 0,5 мм.
Рис.4.Проведение измерения толщины стальной пластины через лакокрасочное покрытие в режиме А-СКАН.
Наносим специальный гель в место установки преобразователя и проводим измерение через лакокрасочное покрытие (рис.4).
Сигнал, получаемый на границе покрытие/металл, настолько мал, что практически не виден на экране толщиномера.
Измерение толщины производится путём фиксации стробом (красный отрезок на экране прибора) получаемых импульсов, отражённых от внутренней стенки стальной пластины (первый и второй донные сигналы), без учёта сигнала от границы покрытие/металл.
Измеренное значение толщины пластины без учёта лакокрасочного покрытия составило 7,95 мм.
3. Теперь проведём измерения через компаундное покрытие в местах с толщиной 2 мм.
Рис. 5.Проведение измерения толщины стальной пластины через компаундное покрытие толщиной 2 мм в режиме А-СКАН.
Наносим специальный гель в место установки преобразователя и проводим измерение через компаундное покрытие толщиной 2 мм. (рис.5).
Примечание: Чем гуще (вязче) состав контактной смазки, тем более информативней полезные сигналы, отделяемые от шумов, что приводит к достоверным и устойчивым результатам измерений при проведении контроля через сильнозатухающие покрытия.
Измерение толщины производится путём фиксации стробом (красный отрезок на экране прибора) получаемых импульсов, отражённых от внутренней стенки стальной пластины (на экране прибора это второй и третий по счёту импульсы). При этом сигнал, получаемый от границы покрытие/металл, не учитывается, т.е. не выделяется стробом.
Измеренное значение толщины пластины без учёта компаундного покрытия составило 7,95 мм.
4. Проведём измерения через компаундное покрытие в местах с толщиной 3 мм.
Рис.6.Проведение измерения толщины стальной пластины через компаундное покрытие толщиной 3 мм в режиме А-СКАН.
Наносим специальный гель в место установки преобразователя и проводим измерение через компаундное покрытие толщиной 3 мм. (рис.6).
Измерение толщины производится путём фиксации стробом (красный отрезок на экране прибора) получаемых импульсов, отражённых от внутренней стенки стальной пластины (на экране прибора это второй и третий по счёту импульсы). Здесь уже мы видим, что сигнал, получаемый от границы покрытие/металл, имеет значительную величину (первый импульс на экране прибора). Также как и в предыдущих случаях требуется исключение его при проведении измерений, т.е. сигнал не выделяется стробом.
Измеренное значение толщины пластины без учёта компаундного покрытия составило 7,95 мм.
Выводы
- Существует возможность измерения толщины металлов через покрытия, пропускающие ультразвук, в случае хорошей адгезии с металлом.
- Ультразвуковой толщиномер А1210 является оптимальным прибором для измерения толщины основного тела металла через лакокрасочные и иные типы изоляционных покрытий.
- Достоверные результаты, устойчивые и стабильные показания обеспечиваются в рабочем режиме А-СКАН с использованием раздельно-совмещенного преобразователя D1771 с рабочей частотой 4 МГц.
- «АКС-гель», применяемый при контроле, со специально разработанной вязкостью (густотой) позволяет получать достоверные результаты измерений при проведении толщинометрии через изоляционные покрытия с высоким затуханием ультразвука.
- Для обеспечения стабильности и избежания неточности в измерениях через различные типы покрытий необходимо выбирать способ измерения «между двумя максимума сигнала».
CALOWEAR 2 измерение толщины и износа покрытий или материалов
Прибор Calowear может измерять толщину и коэффициент износа покрытий. Он позволяет оценить коэффициента износа, k, массивных материалов, а для образцов с покрытием, коэффициенты износа, как покрытия, так и подложки.
Для оценки износа, прибор оборудован ячейкой нагрузки, измеряющей нагрузку шара на образец.В состав стандартного прибора входит магнитная мешалка и перистальтический насос для подачи абразивной суспензии в зону контакта шара с исследуемым образцом.
Абразивный порошок SiC поставляется вместе с прибором. Смешав порошок SiC с водой, Вы получите абразивную суспензию, которую можно подавать на вращающийся шар (в зону контакта) при помощи микро-насоса обеспечивающего равномерность подачи.
Опционально прибор можно оборудовать видеомикроскопом.
Прибор Calowear2 можно использовать для анализа покрытия с толщиной от 0.1 до 50 мкм. Типичные примеры покрытий включают CVD, PVD, плазменное напыление, анодное окисление, поверхности обработанные ионным пучком или ионным напылением, химическим и гальваническим разложением, полимерные покрытия, краски, и лаки.
Calowear2 с опциональным Видеомикроскопом
ТЕХНИЧЕСКИЕ ПАРАМЕТРЫ Calowear2
Скорость вращения вала мотора: | 10 — 1000 об/мин |
Размеры рабочего столика: | 80 x 80 мм |
Задаваемое время вращения: | 2 сек — 15 мин |
Диаметры стандартных шаров: | 20, 25.![]() |
Электропитание: | 105 — 250 В |
Питание мотора: | 24 В |
Мощность мотора: | 15 Вт |
Частота в сети: | 47 — 63 Гц |
Соответствует стандарту: | VDI 3198 |
ДИАПАЗОНЫ ИЗМЕРЕНИЙ | |
Толщина покрытий: | от 0.1 до 50 мкм или более |
Точность измерений: | от 1 до 5 % (зависит от микроскопа и шероховатости поверхности исследуемого образца) |
Диаметр кратера: | от 0.15 до 2 мм |
Точность измерений зависит от следующих факторов:
- Качество поверхности (шероховатость) и/или покрытия
- Контраст между отдельными слоями покрытия и субстратом
- Точность оптической измерительной системы
ПРИНЦИП ИЗМЕРЕНИЙ ТОЛЩИНЫ
Вращающийся шар известного диаметра (шар Ø) располагается на поверхности покрытия с заранее выбранной нагрузкой. Положение шара по отношению к образцу и нагрузка в зоне контакта постоянно. После добавления абразивной суспензии в зону контакта, шар вырабатывает сферическую лунку в поверхности образца (в покрытии и субстрате). Оптический осмотр лунки отображает проекции поверхности разделов покрытия и субстрата. Путем измерения параметров x и y, толщина покрытия = s может быть рассчитана по простому геометрическому уравнению.
РАСЧЕТ КОЭФФИЦИЕНТА ИЗНОСА
Для массива материала, показано (1), (2) что простая модель абразивного износа, Которая полностью эквивалентна известному уравнению Арчарда (3) для износа при скольжении:
(1)
и при b<<d
(2)
где L расстояние скольжения, FN вертикальная нагрузка на образец, V объем изношенного материала, K коэффициент износа, b диаметр кратера и d диаметр сферы. простым преобразованием получим:
(3)
Вычисления для материалов с покрытие дано в руководстве пользователя Calowear.
(1)
и при b<<d
(2)
где L расстояние скольжения, FN вертикальная нагрузка на образец, V объем изношенного материала, K коэффициент износа, b диаметр кратера и d диаметр сферы. простым преобразованием получим:
(3)
Вычисления для материалов с покрытие дано в руководстве пользователя Calowear.
ТЕХНИЧЕСКОЕ ОПИСАНИЕ
По этой ссылке Вы можете загрузить техническое описание на Толщиномеры Calowear2 — скачать в формате PDF
Измерение толщины пленочного покрытия в режиме реального времени
http://www. pharmtech.com/real-time-measurement-coating-film-thickness?pageID=1
Матиас Вольфганг, Патрик Валь, Стефан Сахер, Элен Гартшайн, Йоханнес Г. Хинаст
Pharmaceutical Technology, 43 (3) 2019.
Перевод – Алексей Федоренко
Оптическая когерентная томография (Optical Coherent Tomography – OKT) улучшает контроль качества и разработку лекарственных форм с покрытием, позволяя измерять толщину пленки в режиме реального времени.
Процесс нанесения фармацевтических покрытий – это хорошо обоснованная технологическая операция, но точное измерение конечной точки процесса нанесения покрытия остается сложной задачей. Знание конечной точки имеет решающее значение, особенно для нанесения функциональных покрытий, поскольку такой качественный показатель, как толщина слоя покрытия, оказывает непосредственное влияние на характеристики продукта и, в частности, на скорость его растворения. В данной статье обобщены результаты исследования, посвященного использованию оптической когерентной томографии (ОКТ) в качестве способа мониторинга фармацевтических процессов напыления покрытий в потоке для таблеток и гранул. В исследовании измеряли толщину покрытия как функцию времени для таблеток в барабанной установке для нанесения покрытия и для гранул в установке для нанесения покрытия в псевдоожиженном слое. Также изучено возможное влияние красителя, который, как было установлено, не оказывает влияния на измерения. Толщину покрытия определяли автоматически на основе ОКТ-изображений, а не с помощью калибровочных хемометрических моделей. Поточные данные и автономное трехмерное картирование выявили дополнительные грани качества покрытия таблеток и гранул (то есть внутри- и межчастичную вариабельность покрытия).
