Антикор для авто своими руками – инструкция, как делать
Первый враг автовладельца, который хочет сохранить свой автомобиль недолго – коррозия кузова. Предупредить ее можно, полностью обработав его специальными препаратами. Такую услугу предлагают профессионалы, но далеко не всегда это то, что вам нужно.
Есть несколько видов работ, которые называют общим термином “антикоробработка”. Все они именуются так с полным правом и имеют право на существование, но каждый уместен в своем случае.
- Нанесение защитной мастики (битумной или иной) на открытые участки снизу кузова – днище и колесные арки. Самый распространенный вид работ, который, однако, решает вопрос защиты только самых доступных частей кузова – а это даже не половина всех проблем, которые несет кузову коррозия.
Если старый антикор не отслаивается из-за ржавчины, его можно обновить защитным составом, без помощи препарата с ингибитором. Но с порогами, лонжеронами и прочими закрытыми объемами такое не пройдет.
- Задувка скрытых полостей. Самая опасная коррозия – та, которая невидимо развивается в дверях, порогах, лонжеронах, балках и других несущих частях кузова. Чтобы покрыть антикоррозионным материалом эти труднодоступные объемы, специальный распылитель нужно завести в указанные полости. В большинстве случаев мастера делают это через отверстия – имеющиеся (так называемые технологические) и специально просверленные.
- Полная антикоробработка с частичной разборкой автомобиля. За этот громоздкий процесс берутся только избранные мастера, зато он гарантирует действительно эффективную защиту металла от ржавления. Чаще всего этот способ избирают те, кто хочет проделать работу своими руками – чтобы сделать все на 100 % правильно и сэкономить деньги.
Читайте также: Как быстро высушить салон после дождя
Прежде чем перейти к алгоритму полной задувки кузова, напомним, что строго говоря, любой вид антикорбоработки должен включать в себя первым делом уничтожение имеющихся очагов коррозии, и только затем – нанесение того или иного защитного слоя. Первая задача во многих случаях решается применением препаратов с ингибиторами, вторая – защитными антикорами. То есть новый автомобиль можно задувать сразу защитными восковыми или битумными составами, а машины, в скрытых полостях которых уже имеется ржавчина, придется обрабатывать поочередно двумя препаратами.
К слову, одна из причин, по которой ответственным автомобилистам приходится делать антикор своими руками, в том, что фирменные СТО с полным комплексом антикоробработки, работают только в больших городах. А гаражные умельцы – при всем к ним уважении – предлагают только второй этап обработки, причем с использованием народных смесей на основе пушечного сала, которое бессильно против уже начавшейся коррозии.
Залог успеха – в распылителе на конце шланга-удлинителя. Для жидких составов его отверстия должны быть до 1,0 мм, подходит наконечник от шланга аэрозольного баллона с “Мовилем” (на фото самый тонкий).
Инструменты
Вам понадобится:
- препараты соответствующего назначения: защитно-консервирующий и (если машина не новая) – состав с ингибитором.
По нормам фирменных СТО на автомобиль нужно 2,0 – 2,5 л препарата каждого типа, но практика показывает, что неопытный мастер-автолюбитель в стремлении к идеалу расходует вдвое больше.
- компрессор с давлением 4-6 атм (можно взять в аренду)
- стандартный пистолет для задувки “под евробанку” (продается в автомагазинах как пистолет “для гравитекса”)
- евробанка (придется купить нечто, в нее упакованное – например, гравитекс).
- трубка с распылителем на конце. Важное замечание: отверстия распылителя должны быть диаметром 0,8 – 1,0 мм, расположены радиально в количестве 4 – 6 штук. Для задувки дверей нужен будет распылитель дополнительно с одним отверстием на торце. Трубки из комплекта пистолета обычно имеют отверстия большего диаметра, но нужный распылитель можно купить вместе с аэрозольным баллоном для задувки препарата типа “Мовиль” – придется только помудрить, чтобы состыковать трубки разного диаметра со штуцером пистолета.
Читайте также: Как сделать шумоизоляцию авто своими руками
Да, покупка и аренда инструмента потребует некоторых расходов, но они не идут ни в какое сравнение с ценами на подобные виды работ на СТО.
Подготовка
Чтобы сделать все качественно, придется разобрать салон, снять подкрылки и некоторые узлы под капотом (в зависимости от модели авто). Самое трудное здесь – не сломать пластиковые детали, в особенности в местах крепления у ним крепежных пистонов. Потолок, торпедо и те элементы интерьера, которые останутся на местах, нужно оклеить защитной пленкой и малярным скотчем – препараты под давлением при малейшей неаккуратности будут разбрызгиваться во все стороны.
К задувке машину нужно готовить: удалить отделку салона, просверлить отверстия в недоступные полости, снять некоторые детали под капотом, подкрылки, накладки и пр. То, что осталось в салоне, закрыть пленкой.
К слову, качественные антикоры уважаемых брендов не вредят краске и после некоторых усилий отмываются даже со светлой обивки потолка (проверено!).
Все закрытые объемы нужно продуть сжатым воздухом – в дверях и балках под днищем могут быть скопления пыли и песка. Собственно, в идеале нижнюю часть кузова и прилегающие к нему доступные объемы нужно промыть мойкой высокого давления и тщательно высушить.
Настройка оборудования
Очень важно перед работой отладить работу распылителя: вы должны быть уверены, что жидкость безупречно распыляется даже тогда, когда трубка с распылителем находится внутри закрытой детали и вы не можете контролировать качество распыла. А оно зависит от давления воздуха, длины трубки чистоты отверстий, особенностей пистолета. Имейте в виду, что в некоторых случаях качественное распыление происходит только в момент нажатия на курок пистолета и после его отпускания, а при длительном нажатии на курок распылитель распыляет только воздух.
Распылитель должен давать симметричные конусы препарата, которые охватят все пространство на 360 градусов. Диаметр отверстий на фото – 1,0 мм.
Поэтому “отрепетируйте” работу оборудования, когда распылитель находится на виду, под вашим контролем, играя курком и наблюдая за подачей жидкости через прозрачную трубку. Возможно, на протяжении задувки вам придется все время нажимать и отпускать курок, добиваясь непрерывного распыления. Также подача жидкости будет нарушаться при наклонах неполного баллона.
Куда дуть
Места, которые нужно покрыть антикором, известны всем бывалым автомобилистам. Для многих популярных моделей имеются фирменные карты задувки с указанием всех полостей и отверстий, через которые к ним можно добраться. Неоценимые советы в этом плане даст сварщик-рихтовщик, которому приходилось ремонтировать подобную вашей модель после ДТП или коррозионных разрушений.
Читайте также: Что делать, чтобы уберечь кузов от корозии
Нанесение антикора
Открытые поверхности и замкнутые детали небольшой протяженности можно задувать без трубки, коротким наконечником пистолета, учтите лишь, что в таком случае жидкость подается щедро и нажатия на спуск должны быть короткими – во избежание перерасхода.
Закрытые детали большой протяженности задувайте трубкой, вводя ее на максимальную глубину и вытягивая на себя при нажатом спуске пистолета.
На этом фото – простейший вариант антикоробработки: пистолет без шланга-удлинителя и напыление на легкодоступную поверхность колесных арок.
Не постесняйтесь собирать препарат, который будет стекать через отверстия, щели и сварочные швы – подставляйте под машину тару типа классических консервных банок. После простейшей фильтрации его можно будет использовать повторно (если не хватит чистого препарата). Имейте под рукой ветошь, чтобы вытирать подтеки.
Если вы используете последовательно два препарата (с ингибитором и консервирующий), не забудьте выдержать паузу между ними согласно рекомендаций производителя.
Рекомендации Авто24
Собственно нанесение препарата не займет и половины времени, которое вам придется потратить на данную процедуру в целом – настройтесь на подготовительные работы немалого объема. Будьте готовы к тому, что вас ждет не очень чистая работа, но пусть вас утешает уверенность в том, что вы гарантированно защитили вашу машину от ржавления на многие годы.
Читайте также: Как защитить кузов автомобиля: ТОП-5 способов
Антикоррозийная обработка автомобиля в гаражных условиях
Для того, чтобы сохранить внешний вид машины и сделать его стойким к образованию коррозии, необходимо периодически своими руками делать антикоррозионную обработку днища и арок.
Фабричные мастики, которые наносят на днище и колесные арки для поглощения шумов от дороги, слегка защищают металл от неблагоприятных воздействий. Кроме того, состав обычно наносится до окрашивания, предварительно прикрывая все шпильки и резьбовые отверстия специальными наклейками. При сборке они все снимаются, а участки днища оголяются, а металл становится уязвим к механическим воздействиям. В связи с этим лучший антикор – это тот, который вы сделаете самостоятельно.
к содержанию ↑Как подготовить машину?
Особенно важную роль защита днища машины от коррозии играет в зимнее время. Суровые погодные условия и наличие соли с химическими реагентами на дорогах обязательно напоминают о себе с наступлением весны. Приходится не только счищать ржавчины с днища авто, но иногда и проваривать определенные участки.
Обработка арок
Перед тем, как наносить антикоррозионную защиту на днище автомобиля, надо счистить ржавчину. Начать следует с ближайшей автомойки, где вашу машину хорошо отмоют. Затем транспорт следует загнать в гараж или оставить во дворе, если вы планируете работать на улице. В любом случае вам понадобится эстакада, яма или подъемник.
Для чистки коррозии вам потребуются ершики разного диаметра, болгарка или простая дрель. Сначала нужно демонтировать подкрылки, так как ржавчина часто начинает образовываться на лонжеронах.
После капитальной чистки до нанесения антикора своими руками днище необходимо обработать преобразователем ржавчины. Лучше покупайте составы на основе цинка. Покрыв этим средством все поверхности под машиной, оставьте все на несколько часов, а лучше на сутки. После этого нужно приступить к замешиванию антикора.
Что потребуется для работы?
Для защиты днища авто от коррозии антикором можно использовать различные консерванты для скрытых полостей, антигравийные покрытия, составы для днища, материалы для арок и внутренних частей крыльев. Все они нужны для предотвращения преждевременного образования ржавчины.
Для днища
Антикор для днища
Цена на антикор для днища машины не очень высока, но эти составы формируют эластичную, высокопрочную и достаточно толстую пленку для защиты поверхностей от негативных воздействий. Наносить материалы нужно на очищенную и предварительно загрунтованную поверхность. В антикоре содержатся специальные наполнители, например, мельчайший алюминиевый порошок. Также в составе всегда есть ингибиторы коррозии, замедляющие ее образование.
В домашних условиях антикор можно наносить обыкновенной кисточкой, а что касается материалов отечественного производства, наиболее доступными по цене и распространенными являются битумные мастики с резиновой крошкой.
к содержанию ↑Еще одной задачей, с которой справляется мастика, является повышение виброакустических характеристик кузова. Для этого и предназначена резиновая крошка.
Антикор для арок
Антикор для арок
Специальные антикоррозионные составы для арок обладают теми же свойствами, что вышеупомянутые материалы, но есть одна особенность. Арки имеют меньшую защиту от абразивного износа, чем днище. Они постоянно подвергаются воздействию снега, мокрой грязи, песка, льда и камней, которые вылетают из колес и бьют по поверхностям арок. Если вы их не защитите, коррозия неизбежно начнет образовываться уже через несколько лет даже на новом авто.
Можно вставить пластиковые подкрылки в арки колес, которые решат проблему, но также вы можете приобрести специальный Жидкий Локер, представляющий собой высокопрочный эластичный материал. При нанесении его на поверхность арок формируется слой, предохраняющий металл от абразивного износа.
При желании на внутренние части колесных арок вы можете нанести своими руками антикор для днища, но сделать это в два слоя. Подобно составам для днища, в арочных материалах присутствуют ингибиторы коррозии.
Для скрытых полостей
В любом автомобиле имеются многочисленные скрытые полости:
- стойки;
- пороги;
- лонжероны;
- усилители багажника;
- усилители пола.
Rust Stop
Получить к ним доступ можно только сквозь особые технологические отверстия. Так называемые консерванты для скрытых полостей представляют собой маловязкие жидкие материалы, похожие на моторное масло, содержащие в составе ингибиторы коррозии. Они формируют полувысыхающую пленку на стенках полостей, отличаются уникальной проникающей способностью и способны вытеснять влагу с металлических поверхностей.
Наиболее известным отечественным консервантом для полостей является Мовиль. Он выпускается несколько десятков лет и по-прежнему остается актуальным. Неэкологичный состав обеспечивает надежную антикоррозионную защиту днища машины.
Мы также не советуем покупать средства от компании Waxoil, так как в нем всего 13 процентов сухого остатка, а остальные 87 – это растворители. Отсутствие запаха указывает на высокую степень очистки растворителей, но это не самое главное, если вы хотите сделать антикор днища своими руками.
Существует также состав марки Rust Stop, который создается на базе минерального масла. Он очень гигроскопичен, поэтому обрабатывать им скрытые полости лучше не менее одно раза в два года, иначе вы получите обратный эффект: лишняя влага будет стимулировать развитие ржавчины.
Как наносить антикор?
Обработка колесных арок и днища авто антикором самостоятельно – достаточно распространенная услуга в специализированных сервисных центрах, но вы можете справиться самостоятельно при помощи нашей инструкции. Готовиться к работе и обрабатывать днище необходимо на смотровой яме или подъемнике.
Для начала снимаются подкрылки и обрабатываются скрытые поверхности:
- поперечины;
- пороги;
- внутренние полости лонжеронов;
- полости в кронштейнах;
- усилители и пр.
Нужно тщательно обработать все сварные швы.
Распыляя антикор, укладывайте его ровным слоем на имеющееся покрытие.
Распыление антикора
При обработке моторного отсека или капота есть определенные тонкости. Нельзя допускать попадания средства на генератор, приводные ремни и соты радиатора. Состав вызовет проскальзывание ремней, ухудшение охлаждения мотора или испортит узел зарядки АКБ.
Под капотом нужно обработать все сварные швы, а также не забыть покрыть площадку под аккумулятором и поверхности вокруг фар. Особое внимание уделите следующим деталям и элементам в подкапотном пространстве:
- передние лонжероны;
- усилители подвески;
- цилиндр сцепления;
- моторный щит;
- место крепления усилителя тормозов;
- все крепежные элементы.
Важно обработать всю крышку капота по сварным швам и внутри усилителей.
После этого можно перейти в багажный отсек. Здесь нужно сконцентрироваться на сварных швах, а чтобы добраться до труднодоступных мест используйте различные насадки. Наносите материал тонким слоем на пол багажного отделения и обязательно покройте заднюю сторону задних фонарей во избежание окисления контактов.