Результаты исследования показали, что используемая в промышленности ОКТ-система способствует улучшению понимания процесса и обеспечивает качество продукции при нанесении фармацевтических функциональных покрытий, помогая ученым в области фармацевтики в вопросах разработки, масштабирования и транспортировки, а также при выявлении и устранении проблем. В будущем ОКТ может стать новым инструментом для обеспечения контроля качества, заменив ненадежные и отнимающие много времени процедуры тестирования. Одним из ключевых преимуществ новой технологии является то, что она позволяет детально понять источник и обнаружить наличие дефектов, а также выявить низкое качество покрытия как в одной, так и в нескольких партиях продукции.
Функциональное покрытие – распространенный способ повышения соблюдения пациентом врачебных предписаний, предотвращения подделок и повышения биодоступности, а также определения общей функциональности твердых лекарственных форм для перорального применения. В некоторых случаях наносят «активное покрытие», содержащее один или несколько АФИ, для смягчения взаимодействия разных препаратов или учета различного поведения при высвобождении из одной лекарственной формы. Кишечнорастворимые покрытия обычно наносят на таблетки в дражировочных котлах, предназначенных для нанесения покрытия с перфорированным или неперфорированным барабаном, тогда как для драже, мини-таблеток и гранул с этой целью используют коатеры с псевдоожиженным слоем (например, для маскировки вкуса в лекарственных средствах для детей). Процесс нанесения покрытия необходимо контролировать в зависимости от толщины и вариабельности покрытия (как между раз-личными технологическими линиями, так и в пределах одной линии для нанесения покрытия), а также для обнаружения дефектов покрытия (например, дефектов окраски или поверхностных пятен и трещин).
Проблемы при нанесении покрытия часто возникают в ходе разработки и изготовления, особенно при масштабировании процесса либо его переносе из одной лаборатории или производственной площадки на другую. Таким образом, наличие технологии, способной в режиме реального времени контролировать основные качественные характеристики покрытий (включая толщину, ее изменчивость, морфологию, пористость, дефекты и трещины), способствует сокращению общего времени разработки и ускорению масштабирования производства, а также позволяет более точно определять первичную причину слабости покрытия.
В настоящее время для изучения качества покрытия пероральных твердых лекарственных форм используется ряд методик, включая оптический контроль поперечных надрезов и измерение увеличения диаметра или массы таблеток.
Однако реализация этих подходов требует много времени, к тому же существует риск ошибок, а полученные результаты могут быть приблизительными. Кроме того, данные методы не могут быть применены в процессе производства для обеспечения контроля или управления технологическим процессом.
В целях преодоления этих недостатков были разработаны поточные технологические анализаторы для неразрушающего мониторинга и оценки качества покрытия, каждый из которых имеет свои сильные и слабые стороны.
Эти методы включают в себя:
• ближнюю инфракрасную (БИК) [1, 2] и Рамановскую [3, 4] спектроскопии;
• терагерц (ТГц)-зондирование [5, 6] – эффективный подход, но сложный для реализации в режиме реального времени;
• пространственную фильтрующую велосиметрию [7];
• динамический анализ изображений [8].
Для сравнения: ОКТ позволяет быстро, в режиме реального времени, определять качество полупрозрачных функциональных покрытий без необходимости калибровки. Это также устраняет потребность в разработке и обслуживании хемометрических моделей для интерпретации данных. Эти модели необходимы как для БИК, так и для Рамановской спектроскопии [1]. В сравнении с другими подходами, использующими технологию анализа процессов (PAT), ОКТ обеспечивает гораздо более высокую скорость сканирования (до 250 000 измерений в 1 с в отличие от приблизительно 30 для ТГц и менее чем одно для Рамановской спектроскопии). Кроме того, ОКТ гарантирует очень высокое осевое и боковое разрешение (более чем на порядок выше, чем при использовании всех других подходов).
Как работает ОКТ для измерения покрытий?
ОКТ является неинвазивной методикой, которую используют для получения изображений поперечных срезов глубинных слоев покрытия. Установка и функционирование ОКТ-систем описаны в литературе [9 – 11]. При получении изображений источник света с высокой пространственной и низкой временной когерентностью фокусируется на поверхности покрытия. Бóльшая часть света отражается или преломляется, но значительная его часть проникает через поверхность и отражается от стыков различных материалов с характерными изменениями индекса преломления. Отражаемый свет обнаруживается спектрометром (для спектрально-доменной ОКТ). Измеряя длину оптического пути между отражениями, можно определить расстояние между границами раздела с учетом индекса преломления материала.
Результаты нескольких исследований уже продемонстрировали высокую эффективность ОКТ-систем для измерения толщины покрытия фармацевтических твердых лекарственных форм [12 – 14]. ОКТ можно также использовать для анализа изменений толщины покрытия в пределах отдельных частиц (внутричастичная вариабельность) и между ними (межчастичная вариабельность) во время процесса нанесения покрытия [15]. В последнее время ОКТ была промышленно реализована в качестве технологии мониторинга для применения в Надлежащей производственной практике (GMP). Также модель доступна во взрывобезопасном исполнении и предназначена для промышленного использования. Исследования, рассмотренные в данной статье, проводились на соответствующем требованиям GMP приборе для коммерческого использования.
Материалы и методы
Зонд для ОКТ.
На протяжении всей экспериментальной работы для измерений и регистрации данных использовали промышленную спектрально-доменную ОКТ-систему (OSeeT, Phyllon, Австрия). Система OSeeT работает на центральной длине волны 832 нм со спектральной полосой пропускания 75 нм, что создает теоретическое осевое разрешение 4 мкм. Базовый блок может быть совмещен с одномерным (1D) сенсором с боковым разрешением 14 мкм для проведения измерений в процессе производства. Этот датчик также является частью дополнительно поставляемого поточного пробоотборника. Трехмерный (3D) датчик с боковым разрешением 10 мкм доступен для автономных измерений. Датчики и периферийные устройства могут быть легко изменены благодаря использованию стандартных соединений, таких как волоконно-оптический канал/угловой интерфейс физического кон-такта (Fiber Channel – FC/Angled Physical Contact – APC) для датчиков и оптических периферийных устройств, а также универсальная последовательная шина версии 3.0 (Universal Serial Bus – USB 3. 0) для электрического интерфейса.
В данном исследовании для мониторинга и валидации процесса напыления использовали 1D-сенсорную головку (Phyllon), а для мониторинга экспериментов с жидкостным покрытием – изготовленный на заказ 3D-датчик [16] в двухмерном (2D) режиме работы (то есть с одним отключенным гальваническим зеркалом). 3D-датчик также использовали для измерения гранул и таблеток, периодически извлекаемых из процесса, в автономном режиме.
Время выдержки датчика было установлено на 15 мкс для (1D) и 30 мкс для (2D) и автономных измерений таблеток в процессе производства (3D). Время простоя (для считывания и оцифровки) составляло 1,9 мкс для всех измерений. Время выдержки и время простоя привело к скорости сбора данных 59,2 кГц (1D) и 31,3 кГц (2D/3D). Скорость сбора данных соответствует числу сканирований на определенную глубину в 1 с, в результате чего частота кадров составила 57,8 в 1 с (frames per second – fps) для 1D-устройства и 30,6 в 1 с для 2D- и
3D-устройств.
Измерение толщины покрытия (цифровое) — Русский
The PaintChecker mobile LED Blue 591 is a photothermal measuring device used for the non contact and non destructive determination of coating thicknesses in accordance with DIN EN 15042-2.
Specially developed for the measurement of powder coatings before curing on various substrates such as steel, aluminium and ceramics.
Cured coatings can also be measured. The precise layer thickness measurement is geometry indepedent and therefore also possible on complex parts such as corners, edges or curved inner sides.
The photothermal measuring method used in PaintChecker mobile LED Blue is an indirect measuring method.
This means that the measuring device does not measure coating thickness values directly, but that they are derived indirectly from the evaluation of the photothermal measurement signal.
The Sensor
The sensor made of extruded high-strength plastic is designed for manual handling and contains, in addition to eye-safe positioning LEDs (UV light), the measurement data recording.
The fabricated cable that connects the sensor and the controller unit is 0.8 m in length.
With the ergonomic, lightweight sensor, measurements can be made directly by hand.
With its optomechanical structure, the sensor can also be used in the immediate vicinity of the application.
The Controller-Unit
The controller-unit is contained in a rugged aluminum housing. All of the settings can be selected and modified conveniently with the membrane keypad using a context-related menu that is easy to understand.
The USB connection is used for communicating with a PC. The software allows complete control over the measurement procedure and storage of
measurement data.
The measuring values are saved in measuring series for immediate or later use.
Included in the scope of supply:
- Sensor with lead
- Controller unit
- Protective case for controller unit
- Reference sample
- Lithium-ion rechargeable 14500 batteries
(4 pcs.)
- Quadruple battery charger
- Software
- USB cable
- Manual
Толщина | Библиотека измерений | KEYENCE America
Для лиц, ищущих системы измерения толщины
При поиске наилучшего способа измерения толщины следует учитывать ряд важных факторов, включая форму и материал цели, а также тип системы измерения. Выбор оборудования, не отвечающего вашим потребностям, может привести к недостаточной точности и увеличению трудозатрат во время производства, поэтому убедитесь, что вы выбрали правильное оборудование.Этот сайт разработан, чтобы помочь тем, кто ищет систему измерения толщины, найти лучший способ уверенного измерения.
Обязательно прочтите информацию о , измеряющую , и советы по , чтобы выбрать идеальную измерительную систему!
Помимо ознакомления с системами измерения, в этом руководстве подробно описаны лучшие методы измерения толщины, внешнего диаметра, формы и т. Д.
Скачать
Как измерить толщину (форма листа)
- ШАГ 1: Выберите форму объекта измерения — тонкий лист или другую форму.
- ШАГ 2: Посмотрите на методы, описанные в каждом пункте, чтобы найти лучший метод измерения.
- ШАГ 3: Загрузите соответствующий каталог измерительных систем.
Как измерить толщину (разные заготовки)
- ШАГ 1. Посмотрите на методы, описанные в каждом пункте, чтобы найти лучший метод измерения.
- ШАГ 2: Загрузите соответствующий каталог измерительных систем.
Меры предосторожности при измерении толщины между двумя головками датчика
О юстировке оптических осей
Когда вы измеряете заготовку между двумя сенсорными головками, измеренная толщина в принципе не изменится, даже если заготовка будет вибрировать вверх и вниз.
Однако, если оптические оси двух сенсорных головок не выровнены друг с другом по прямой линии, ошибки измерения могут быть вызваны из-за вибрации заготовки вверх и вниз или изгиба. Обратите внимание на следующие моменты и расположите установку так, чтобы можно было совместить оптические оси.
- 1) Чтобы свести к минимуму влияние смещения оптических осей, установите сенсорные головки рядом с роликами и выберите место, где натяжение заготовки стабильно, а расстояние от одного ролика до другого небольшое.
Это позволяет проводить измерения с небольшими изгибами и вибрацией заготовки. - 2) Сориентируйте сенсорные головки так, чтобы направления проецируемого и принимаемого света были перпендикулярны направлению движения заготовки, как показано на рисунке.
Это затрудняет воздействие на сенсорные головки наклона и тряски в направлении движения заготовки из-за вибрации во время транспортировки. - 3) Во время юстировки оптических осей измерьте тонкую белую пластину из смолы или лист бумаги в качестве временной цели измерения. Когда вы измеряете эти цели, лазерные пятна проходят сквозь цель и становятся видимыми. Установите сенсорные головки так, чтобы пятна на передней и задней части цели всегда были выровнены, даже если цель перемещается вверх и вниз.
Меры предосторожности при измерении толщины над роликом
О зазоре между роликом и заготовкой
При измерении толщины заготовки на ролике с этим роликом в качестве эталона ошибки измерения будут возникать, если между роликом и заготовкой есть зазор.
Обратите внимание на следующие моменты и сделайте установку так, чтобы не возникало зазоров.
- 1) Приложите как можно большее усилие к заготовке.
Если натяжение слабое, заготовка не будет полностью контактировать с валком, поэтому возникнет зазор от нескольких микрометров до нескольких десятков микрометров.
Мы рекомендуем выполнять измерения с приложенным натяжением 50 Н или более, но обязательно учитывайте предел прочности заготовки на разрыв.
Выполняйте измерения из места, в котором натяжение заготовки максимально стабильно, расстояние от одного ролика до следующего небольшое, а заготовка расположена на вершине ролика. - 2) Совместите оптическую ось с пиком ролика.
Как показано на рисунке, если оптическая ось смещена относительно пика ролика, возникает ошибка измерения (зазор Z).- а) Установите механизм, позволяющий точно настроить положение сенсорной головки в направлении подачи.
- b) Выполните измерения на валке большого диаметра, чтобы минимизировать зазор Z, даже если оптическая ось смещена от пикового положения валка.
Об эксцентриситете ролика
При вращении ролика могут возникать ошибки измерения из-за эксцентриситета ролика.
Обратите внимание на следующие моменты, чтобы исключить влияние эксцентриситета ролика.
- 1) Когда точки, используемые для измерения толщины, являются обоими краями заготовки, измерьте и поверхность ролика, и поверхность заготовки одновременно, чтобы найти толщину по значению шага.
- 2) При измерении заготовки на ролике с роликом в качестве эталона вы можете выполнять измерения при том же угле поворота (положении), чтобы исключить влияние эксцентриситета, даже если ролик движется эксцентрично.
- Назад: Прикладные решения Список измерений
- Далее: Прикладные решения Измерение размеров — ширина
Ультразвуковое измерение толщины краски — пластиковые подложки | Ресурсы
DeFelsko производит портативные неразрушающие ультразвуковые измерители толщины покрытий, которые идеально подходят для неразрушающего измерения толщины сухой пленки покрытий на пластике.Многие отрасли промышленности теперь используют эту неразрушающую технологию в своих программах обеспечения качества.
Две модели идеально подходят для пластиковых подложек.
- PosiTector 200 B1 (стандартная модель) — это экономичное и наиболее распространенное решение для измерения ОБЩЕЙ толщины системы покрытия.
- PosiTector 200 B3 (расширенная модель) может измерять как ОБЩУЮ толщину покрытия, так и до 3 толщин отдельных слоев в многослойной системе.
Он также имеет графический режим для детального анализа системы покрытия.
Измерения:
- Общая толщина покрытия на пластике
- Измерение шероховатой поверхности покрытия
- Измерение толщины отдельного слоя при многослойном нанесении
- Измерение на автомобильном пластике
Дополнительные примечания:
- Как проводить измерения
- Графический режим
- Другие методы измерения
- Сведения о пластиковых покрытиях
- Зачем проводить измерения с помощью ультразвука?
- Где рынок?
Приложение №1: Измерение общей толщины
Некоторые системы пластиковых покрытий наносятся в несколько слоев для достижения желаемой цели.Наш PosiTector 200 B1 — идеальное решение, когда аппликаторам нужно знать только конечную общую толщину покрытия.
PosiTector 200 B1 готов к измерению большинства применений пластиковых покрытий прямо из коробки. Он имеет диапазон измерения от 13 до 1000 микрон (от 0,5 до 40 мил) и идеально подходит для измерения общей толщины системы покрытия. Он не требует настройки калибровки для большинства приложений, имеет возможность переключения мил / микрон и имеет большой, толстый, ударопрочный дисплей Lexan.
Для тех, кто знаком с измерителями толщины магнитного покрытия, использование ультразвуковых измерителей толщины покрытия является простым и интуитивно понятным.Метод измерения прост и неразрушает.
Приложение № 2: Измерение шероховатых поверхностей покрытия
Покрытия с шероховатыми поверхностями бросают вызов любому методу измерения, и ультразвуковые испытания не являются исключением. PosiTector 200 способен справиться с этими ситуациями.
На микроскопическом уровне толщина может варьироваться (см. Рис. 2). Значимые измерения толщины лучше всего получить, выполнив несколько измерений в одном и том же месте и усреднив результаты.
На шероховатых поверхностях PosiTector 200 обычно определяет толщину от вершины выступов покрытия до основы.Это представлено расстоянием №1 на рисунке 2. Связующее вещество заполняет пустоты между зондом и покрытием, помогая ультразвуковому импульсу проникать в покрытие.
Из-за сильной шероховатости прибор может отображать низкие значения толщины (расстояние №2). Это происходит потому, что эхо-сигналы от поверхности раздела контактное вещество / покрытие сильнее, чем от поверхности раздела покрытие / подложка. PosiTector 200 имеет уникальную настраиваемую пользователем функцию УСТАНОВКИ ДИАПАЗОНА для игнорирования эхо-сигналов от шероховатости.
Для этих приложений режим памяти PosiTector 200 предоставляет помощь.Когда память включена, PosiTector 200 вычисляет и отображает количество снятых показаний, среднее значение этих показаний, стандартное отклонение этих показаний, а также максимальное и минимальное значения (см. Рисунок 3). Прилагаемый контактный агент действует лучше, чем вода на неровных поверхностях.
Рис. 3 Для получения значимых результатов измерения толщины на шероховатых поверхностях режим памяти PosiTector 200 используется для вычисления скользящего среднего.Приложение № 3: Измерение толщины отдельных слоев в многослойном приложении
PosiTector 200 B3 может измерять как общую толщину системы покрытия, так и до 3 толщин отдельных слоев в многослойной системе. Он также имеет графическое отображение для подробного анализа системы покрытия.