Перед обработкой салона нужно тщательно осмотреть все места, куда вы планируете наносить состав. Первоначально надо обеспечить удобный доступ ко всем поверхностям, чтобы не пришлось останавливаться в процессе работы. Уделите особое внимание коробчатым элементам, которые испытывают высокие нагрузки – точки крепления кронштейнов и поперечин сидений. Их лучше обрабатывать изнутри тоже, используя технологические отверстия.
Дальше можно приступить к обработке дверного проема по всем швам и уплотнителям снизу. Заранее обеспечьте доступ к поверхностям, удалив накладку порога. Вы увидите специальные технологические отверстия, через которые можно заполнить скрытые полости. Действуйте осторожно, распыляя антикор своими руками. Не разбрызгивайте состав, чтобы не испачкать салон – отмыть будет очень непросто.
Обрабатывая двери, уделите особое внимание механизмам, которые скрыты в полостях двери. В целом современные составы для антикора днища авто своими руками не навредят электрическим контактам. Испортить что-либо вы можете только механическим путем, вводя насадку в ту или иную скрытую полость. Если внутренние части двери перегружены дополнительными элементами, можете воспользоваться технологическими отверстиями в нижней части.
Видео:
Видео:
Как сделать антикоррозионную обработку автомобиля своими руками
Коррозия автомобиля является неизбежным процессом, который происходит с машиной так же, как и с любым другим физическим телом. В настоящее время придумано много способов избавления от коррозии и некоторые из них весьма эффективны. Однако самым лучшим способом борьбы с коррозийными процессами является их профилактика или предотвращение. Рассмотрим, как выполняется антикоррозийная обработка авто своими руками.
Для предотвращения коррозии необходимо делать специальную обработку автомобияВиды коррозии в автомашинах
Различают несколько типов коррозийных повреждений:
- Косметическая коррозия возникает в местах соприкосновения различных аксессуаров: таких как фонари, молдинги, радиаторная решётка и других.
Ржавчина на таких местах легко счищается на начальной стадии. Её нужно устранить на начальной стадии, иначе она развивается и превращается в следующие виды коррозии. Лучший способ профилактики — недопущение появления таких очагов ржавчины.
- Подплёночная коррозия развивается под лакокрасочным или иным покрытием. Она проявляется в виде гнёзд ржавчины или пузырьков и локальных вздутий краски. Пятна такой коррозии быстро разрастаются как вглубь, так и в ширину.
- Сквозная коррозия является заключительной стадией подплёночной коррозии в том случае, если её вовремя не остановить. На этом этапе возникают сквозные отверстия, а пятна ржавчины на металле можно без усилия проткнуть даже простой отвёрткой.
- Точечная коррозия является разновидностью подплёночной и часто предшествует сквозной коррозии. В этом случае точки поражения растут вглубь металла.
- Пятновидная коррозия представляет собой появление повреждений в виде пятен, которые захватывают всё большую часть поверхности и на конечном этапе приводят к полному разрушению всего кузова.
Виды антикоррозионной обработки
В зависимости от типов повреждений металла, а также их локализации, существуют различные виды антикоррозионной обработки. Самыми популярными способами являются:
- покрытие антикоррозионным составом;
- электромеханическая защита;
- оклейка виниловой плёнкой.
Основные способы антикоррозионной обработки автомобиля своими руками
Антикоррозионная обработка авто своими руками теоретически может выполняться любым из перечисленных выше способов. Но на практике, а особенно в случае выполнения работы самостоятельно автолюбители защищают свои машины от ржавчины путём нанесения различных защитных составов.
Все антикоррозионные средства, применяемые для этого, бывают густыми и жидкими.
Антикор для днища автомобиля и колёсных арок имеет густую консистенцию. Его можно наносить вручную и с помощью пистолета-распылителя. Любой человек, который хоть раз держал в руках кисточку, способен сделать антикоррозийную обработку своего транспортного средства.
Жидкие вещества применяются для обработки дверей и порогов автомашины. Они распыляются с помощью специального пистолета, работающего под давлением. Для обработки локальных поверхностей или узлов используются жидкие средства в аэрозольных баллончиках.
Антикоррозийные материалы по составу делятся на металлические и неметаллические:
- Металлические составы имеют частицы цинка, алюминия, олова и свинца, то есть металлов, которые не боятся коррозии. Они, например, используются для обработки деталей, испытывающих влияние значительных температурных колебаний. Но для их использования обязательно применение пистолетов-распылителей.
- Неметаллические антикоррозионные составы отлично наносятся вручную, простыми малярными кистями. Они изготавливаются из эпоксидных и полиэфирных смол. Применение таких неметаллических антикоррозионных составов обычно не требует каких-либо специальных навыков, и они пользуются наибольшей популярностью среди автолюбителей.
Технология антикоррозионной обработки автомобиля своими руками
Рассмотрим, как сделать антикоррозийную обработку автомобиля самому.
Перед нанесением защитного состава сначала необходимо промыть покрываемые поверхности. Желательно при этом не использовать химические моющие средства, достаточно струи воды, подаваемой под большим давлением. Затем поверхности следует обезжирить с помощью чистой ветоши, намоченной уайт-спиритом.
Если после промывки на металле останутся следы коррозии, их следует очистить наждачной бумагой и снова протереть ветошью с обезжиривающим составом. В случае если очаги ржавчины и таким способом удалить не удаётся, можно попробовать применить специальный преобразователь ржавчины, изготовленный на основе ортофосфорной кислоты.
После этого самое время приступить собственно к покрытию поверхностей автомашины антикоррозионным слоем. Начать рекомендуется с обработки днища и колёсных арок. Для этого на поверхности этих частей автомобиля кистью равномерно наносится первый слой антикора, а после его высыхания — второй.
Время высыхания предварительно нанесённого слоя антикора можно использовать для обработки элементов кузова с помощью аэрозольного баллончика. Рекомендуется держать распылитель на расстоянии 30–40 см от защищаемой поверхности. Так состав распределяется более равномерно.
Один слой защитной мастики сохнет примерно 2–3 часа. Учитывая, что для эффективной защиты днища и колёсных арок лучше нанести 3–4 слоя, на полную обработку транспортного средства необходимо от 8 до 10 часов. Однако к этому времени ещё нужно добавить около 4–5 часов, необходимых для того, чтобы все слои антикоррозионного покрытия окончательно подсохли.
Зная, как сделать антикор своими руками, вы эффективно защитите автомобиль от ржавчины, продлите срок его службы и сэкономите немалое количество денег, которые иначе пришлось бы отдать за аналогичную работу специалистам на станции техобслуживания.
Если у вас уже есть опыт антикоррозийной обработки или вы знаете способы более эффективной защиты транспортного средства от ржавчины, нашим читателям было бы интересно узнать о них из комментариев к этой статье.
состав, цена и обработка автомобиля своими руками
Практически любой автовладелец, закрыв автомобиль и отойдя на некоторое расстояние, обязательно обернется, чтобы еще раз полюбоваться своей машиной и оценить ее состояние.
Автомобиль постоянно подвергается агрессивному действию окружающей среды. Главным врагом является влага – причина появления ржавчины.
Для защиты от нее детали машины необходимо обрабатывать антикоррозийным покрытием. Рынок средств для ухода за машинами предлагает много вариантов. Один из наиболее востребованных – обработка автомобиля пушечным салом.
Требования к антикоррозийному покрытию
Правильный антикор должен обладать следующими свойствами:
- Образовывать на металлической поверхности эластичную пленку.
- Обладать высокой степенью адгезии – сцеплению различных поверхностей в твердой или жидкой форме.
- Пропитывать не только ровные поверхности, но и проникать в трещины и впадины.
- Вытеснять накопившуюся влагу.
- Хорошо смачивать поверхность.
- Не должно высыхать.
- Не образовывать трещин, куда возможно проникновение воды.
- Не требовать особой подготовки поверхности.
- Обладать устойчивостью к механическому воздействию мелких частиц, поднимающихся с дорожного покрытия, – гравия, песка, камушек.
- Быть устойчивым к перепаду температур и сохранять свои характеристики в любое время года.
Применение пушечного сала удовлетворяет этим требованиям и создает надежную изоляцию от окружающей среды. Состав пушечного сала – нефтяное масло, которое загустили петролатумом и церезином. Для обеспечения эксплуатационных свойств добавляется антикоррозионная присадка.
Свое название покрытие получило из-за того, что сначала оно применялось для консервации артиллерийского оружия, в том числе пушек.
Преимущества пушечного сала
Основные особенности вещества:
- высокая степень эластичности;
- способность удерживаться на поверхности, не скатываясь с нее при нанесении и дальнейшей эксплуатации;
- отсутствие взаимодействия с водой, что позволяет успешно использовать на днище автомобиля;
- температурный диапазон использования – от минус 50° до плюс 50°C;
- защита от коррозии при действии морской воды и соляного тумана;
- область применения – черные и цветные металлические поверхности.
Визуально представляет собой однородную мазеобразную массу цветом от желтого до светло-коричневого. Продается в металлических банках или ведерках различной емкости. Расфасовка начинается с 1 кг.
Цена этого вида антикоррозийного покрытия является весьма демократичной. Для сравнения в таблице представлена стоимость в зависимости от объема и производителя.
Совет! Сэкономить на покупке можно, приобретая товар в магазинах, оказывающих свои услуги через интернет.
Подготовка
Перед тем, как наносить покрытие, следует подготовить все необходимое. Для проведения антикоррозийной обработки понадобится:
- пушечное сало в банке или ведре;
- средство для разведения;
- электроплитка или строительный фен;
- малярная кисть;
- шприц.
Особо следует поговорить о средстве для разведения. Существует несколько вариантов, чем разбавить пушечное сало до жидкого состояния.
Для этого могут применяться:
- бензин;
- растворитель;
- отработанное масло;
- мовиль;
- антикоррозийное средство типа RUST STOP.
Каждое из них имеет свои недостатки и преимущества. Растворитель обойдется несколько дороже. Свойства отработки зависят от того, какое изначально масло применялось.
Антикоррозийное средство RUST STOP относится к веществам, успешно борющимся с коррозией металла. Производитель – канадская фирма «A.M.T. Inc.».
Достоинство RUST STOP в том, что оно никогда не замерзает. Находясь в полужидком состоянии, это средство заполняет все трещины и царапины на металлической поверхности, не портя при этом резиновые детали. Слой ингибиторов коррозии надежно защищает поверхность от появления ржавчины.
Это антикоррозионное средство не требует особо тщательной подготовки обрабатываемой поверхности – наносить его можно и поверх незначительного слоя ржавчины. Вследствие этого значительно упрощается технология антикоррозионной обработки, уменьшается время на весь процесс. Дополнительный бонус – производитель применяет различные отдушки, например, вишневую или земляничную.
Информация! Добавление средства в пушечное сало придает ему антикоррозийные свойства и способствует лучшему расползанию. Ингибиторы снижают скорость коррозии.
Способ применения
Сначала надо подготовить машину. Необходимо снять все пластиковые детали, мешающие работе. Промыть поверхности, которые будут подвергнуты защите. Очистить следы коррозии. Обезжирить поверхность, протерев ее уайт-спиритом.
Затем следует подготовить пушечное сало. Эта работа заключается в разогревании и доведения его до консистенции густой сметаны. Разогревать можно на электрической плитке, постоянно помешивая. Возможно также использование строительного фена.
Минуты через две после окончания разогревания добавить в растопленное сало растворитель или антикоррозийное средство в пропорции 4:1. Раствор готов к употреблению.
Рекомендация! Наносить раствор на детали автомобиля следует достаточно быстро. Пушечное сало довольно быстро остывает и приобретает первоначальную консистенцию.
На большие поверхности раствор наносится малярной кистью. Обработка днища автомобиля пушечным салом предполагает, что машину надо приподнять на домкратах. Еще удобней будет работать, находясь в смотровой яме.
Внизу разумно подставить емкость, куда будут стекать или капать излишки. Наносить пушечное сало на поверхность следует широкими мазками. Каждый слой должен получаться толщиной 0,3-0,4 мм. При соприкосновении с холодным автомобилем сало быстро схватывается. После застывания поверх можно нанести еще один.
Было бы ошибкой обработать только наружные поверхности. Обязательно надо внимательно осмотреть салон и промазать металлические детали внутри него. Влага попадает внутрь машины через щели, способствуя возникновению там ржавчины.
Кроме больших поверхностей, работа с которыми не представляет большой трудности, придется заниматься более труднодоступными местами:
- залить жидкость через технологические отверстия в имеющиеся полости;
- обработать пороги и проемы дверей;
Вот тут-то и понадобится шприц, с помощью которого можно под давлением закачать антикор в необходимые полости.
Видео:
Затратив большее количество времени на тщательную обработку, владелец автомобиля сможет обеспечить себе спокойствие на несколько лет.
Необходимо соблюдать правила безопасности:
- работать в перчатках;
- обработку производить на открытом воздухе, при невозможности – в хорошо проветриваемом гараже;
- не оставлять без присмотра включенную электрическую печку.
Время, за которое образуется устойчивая пленка, составляет приблизительно 30 минут.
Видео:
Сравнение с другими видами – отзывы
Существует очень много форумов, где обсуждаются свойства различных антикоррозийных покрытий. Эта тема волнует практически всех автолюбителей. Задаются вопросы, делятся успешным опытом.
Отзывы об антикоре пушечное сало всегда носят положительный характер. Главным достоинством считается обеспечение спокойствия после обработки на долгие годы. При обсуждении вопроса типа «что лучше мовиль или пушечное сало» большинство участников рекомендуют последнее.
Предпочтение следует отдавать проверенным средствам. История применения пушечного сала исчисляется даже не годами, а десятилетиями. За это время оно отлично зарекомендовало себя.
Видео:
Загрузка…Антикоррозийная обработка автомобиля своими руками
Добро пожаловать!
Антикоррозийная обработка автомобиля – в ней нуждается каждая машина, без неё, те детали на которые попадёт влага, в скорем времени начнут гнить и вследствие чего, автомобиль потеряет свою прочность, как правило антикором выступают такие вещества как мовиль, мастика и другие, из этих двух веществ, каждая имеет свой цвет (Мастика чёрная) и поэтому их не пригодно наносить на лакокрасочное покрытие (Наносится только в том месте, где человеческий глаз их заметить не сможет, например днище автомобиля), благодаря обоим веществам, влага сдерживается и не просачивается через них просочится не может, наносятся они только на чистую поверхность, после нанесения, при попадании воды, на кузов она уже не попадёт, а будет скапливаться только на антикоррозийной обработки.
Примечание!