В приведенном выше примере толщина слоя 1 составляет 1,5 мил. Слой 2 имеет толщину 1,5 мил. Общая толщина составляет 3,0 мил. Графический ЖК-дисплей отображает два «пика», представляющих две границы раздела материалов. Двухэтапный процесс настраивает инструмент для многоуровневых приложений.
Приложение №4: Измерение автомобильного пластика
Большое количество пластиковых компонентов присутствует как в салоне, так и снаружи автомобиля.Очень часто эти пластиковые компоненты необходимо покрывать из соображений эстетики и защиты.
Внутренние компоненты, такие как приборные панели, дверные панели, крышки подушек безопасности, рулевые колеса и т. Д., Сложнее измерить по двум причинам. Во-первых, многие компоненты слишком малы или слишком сложны геометрически для того, чтобы зонд PosiTector 200 мог получить надлежащий доступ. Во-вторых, некоторые детали имеют либо очень тонкое покрытие, либо покрытие слишком грубое, чтобы прибор мог его измерить постоянно. Измеритель лучше всего работает на гладкой, плоской, твердой поверхности с толщиной покрытия не менее 13 микрон (0.5 мил).
Внешние компоненты, такие как бамперы, корпуса зеркал, боковая облицовка и т. Д., Могут быть измерены при условии, что датчик PosiTector 200 снова сможет получить доступ к измеряемой поверхности. Измеритель может измерять общую толщину в большинстве случаев и может измерять отдельные слои в многослойной системе.
Автомобильные системы покрытий состоят из нескольких слоев покрытия. Базовая модель PosiTector 200 B1 может измерять общую толщину этих систем покрытий.
Слои промотора адгезии и грунтовки в автомобильной промышленности обычно слишком тонкие, чтобы более продвинутая модель PosiTector 200 B3 могла измерять индивидуально.Таким образом, инструмент комбинирует их толщину с толщиной основного покрытия для получения общего результата. Верхний прозрачный слой покрытия измеряется отдельно и индивидуально.
Рис. 5 Рис. 5 типичен для результатов PosiTector 200 B3 на внешнем автомобильном пластике. На изображении слева показано измерение в британских единицах (милы). Правое изображение — это эквивалентное измерение в метрических единицах (микронах). Хотя система покрытия состоит из 4 слоев, прибор объединяет толщину первых 3 слоев (усилитель адгезии, грунтовка, базовые покрытия) в одно значение, равное 1.7 мил (43 микрона). Размер конечного верхнего прозрачного покрытия индивидуально составляет 1,7 мил (43 микрона). Общая толщина системы покрытия составляет 3,4 мил (86 мкм).
Этот результат полезен, когда окончательная толщина прозрачного покрытия является важным слоем, который необходимо определить. Автодетейлеры используют эту функцию для просмотра оставшегося количества лака во время полировки. Аппликаторы используют эту функцию для обеспечения постоянной толщины нанесения.
Ультразвуковые датчики, обсуждаемые в этой статье, имеют диаметр 8 мм (0.3 дюйма) плоская измерительная поверхность, которая должна полностью контактировать с пластиком с покрытием для получения наилучших результатов измерения. Для получения значимых результатов измерения, проводимые на изогнутых поверхностях, могут потребовать усреднения нескольких показаний.
Дополнительные примечания
Как проводить измерения
Ультразвуковое измерение толщины покрытия работает, посылая ультразвуковые колебания на покрытие с помощью зонда с помощью связующего вещества, нанесенного на поверхность.К каждому прибору прилагается флакон объемом 4 унции обычного гелевого геля на водной основе.Как вариант, капля воды может служить связующим веществом на гладких горизонтальных поверхностях.
Рис. 6 Проведение измерения. После того, как капля связующего вещества была нанесена на поверхность детали с покрытием, зонд помещается на поверхность плашмя. Нажатие вниз инициирует измерение (см. Рис.6). Поднимая датчик, когда слышен двойной звуковой сигнал или когда мигает зеленый индикатор, отображается последнее измерение на ЖК-дисплее. Второе показание можно снять в том же месте, продолжая удерживать зонд на поверхности. По окончании протрите зонд и поверхность тканью или мягкой тканью.
Точность измерения
Точность любого ультразвукового измерения напрямую соответствует скорости звука измеряемого покрытия. Поскольку ультразвуковые инструменты измеряют время прохождения ультразвукового импульса, они должны быть откалиброваны по «скорости звука» в этом конкретном материале.
С практической точки зрения значения скорости звука не сильно различаются между материалами покрытия, используемыми в индустрии пластмасс.Поэтому ультразвуковые толщиномеры покрытия обычно не требуют настройки заводских настроек калибровки.
Графический режим (только модель PosiTector 200 B3)
Правая сторона экрана PosiTector 200 может использоваться для отображения графического представления ультразвукового импульса, когда он проходит через систему покрытия. Этот мощный инструмент позволяет пользователю лучше понять, что датчик «видит» под поверхностью покрытия.
Слева: Графический режим ВКЛ.
По мере того, как зонд опускается и ультразвуковой импульс проходит через систему покрытия, импульс сталкивается с изменениями плотности на границах раздела между слоями покрытия и между покрытием и подложкой.
«Пик» изображает эти интерфейсы. Чем больше изменение плотности, тем выше пик. Чем плавнее изменение плотности, тем больше ширина пика. Например, два слоя покрытия, сделанные по существу из одного и того же материала и «смешанные», приведут к низкому и широкому пику.Два материала с очень разной плотностью и четко определенной границей раздела приведут к высокому узкому пику.
PosiTector 200 B3 выбирает самый высокий из пиков при попытке определить толщину слоя покрытия. Например, если количество уровней установлено на 3, 3 самых высоких пика между диапазонами Lo и Hi выбираются в качестве интерфейсов между этими уровнями. Пики, выбранные датчиком, обозначены красными треугольными стрелками (см. Рис.9).
На рисунке 9 верхнее ( Lo = 0,5 мил) и нижнее ( Hi = 15,0 мил) значения диапазона отображаются в виде двух горизонтальных линий вверху и внизу графической области. Lo (минимальный лимит) находится вверху. Hi (максимальный предел) внизу. Эхо-сигналы или пики (значения толщины) вне этих диапазонов игнорируются. Значения диапазона устанавливаются и изменяются с помощью опции меню УСТАНОВИТЬ ДИАПАЗОН.
Этим графическим дисплеем можно управлять с помощью параметра меню УСТАНОВИТЬ ДИАПАЗОН.Помимо возможности настройки значений диапазона, курсор можно расположить в любом месте между двумя значениями диапазона, чтобы исследовать другие пики.
Рис.10 Курсор используется при наличии более трех слоев.В этом примере прибор объединяет два нижних слоя в результат 3,9 мил.
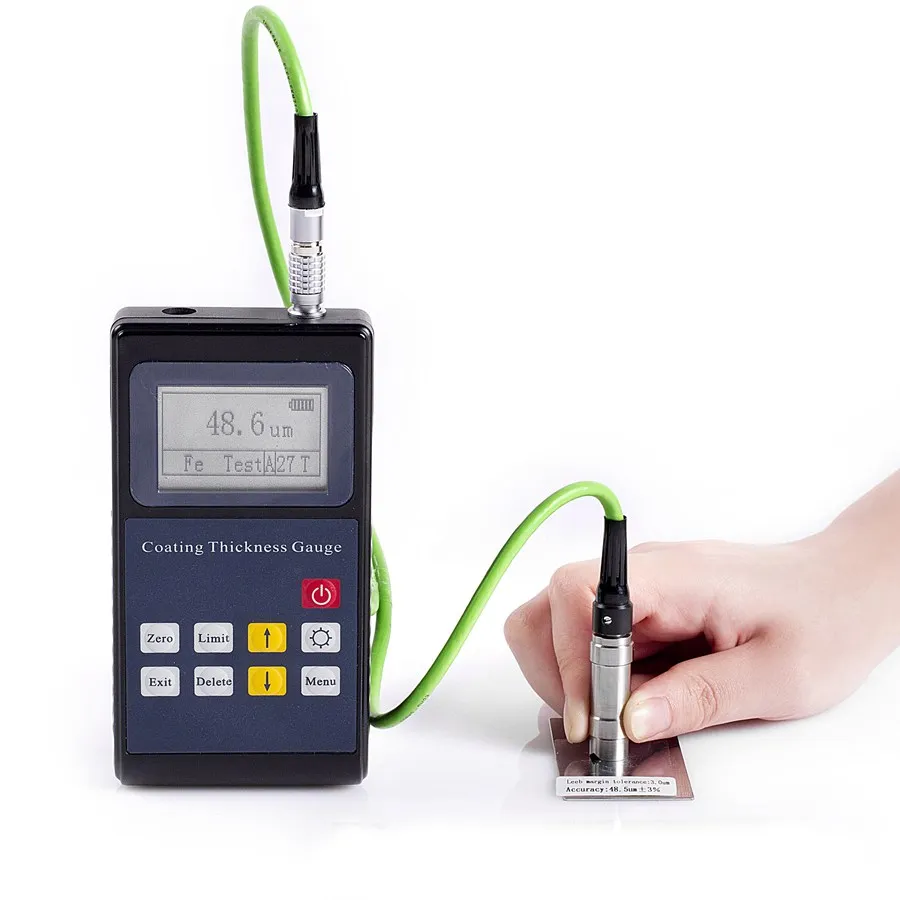
Третий слой, таким образом, составляет 2,5 мил (5,9–3,4 (сумма слоев 1 и 2).
Другие методы измерения
Обычные магнитные и вихретоковые датчики работают только с металлами.Таким образом, промышленность пластмасс полагалась на другие методы измерения, в том числе:
- Оптическое поперечное сечение (разрезание детали с покрытием и микроскопический просмотр разреза)
- Измерение высоты (измерение до и после с помощью микрометра)
- Гравиметрическое и площадь покрытия для расчета толщины)
- Погружение толщиномеров мокрой пленки во влажную краску и расчет толщины сухой пленки с использованием процентного содержания твердых веществ по объему
- Замена (размещение стального купона рядом с пластиковой частью и нанесение на нее покрытия одновременно время).
Эти методы требуют много времени, трудны в исполнении и могут быть интерпретированы оператором и подвержены другим ошибкам измерений. Аппликаторы считают деструктивные методы нецелесообразными. Чтобы получить статистически репрезентативный образец, несколько деревянных изделий из партии, возможно, потребуется утилизировать в рамках процесса разрушающих испытаний.
Типичный метод разрушения требует разрезания покрытой детали в поперечном сечении и измерения толщины пленки под микроскопом.В другом методе поперечного сечения используется масштабированный микроскоп для просмотра геометрического разреза через покрытие из сухой пленки. Для этого специальный режущий инструмент проделывает небольшую точную V-образную канавку через покрытие в подложке (см. Рис. 11). Доступны измерительные приборы, которые поставляются в комплекте с режущими наконечниками и лупами с подсветкой. Подробное описание этого метода испытаний приведено в ASTM D4138-07a, «Стандартная практика измерения толщины сухой пленки систем защитных покрытий с помощью разрушающих средств поперечного сечения».
Рис. 11 Хотя принципы этого метода легко понять, существует множество возможностей для внесения ошибок. Подготовка образца и интерпретация результатов требуют умения. Кроме того, настройка сетки измерений на неровный или нечеткий интерфейс может привести к неточности, особенно между разными операторами. Этот метод используется, когда недоступны недорогие неразрушающие методы, или как средство подтверждения результатов неразрушающего контроля.
С появлением ультразвуковых инструментов многие компании по нанесению покрытий перешли на неразрушающий контроль.
Справочная информация о пластиковых покрытиях
Каково применение?
Покрытие пластмасс, особенно в автомобильной промышленности, включает нанесение нескольких слоев покрытия для достижения полного эстетического вида и защитных свойств. Не только внешняя отделка, как правило, является сильным отражением качества и долговечности дорогостоящих потребительских товаров, но и покрытия для пластиковых компонентов должны решать проблемы, уникальные для пластиковых подложек, включая адгезию, гибкость и температурные ограничения.
Обычные пластиковые подложки (например, полиэтилен, полипропилен, термопластичный полиолефин, АБС, нейлон, ПВХ) непористые, устойчивые к большинству растворителей и имеют низкую поверхностную энергию по сравнению с другими материалами. Это затрудняет смачивание пластиковой поверхности и дает покрытиям мало возможностей для прилипания за счет проникновения или физического сцепления с неровностями поверхности. Чтобы противостоять этим трудностям, промоторы адгезии используются в качестве добавок к краске или в качестве грунтовок для улучшения адгезии покрытий к их субстратам.Промотор адгезии обычно имеет сродство к субстрату и нанесенному покрытию, что позволяет нанесенным покрытиям соответствовать намеченным эксплуатационным требованиям.
Автомобильные покрытия
В автомобильных покрытиях термин «усилитель адгезии» относится к грунтовке (обычно хлорированному полиолефину или другим модифицированным полиолефинам), которая облегчает адгезию последующего слоя краски к пластику. Обычно промоторы адгезии наносятся для достижения толщины сухой пленки 0.3 — 0,5 мил (7,5 — 12,5 мкм). Поскольку толщина промотора адгезии ниже рекомендуемой толщины отдельного слоя в 1 мил (25 мкм), ультразвуковому датчику может быть трудно отличить его от последующих слоев.
Грунтовки заполняют любые небольшие дефекты в процессе формования и могут образовывать проводящий слой, который облегчает электростатическое нанесение последующих слоев покрытия. Грунтовка также защищает основание от потенциально вредного воздействия ультрафиолетового излучения от солнца, а также обеспечивает устойчивость к химическим веществам (бензину) и влажности.Часто составы грунтовок подбираются по цвету, чтобы обеспечить минимальную толщину пленки базового покрытия и свести к минимуму эффект отслаивания камня.
Basecoat — это слой покрытия, обеспечивающий большую часть цвета, физических характеристик и эстетических эффектов. Устойчивые к выцветанию базовые покрытия часто включают особую пигментацию внешнего вида, такую как металлическое покрытие, обычное для автомобильных покрытий. Базовые покрытия можно наносить в один или несколько слоев. В зависимости от метода нанесения, ультразвуковому датчику может быть сложно различить несколько слоев базового покрытия.
Стойкие прозрачные лаки образуют защитные поверхности от таких факторов окружающей среды, как травление, птичий помет, царапины от автомойки и каменные сколы. Хотя прозрачные лаки используются в сочетании с базовым покрытием для формирования окончательной отделки, акустически они обеспечивают значительную границу раздела между слоями покрытия и, таким образом, отличаются от ранее нанесенных слоев.
Рис. 12 PosiTector 200 B3 может вычислять среднее значение и стандартное отклонениесерии измерений для каждого слоя в многослойной системе.
Поскольку автомобильное покрытие — один из самых дорогостоящих процессов при сборке автомобилей, производители и сборщики постоянно ищут пути совершенствования технологий. Когда-то такой метод нанесения называется мокрым по мокрому, когда покрытия на водной основе наносятся непосредственно поверх друг друга, не позволяя предыдущим слоям отвердеть. Такие методы сводят к минимуму использование энергии, красок и требований к переоснащению, не жертвуя при этом качеством готового внешнего вида. К сожалению, нанесение покрытия «мокрым по мокрому» имеет тенденцию вызывать эффект «переходного слоя» (смешение отдельных слоев).Отсутствие четких акустических границ сводит к минимуму способность ультразвукового прибора определять толщину отдельного слоя.
Зачем проводить измерения с помощью ультразвука?
Производители и специалисты по нанесению покрытий давно считают, что не существует простых и надежных средств неразрушающего контроля покрытий на пластиковых подложках. Их обычным решением было разместить металлические (стальные или алюминиевые) купоны рядом с деталью, а затем измерить толщину, нанесенную на купон, с помощью механического или электронного (магнитного или вихретокового) манометра.Это трудоемкое решение основано на предположении, что плоский купон, помещенный в общую зону покрытия, получает тот же профиль окраски, что и рассматриваемая пластиковая деталь. Ультразвуковое решение позволяет пользователю измерить общую толщину покрытия реальной детали. В зависимости от используемого ультразвукового датчика и процесса нанесения покрытия дополнительным преимуществом является возможность идентифицировать несколько отдельных слоев.
Ультразвуковое измерение толщины покрытия в настоящее время является общепринятой и надежной программой контроля, используемой в деревообрабатывающей промышленности.Стандартный метод испытаний описан в ASTM D6132-08. «Стандартный метод испытаний для неразрушающего измерения толщины сухой пленки нанесенных органических покрытий с использованием ультразвукового датчика» (2008, ASTM). Для проверки калибровки манометра доступны стандарты толщины с эпоксидным покрытием, сертифицированные национальными организациями по стандартизации.
Теперь можно проводить быстрые неразрушающие измерения толщины материалов, которые ранее требовали разрушающего контроля или лабораторного анализа. Эта новая технология улучшает стабильность и производительность в отделочном цехе. Потенциальное снижение затрат включает:
- Минимизация отходов от чрезмерного покрытия за счет контроля толщины наносимого покрытия
- Минимизация переделок и ремонта за счет прямой обратной связи с оператором и улучшенного управления процессом
- Устранение необходимости уничтожать или ремонтировать объекты путем снятия измерения толщины разрушающего покрытия.
Сегодня эти инструменты просты в эксплуатации, доступны по цене и надежны.