Для того чтобы осуществить процедуру по обработки автомобиля, нужна будет обязательно: Смотровая яма, если Вы днище решите обработать снизу, а так же отвёртки и другие инструменты, за счёт которых можно будет снять детали, которые будет препятствовать доступу к кузову (Например если в салоне днище будете обрабатывать, то можно сиденья снять, так гораздо удобней будет, для снятия сидений понадобятся ключи, гаечные и накидные)!
Краткое содержание:
Когда нужно делать антикоррозийную обработку автомобиля?
1. Прежде чем машину обрабатывать решите для себя на долго ли Вам автомобиль нужен, если Вы его собираетесь в ближайшее время продавать, то делать обработку вообще не имеет никакого смысла, ну только если при продаже, указать на факт хотите, что машина обработана но цена от этого на автомобиль не сильно изменится, а деньги свои и время Вы потратите.
2. Новый автомобиль или же старый не имеет значения, обрабатывать и тот и другой нужно, если брать во внимание автомобили ВАЗ то на заводе не очень хорошую обработку кузова делают, так сказать экономят на всём чём можно, поэтому после покупки, рекомендуем Вам найти время и заняться полной обработкой кузова у автомобиля.
3. И последний случай при котором обрабатывать автомобиль нужно, это смена времени года, а именно летом большинство водителей промазывают хорошенько днище у автомобиля, это и правильно, вить зимой дороги посыпают солью и тому подобными вещами и поэтому обработать кузов, не будет лишним, да и к тому же летом гораздо легче произвести обработку, так как на улице тепло, антикоррозийное покрытие быстро засохнет и днище особо от грязи не нужно будет очищать, просто выберите хорошую погоду и приступайте к обработки кузова автомобиля.
Как произвести антикоррозийную обработку автомобиля?
1. Прежде чем приступать к работе, выберите солнечный день и когда мало грязи будет на дорогах, затем подготовьте нужный инструмент и можно приступать к работе, все детали которые будут мешать снимаются (К таким деталям относятся локера, колёса, сиденья, ковролин и т.д.), если обрабатывать будете днище снизу, то его обязательно от грязи зачистить придётся, чтобы антикоррозийная защита пристыла хорошо (Грязь хорошо убирается кёрхером и горячей водой, при необходимости наждачной бумагой в тех местах где грязь не убралась пройдитесь), это самая главная часть при обработки кузова, если Вы не уберёте грязь, то толку от обработки ни какого не будет.
Примечание!
Если автомобиль был уже обработан чем то, то можно эту обработку не убирать, если она хорошенько пристыла, просто такую же обработку использовать повторно придётся!
2. После очистки днища, дождитесь пока всё высохнет, чтобы днище от воды долго не сохло, при помощи тёплого сжатого воздуха высушите воду и приступайте к нанесению материала, при помощи кисточки и кстати, толстый слой не делайте, это не к чему, потому что составу легче будет отслоится.
Примечание!
Наносите материал так, чтобы все стыки, все углы он закрыл, вообще антикоррозийную обработку лучше бы наносить методом воздушного распыления, так гораздо лучше материал на несется и будет именно небольшой слой, который ни влагу не пропустит, не песок, не гравий и при этом не отслоится в ближайшее время!
3. После обработки ждите чтобы материал схватился и чтобы он полностью высох, на это бывает уходит один, а то и два дня (Это зависит от материала и от того, как он нанесён), пока он сохнет, попытайтесь воздержаться от поездок или если всё таки придётся ехать, то старайтесь ехать чтобы как можно меньше грязи летело на днище автомобиля и чтобы днище не касалось не воды, не камней особо.
Дополнительный видео-ролик:
Как сделать так, чтобы глушитель автомобиля не ржавел — Российская газета
Не секрет, что за пару лет, а то и месяцев грязь, соли, реагенты, равно как летящие из-под колес камни, гравий и песок агрессивно воздействуют на кузов автомобиля, причем если ЛКП и обработанные антикором полости и элементы днища еще держат удар, то выхлопная система, в особенности ее внутренняя часть, сильно страдает — ее начинает в буквальном смысле пожирать ржавчина.
Все дело в том, что из-за конструктивных особенностей глушителя и разницы температур (особенно это актуально зимой) в задней банке глушителя скапливается конденсат, который и запускает процесс коррозии. Поэтому, как правило, при замене прохудившейся выхлопной системы опытные и рачительные владельцы доводят ее до ума, значительно увеличивая срок ее эксплуатации.
Спасительный дренаж
Что можно сделать в этих целях? Прежде всего, в глушителе нужно сделать дренаж — просверлить тонким сверлом отверстие в той самой задней «банке» глушителя. Это позволит значительно уменьшить скопление конденсата, что наилучшим образом скажется на долговечности глушителя.
В Сети можно найти много инструкций, где владельцы сверлят дыры в задней банке глушителя прямо в гаражах, не снимая элементы выпуска с машины. После такой процедуры из глушителя выливается порядочное — иногда до полулитра — количество воды. Комментарии, как говорится, излишни.
Отметим важный нюанс. На ряде новых моделей (в частности глушителях Lada Granta и Vesta) отверстие в банке уже предусмотрено, так что сверлить дополнительные не нужно. Если же технологического отверстия нет, потратьте немного времени на изучение конструкции глушителя вашего автомобиля. Дело в том, что некоторые модели имеют сложный конструктив с внутренними перегородками. В этом случае придется сделать не одно, а два или даже три отверстия.
Многосторонний антикор
После «продырявливания» приступаем к следующему важному этапу — обработке внешней и внутренней частей глушителя специальными термолаками. Если элементы выхлопа не новые, то предварительно нужно воспользоваться корщеткой (щеткой с ворсом из металлов или полимеров), чтобы удалить ржавчину, а также бескислотным преобразователем ржавчины, затем дать обработанным поверхностям просохнуть, после чего нанести на внешнюю часть глушителя специальный термолак из баллончика — такая краска обеспечит защиту от коррозии и не слезет при высокой температуре.
Есть способ защитить также и внутренние полости системы выпуска. Для этого снимаем глушитель и заливаем через лейку внутрь антикоррозийный «коктейль». Как вариант, это может быть состав на основе графитовой смазки и растворителя. Затем тщательно встряхиваем металлические детали в течение нескольких минут, предварительно прикрыв оба отверстия трубы.
Для наилучшего результата перед монтажом стоит дать детали полежать с закрытыми отверстиями сутки, чтобы состав «схватился». После этого сливаем излишки антикоррозийной жидкости и устанавливаем обработанные элементы глушителя на машину. По оценкам бывалых владельцев, такая обработка вкупе с дренированием может увеличить срок службы элементов выпуска втрое.
Антикор | Страница 2 | Dongfeng DFM AX7 Club
«Антикор» (рассказ-отчёт)Стать добровольцем, машину которого «отантикорят» бесплатно, мне не довелось. Предложение салона я увидел вечером, придя с работы, когда счастливый избранник уже принимал поздравления (я думаю, в ближайшее время мы с Вячеславом сравним результаты). Поскольку решение зрело давно, ещё раз взглянув на белые разводы на сохнувших башмаках, я записался вторым добровольцем, но уже за деньги.
В доперестроечные годы автомобили меняли не часто, поэтому прошприцевать всё, что можно, и «промовилить» брюшко и крылышки долгожданной ласточки, считалось хорошим тоном. Старая гвардия поддержит, что лучшим вариантом было достать «пушсало», самому всё промазать, найти самую пыльную дорогу (или обочину) и укатать там машинку до запекания «вкусной» защитной корочки.
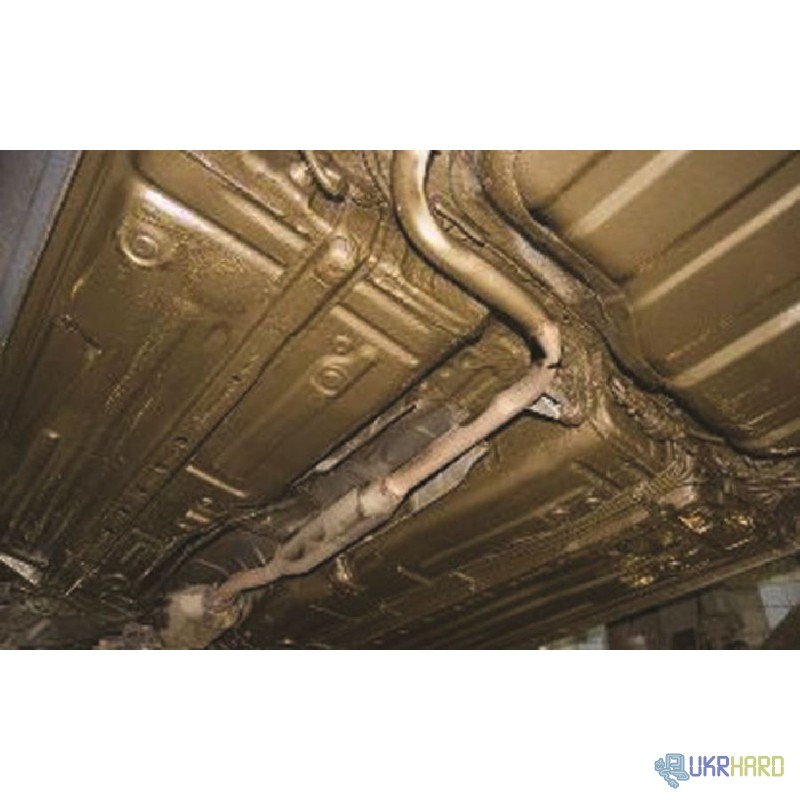
Заранее помыл Ах7 (у нас это стоит 390 руб) и к 9.00 направился в салон Дунфен «Отрадное». По дороге, учитывая просьбу Дениса, навострил уши, запоминая шумовой фон. Пришлось выключить все (кроме движка, конечно): радио, обдув и даже дворники, хотя накрапывал февральский дождь. Только на тихой Поморской улице я услышал урчание на ускорениях двигателя, да шлёпанье по лужам зимних шин-липучек, полученных в подарок по акции при покупке.
Сдавал я свой Ах много дольше намеченного срока, зато пообщался с уважаемыми Денисом, Ильей, другими «старыми» знакомыми. Спасибо красавице Насте за трогательную заботу о ветеране движения. Кстати, Дунфенов в смотровом зале не оказалось. Мне объяснили – все проданы(!), остались только Пежо и Ситроены.
Теперь внимание! Клубный сервис интернет-сообщества AX7-club.ru на антикоррозийные работы представляет своим членам скидку — 20%. Нам «антикор-антишум «PRIM» в салоне Дунфен «Отрадное» обходится в 15 200 руб. Машину оставлял на сутки. Посмотреть сами работы не смог, дела. Ребята обещали опубликовать технологию на клубном сайте.
Денис, спасибо ему большое, выкатил автомобиль , показал, рассказал (свой Ах7 он также «отантикорил»). Объяснял он очень деликатно, оставив выводы делать самому. Денис чуял запах антикора первые сто километров. Мой Ах7 сох в техцентре сутки и запаха в салоне нет. Вот от арок резиной немного отдает. На обратной дороге я слушал все оттенки работы собственного мотора Пежо, шум улицы не мешал. Припарковался, мимо идет поток, а я слышу , как электро-ручник отрабатывает. Мое суждение о том, что шум, как в домах, попадает в автомобиль, в основном, через окна было ошибкой. Он, оказывается, лез снизу! Эффект антишумной обработки очевиден. Оценить сразу противодействие покрытия влаге и химическим реагентам, естественно, невозможно. Производитель «PRIM» дает срок службы покрытия – 10 лет. И хотя служить можно по-разному, очень хочется и этому верить, как можно дольше. Поживем и проверим.. Владимир Романов
P.S. Безусловно, дополнительная обработка «пузика» полезна. Я доволен. Тем более, что в бюджете нашей семьи эти работы прошли по статье — «Подарок любимой жене». Для солидности отчета прилагаю счета и рекламу «PRIM».
Обзор последних стратегий и методов оценки
Реферат
Использование самовосстанавливающихся покрытий для защиты металлических поверхностей, таких как алюминиевые сплавы, нержавеющая сталь, углеродистая сталь и сплавы Mg, от коррозии является важным аспектом защиты металлов и для экономики. В течение последнего десятилетия в защитные покрытия были внесены значительные изменения в стратегии самовосстановления, включая использование зеленых компонентов. Ученые использовали экстракты листьев хны, алоэ вера, табака и др.в качестве ингибиторов коррозии и нановолокон целлюлозы, нанотрубок галлиозита и т. д. в качестве контейнеров для заживляющих веществ. В этом обзоре дается краткое описание потребности в самовосстанавливающихся защитных покрытиях для металлических деталей, последних стратегий внешнего самовосстановления и методов, используемых для отслеживания процесса самовосстановления для контроля коррозии металлических подложек. Объясняются общие методы, такие как ускоренный тест погружением в соль и спектроскопия электрохимического импеданса (EIS), для оценки процесса самовосстановления защитных покрытий.Мы также показываем последние достижения в области технологий, таких как метод сканирующего вибрирующего электрода (SVET) и сканирующая электрохимическая микроскопия (SECM), как успешные методы оценки процесса самовосстановления защитных покрытий.
Ключевые слова: защитное покрытие, самовосстановление, антикоррозия
1. Введение
Важно защитить поверхность металлов от коррозии. Эта защита более важна по сравнению с общей защитой, поскольку поверхность более подвержена воздействию окружающей среды и подвержена механическим воздействиям и воздействию растворителей. В металле можно ожидать коррозии, если на его поверхности есть трещины или ямки. Расчетная стоимость коррозии составляет примерно 3,4% мирового ВВП (2013 г.) [1]. Большая часть этих затрат связана с процессами проверки, методами ремонта, а также процедурами охраны окружающей среды и безопасности. Одна из самых дорогих затрат на коррозию приходится на нефтегазовые объекты. Защита от коррозии важна для современного мира, так как это снизит финансовые затраты. Важно обеспечить безопасность и надежность промышленности, сократить образование отходов и потребление энергии.
Катодная защита, анодная защита, добавление ингибиторов, защитное покрытие и т. Д. — широко применяемые методы защиты от коррозии. Среди них широко распространенным методом защиты является использование подходящего покрытия, которое может защитить поверхность металла от окружающей среды. Химические вещества, называемые ингибиторами, могут добавляться в покрытие в небольших количествах для уменьшения скорости коррозии. Основная идея покрытия — предотвратить диффузию кислорода и влаги к металлу.Кроме того, органические покрытия обладают отличной ударопрочностью, эстетическими свойствами и адгезией к подложке [2]. Среди защитных покрытий органическое покрытие — старейшая и наиболее широко используемая технология защитных покрытий [3]. В покрытия могут быть добавлены ингибиторы, что гарантирует, что они не выщелачиваются, и эффективно для используемого металла [4].