Где рынок?
За последние несколько лет использование пластмасс быстро расширилось.Хотя автомобильная промышленность, безусловно, является лидером, другие отрасли также широко используют пластмассы. По данным Общества производителей пластмасс, прочие изделия из пластмасс (на долю которых приходится большая часть отрасли по переработке пластмасс) являются четвертой по величине обрабатывающей промышленностью в Соединенных Штатах. Его превосходят только автомобили и оборудование, нефтепереработка, электронные компоненты и аксессуары. Хотя пластмассы часто окрашиваются непосредственно в процессе производства, многие пластмассовые детали необходимо красить, чтобы улучшить внешний вид, добиться соответствия цвета другим деталям, повысить стабильность пластмассовой поверхности или добиться желаемого особого эффекта.
По данным консультанта PG Phillips & Associates, в 2001 году мировой рынок автомобильных красок составил 6,6 миллиарда долларов. Растущая доля этого рынка включает покрытие из пластика, используемого для бамперов, внешних панелей и декоративной отделки. Специалисты по нанесению покрытий и сборщики в конкурентной автомобильной промышленности должны соответствовать критическим эстетическим критериям и критериям ожидаемого срока службы. Поскольку покраска является наиболее дорогостоящим процессом в автомобилестроении, существует конфликтующий приоритет — минимизировать количество времени, материалов и необходимых доработок, при этом соблюдая требования технологии повышения производительности и соблюдения экологических требований. Таким образом, необходим эффективный метод измерения для точного и надежного обнаружения и исправления проблем нанесения как можно раньше в процессе нанесения покрытия.
Связующее вещество
Связующее вещество используется для распространения ультразвуковых колебаний от датчика на покрытие. Вода — хорошее связующее для гладких покрытий. Для более грубых покрытий используйте прилагаемый гликоль-гель. Хотя маловероятно, что связующее вещество повредит отделку или оставит пятно на поверхности, мы предлагаем протестировать поверхность, используя контактное средство на образце.Если тестирование показывает, что произошло окрашивание, вместо контактной жидкости можно использовать небольшое количество воды. Обратитесь к паспорту безопасности материала, доступному на нашем веб-сайте, и у поставщика покрытия, если вы подозреваете, что контактная смазка может повредить покрытие. Также можно использовать другие жидкости, такие как жидкое мыло.
Режим памяти
Стандартные модели PosiTector 200 могут записывать 250 измерений. Модели PosiTector 200 Advanced могут сохранять 100 000 измерений в 1000 пакетов для статистических целей на экране, для печати на дополнительный беспроводной принтер Bluetooth или для загрузки на персональный компьютер с помощью прилагаемого USB-кабеля и одного из решений PosiSoft.
Инструменты для измерения толщины | Sciencing
Инструменты для измерения толщины бывают всех размеров и форм, с различными диапазонами измерения и методами. Измерение толщины важно во многих отраслях промышленности, и есть области, такие как аэронавтика, где толщина материала должна быть очень точной, иначе результаты могут быть катастрофическими. Инструменты для измерения толщины могут быть механическими или цифровыми.
Штангенциркуль
Штангенциркуль — это высокоточный измерительный инструмент, который можно использовать в различных типах измерений.Он может измерять толщину, диаметр и даже внутренний диаметр труб. Он состоит из двух губок для измерения толщины, двух губок меньшего размера для измерения внутреннего диаметра и ручки со шкалой. Нижняя губка для измерения толщины соединена с нижней меньшей губой, и на всей детали также есть другая шкала. Комплект скользит по рукоятке штангенциркуля, когда вы открываете губки для измерения, а комбинация двух шкал дает точное измерение. Штангенциркуль имеет ошибку считывания 0.05 мм.
Микрометр
Микрометр — самый точный механический измерительный инструмент. Он состоит из наперстка с вращающимся винтом на одном конце и рамы на другом конце. Внутри гильзы шпиндель движется вместе с винтом. Измеряемый объект вставляется в рамку между шпинделем и опорой, расположенной на противоположном конце рамки, и винт вращается до тех пор, пока объект не будет зафиксирован между шпинделем и опорой. Есть две шкалы для чтения, одна из которых расположена на наперстке, а другая — на корпусе, над которым вращается наперсток, называемом стволом.Погрешность считывания микрометров составляет около 0,003 мм.
Системы измерения толщины пленки
Эти системы используются для измерения толщины пленок или других полупроводниковых материалов. Измерение проводится с использованием отражений света и компьютера для обработки и отображения показаний. Диапазон измерения толщины от 1 нм до 1 мм. Эти системы обычно используются в научных лабораториях, и их главный недостаток — их цена, которая может доходить до десятков тысяч долларов.
Измерение толщины с помощью бесконтактных датчиков
Общие указания по применению LA05-0021
Авторские права © Lion Precision, 2013 г. www.lionprecision.com
Резюме:
Подробно описаны два метода бесконтактного измерения толщины проводящей цели: одноканальный (хорошо) и двухканальный (наилучший). Предупреждает о распространенных ошибках.
Одноканальный метод
Рис. 1. Измерения толщины в одноканальном режиме предполагают, что деталь плоская и идеально прилегает к эталону.
При одноканальном измерении толщины (рис. 1) измеряется положение верхней поверхности испытуемой детали, когда деталь опирается на контрольную поверхность. Как и во многих бесконтактных приложениях, внутрипроизводственные измерения относятся к эталонным измерениям. Известная толщина устанавливается в качестве контрольной точки, и все последующие измерения показывают величину отклонения от этой контрольной точки.
Базовая одноканальная процедура
1. Поместите деталь известной толщины на контрольную поверхность.
Рисунок 2 — Деформированные детали и эталонные поверхности или посторонние предметы между эталоном и деталью создают ошибку измерения толщины в одноканальных системах.
2. Отрегулируйте датчик, чтобы измерить верхнюю поверхность детали. Датчик следует располагать около центра диапазона измерения, чтобы учесть положительные и отрицательные отклонения от эталонного измерения.
3. Если возможно, настройте выходной сигнал датчика на ноль вольт или отображаемое значение нуля, если используется дисплей измерений.В противном случае запишите «основное» измерение для справки при измерении тестовых деталей.
4. Замените эталонную деталь деталью, которую нужно измерить.
5. Считайте отклонение толщины на дисплее или вычислите отклонение от выходного напряжения.
Ограничения точности
Одноканальный метод предполагает, что деталь идеально ровная относительно контрольной поверхности. Любая деформация детали или контрольной поверхности приведет к ошибке измерения толщины.Кроме того, любые посторонние предметы, в том числе воздух, между деталью и эталонной поверхностью также вызовут ошибку (рис. 2).
Двухканальный метод
Рисунок 3 — системы Двухканальные компенсации деформаций в части или опорной поверхности путем измерения изменений в положении нижней и верхней поверхности части в.
Двухканальные измерения толщины помещают измеряемую деталь между двумя датчиками (рис. 3). Каждая сторона детали измеряется отдельным датчиком.Сумма измерений двух датчиков дает окончательное измерение толщины (рис. 4). Если деталь движется к одному датчику, она удаляется от другого; изменения на выходах датчиков взаимно отменяют друг друга. Это исключает ошибки, которые могут возникнуть в результате одноканальных проблем с деформацией и / или контактом с эталонной поверхностью.
Деталь может быть измерена с одним датчиком, установленный в опорной поверхности, или его часть может быть подвешена между двумя датчиками.
Как и во многих бесконтактных приложениях, измерения относятся к эталонному измерению. Известная толщина устанавливается в качестве контрольной точки, и все последующие измерения показывают величину отклонения от этой контрольной точки.
Базовая двухканальная процедура
Рисунок 4 — Суммирование двух каналов датчика дает выходной сигнал «только толщина» путем отмены изменений положения детали между датчиками.
1. Поместите часть известной толщины между двумя датчиками.
2. Отрегулируйте положение датчика, чтобы измерить верхнюю и нижнюю поверхности детали. Датчики следует располагать рядом с центром диапазона измерения, чтобы учесть положительные и отрицательные отклонения от эталонного измерения.
3. Если возможно, настройте выходы датчика на ноль вольт и отображаемое значение нуля при использовании дисплея измерений с возможностью суммирования (см. Рекомендации ниже).
4. Замените эталонную деталь деталью, которую нужно измерить.
5. Считайте отклонение толщины с дисплея с возможностью суммирования или вычислите отклонение, сложив два выходных напряжения и переведя их в размерные единицы.
Двухканальный пример
В проиллюстрированном примере используются два датчика, которые откалиброваны на 10 В / 1 мм. Условие 1 устанавливает цель толщиной 1 мм в качестве эталона при 0 вольт. Условие 2 показывает эффект приближения цели толщиной 1 мм к одному датчику. Условие 3 показывает нецентрированное измерение испытываемой детали, равное 1.Толщина 5 мм.
Важные предупреждения
Одной из самых больших проблем при проведении измерений толщины с высоким разрешением является конструкция системы крепления зонда и способ размещения исследуемого материала в зоне измерения.
Любые изменения расстояния между датчиком и целевой поверхностью будут регистрироваться как изменения толщины в системе с одним датчиком. Любые изменения расстояния между двумя датчиками в системе с двумя датчиками будут регистрироваться как изменение толщины.При проведении измерений на точном, субмикронном уровне перемещение системы крепления зонда, которое слишком мало, чтобы быть видимым, исказит результаты измерения.
Жесткое крепление зонда и позиционирование исследуемого материала имеют решающее значение для получения точных результатов. Любая вибрация, тепловое расширение / сжатие или другое движение датчиков или материала не позволит получить надежные результаты. Не относитесь к этому легкомысленно; если вы хотите измерить микроны, вы должны контролировать стабильность положения зонда лучше, чем микроны.
Проблемные примеры:
Горячий материал
Распространенное приложение для измерения толщины — контроль толщины материала, транспортируемого во время обработки. Иногда это означает, что материал горячий. В дополнение ко всем заботам о стабильности положения зонда и материала во время транспортировки (см. Ниже), горячий материал будет нагревать зонды. Все бесконтактные датчики обладают некоторой чувствительностью к изменениям температуры. Различная температура зондов будет означать разные измерения толщины.
Необходимо учитывать тепловые характеристики датчиков и рассчитывать их для конкретного применения; сдвиги из-за тепловых изменений должны быть меньше желаемой точности измерения толщины.
В более экстремальных случаях датчики могут перегреться сверх пределов окружающей среды и выйти из строя. При применении необходимо учитывать экологические характеристики зондов.
Толщина материала, проходящего через ролик
Биение ролика (радиальное смещение при вращении ролика) затрудняет измерение толщины из-за появления ошибок, часто превышающих желаемую точность измерения толщины.
Измерение толщины материала при его прохождении по ролику представляет собой сложную задачу.
«Биение» ролика (радиальное движение его поверхности при вращении) почти всегда превышает точность, необходимую для измерения толщины.
Метод с одним датчиком
Использование одного датчика непосредственно над роликом для контроля верхней поверхности материала не будет работать, если биение ролика не будет значительно меньше точности измерения толщины; это редко.При более экстремальном биении биение ролика может превышать диапазон измерения датчика, особенно если датчик небольшой.
Если измерения остаются в пределах допустимого диапазона, можно скомпенсировать биение роликов. Система может измерить биение ролика и вычесть его из измерения толщины. Но датчик, контролирующий биение, должен находиться рядом и в том же угловом положении, что и датчик толщины, потому что биение не одинаково во всех точках ролика.
Метод с двумя датчиками
Одним из подходов к решению проблемы биения ролика является использование метода двойного датчика, когда материал подвешивается непосредственно перед роликом или после него. В принципе, это разумная идея; однако материал по-прежнему отклоняется биением роликов, а также нестабильностью или биением других механизмов, поддерживающих материал. Метод двойного зонда минимизирует ошибки, поскольку материал перемещается вверх и вниз в зазоре между зондами, но эти движения не должны выходить за пределы диапазона измерения зондов.
Лучшие методы ультразвукового измерения толщины
Лучшие методы ультразвукового измерения толщины
В нефтегазовой сфере целостность активов не подлежит обсуждению.Крупные объекты инфраструктуры, в том числе трубопроводы, резервуары для хранения, большие поковки, бурильные трубы и концы куполов, должны регулярно проверяться на наличие признаков износа или ослабления из-за эрозии или истирания, которые проявляются в уменьшении толщины стенок. Они также должны быть проверены перед установкой на предмет дефектов. Уменьшение толщины стенок может указывать на надвигающийся отказ оборудования, который может стоить миллионы из-за простоя, потери продукта, штрафов и судебных исков.
Для измерения толщины металлических и неметаллических конструкций требуются специальные инструменты.Чтобы правильно измерить толщину и записать результаты, аналитикам следует предоставить три компонента на каждую инспекционную группу — эффективный сканер, портативный ультразвуковой прибор и эффективное программное обеспечение для анализа и составления отчетов. Стоимость инвестиций в надлежащее оборудование, обучение и время для ультразвукового измерения толщины значительно превышает предотвращение дорогостоящих и опасных отказов.
Какой сканер для ультразвукового измерения толщины лучше всего?
Сканеры, которые могут эффективно и действенно обнаруживать различия в толщине металлических и неметаллических структур с помощью ультразвуковой визуализации, как правило, обладают некоторыми общими характеристиками:
Способность плавно перемещаться как по изогнутым, так и по плоским поверхностям. Некоторые трубы, которые необходимо сканировать, имеют диаметр пяти дюймов или меньше, что требует существенно иной или гибкой геометрии сканера для прохождения. Если один и тот же сканер может измерять и то, и другое, общая стоимость владения снижается, как и необходимое пространство для хранения. Это также улучшает портативность и, следовательно, эффективность за счет уменьшения количества оборудования, которое техники должны перевозить в течение рабочего дня. Наконец, это избавляет от необходимости останавливать работу для переключения сканеров.
Значительная ширина. Даже на изогнутой поверхности сканеры перемещаются по двумерной траектории, чтобы отобразить область оси Z внизу. Их ширина X определяется шириной сканера. Их продвижение по длине их пути, Y, определяется скоростью, с которой они могут обрабатывать возврат своих ультразвуковых эхо (что на самом деле требует движения через четвертое измерение, которое можно описать как Y / T [время]). Более широкие сканеры увеличивают размер делителя, используемого для разделения общей площади, которую необходимо сканировать, уменьшая количество проходов, которые необходимо сделать (частное), и позволяя техническим специалистам быстрее выполнять свою работу. Сканеру шириной два дюйма требуется вдвое меньше времени на сканирование трубы, чем сканеру шириной в один дюйм.
Возможности точной визуализации. Дефекты и различия в толщине стенок, измеряемой в единичных и десятичных миллиметрах, могут привести к выходу оборудования из строя. Сканеры должны быть достаточно точными, чтобы отображать даже эти мелкие изъяны.
Выбор правильных сканеров во время закупок может повысить эффективность сотрудников, снизить затраты на проверки или увеличить объем проверок при тех же затратах.
Выбор ультразвуковых инструментов для эффективного измерения толщины
Сканерам требуется базовый прибор для питания и обработки данных, точно так же, как для камеры в телефоне требуется телефон. Правильный выбор ультразвуковых инструментов также может повысить эффективность работы сотрудников за счет увеличения времени обработки. Это позволяет сотрудникам быстрее перемещаться по оси Y данного сканирования, сокращая общее время, необходимое для сканирования данной области.
Другие факторы также влияют на общую стоимость каждого отдельного ультразвукового инструмента.Измерение толщины требует, чтобы сотрудники выезжали к физическому месту каждой трубы или резервуара, которые необходимо сканировать. Чем портативнее ультразвуковой прибор, тем легче сотрудникам путешествовать, что увеличивает объем сканирования, которое может быть выполнено. Ультразвуковые инструменты, которые заменяют традиционные терминалы с клавишами сенсорными экранами, более портативны, чем старые и большие модели.
Кроме того, места сканирования не обязательно должны располагаться в дружественной среде. Они могут подвергаться воздействию сильной жары, сильного холода, насыщения, вибрации и пыли.Ультразвуковые инструменты, которые созданы, чтобы выдерживать такие суровые условия, как правило, служат дольше, что увеличивает их ценность.
Важные программные возможности для ультразвукового измерения толщины
Интеллектуальное программное обеспечение требуется для сбора и интерпретации результатов ультразвуковых измерений толщины. Он также позволяет экспортировать и хранить информацию, создавать базы данных, которые можно использовать для подтверждения соответствия нормативным требованиям или для проведения исследований и анализа компании. Чем удобнее и функциональнее программное обеспечение, тем эффективнее смогут работать технические специалисты.Некоторые функции, улучшающие результаты сканирования:
- Немедленный анализ данных для отображения в реальном времени
- Визуальное представление уже отсканированных областей и областей, которые еще предстоит сканировать
- Сшивание составных данных, что позволяет техническим специалистам объединять меньшие отдельные участки сканирования в полную картину
- Хранение и программирование компиляции для систематизации результатов в отчеты, требующие действий.
- Легко экспортируемые структуры данных, позволяющие легко конвертировать в форматы Excel или текстовые форматы.
Пакеты программного обеспечения часто привязаны к определенным компонентам оборудования. При сравнении вариантов учитывайте общую стоимость, удобство использования и возможности программного обеспечения, надежность оборудования, а также гибкость и полезность сканера.