Как вариант органического покрытия, органо-неорганические гибридные покрытия состоят как из органического компонента, так и из неорганических наполнителей (в основном кремнезема), связанных ковалентными связями [5].О гибридных покрытиях с диоксидом титана в качестве неорганического компонента также сообщалось в золь-гель покрывающих пленках и нанокомпозитных покрытиях [6,7]. Комбинация этих двух типов материалов обеспечит хорошие механические свойства, гибкость, адгезию и прозрачность. Хотя органические покрытия эффективны, потребность в экологически чистых методах защиты от коррозии высока из-за экологических проблем, таких как выбросы парниковых газов и глобальное потепление. Более того, экономические проблемы, связанные с сырой нефтью и ценами на продукцию, побуждают нас искать экологически чистые альтернативы органическому покрытию.
С развитием исследований покрытий многие исследователи сообщили об интеллектуальных покрытиях, которые проявляют действие, реагирующее на раздражители. Интеллектуальное покрытие может включать в себя различные реакции, такие как самовосстановление, самоочищение, определение коррозии и предотвращение обрастания. Среди технологий интеллектуальных покрытий концепция самовосстанавливающегося покрытия была представлена как новый подход к достижению функции защиты от коррозии. Автоматическая реакция на коррозию может быть адаптирована к различным факторам, таким как истирание, изменение pH, поверхностное натяжение и температура.Самовосстанавливающееся органическое и неорганическое покрытие может увеличить срок службы получаемой структуры покрытия. Функциональность самовосстановления может быть придана за счет наличия нано / микроконтейнеров полимерного и неорганического происхождения в структуре покрытия. Настоящий обзорный документ предназначен для подробного описания этих внешних стратегий при проектировании самовосстанавливающихся структур покрытия с уделением особого внимания экологическим подходам. В зависимости от приложений конечного использования важны методы контроля, которые были приняты для оценки процесса заживления, и они также будут обсуждаться.
2. Стратегии самовосстановления защитных покрытий
2.1. Общие методы
С введением концепции самовосстановления были приняты различные стратегии самовосстановления для ремонта трещин и повреждений в системах покрытия [8]. Для создания самовосстанавливающихся покрытий применялись как внутренние, так и внешние стратегии. При собственном самовосстановлении восстановление трещины может быть достигнуто с помощью обратимой химии [9]. При внешнем типе используется метод заживления с помощью капсулы или сосудистой сети.При самовосстановлении с помощью капсул лечебные агенты инкапсулируются в подходящие капсулы для доставки заживляющего агента в поврежденную область [10]. В качестве альтернативы можно использовать покрытие, состоящее из сосудистой сети, для обеспечения однородной системы заживления по всей поверхности [11].
Самовосстанавливающиеся покрытия на основе микро / нанокапсул являются наиболее распространенными системами. Факторы, такие как контролируемое поглощение и высвобождение заживляющего агента / ингибитора коррозии, высокая несущая способность, многофункциональность и т. Д.можно контролировать эффективность таких капсул. Микрокапсулы, имеющие оболочку полимерного происхождения, такую как эпоксидная смола, карбамидоформальдегид (UF) и полиуретан (PU), обычно используются либо с заживляющими агентами, либо с ингибиторами коррозии в качестве материалов сердцевины [12,13,14]. Сообщается, что помимо микрокапсул, нанокапсулы, такие как нанокапсулы кремнезема [15], керамические наноконтейнеры [16], наноконтейнеры TiO 2 [17,18] и т. Д., Обладают эффективной способностью накапливать лечебный агент / ингибитор. Мезопористые материалы также продемонстрировали отличную хостинговую способность [19,20,21].
Микроинкапсуляция — важный шаг в разработке самовосстанавливающихся материалов. Желаемые свойства микрокапсул могут быть адаптированы путем надлежащего контроля параметров приготовления. показывает изменение размера микрокапсул из поли (мочевиноформальдегида) (ППУ), инкапсулированных алкидной смолой (полученной из пальмового масла), которые были приготовлены при различной скорости перемешивания [22]. Многие авторы [23,24,25,26] упоминали возможность адаптации необходимых капсул с различной толщиной, морфологией и размерами перед добавлением их в краску или полимерную матрицу.Fayyad et al. [24] заключают тунговое масло в карбамидоформальдегидную оболочку. Группа использовала полимеризацию на месте для приготовления микрокапсул разных размеров путем изменения скорости перемешивания. Микрокапсулы меньшего размера имели более высокую коррозионную стойкость по сравнению с микрокапсулами большего размера [27].
Распределение размеров (слева) и цифровые микроскопические изображения инкапсулированных алкидной смолой микрокапсул поли (мочевино-формальдегид) (PUF) (справа), приготовленных при различных скоростях перемешивания, ( a ) 500 об / мин, ( b ) 400 об / мин , и ( c ) 300 об. / мин.Взято из [22], с разрешения © 2016 Elsevier.
Когда капсулы разламываются из-за повреждения покрытия, содержимое этих капсул выходит наружу и активируется реакция на процедуру самовосстановления. Например, изображен разрыв капсулы микрокапсул УФ и высвобождение реактивной эпоксидной смолы, которая действует как заживляющий агент [12]. Подобное действие может быть выполнено для изменения цвета или флуоресцентного света, возникающего после разрыва, как признака повреждения. Перед настройкой самовосстанавливающегося покрытия необходимо определить различные параметры [28], такие как концентрации контейнеров, концентрация ингибиторов, кинетика добавок, кинетика диффузии и условия окружающей среды.
Изображение разорванных карбамидоформальдегидных (УФ) микрокапсул, содержащих реактивную эпоксидную смолу и растворитель в качестве материала ядра. Обозначены области наплавленной эпоксидной пленки. Адаптировано из [12] с разрешения © 2009 Elsevier.
Пористые неорганические материалы также широко использовались в качестве контейнеров для лечебных средств. Правильная функционализация отверстия мезопористого диоксида кремния позволила им действовать как pH-чувствительные контейнеры для самовосстановления [29]. Органосилильную функционализацию контейнеров из мезопористого диоксида кремния проводили с помощью этилендиамина (en), соли эн-4-оксобутановой кислоты (en-COO–) и энтриацетата (en- (COO–) 3 ) с различными органическими наполнителями. .Было обнаружено, что функционализация типа эн- (COO–) 3 с содержанием 0,23 ммоль / г показала лучшие самовосстанавливающиеся антикоррозионные свойства рН-стимулов, поскольку функционализированный мезопористый диоксид кремния имеет высокую загрузку (26 мас.%) И высвобождение (80%). %) емкости для ингибитора и прекращение любой возможной утечки.
Количество инкапсулируемого заживляющего или антикоррозионного средства в неорганических и полимерных контейнерах сравнительно невелико. Низкое количество заживляющего агента и высокая стоимость производства могут ограничить коммерциализацию технологии самовосстановления, основанной на таких контейнерах, для применения в автомобилях и самолетах. Чтобы преодолеть это ограничение, были введены новые антикоррозионные слои, которые содержат нано- и микроволокна ядро-оболочка в качестве контейнеров с лечебным агентом [30]. Электропрядение можно использовать для изготовления сетей из нано- и микроволокон ядро-оболочка, заполненных достаточным количеством заживляющего агента. В такой попытке Ли и др. [30] приготовили покрытия из нановолокна ядро-оболочка на стальной подложке с диметилсилоксаном (ДМС) в качестве самовосстанавливающегося агента и диметилметилгидроген-силоксаном (в качестве отвердителя) отдельно в сердцевинах с помощью метода двойного эмульсионного электропрядения.И ДМС, и диметилметилгидроген-силоксан были инкапсулированы в оболочки из полиакрилонитрила (ПАН). Эти двойные нановолокна были нанесены на стальную подложку. Наконец, маты из нановолокон интеркалировали матрицей из поли (диметилсилоксана) (ПДМС). Эксперименты по коррозии, которые были проведены на покрытии из нановолокна, поврежденном вручную, подтвердили эффективность самовосстановления и коррозионную стойкость этих покрытий.
Помимо метода эмульсионного электропрядения, совместное электропрядение также оказалось эффективным методом изготовления инкапсулированных матов из нановолокон [31].показывает схематическое изображение установки для коаксиального электропрядения. При совместном электроспиннинге два шприца одновременно использовали для электроспиннинга нановолокон PAN, инкапсулированных диметилвиниловым концевым диметилсилоксаном (смолой), и инкапсулированных диметилсилоксаном (отвердителем), которые были собраны вместе барабаном для получения переплетенного мата из нановолокон. Этот мат из нановолокна, заделанный прозрачным покрытием из ПДМС на стальной поверхности, эффективно действовал в качестве барьера для коррозии в процессе заживления путем высвобождения мономера смолы из сердцевины волокна для устранения коррозии.
Установка коаксиального электроспиннинга для создания волокон типа сердцевина-оболочка.
Другой стратегией внешней защиты от коррозии является послойное (LbL) нанесение нанослоев полиэлектролита и ингибитора на поверхность металлов. В этом процессе высвобождение ингибитора моделируется изменением pH [32]. Андреева и др. [33] нанесли нанослои полиэтиленимина (PEI), поли (стиролсульфоната) и экологически чистого ингибитора коррозии (8-гидроксихинолина) на поверхность алюминия.Они предложили механизм самовосстановления, который включает три основных этапа: (i) pH-нейтрализационная активность полиэлектолитов, (ii) пассивация растрескавшейся поверхности металла путем введения ингибиторов для осаждения между слоями полиэлектролита и (iii) залечить поврежденный слой.
2.2. Зеленая концепция в самовосстанавливающемся покрытии
Обычные органические молекулы, содержащие гетероатомы, считаются хорошими ингибиторами. К ним относятся сера, фосфор и азот [34]. Однако эти материалы могут оказывать негативное воздействие на окружающую среду.Использование натуральных материалов в качестве заживляющих агентов или ингибиторов коррозии для заполнения этих капсул считается хорошим подходом к экологически чистой обработке. Использование зеленых ингибиторов изучалось многими авторами [35,36,37], где защита от коррозии может быть достигнута за счет адсорбции органических соединений на поверхности металла через составляющие полярные функциональные группы. Экстракт листьев хны (HLE) обладает хорошей защитой от коррозии. Сообщалось, что HLE с акриловым покрытием (0,2 мас. / Об.%) Обеспечивает хорошую защиту за счет образования барьера, тем не менее, полимерное покрытие разрушается при повышении температуры из-за образования путей для ионной проводимости.Эти проводящие пути образуются за счет теплового расширения [37].
Многие исследователи использовали различные типы масел, такие как тунговое масло [38,39], льняное масло [40,41,42,43,44], масло нима [45] и подсолнечное масло [46], в качестве более экологичной коррозии. ингибиторы. Эти природные масла оксидаза с атмосферным кислородом и пленка полимеризованных сухих масел образуются для дополнительной защиты поверхности покрытия. Среди этих натуральных масел тунговое масло и льняное масло являются наиболее часто применяемыми самовосстанавливающими средствами из-за их лучших характеристик сушки и способности к эмульгированию и сшиванию.
Аналогичным образом были исследованы экологически чистые альтернативы наноконтейнерам, такие как хитозан [47] и нановолокна целлюлозы [48,49], а также различные типы природных глинистых минералов, включая нанотрубки галлуазита [50], аттапульгит [51] и т. и другие. [47] успешно разработали предварительный слой хитозана, легированного церием, который действует как резервуар для ингибитора коррозии для подложки из алюминиевого сплава 2024. Между катионами церия и хитозаном образуется комплекс. Сообщается, что этот комплекс отвечает за иммобилизацию и высвобождение ингибитора коррозии.Механизм иммобилизации и высвобождения самовосстановления в нановолокне целлюлозы несколько отличался от такового в хитозане. Виджаян и др. [49] сообщили, что эпоксидный мономер и аминный отвердитель были иммобилизованы на целлюлозных нановолокнах и включены в эпоксидное покрытие на подложке из углеродистой стали. В то время как эпоксидный мономер прилипает к поверхности нановолокон целлюлозы, отвердитель на основе аминов химически связывается с волокнами. На поверхности повреждения нановолокна вступили в контакт с водой и деформировались, высвободив эпоксидный мономер, который впоследствии вступил в реакцию с активной функциональной группой в отвердителях, чтобы восстановить повреждение.Доказано, что покрытие на основе целлюлозных нановолокон подходит для использования в морской воде, поскольку эти нановолокна деформируются при контакте с водой, высвобождая прилипшие ингибиторы коррозии в поврежденную область. Донг и др. [52] использовали зависящее от pH электростатическое взаимодействие между L-валином и нанотрубками галлуазита для создания интеллектуального антикоррозионного покрытия. Перемещение заряда L-валина между кислотным и основным pH было использовано для высвобождения L-валина из просвета HNT на основе pH.
показывает зеленые компоненты, используемые при проявлении зеленых покрытий.
Зеленые компоненты самовосстанавливающихся антикоррозионных покрытий.
2.3. Графен как потенциальный самовосстанавливающийся компонент
С развитием исследований графена ученые разработали покрытия на основе графена с хорошими самовосстанавливающимися и антикоррозийными свойствами. Материалы на основе графена обычно используются в покрытиях на водной основе в качестве антикоррозионных наполнителей из-за их превосходных барьерных свойств.В дополнение к этому сообщалось о различных подходах к использованию материалов семейства графена для повышения способности к самовосстановлению. Микрокапсулы оксида графена могут действовать как укрепляющие заживляющие капсулы. Их используют, потому что они обладают следующими свойствами: механической стабильностью, тонкими стенками и высокой загрузкой лечебных материалов [53], которые являются важными параметрами при определении хороших микрокапсул в покрытии. Ли и др. [53] сообщили о производстве микрокапсул из оксида графена (GO) с тонкими оболочками толщиной нанометров.Лечебным материалом было льняное масло. Была хорошая совместимость между ГО и полиуретановой (ПУ) матрицей из-за наличия функциональных групп на оболочке. Изготовление этих механически стабильных микрокапсул легко благодаря самостоятельной сборке листов GO. Было обнаружено, что 10 мас.
% Этих микрокапсул в покрытиях из полиуретана на водной основе залечивают царапины шириной 20 мкм на стальных поверхностях, оцинкованных горячим способом. В другом методе контейнеры оксид графена / полистирол (GO / PS) были изготовлены с ингибиторами 8-HQ [54].Авторы контролировали размер контейнеров от 700 нм до 35 мкм. Полученные порошки могут быть использованы в эпоксидных покрытиях на мягкой стали в качестве недорогих самовосстанавливающихся антикоррозионных материалов. В качестве альтернативы Fan et al. [55] использовали многослойную структуру GO с разветвленным поли (этиленовым рудником) (PEI) / поли (акриловой кислотой) (PAA) для защиты магниевого сплава. В этом случае GO действовал как барьерный слой, так и мультислои для самовосстановления. Совсем недавно Ван и др. использовали гибридные структуры на основе оксида графена в качестве контейнеров для заживления [56].Они создали структуру оксид графена-мезопористого диоксида кремния-наносфера, полную заживляющего агента дубильной кислоты ().
Доказано, что такое покрытие эффективно защищает металлические детали подводных лодок от переменного гидростатического давления (AHP). Аналогичным образом, другая группа исследователей использовала гидроталькит, интеркалированный оксидом графена и фосфатом, для придания самовосстанавливающемуся эпоксидному покрытию на водной основе [57]. Способность к самовосстановлению гидроталькита, интеркалированного оксидом графена и фосфатом, возникла в результате ионного обмена между PO 4 3- и Cl — на границе раздела металл-покрытие.
( и ). Схематическое изображение процедуры синтеза слоя-наносферы оксид графена-мезопористый диоксид кремния; ( б ). Заполнено эмиссионно-сканирующим электронным микроскопом (FE-SEM) изображение оксида графена-мезопористого слоя диоксида кремния-наносферы. Адаптировано из [56] с разрешения © 2019 Elsevier.
2.4. Другие новейшие концепции
Поколение микрокапсул с несколькими оболочками стимулировало исследования в области самовосстановления покрытий. Микрокапсулы с двойной оболочкой показали лучшую устойчивость к соленой воде, что делает их новыми многообещающими материалами для использования с покрытиями на водной основе [58].На рисунке показаны образования двухслойной микрокапсулы полимочевины. Внутренний слой микрокапсулы из полимочевины был сформирован посредством межфазной полимеризации, а затем покрыт внешним слоем оболочки из ППУ посредством полимеризации in situ.
Схематическое изображение образования двухслойных микрокапсул из полимочевины. Адаптировано из [58] с разрешения © 2016 Elsevier.
Аналогичным образом были исследованы многоядерные микрокапсулы. Эти материалы обеспечивали двойное самовосстановление и антикоррозионное действие [59].Авторы показали, что микрокапсулирование как ингибиторов коррозии, так и льняного масла в многоядерных фенолформальдегидных оболочках может обеспечить успешное самовосстанавливающееся антикоррозионное покрытие поверх полиуретановой краски.
За последнее десятилетие полидофамин превратился в универсальный материал для функционализации поверхностей [60]. Qian et al. [61] разработали новое самовосстанавливающееся покрытие с использованием полидофамина (PDA) в качестве pH-чувствительного протектора для ингибитора, загруженного в мезопористые наночастицы кремнезема (MSN), что позволило преодолеть ограничение спонтанного потока молекул ингибиторов из мезопор.Разработанные PDA-декорированные наноконтейнеры MSN, наполненные ингибитором коррозии, были использованы для приготовления самовосстанавливающихся алкидных покрытий на водной основе на мягкой стали. Бензотриазол, используемый в качестве ингибитора коррозии, загружали при нейтральном pH, и он способствовал быстрому высвобождению при кислом pH. КПК управлял выбросом ингибиторов и образовывал защитные комплексы с продуктами коррозии.
Умные контейнеры, адаптированные к конкретным действиям, могут использоваться как самовосстанавливающиеся материалы. Например, могут быть созданы контейнеры, которые реагируют на функцию световой стимуляции более контролируемым образом по сравнению с теми, которые реагируют на другие раздражители, такие как pH или температура. Chen et al. [20] разработали самовосстанавливающееся алкидное покрытие на водной основе на алюминиевом сплаве, активируемое обратимым светом, путем включения полых мезопористых наноконтейнеров кремнезема, модифицированных азобензолом. При ультрафиолетовом (УФ) облучении азобензол претерпевал обратимую транс-цис-изомеризацию, связанную с уменьшением размера транс-цис-изомеров, что приводило к вытеснению молекул из наноконтейнеров к месту коррозии. Под воздействием видимого света транс-изомер превращается в цис-изомер, что предотвращает высвобождение ингибитора коррозии.Таким образом можно избежать лишнего разряда ингибиторов после заживления корродированного участка.
3. Методы наблюдения за процессом самовосстановления защитных покрытий
В этом разделе мы описываем общие экспериментальные методы, которые используются для подтверждения процесса самовосстановления в упреждающем покрытии металлических конструкций. В этом разделе обсуждаются принцип работы и применение в самовосстанавливающихся покрытиях электрохимической импедансной спектроскопии (EIS), метода сканирующих вибрирующих электродов (SVET) и сканирующей электрохимической микроскопии (SECM).
3.1. Испытание на ускоренное погружение в соль
Испытание на ускоренное погружение в соль — это предварительная процедура оценки самовосстанавливающихся покрытий. Это простейшая процедура для продолжения процесса самовосстановления защитного покрытия. Покрытия с разметкой погружают в 10 мас.% Солевой раствор, концентрация которого выше, чем у нормальной концентрации морской воды. Видимое развитие коррозии оценивается через определенные промежутки времени. Например, Хуанг и др. [62] использовали ускоренный тест на погружение в соль для оценки способности эпоксидного покрытия к самовосстановлению, которое содержало 10 мас.% Полиуретановых микрокапсул с гексаметилендиизоцианатом (HDI) в качестве материала сердцевины на стальной подложке.Было замечено, что нагруженное микрокапсулами HDI покрытие могло выдерживать коррозию (а), в то время как контрольное покрытие сильно корродировало (б).
Фотографии стальной панели, покрытой ( a ) 10 мас.% Гексаметилендиизоцианатного (HDI) микрокапсульного покрытия и ( b ) чистого покрытия после испытания ускоренным погружением в соль в течение двух дней с последующим хранением при комнатной температуре в течение шести месяцев . Адаптировано из [62] с разрешения © 2014 Elsevier.
3.2.Электрохимическая импедансная спектроскопия (EIS)
Электрохимическая импедансная спектроскопия (EIS) — это рутинный метод изучения самовосстановительных свойств защитных покрытий для металлов [63]. Традиционно этот метод использовался для оценки физико-химических процессов, связанных с коррозией на подложках с покрытием. С разработкой самовосстанавливающегося покрытия в качестве альтернативного способа защиты от коррозии EIS был расширен, чтобы отслеживать процесс заживления. EIS был успешно применен к различным самовосстанавливающимся системам покрытий, таким как покрытия из полимеров и их композитов, покрытия из оксидов металлов, покрытия на основе углеродных наноматериалов, таких как углеродные нанотрубки (MWCNT) и графен и т. Д.
Рисование на поверхности покрытия вручную образует дефекты. EIS состоит из трехэлектродной системы, в которой нанесенное покрытие действует как рабочий электрод, а электрод Ag / AgCl обычно действует как электрод сравнения. Противоэлектрод выравнивается параллельно покрытому материалу для завершения ячейки. В качестве электролита используется водный раствор NaCl желаемой концентрации. Используемая концентрация раствора NaCl зависит от нескольких факторов, таких как тип покрытия, область применения и т. Д.Использование NaCl с низкой концентрацией помогает более точно оценить процесс коррозии на ранней стадии, так как это снижает скорость коррозии. Схема всей экспериментальной установки представлена на рис.
Принципиальная схема измерения спектроскопии электрохимического импеданса (EIS). Адаптировано из [62] с разрешения © 2014 Elsevier.
Одним из популярных методов представления результатов EIS является диаграмма Боде, где логарифмическая частота отображается как против абсолютных значений импеданса (| Z | = Z 0 ), так и фазового сдвига.График Боде для покрытой металлической поверхности с дефектом в основном используется для исследования явления самовосстановления. При создании искусственного дефекта на поверхности покрытия сопротивление на низких частотах внезапно падает из-за разрушения оксидной пленки и начала процесса коррозии. Как только начинается восстановление дефекта, импеданс восстанавливает свои первоначальные значения. Например, Желудкевич и др. [64] проанализировали график Боде, чтобы проследить за характеристиками самовосстановления гибридного гелевого покрытия, легированного ингибитором коррозии, на алюминиевом сплаве ().В этом покрытии в качестве ингибитора коррозии используется 8-гидроксихинолин. Авторы обнаружили, что изначально пониженные значения импеданса восстанавливали исходное значение через короткий период в 20 минут. (а). Однако постоянно уменьшающиеся значения низкочастотного импеданса нелегированного однослойного золь-гелевого покрытия указывали на разрушение покрытия без восстановления (б).
EIS-графики ( a ) легированной ингибитором двухслойной золь-гелевой пленки и ( b ) нелегированной однослойной золь-гелевой пленки при погружении в 0.5 NaCl. Адаптировано из [64] с разрешения © 2007 Elsevier.
Время, необходимое для начала процесса заживления, является важным параметром при оценке самовосстанавливающегося покрытия. EIS свидетельствует об этом времени самовосстановления. Исследование методом EIS эпоксидного покрытия с эпоксидными микрокапсулами, нанесенного на углеродистую сталь, показало, что покрытие способно зажить в течение 4 часов () [14]. Это подтвердило, что микрокапсулы немедленно высвободили заживляющий агент по мере распространения трещин через покрытие.
EIS Графики Боде эпоксидных покрытий, содержащих 20% микрокапсулы, при погружении в 12 мас.% Раствор NaCl через различные интервалы времени. Адаптировано из [14] с разрешения © 2012 Elsevier.
Альтернативный метод количественной оценки процесса самовосстановления — сопоставление данных EIS с эквивалентной схемой при использовании анализа данных. Этот метод дает некоторые дополнительные сведения о характеристиках самовосстановления покрытых слоев путем присвоения спектров импеданса компонентам схемы [62].Изменение компонентов эквивалентных схем, таких как сопротивление заживления ( R заживление ) и емкость заживления ( C заживление ) с временем погружения, дает прямую информацию о процессе самовосстановления. Полиуретановые микрокапсулы, заполненные гексаметилендиизоцианатом (HDI), содержащие эпоксидное покрытие на стальной подложке, были оценены на предмет их самовосстановления путем сопоставления графиков EIS с эквивалентной схемой [62] (a). Эквивалентная схема поцарапанной заполненной HDI микрокапсулы, содержащей самовосстанавливающееся покрытие, при измерении EIS показана на b.Значение R заживления увеличивается с увеличением времени погружения (c), что отражает самовосстановление поверхности покрытия.
( a ) графики Боде и аппроксимированные кривые (сплошная линия) поцарапанного эпоксидного покрытия с полиуретаном, наполненным HDI, после 8 часов погружения в 1 M раствор NaCl, соответствующая ( b ) эквивалентная схема при измерении EIS и ( c ) сопротивления исцелению ( R исцеление ) в зависимости от графика времени погружения. Адаптировано из [62] с разрешения © 2014 Elsevier.
3.

Коррозия и процесс самовосстановления в покрытых металлических подложках инициируются на микроплощадке. Этот процесс обычно связан с изменением электрохимического потенциала и плотности тока. SVET может исследовать возникновение коррозии путем измерения локальной плотности тока коррозии в микродефектах. SVET отображает электрическое поле, создаваемое над уровнем электрохимически активной поверхности, и графически отображает его в виде контурной карты.Этот метод обеспечивает отображение и количественную оценку локальных электрохимических и коррозионных событий в реальном времени. Использование вибрирующего электрода сравнения для измерения электрического поля улучшает разрешение и снижает минимальный измеряемый сигнал по сравнению со статическим электродом сравнения.
В состав электрохимической ячейки SVET входит микроэлектрод, который является основной частью SVET. Он погружен в электролит, в котором покрытый материал закреплен держателем. показывает установку электрохимической ячейки для СВЭТ.Компьютерная программа механически управляла сканирующим зондом микроэлектрода. Наблюдатель может вертикально раскачивать зонд над материалом с покрытием. Результаты могут быть записаны в виде карты плотности тока.
Электрохимическая ячейка для экспериментов с методом сканирующих вибрационных электродов (СВЭТ). Адаптировано из [65] с разрешения © 2017 Electrochemical Society, Inc.
SVET использовался для отслеживания процесса самовосстановления эпоксидного покрытия, содержащего микрогель, легированный ингибитором коррозии, на алюминиевой подложке Латниковой и др.[66]. Максимальное увеличение плотности тока, зарегистрированное после 12 часов погружения в карту плотности тока SVET, подтвердило интенсивную коррозию контрольного эпоксидного покрытия, как показано на a – c. В то же время эпоксидное покрытие, содержащее 5 мас.% Частиц микрогеля, допированных ингибитором коррозии, не показало признаков коррозии, что указывает на непрерывное высвобождение 2-метилбензотиазола (MeBT) из микрогеля в поврежденную область (d – f).
Распределение плотности тока над поцарапанными алюминиевыми подложками, покрытыми ( a — c ) контрольным эпоксидным покрытием и ( d — f ) эпоксидным покрытием, модифицированным 5 мас.% Легированных частиц микрогеля MeBT: a , d —0 ч погружения, b , e —6 ч погружения, c , f —12 ч погружения в 0.1MNaCl раствор. Взято из [66] с разрешения © 2012 Royal Society of Chemistry.
SVET успешно использовался для отслеживания процесса самовосстановления в многослойном полиэлектролитном покрытии, содержащем ингибитор, на алюминиевых пластинах [33]. Карты плотности тока этого покрытия на основе полиэлектролита сравнивали с картами золь-гелевого покрытия SiO x / ZrO x . Карта плотности тока поверхности Al, покрытой золь-гелевой пленкой, показала возрастающую анодную активность со временем погружения, что в конечном итоге привело к полному разрушению металлической поверхности. Однако совершенно иное поведение продемонстрировала поверхность из алюминиевого сплава с покрытием из полиэлектролита, содержащего ингибитор, поскольку ни анодная активность, ни продукты коррозии не наблюдались до 16 часов погружения.