Важно отметить, что, хотя сами сканеры могут быть ограничены в своих приложениях измерениями толщины, ультразвуковой инструмент и программное обеспечение — нет. Тот же инструмент можно использовать с другим сканером для выполнения многих других необходимых ультразвуковых проверок. Эта изменчивость значительно увеличивает ценность этого оборудования, так как гарантирует, что его всегда можно использовать на полную мощность.
По адресу Zetec мы десятилетиями разрабатываем более эффективные методы и оборудование для ультразвукового измерения толщины. Чтобы узнать больше о наших решениях для ультразвукового и вихретокового неразрушающего контроля, , свяжитесь с сегодня!
Zetec являются ведущими специалистами в области ультразвуковых и вихретоковых технологий, и мы можем помочь вам сориентироваться в любом из наших решений или устройств для неразрушающего контроля.
Ультразвуковое измерение толщины с помощью EMAT: 5 преимуществ использования
Существует множество методов, используемых для измерения толщины в производственных условиях.Традиционные варианты измерения толщины включают изотопный, рентгеновский, лазерный оптический, пьезо-ультразвуковой и лазерный ультразвуковой. Эффективным, но малоиспользуемым методом является УЗИ, генерируемый ЭМАП (электромагнитно-акустическим преобразователем). EMAT генерирует ультразвуковые звуковые волны в исследуемом материале и измеряет время пролета (TOF) сигнала через деталь для расчета толщины.
Возможно, вы уже используете один из традиционных методов для удовлетворения ваших потребностей в проверке, но действительно ли эти методы лучше всего подходят для вашего приложения? Почему вам следует рассмотреть возможность использования EMAT для измерения толщины?
В отличие от традиционных датчиков Piezo UT, EMAT не использует жидкую связку для измерения толщины.Это на 100% сухой, бесконтактный метод. Это значительно упрощает автоматизацию и интеграцию. EMAT устраняет ошибки, вызванные связующим веществом, позволяет проводить проверки на высоких скоростях (до 60 м / с) и может выполнять проверки при высоких и отрицательных температурах.
Доступ с одной стороны
EMAT требуется только один датчик для точных измерений толщины. Традиционные методы, такие как изотопный, рентгеновский и лазерно-оптический, требуют наличия нескольких датчиков и двустороннего доступа для измерения толщины.
Измерение через шероховатые, масляные, окисленные или окрашенные поверхности
Поскольку сигнал EMAT генерируется в измеряемом материале, а не в датчике, на EMAT не влияют условия поверхности. Точные измерения легко получить с помощью покрытий, коррозии и загрязнений, которые могут сбить с толку или сделать недействительными другие методы.
Высокая точность
EMAT имеет точность до 12,7 мкм (0,0005 дюйма) с разрешением до 3 мм. Даже на высоких скоростях точность и разрешение, обеспечиваемые с помощью EMAT, не меняются.
100% сейф
EMAT не связан с опасностями и расходами, связанными с радиационными методами, такими как рентгеновские лучи и изотопы. Отсутствие необходимости в жидких связующих веществах исключает расходы, связанные с транспортировкой, хранением и утилизацией.
Заключение
Использование EMAT дает множество преимуществ по сравнению с традиционными методами измерения толщины, и эти преимущества превращаются в эффективную высокоскоростную систему сканирования для интегрированных заводских проверок измерения толщины.
Как измерить толщину тонкопленочного покрытия
Не можете измерить покрытие? Мы обсуждаем, как измерить толщину тонкопленочного покрытия.
В SilcoTek® мы специализируемся на нанесении ультратонких покрытий на нержавеющую сталь и другие металлические сплавы, стекло и керамические поверхности. Мы часто измеряем толщину нашего покрытия в рамках контроля качества и разработки покрытий. Мы узнали, что измерение тонких кремниевых покрытий может быть непростой задачей. Вот несколько советов, как измерить толщину покрытия.
Есть вопрос об этом блоге или об измерении толщины покрытия? Щелкните поле ниже, чтобы обсудить вашу заявку с одним из наших специалистов по покрытиям.
Есть вопрос? Свяжитесь с нашей командой технической поддержки
Из этого сообщения в блоге вы узнаете:
|
На заре разработки покрытий SilcoTek (30+ лет назад) наши знания о методах измерения покрытий ограничивались лишь несколькими довольно дорогостоящими методами испытаний. Мы обнаружили, что другие методы измерения толщины просто не обладают точностью и способностью измерять сверхтонкое силиконовое покрытие на нержавеющей стали.С тех первых дней разработки покрытий методом проб и ошибок мы узнали, что работает, а что нет, когда дело доходит до измерения покрытия CVD.
Хотите узнать больше о том, как оценить и охарактеризовать покрытие? Прочтите нашу публикацию в блоге о характеристиках поверхностей.
Вот несколько примеров инструментов и методов измерения толщины покрытия. Если у вас есть вопрос о наших покрытиях, наша команда технической поддержки готова помочь вам выбрать лучшее покрытие для вашего применения.
Наша команда может:
Хотите получить более подробную информацию о наших покрытиях и узнать, как они повышают производительность продуктов и процессов в сложных условиях?
Перейти на страницу наших приложений для нанесения покрытий
Инструменты для измерения толщины покрытия
Оже-электронная спектроскопия (AES)
Этот метод разрушения широко используется в материаловедении для оценки состава поверхности. Это также удобно для оценки точной глубины покрытия.В приведенном ниже примере показан состав и глубина образца покрытия из дурсана. Обратите внимание, как четко очерчена зона диффузии кремний / сталь. Узнайте, как SilcoTek создает зону диффузии, прочитав о нашей технологии покрытия.
Метод AES измеряет материал, который отрывается от поверхности, когда на поверхность фокусируется электронный луч. Электронный пучок проникает в поверхность, и характеристики материала измеряются детектором по мере испускания распыленного материала.
ОборудованиеAES может быть дорогим и требовать специальных знаний для работы. Это также может занять много времени и разрушительно для поверхности, поэтому AES не является реалистичным инструментом быстрого измерения для оценки поверхности в полевых условиях или при добыче.
Есть еще вопросы о том, как оценить покрытие или о наших покрытиях в целом? Перейдите на нашу страницу часто задаваемых вопросов.
Секционная и оптическая техника
Проверенный и проверенный метод оценки толщины. Разделение детали пополам и оптическое измерение толщины покрытия может быть эффективным инструментом для измерения толщины покрытия микронного уровня. Однако может быть трудно измерить точный переход покрытия к основной поверхности и, конечно, это разрушительный тест. Опять же, это не реалистичный инструмент для быстрого измерения в полевых условиях. Точность ограничена, особенно при измерении покрытий субмикронной толщины.
F20 Анализатор тонких пленок
Анализатор тонких пленок SilcoTek F20 — это настольный прибор, который можно настроить для измерения толщины тонких пленок (от 30 до 350 мм), оптических констант, таких как показатель преломления, коэффициент экстинкции и коэффициент пропускания.В основном он используется SilcoTek как быстрый, точный и неразрушающий способ измерения толщины поверхности и обеспечения стабильного качества покрытия. Анализатор полагается на преломление света, когда он проходит через тонкую поверхность, отражается от базовой поверхности, а затем снова проходит через покрытие. Прибор измеряет изменение, вызванное рефракцией, и соотносит это изменение со стандартами толщины. Материал основы, шероховатость поверхности и показатель преломления покрытия могут сыграть большую роль в эффективности и надежности этого метода измерения.
Рентгенофлуоресцентные анализаторы (XRF и ED-XRFA) и рентгеновская спектрометрия
Используемый в основном в цехах нанесения покрытий для измерения толщины металлического покрытия, XRF может быть относительно дешевым методом измерения толщины покрытия. Поверхность облучается рентгеновским излучением, покрытие и основной материал вызывают рентгеновское флуоресцентное излучение. Поверхность покрытия будет ослаблять излучение основного материала, позволяя прибору соотносить толщину между излучением покрытия и излучением основного материала.Этот метод является неразрушающим и может быть эффективным для измерения на субмикронном уровне. XRF эффективен для измерения большинства элементов и сплавов, но не органических материалов. Этот метод обычно используется при отделке металла.
Магнитоиндукционные и вытяжные манометры
Магнитные приборы для измерения натяжения или электромагнитной индукции основаны на разнице между магнитным основным металлом и непроводящим покрытием (например, краской).Чем гуще краска, тем меньше усилий нужно для отрыва калибра. Это может быть эффективным полевым испытанием для грубой оценки толщины покрытия, но не эффективным для очень тонких покрытий или проводящих покрытий. Электромагнитные измерительные приборы могут иметь точность + 1%.
Ультразвуковое измерение
Эти ручные инструменты измеряют толщину покрытия на металлических материалах, т. Е. краска на деревянной поверхности, например. Существует быстрый неразрушающий способ измерения толщины покрытия, но не для покрытия на металлической поверхности.
Гравиметрическое сравнение
В основном измерение веса детали с покрытием и без покрытия.