3.4. Сканирующая электрохимическая микроскопия (SECM)
Подобно SVET, сканирующий электрохимический микроскоп (SECM) также является важным локальным электрохимическим методом для последующего самовосстановления с высоким пространственным разрешением [67]. Микроэлектродный зонд является основным компонентом SECM. Этот зонд сканирует поверхность покрытия в боковом направлении и используется для локального мониторинга процессов в растворах и картирования соответствующей реакционной способности поверхности [68].Размер наконечника зонда имеет решающее значение, поскольку он контролирует пространственное разрешение измерений SECM. SECM облегчает химические изменения, обнаруживая ионные частицы, участвующие в процессе коррозии, что невозможно обеспечить с помощью SVET. В последних литературных источниках сообщается об использовании режима окислительно-восстановительной конкуренции и комбинированного режима окислительно-восстановительной конкуренции и отрицательной обратной связи для мониторинга процесса заживления. Гонсалес-Гарсия и др. [69] наблюдали за явлениями самовосстановления в эпоксидном покрытии с капсулами, содержащими силиловый эфир на алюминиевых сплавах, с помощью SECM.Они выбрали комбинированный режим в SECM, который четко различал поведение кислорода как активного компонента в катодных процессах и как посредника. показан SECM-профиль переходной зоны на поверхности алюминиевого сплава с контрольным покрытием и покрытием, обработанным силилом, при погружении в раствор соли. Среднее плато более отрицательного тока, которое наблюдалось на силилэфирной области, указывает на отсутствие катодной активности. Силиловый эфир, который высвободился из капсул, регенерирует однородный поверхностный слой для защиты металла от коррозии, и, следовательно, в иммерсионной среде доступно больше кислорода.
Сканирующая электрохимическая микроскопия (SECM) профиль переходной зоны на алюминиевом сплаве с контрольным и силильным покрытиями, погруженными в 0,05 М раствор NaCl на 1 день. Адаптировано из [69] с разрешения © 2011 Elsevier.
4. Применение самовосстанавливающихся покрытий
При рассмотрении различных доступных технологий разработка самовосстанавливающихся покрытий зависит от конечного применения. Большинство рассмотренных выше самовосстанавливающихся покрытий в настоящее время находятся в стадии разработки.Внедрение таких умных покрытий во многих современных отраслях промышленности защитит металлические детали от агрессивной среды, улучшит характеристики и обеспечит безопасность. Области применения включают автомобильную, электронную, аэрокосмическую, нефтегазовую, медицинскую и морскую промышленность. Существующие на рынке технологии самовосстановления позволяют восстанавливать царапины на красках и покрытиях автомобилей [70]. Сообщалось о покрытиях бетона, обладающих способностью к самовосстановлению под действием солнечного света [71], и подобное покрытие на металлической подложке могло бы иметь потенциальное применение на открытом воздухе. Покрытия, в которых используются ингибиторы коррозии в качестве заживляющих агентов, позволят получить экономичные антикоррозионные покрытия для инфраструктуры и нефте- и газопроводов. Тонкие самовосстанавливающиеся покрытия, полученные золь-гель методом, потенциально могут использоваться для алюминиевых сплавов в аэрокосмической отрасли. Самовосстанавливающиеся покрытия представляют собой интеллектуальные материалы, которые могут придавать эстетическую функцию в дополнение к защитным функциям автомобилям и объектам инфраструктуры.
Передовые исследования в этой области сосредоточены на интеграции многофункциональных функций в самовосстанавливающиеся покрытия.Что наиболее важно, такие свойства, как противообрастающие, супергидрофобные и антифрикционные, могут быть объединены вместе с самовосстановлением [72,73]. В этом процессе используются разные функциональные материалы, в зависимости от требуемых приложений. Длительное высвобождение заживляющих веществ важно для различных применений, особенно тех, которые связаны с защитой от старения. В этой системе необходимое лечение отпускается по мере необходимости. Например, в [74] одновременно могут использоваться два метода: первый метод — быстрое высвобождение ингибиторов наноконтейнером в требуемых условиях окружающей среды, другой метод — длительное медленное высвобождение ингибиторов.Экологически чистые растительные масла и глинистые минералы являются потенциальными кандидатами в качестве заживляющих агентов и наноконтейнеров, соответственно, для масштабируемого промышленного применения.
обобщает различные типы самовосстанавливающихся покрытий, их основные характеристики и потенциальные области применения.
Таблица 1
Различные типы самовосстанавливающегося покрытия, основные характеристики и возможности применения.
Sl № | Тип самовосстанавливающегося покрытия | Характеристики | Возможные области применения |
---|---|---|---|
1 | Микро / нанополимерные капсулы для загрузки заживляющего агента.![]() | Популярные самовосстанавливающиеся покрытия. Приготовление капсул может быть утомительным. Проблемы стабильности. | Антикоррозионное покрытие для повышения прочности металлических конструкций. |
2 | Многоболочные микрокапсулы для загрузки заживляющего агента. | Хорошая стойкость к соленой воде. | Самовосстанавливающиеся покрытия на водной основе для автомобилей. |
3 | Пористые неорганические материалы с функционализированными отверстиями для загрузки заживляющего агента.![]() | Можно напрямую использовать коммерчески доступные пористые неорганические материалы. Контролируемое высвобождение заживляющего средства. | pH-чувствительное самовосстанавливающееся покрытие для металлов. |
4 | Нано- и микроволокна ядро-оболочка в качестве контейнеров для заживляющего агента | В волокна сердцевина-оболочка может быть загружено достаточно большое количество заживляющего вещества. | Антикоррозионное покрытие для крупномасштабного промышленного применения. |
5 | Послойное покрытие для иммобилизации заживляющего агента / ингибитора коррозии | Тонкое покрытие обеспечивает долговременную защиту от коррозии.![]() | Для защиты алюминиевых сплавов, используемых в аэрокосмической отрасли |
6 | Нановолокна целлюлозы для иммобилизации заживляющего агента / ингибитора коррозии | Экологичная технология покрытия. | Для подводных лодок. |
7 | Галлуазитовые нанотрубки как контейнеры для заживления | Экономичные и зеленые покрытия. Нанотрубки галлуазита действуют как усиливающий агент для покрытия. | Антикоррозионная краска для коммерческого применения.![]() |
8 | Натуральные масла как лечебные средства | Зеленые и экономичные. | Антикоррозионные металлические покрытия для масштабируемого промышленного применения. |
9 | Экстракт листьев хны как ингибитор коррозии | Экологичный ингибитор коррозии. | Подходит для защиты различных металлов, подвергающихся воздействию широкого спектра электролитов. |
10 | Микрокапсулы на основе оксида графена (GO) в качестве контейнера для заживления | Механическая стабильность и высокая несущая способность.![]() | Защищает металлические части подводных аппаратов от переменного гидростатического давления (AHP). |
Самовосстанавливающаяся минерализация и улучшенные антикоррозионные свойства полиуретановой композитной пленки CaCO3 за счет индукции β-CD
Основные моменты
- •
Новая пленка полиуретан-CaCO 3 создается путем минерализации на месте в морской воде.
- •
Компактная самовосстанавливающаяся пленка эффективно улучшает антикоррозионные свойства.
- •
β-Циклодекстрин с богатыми гидроксильными группами и гидрофобной полостью способствует минерализации.
- •
Механизм через адсорбцию прочно подтверждается молекулярно-динамическим моделированием.
Реферат
Новое органическое композитное покрытие было успешно изготовлено путем минерализации на месте в искусственной морской воде для получения стойкого антикоррозионного покрытия. Минерализованные композитные пленки в полной мере используют преимущества, включая богатую гидроксильную группу и особую кольцевую структуру β-циклодекстрина, а также превосходную адгезию и высокую гибкость полиуретанового покрытия на водной основе.Результаты показывают, что β-CD заметно способствует минерализации CaCO 3 на веществах WPU за счет эффективной адсорбции и комплексообразования гидрофобной полости с ионами кальция. Плотная органо-неорганическая композитная пленка демонстрирует выдающиеся антикоррозионные свойства со скоростью коррозии 1,39 × 10 –3 мм / год для образца 3CD-WPU, что намного меньше, чем 7,36 × 10 –2 мм / год для покрытия WPU. при тех же условиях. Превосходные антикоррозионные свойства в основном приписываются однородному центру зародышеобразования, обеспечиваемому CD-WPU, и дальнейшему образованию плотной пленки CaCO 3 .Кроме того, функция радиального распределения и теоретический анализ энергии адсорбции с помощью молекулярно-динамического моделирования определенно выявляют и подтверждают механизм β-CD, способствующего минерализации CaCO 3 .
Ключевые слова
Минерализация
Антикоррозийное покрытие
Молекулярно-динамическое моделирование
Морская среда
Самовосстановление
Рекомендуемые статьи Цитирующие статьи (0)
Посмотреть аннотацию© 2019 Авторы.Опубликовано Elsevier Ltd.
Рекомендуемые статьи
Цитирующие статьи
Интеллектуальные антикоррозионные самовосстанавливающиеся нанокомпозитные покрытия на основе молибдата на основе цинка и металлического мезопористого кремнезема (MCM-41)
Мы сообщаем об электроосаждении интеллектуальных коррозионно-стойких композиционных покрытий на основе цинка, содержащих мезопористый диоксид кремния (MCM-41), пропитанный молибдатом. Функционализация молибдата, известная как обычный ингибитор коррозии, была добавлена к покрытию в качестве «антикоррозионного самовосстанавливающегося» агента, который высвобождается в процессе коррозии. Дисперсия и связывание функциональных частиц MCM-41 в растворе для электроосаждения были улучшены путем добавления 3-меркопропилтриметоксисилана (MPTMS). Цинковая металлическая основа была гальваностатически осаждена совместно с частицами MCM-41 в условиях, которые менялись для получения наиболее гладких и устойчивых к коррозии пленок. Потенциал разомкнутой цепи Zn-MCM-41-SH-Mo (SH: силан, Mo: функционализация молибдата) в растворе хлорида увеличивается как функция времени из-за высвобождения Mo в качестве анодного ингибитора, который вызывает самовосстановление. функциональность в покрытии.На основании спектроскопии электрохимического импеданса и потенциодинамических поляризационных испытаний было обнаружено, что коррозионная стойкость увеличивается в следующем порядке: Zn – MCM-41 – SH – Mo> Zn – MCM-41 – Mo> Zn – MCM-41> Zn.
Эта статья в открытом доступе
Подождите, пока мы загрузим ваш контент.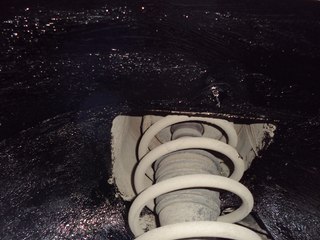
Экологически чистые антикоррозионные покрытия | База данных исследовательского проекта | Исследовательский проект грантополучателя | ЗАКАЗ
Экологически чистые антикоррозионные покрытия
Номер контракта EPA: 68D00244Название: Экологически чистые антикоррозионные покрытия
Исследователи: Кларк, Ричард Л.
Текущие следователи: Миллер, Майкл Б.
Малый бизнес: Luna Innovations Inc. , F and S Inc
Текущий малый бизнес: Luna Innovations Inc.
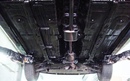
Обращение EPA: Ричардс, апрель
Этап: I
Срок проекта: 1 сентября 2000 г. 1 марта 2001 г.
Количество проекта: 69 974 долл. США
RFA: Исследование инноваций малого бизнеса (SBIR) — фаза I (2000) RFA Text | Списки получателей
Категория исследований: Нанотехнологии , SBIR — Предотвращение загрязнения , Предотвращение загрязнения / устойчивое развитие , Исследование инноваций малого бизнеса (SBIR)
Описание:
Коррозия металлических конструкций оценивается во многие миллиарды долларов. ежегодно.Наиболее распространенные методы ингибирования или предотвращения коррозии включают: нанесение тяжелых поверхностных покрытий (краски и грунтовки) или конверсия покрытия с использованием различных металлов в строго контролируемых процессах и регулируется из-за токсичности и возможных канцерогенных свойств.
Предлагаемый процесс найдет применение в защите крупных сооружений.
такие как корабли, мосты, автомобильные компоненты и коммерческие самолеты
изготовление. Он послужит недорогой, экологически чистой заменой
антикоррозионных покрытий для многих небольших конструкций и компонентов в
коммерческое и промышленное применение.
Публикации и презентации:
Публикации по этому проекту были представлены: Просмотреть все 3 публикации для этого проектаДополнительные ключевые слова:
малый бизнес, SBIR, предотвращение загрязнения, покрытия, машиностроение, химия, EPA. , RFA, научная дисциплина, устойчивая промышленность / бизнес, чистое производство / предотвращение загрязнения, устойчивая окружающая среда, химия, технологии для устойчивой окружающей среды, новые / инновационные технологии, инженерия, устойчивость к коррозии, экологически безвредное покрытие, ионные самосборные монослои, чистые технологии , опасные материалы, процессы нанесения покрытий, экологически безопасные покрытия, канцерогенность, токсичность, составы покрытий, альтернативные покрытия, покрытия, предотвращение загрязнения, защита от коррозииВыполнение и окончательные отчеты:
Интеллектуальные покрытия двойного действия с самовосстанавливающейся супергидрофобной поверхностью и антикоррозийными свойствами
rsc.org/schema/rscart38″> Эта работа представляет новое самовосстанавливающееся супергидрофобное покрытие, основанное на двойном действии ингибитора коррозии бензотриазола (БТА) и полимера с памятью формы на основе эпоксидной смолы (SMP).Показано, что повреждения морфологии поверхности (, например, , раздробленные участки и царапины) и соответствующая супергидрофобность быстро восстанавливаются с помощью простой термообработки при 60 ° C в течение 20 минут. Электрохимическая импедансная спектроскопия (EIS) и сканирующая электрохимическая микроскопия (SECM) были использованы для изучения антикоррозионных характеристик поцарапанных и отвержденных супергидрофобных покрытий, погруженных в 3,5% -ный раствор NaCl. Результаты показали, что антикоррозионные свойства поцарапанных покрытий улучшились при введении БТА.После термообработки поцарапанные супергидрофобные покрытия продемонстрировали превосходное восстановление своих антикоррозионных свойств, что объясняется закрытием царапины за счет эффекта памяти формы и улучшенной ингибирующей эффективностью БТА.
У вас есть доступ к этой статье
Подождите, пока мы загрузим ваш контент.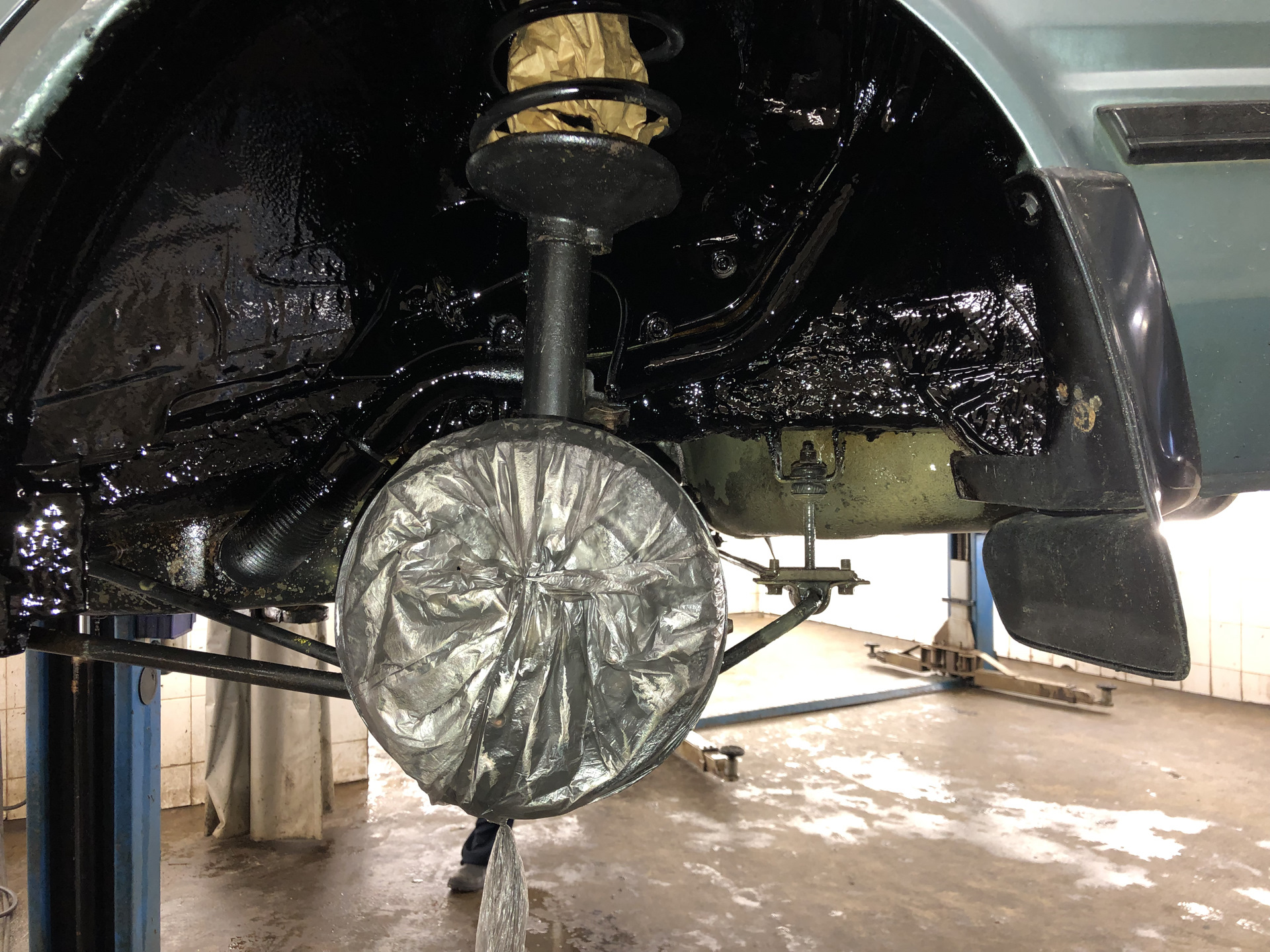
Предотвращение повреждений с помощью барьеров и ингибиторов
Барьерные покрытия
Один из способов прервать работу электрохимической ячейки — создать барьер.Обычно это барьер для влаги и / или кислорода, предотвращающий образование жизнеспособной электрохимической ячейки. Это может быть достигнуто за счет использования покрытий из высококристаллических полимерных связующих, которые предотвращают диффузию этих компонентов через пленку к подложке. Включение пластинчатых (пластинчатых) пигментов также может создавать барьер для кислорода и воды, прерывая поток электронов и предотвращая развитие коррозии.
Два хорошо известных типа полимерных связующих, используемых в барьерных покрытиях, — это эпоксидные смолы и галогенированные сополимеры . Эти системы образуют пленки с высоким сопротивлением пропусканию воды, водяного пара и кислорода. Предотвращение попадания воды на поверхность предотвращает образование проводящего пути электролита, по которому электроны текут от анода к катоду.
Если кислород не может достичь поверхности металла, значит, нет акцептора (катода) для электронов от металла, и коррозия не может продолжаться.
Пластинчатые пигменты также препятствуют перемещению воды и кислорода к поверхности металла. Эти пластинчатые пигменты, такие как слюда и тальк, образуют своего рода «лабиринт».Даже если полимерная пленка допускает проникновение кислорода и воды, косвенный путь к поверхности длиннее. Процесс коррозии замедляется, если не прекращается, и поверхность сохраняется.
Барьерные свойства покрытия также зависят от других факторов, таких как толщина пленки. Обычно, пока не нарушаются другие свойства (например, адгезия), более толстые барьеры лучше защищают от коррозии.
Покрытия, ингибирующие коррозию
В то время как барьерные покрытия физически защищают поверхность металлов, антикоррозионные покрытия защищают поверхность за счет химических механизмов. Металлы обладают более высокой электрохимической активностью и будут окисляться вместо субстрата или пигментов, что может прервать электрохимический процесс. Следовательно, металлы могут использоваться в качестве компонентов антикоррозионных покрытий.
Одним из самых простых антикоррозионных покрытий является грунтовка с высоким содержанием цинка. Поскольку цинк окисляется быстрее, чем железо или сталь, он является предпочтительным анодом в электрохимической ячейке, предотвращая коррозию основы. Это пример катодной защиты металлической подложки, поскольку цинк действует на катод электрохимической ячейки.
Алюминий также используется для катодной защиты стальных поверхностей. Свинец и хром чрезвычайно эффективны в качестве ингибиторов коррозии, но проблемы со здоровьем и безопасностью серьезно ограничивают или исключают их использование.
Если на анод действует ингибитор коррозии, он обеспечивает анодную защиту. Ингибиторы анодной коррозии предотвращают образование оксидов металлов в подложке. Часто они представляют собой частично растворимые соли анионов, содержащие фосфор или бор. Эти анионы могут иметь различные степени окисления (заряды) в зависимости от химической среды.
Эффективность ингибитора коррозии может широко варьироваться в зависимости от связующего вещества системы покрытия и условий окружающей среды. При выборе или формулировании защитных покрытий на основе ингибиторов коррозии необходимо учитывать конечное применение, ожидаемый срок службы и условия воздействия.
При правильном выборе и правильном нанесении на должным образом подготовленную основу антикоррозионные покрытия могут прослужить долгие годы для защиты металлических предметов.
Дополнительная литература:
Типы и советы по выбору рецептуры покрытия
TAGS : Ингибиторы коррозии в покрытиях
Хотя само покрытие играет важную роль в защите от коррозии, использование жидких ингибиторов коррозии помогает и значительно улучшает это свойство.
Эти агенты можно использовать отдельно, например, в прозрачных лаков, или в сочетании с различными антикоррозийными пигментами. Эта синергия улучшает коррозионную стойкость краски и даже позволяет:
- Уменьшить количество антикоррозионных пигментов
- Обеспечивает отличные результаты и является альтернативой вопросам снижения затрат и защиты окружающей среды.
Но, прежде чем переходить к ингибиторам коррозии, давайте сначала разберемся с явлением коррозии.
Коррозия покрытий
Коррозия — это окислительно-восстановительная реакция в присутствии электролита, приводящая к ухудшению качества металла. Обычно для черных металлов, таких как железо и сталь, коррозия также называется «ржавчиной» .
Проводимость электролита имеет решающее значение: чем выше проводимость, тем быстрее коррозия
Вот почему в соленой воде ржавчина развивается быстрее, чем в чистой.
Коррозия металлической детали может:
- Изменение внешнего вида поверхности
- Ослабить его свойства
- Повреждение прилегающих частей
Помимо изменения цвета и внешнего вида, он может ослабить структуру / разрушить саму структуру .

В покрытиях преобладает электрохимическая коррозия . Это комбинация двух проводников (электродов) с водным раствором электролита. Металл с более отрицательным потенциалом будет анодом и подвергнется коррозии, тогда как металл с более положительным потенциалом будет катодом. Затем в растворе электролита происходит окислительно-восстановительная реакция.
Но коррозия также может происходить в той же металлической системе, где на поверхности существуют разности потенциалов. Эти различия в потенциале могут происходить из-за гетерогенного химического состава, например:
- Различия в слое покрытия
- Загрязнение
- Царапины
- Точечные отверстия…
В чугуне коррозия возникает, когда различные части поверхности, образующие анод и катод, подвергаются воздействию раствора электролита.Без электролита коррозия сильно снижается. Другими словами, соленая атмосфера (как и морские условия) более агрессивна, чем незагрязненная.

Помимо этой реакции коррозии, на коррозию покрытия могут влиять многие другие факторы, например:
- Качество поверхности : Неоднородная поверхность увеличивает риск коррозии. Обработанная поверхность предотвратит это. Перед нанесением покрытия поверхность должна быть очищена от загрязнений.
- Адгезия слоя покрытия : Покрытие образует защитный барьер на металлической поверхности. Отсутствие адгезии будет слабым местом с высоким риском развития коррозии. Требуется идеальная поверхность смачивание …
»Ознакомьтесь с советами: адгезия красок и покрытий! - Качество слоя покрытия : Проколы, кратеры и другие дефекты поверхности также ослабят защиту металла.
Когда возникает коррозия?
Риск коррозии присутствует на протяжении всего срока службы покрытия, от хранения самой жидкой краски (коррозия в банке) до нанесения (мгновенная коррозия) и спустя много лет (долговременная коррозия):
Хранение Внутренняя коррозия. | Внутренняя коррозия Во время хранения краска непосредственно контактирует с железной банкой, вызывая коррозию. |
Применение Обрыв ржавчины краской на водной основе. Кроме того, нанесение краски на поверхность, загрязненную ржавчиной, может стать источником коррозии. | Вспышка ржавчины Краска на водной основе наносится непосредственно на металл. Появляется вскоре после нанесения из-за миграции ржавчины через пленку. |
Старение краски и основания Агрессивная среда, загрязнение, атмосферные воздействия могут ослабить пленку краски и увеличить риск развития коррозии. | Старение — долговременная коррозия Защитный барьер краски разрушается и появляются слабые места. Кроме того, незащищенные части подложки могут подвергнуться коррозии. |
Стратегии контроля / снижения коррозии
Контроль коррозии включает естественные химические реакции между металлической подложкой и окружающей средой.

- Изменение свойств металла : Предварительная обработка улучшает коррозионную стойкость металла.
- Переход на неметаллические материалы : Но это не может удовлетворить все требования к конечному продукту…
- Подайте электрический ток для питания электронов : Дорого и не всегда возможно!
- Используйте расходуемый анод : состав краски, богатый защитными пигментами на основе цинка.
- Используйте антикоррозионные пигменты. : Самый распространенный раствор, антикоррозионные пигменты, которые со временем химически пассивируют металлическую поверхность (особенно хроматы, фосфаты и молибдаты).И может действовать как жертвенный пигмент в сочетании с оксидом цинка, как ингибитор коррозии фосфат цинка. Но некоторые из этих пигментов вредны для окружающей среды.
- Используйте органический ингибитор коррозии. : На основе различных структур, таких как амин, кислота, полимеры, соли, эти продукты образуют защитный барьер на поверхности металла и нарушают химическую реакцию, предотвращая развитие ржавчины.
Пассивирующий слой предотвращает окисление металла.
Понять, каков механизм работы органических ингибиторов коррозии, можно по рисунку ниже:
Как работают ингибиторы коррозии?
Ингибитор коррозии может образовывать защитный слой на поверхности металла за счет:
- Химическая адсорбция
- Ионная комбинация
- Окисление основного металла (особенно алюминием)
Ингибитор контроля коррозии может образовывать комплекс с потенциально коррозионным компонентом и нейтрализовать реакцию коррозии.
Мы можем обобщить риск коррозии и способы повышения коррозионной стойкости со стороны состава:
Риск коррозии | На основе растворителей | На водной основе | |
Контейнер для хранения | Паровая фаза | ★ | ★ ★ ★ |
Мокрая фаза | – | ★ ★ ★ | |
Применение | – | ★ ★ ★ | |
Долговременная коррозия | ★ ★ ★ | ★ ★ ★ |
Раствор против коррозии | На основе растворителей | На водной основе | |
Контейнер для хранения | Паровая фаза | — | Ингибиторы мгновенной коррозии |
Мокрая фаза | – | Ингибиторы ржавчины | |
Применение | – | Ингибиторы ржавчины | |
Долговременная коррозия | Антикоррозийные пигменты Ингибиторы коррозии | Антикоррозийные пигменты Ингибиторы коррозии |
Предварительная обработка основания для обеспечения антикоррозийных свойств
Когда покрытия используются как средство уменьшения коррозии, важно, чтобы покрытие очень плотно прилегало к поверхности.
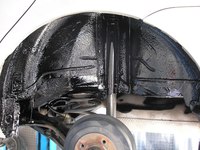
Конверсионные покрытия
Конверсионное покрытие действует как отличная основа для красок и в то же время обеспечивает отличную защиту от коррозии. Конверсионное покрытие представляет собой слабокислый водный раствор (на водной основе) химикатов. Фосфаты железа или цинка являются наиболее распространенными химическими веществами в составе, хотя другие химические соли также добавляются для выполнения различных функций.Металл обычно погружают в емкость, содержащую раствор. При погружении металл очень немного растворяется, и фосфат фактически оседает на чистом металле.
Праймеры Wash
На поверхность перед нанесением покрытия наносятся грунтовки Wash:
- Для пассивирования поверхности и временного обеспечения коррозионной стойкости
- Для создания клеевой основы для следующего покрытия
Гальваническое покрытие (OEM-процесс)
При нанесении гальванических покрытий используется электрический ток для нанесения органического покрытия, при котором на металлические поверхности равномерно наносятся тонкопленочные грунтовки и однослойные покрытия.
Процесс нанесения гальванического покрытия включает четыре этапа:
- Очистка поверхности
- Преобразовательное покрытие
- Уплотнение
- Сушка и охлаждение
Основные праймеры
Грунтовки используются для «герметизации» поверхности, чтобы растворители или вода верхних покрытий могли испаряться, поскольку они были разработаны для защиты от кислорода, влаги и коррозионных соединений на поверхности металла.
Типы ингибиторов коррозии и критерии выбора
Ингибиторы ржавчины
Покрытия на водной основе более чувствительны к коррозии, поскольку в них участвует… вода.Кроме того, многие катионы металлов (например, Fe 2+ , Железо II) растворимы в воде. Типичным примером является мгновенная ржавчина, быстрое развитие коррозии, которая появляется только при нанесении покрытий на водной основе непосредственно на металл, когда слой краски еще влажный.
Покрытия на водной основе, наносимые на металл, когда слой краски еще влажный, — типичная жертва мгновенной коррозии. Покрытия на водной основе при контакте с металлом создают высокий риск мгновенной коррозии и коррозии внутри банки. Следовательно, становится необходимым использовать ингибитор ржавчины .
Большинство ингибиторов ржавчины содержат нитрит натрия (токсичные ингибиторы коррозии) . Также доступны безнитритные ингибиторы. Их необходимо использовать в более высоких дозах (до 1,5% от общей рецептуры).
Более экологичные версии без нитритов и боратов заменяют водорастворимые / диспергируемые и основанные на нитритах натрия. Большинство продуктов, представленных на рынке, имеют уровень дозировки от 0,2% до 1,5% (форма доставки от общего состава), что оказывает значительное влияние на коррозию в банке и мгновенное ржавление.
ПРИМЕЧАНИЕ: Ингибитор коррозии на основе кальция обеспечивает лучшую совместимость с водой. Он может помочь диспергировать пигмент при использовании на стадии измельчения пигмента. Хотя некоторые эмульсионные смолы могут быть чувствительны к Ca 2+ .
Ингибиторы / протекторы коррозии длительного действия
Помимо антикоррозионных пигментов , жидкие органические ингибиторы коррозии также обеспечивают долговременную защиту от коррозии с помощью ингибиторов . Жидкие ингибиторы коррозии работают совместно с антикоррозийными пигментами.
Поскольку реакция коррозии представляет собой окислительно-восстановительный химический процесс, сначала можно выбрать требуемый вариант металла-ингибитора коррозии, используя стандартный химический восстановительный потенциал. Эта шкала является первым подходом, поскольку значения основаны на измерениях в водном растворе при 25 ° C, что не является идеальным случаем для всех покрытий!
Тогда становится легко выбрать металлический вариант ингибиторов коррозии:
- Первым выбором будет ингибитор коррозии на основе бария.
- В случае антикоррозионных пигментов на основе цинка: Ингибитор коррозии на основе цинка
- В случае новых и менее токсичных пигментов ингибиторов коррозии: Ингибитор коррозии на основе магния
- Ингибитор коррозии на основе аминов и полимеров для безметалловой альтернативы
При выборе долгосрочного ингибитора коррозии на тип и дозировку агента влияют:
- Тип защищаемого металла
- Эффективность защиты во времени при заданном условии
- Наличие и эффективность антикоррозионных пигментов
- Формулировка глобальной стоимости
- Ограничения по охране окружающей среды, здоровья и труда
Кроме того, существует множество пигментов с их антикоррозийными свойствами.Давайте посмотрим:
Пигменты барьерные
Многие пигменты работают в основном за счет «пассивной защиты», усиливая барьерный эффект покрытия. Слюда, алюминий, стеклянные чешуйки и слюдяной оксид железа (MIO) широко используются. Их эффективность зависит от того факта, что они имеют пластинчатую, чешуйчатую форму и обычно выравниваются более или менее параллельно поверхности покрытия. Это снижает водопроницаемость и ионную проницаемость, заставляя ионы или молекулы воды проходить непрямой путь от поверхности к субстрату, как показано на рисунке ниже:
Пластинчатый расширитель (вверху) демонстрирует барьерный эффект, снижающий проникновение влаги,
с частицами, близкими к сферическим (внизу) для сравнения
- Тальк , обычно классифицируемый как «наполнитель», а не как первичный пигмент, также обычно встречается в антикоррозионных красках, поскольку он одновременно очень инертен и имеет пластинчатую форму.
- MIO — высокоэффективный антикоррозионный пигмент. В настоящее время существует тенденция смешивать этот материал с неламеллярным MIO, который можно легко получить за десятую часть цены.
- Из других распространенных барьерных пигментов слюда почти полностью инертна. Алюминиевая чешуйка чувствительна к влаге и щелочам. Хлопья нержавеющей стали находят применение в некоторых случаях, но они относительно дороги. Стеклянные хлопья популярны в толстослойных покрытиях для тяжелых условий эксплуатации.
Пигменты активной защиты
Фосфат цинка занял прочную позицию в качестве активного пигмента в антикоррозионных грунтовках. Считается, что он имеет три защитных механизма:
- Формирование защитной анодной пленки
- Донорство фосфат-иона субстрату
- Образование антикоррозионных комплексов с некоторыми связующими
Модификации фосфата цинка включают, например: фосфат алюминия-цинка, фосфат молибдата цинка и гидрат силикофосфата цинка.
Силикагели, модифицированные кальцием , представляют собой экологически безопасные ингибиторы коррозии. Пигмент — это не содержащие тяжелых металлов, нетоксичные, микронизированные, аморфные частицы, которые предлагают альтернативу антикоррозионным агентам, не соответствующим требованиям государственных органов. Модифицированный кальцием силикагель является слабощелочным (pH 9-10) и производится посредством реакции ионного обмена на поверхности силикагеля между слабокислотными силанольными группами и гидроксидом кальция. Модифицированный кальцием силикагель представляет собой пористое твердое вещество, имеющее низкую плотность и большую площадь поверхности по сравнению с антикоррозийными пигментами на основе тяжелых металлов.
Следовательно, количество модифицированного кальцием силикагеля, необходимого для обеспечения противокоррозионной защиты, значительно меньше по сравнению с антикоррозийными агентами, содержащими тяжелые металлы. Модифицированный кальцием силикагель защищает металлические поверхности посредством механизма диффузии ионов кальция и растворимых частиц кремнезема. И разработать катодные и анодные площадки и подавить процесс коррозии. Модифицированный кальцием силикагель обычно используется для рулонных покрытий и тонкопленочных покрытий.
Фосфосиликат кальция-стронция — это относительно новый антикоррозионный пигмент, не содержащий цинка, который считается более экологически безопасным, чем ингибитор коррозии фосфат цинка.Обработка поверхности фосфосиликата кальция-стронция специально разработанными органическими соединениями улучшает смачивание и совместимость с различными составами покрытий. Кроме того, фосфосиликат кальция-стронция также можно использовать в широком спектре воды и Системы покрытий на основе растворителей .
Фосфат алюминия , используемый в качестве антикоррозийного пигмента, представляет собой триполифосфат алюминия (Al 5 P 3 O 10 ). Триполифосфат алюминия считается экологически чистым пигментом и доступен для использования в качестве недорогого антикоррозийного пигмента с середины 1980-х годов.Триполифосфат алюминия можно использовать в широком спектре систем покрытий на основе растворителей, а также в покрытиях на водной основе. Также было обнаружено, что он полезен в термостойких покрытиях.
Перестановки и комбинации
Можно считать, что ряд элементов и соединений обладают некоторым защитным действием от коррозии. И это привело к развитию широкого спектра пигментов, которые, как выясняется при исследовании, содержат один и тот же относительно небольшой набор защитных материалов в различных комбинациях.Можно вкратце упомянуть некоторые дополнительные примеры (обязательно неполные):
- Молибдаты эффективны, но дороги, и поэтому обычно встречаются в форме соединений, которые включают другие антикоррозионные элементы, такие как молибдат цинка, молибдат цинка кальция и фосфат молибдата цинка. .
- Триполифосфат алюминия (также доступен в формах, модифицированных ионами цинка или силикатом) — ион триполифосфата способен хелатировать ионы железа в дополнение к защитному эффекту самого фосфата.
- Силикаты могут быть найдены в форме комбинаций, таких как боросиликат кальция, фосфосиликат кальция-бария, фосфосиликат кальция-стронция-цинка, фосфосиликат стронция, фосфосиликат бария.
- Оксиаминофосфатная соль магния коммерчески предлагается, но рекомендуется только для использования в грунтовках на основе растворителей. Имея относительно низкий удельный вес 2,2, его можно использовать с меньшим весом, чем пигменты на основе цинка.
Проводящие полимеры
По своей природе проводящие полимеры, из которых наиболее широко известен полианилин, представляют собой действительно современную разработку. И среди их многочисленных применений было обнаружено, что они обладают двойным антикоррозийным действием:
- Каталитическая реакция со сталью дает тонкий, плотный слой оксида Fe 2 O 3 , который имеет барьерный эффект, аналогичный слоя Al 2 O 3 , который образуется естественным образом на алюминии
- Механизм катодной защиты, аналогичный тому, который обеспечивается ингибитором коррозии цинком
Таким образом, чтобы быть эффективным, полианилин должен находиться в прямом контакте с металлической подложкой.Было показано, что он хорошо работает в качестве тонкой пленки для предварительной обработки под другими антикоррозийными красками, и был коммерциализирован в виде грунтовок. Утверждается, что эти грунтовки превосходят грунтовки с высоким содержанием цинка при перекрытии эпоксидными смолами и способны защищать поверхность даже тогда, когда повреждение покрытия распространяется до царапины шириной 2 мм.
Кроме того, в патенте заявлено, что этот уровень защиты может быть повышен за счет включения жертвенных анодных частиц металла или металлического сплава вместе с собственно проводящими полимерами, такими как полианилин.Таким образом, в одном покрытии наносятся как барьерная, так и анодная защита.
Испытания ингибиторов коррозии
Для получения лучших результатов следует тестировать различные ингибиторы коррозии, используемые в разных дозировках. Конечно, стойкость и свойства краски не должны изменяться при использовании этого ингибитора коррозии.
Обычно до 3,0 — 4,0% от общего состава
Жидкие ингибиторы коррозии работают совместно с антикоррозийными пигментами.Они также улучшают долговременную коррозионную стойкость.
Чтобы обеспечить наилучшие характеристики, они должны быть идеально диспергированы:
- Предпочтительно добавлять на стадии диспергирования пигмента для обеспечения идеальной гомогенизации. В случае последующего добавления требуется достаточное перемешивание
- На водной основе может потребоваться предварительная смесь с нейтрализующим амином и / или коалесцирующим растворителем
Что касается основания, подготовка поверхности и особенно смачивание и адгезия жидкой краски имеют решающее значение.Загрязненная, грязная и пористая поверхность увеличивает чувствительность к коррозии. Шероховатая поверхность после шлифовки улучшит адгезию краски.
Для проведения лабораторных испытаний настоятельно рекомендуется использовать некоторые стандартизированные панели
для испытаний на коррозию.
После приготовления состава и полного отверждения краска должна быть испытана другим методом коррозии, например:
Циклические испытания
- Циклические испытания QUV
- Конденсация QUV (ASTM G154)
- Цикл-УФ-свет * -4 часа с последующим циклом конденсации-4 часа
- Цикл-камера конденсации поддерживает 100% относительной влажности, 50 ° C * Люминесцентные УФ-лампы
- QUV Prohesion (ASTM G85 A5)
- Циклический, воздействие панелей во влажный / сухой периоды
- Циклическое испытание на коррозию, состоящее из одной недели в QUV и одной недели в цикле износостойкости *
- УФ-облучение
* Цикл протезирования — образцы, подвергшиеся воздействию раствора электролита (0.05% NaCl + 0,35% сульфата аммония) при 35 ° C в течение одного часа, затем сушат при 40 ° C в течение одного часа, цикл повторяется - Конденсация QUV (ASTM G154)
- Xenon Arc Exposure (ASTM D2568, G26)
Имитирует полный спектр солнечного излучения — УФ, видимое и инфракрасное излучение.
Статические испытания
- Испытание в солевом тумане (ASTM B-117)
5% раствор хлорида натрия распыляется с помощью форсунки в закрытую камеру для образования статического тумана. Панели подвешиваются в нем на установленный период времени.Температура поддерживается постоянной (95 ° F). Слабая корреляция с ожидаемым сроком службы покрытия. - Испытание на контролируемую влажность (ASTM D2247)
Оценивает влияние влаги на коррозию. Образцы подвергаются воздействию относительной влажности 100%. - Испытание на погружение (ASTM D870)
Образцы погружают в ванну с деионизированной водой при 100 ° F. - Спектроскопия электрохимического импеданса (EIS)
Сигнал малой амплитуды подается на ранее погруженную панель с краской в широком диапазоне частот.EIS измеряет разрушение покрытия из-за воздействия электролита. Оценка скорости коррозии (от 30 минут до 24 часов после погружения) выполняется быстро. - Испытание на нитевидную коррозию (ASTM D2803)
Панели с разметкой, помещенные в коррозионную атмосферу (солевой туман на 4-24 часа) или погруженные в солевой раствор Панели, подверженные воздействию влажности (77oF и относительная влажность 85%)
Другие методы тестирования
- Внешний вид
- Тест на влажность (ASTM D2247)
Могут быть проведены другие испытания на коррозию, такие как ускоренное атмосферное воздействие с использованием определенных устройств или специальные испытания на распыление, чтобы воспроизвести состояние загрязненной атмосферы.
Цель достигается, когда уровень коррозии ниже предельного уровня по прошествии необходимого времени
Антикоррозионные преимущества органических-неорганических гибридных покрытий
Термин « гибридных покрытий » правильно используется в связи со многими различными системами, в которых присутствуют две (или более) системы связующих с различными свойствами и механизмами отверждения. Хотя существует множество таких систем, наибольший потенциал для повышения уровней характеристик покрытия — или достижения эффектов, которые нельзя получить никаким другим способом, — связан с крайним случаем гибридного покрытия.То, в котором органические и неорганические компоненты объединены на молекулярном уровне или на уровне тонко функционализированных наночастиц.
Некоторые из наиболее часто используемых гибридных покрытий включают:
- Силикатные покрытия с высоким содержанием цинка
- Эпоксидно-силоксановые гибридные покрытия
- Золь-гель покрытие
Покрытия с высоким содержанием цинка — Классический пример — это силикатные покрытия с высоким содержанием цинка, содержащие небольшие количества органических связующих материалов (в частности, алкилсиликатного типа).Эта форма гибридного покрытия используется для обеспечения превосходной защиты от коррозии.
Органосилоксановые покрытия для тяжелых условий эксплуатации — Было обнаружено, что эпоксидно-силоксановые гибридные покрытия обеспечивают лучшую внешнюю долговечность, чем даже двухкомпонентные полиуретановые покрытия. Связующие могут иметь очень низкую вязкость, что позволяет наносить покрытия с содержанием летучих органических соединений около 120 г / л и толщиной пленки до 200 мкм. Они также обладают высокой устойчивостью к граффити, инертны к большинству ядерных излучений, огнестойки и устойчивы к коррозии.
Золь-гелевые покрытия — Золь-гелевые покрытия из модифицированного уретаном полисилоксана обладают отличной адгезией к металлам, таким как алюминий. Кроме того, они эффективно противостоят химическому воздействию благодаря образованию плотно упакованной сшитой сети. Было обнаружено, что они полезны в качестве защитных покрытий на таких элементах, как теплообменники, которые имеют множество плотно упакованных металлических «ребер», на которые трудно нанести покрытие, и для которых желательны небольшие пленки.