Обработка порогов автомобиля своими руками
Обработка порогов автомобиля от коррозии своими руками – невероятно важный вопрос, имеющий большой вес в автомобильном сообществе. Накладные пластиковые или металлические накладки не имеют ничего общего с полноценными порогами авто. Это несущие части корпуса, которые отвечают за жесткость и безопасность. Пороги находятся в непосредственной близости к дорожному просвету, что ставит их сохранность и целостность под угрозу. Осложняется задача и местом расположения.
Немного автолюбители имеют достаточно свободного времени, чтобы регулярно осматривать пороги. Наиболее сложной ситуация становится после небольшого повреждения, например, наезда на высокий бордюр. Достаточно небольшой царапины на слое лакокрасочного покрытия, чтобы коррозия начала свое действие. Сегодня мы поговорим о способах защитить уязвимую часть кузова от ржавчины. Поговорим и о том, как проверить состояние порогов после замены.
Как правильно обработать изнутри
К целом, весь процесс обработки порогов можно разделить на две большие категории: внутренняя и наружная обработка.
- Моем авто. Не пропускайте этот этап, на загрязненной поверхности легко пропустить следы механических повреждений.
- Снимаем защитные элементы и внутренние части порогов. На этом же шаге важно промыть пороги, из старых автомобилей можно вымыть более килограмма песка.
- Полное высыхание. Остается выждать перед нанесением антикоррозийного состава. Спешить нельзя, иначе работа будет выполнена впустую.
- Нанесение антикоррозийного состава. Здесь выбор только за вами, мы поговорим подробнее о выборе средства ниже.
Про выбор состава для обработки модно писать целые тома научных докладов. Условно мы можем их разделить на заводские стандартны и любительские методы. Последние ничем не уступают, а иногда и превосходят дорогостоящие аналоги. Здесь важно учитывать несколько моментов. В первую очередь нам нужен вязкий, тягучий, но жидкий состав, который плотно прилегает к порогу, обеспечивает его защиту долгое время. Состав должен хорошо противостоять коррозии, не смываться влагой. Мы лишь приведем по одному примеру из каждой категории.
К проверенному любительскому средству относятся свечи и солярка. Да, да, вы не ослышались, именно обычные парафированные свечи. Покупает около 10 – 15 больших штук и кладем в ведро или кастрюлю из металла. Теперь нам потребуется газовая горелка, вы уже догадались для чего. Растопим свечи до жидкого состояния, добавим солярки и состав готов. Вязкий парафин прекрасно держится на поверхности. Солярка препятствует быстрому застыванию смеси и великолепно справляется с ржавчиной.
Профессиональными составами является «Мовиль» и «Dinitrol». Второй состав намного дороже «Мовиля», но по своей сущности они очень похожи. Обусловить разницу в цене сложно, но при первом же использовании бросается в глаза долгий процесс высыхания более бюджетного средства.
Вообще, мы бы настоятельно рекомендовали выполнять работы в сервисном центре, если вы не уверены в возможности качественно обработать пороги авто с внутренней стороны своими силами. Если мы говорим про надежное СТО, то мастера знают слабые места каждого автомобиля, имеют представление и о том, как правильно получать доступ к внутренней части порога. Иногда мастер может дать рекомендацию, которая не только сэкономит средства, но и продлит жизнь вашему автомобилю: заменить порог.
Чем обработать пороги автомобиля снаружи
Почему вообще возник вопрос, чем обработать пороги автомобиля снаружи в XXI веке? Ведь на рынке продаются сотни профессиональных средств, которые полностью решают проблему. В реалии дело в том, что эти профессиональные составы на практике не обладают нужными качествами. Не все. Но выбрать среди десятков некачественных составов подходящий невероятно сложно, а цена риска слишком высока.
Если обработать пороги составом невысокого качества или нарушить технологию, то пороги продолжат разрушаться коррозией. В то же время автовладелец может быть уверен в полной защите своего авто и не обращать внимания на состояние порогов в зимнее время, когда реактивы и соли разрушают кузов.
Сегодня мы расскажем о 4 средствах обработки порогов автомобиля снаружи. Первые три можно назвать любительскими, хотя многие профессиональные средства лишь созданы на их основе. Выбор будет только за вами. А пока короткая справочная информация о том, как технически правильно приступать к обработке порогов:
- Тщательно моем машину. Это не просто формальность, вам просто необходимо оценить состояние порогов на автомобиле. Если есть сквозные дыры из-за ржавчины, то пороги целесообразно заменить полностью. И еще один важный момент: какое бы средство для обработки вы не выбрали, наносить его нужно на чистую и абсолютно сухую поверхность.
- Устраняем следы ржавчины. Ржавчину нужно убрать полностью. Зачищайте вручную или шлифовальным кругом, но нужно дойти до чистого слоя металла. Сейчас мы не будем приводить примеры достаточно толщины металла, чтобы не прибегать к замене, просто запомните эти два простые шага, предшествующие обработке любыми составами, о которых и пойдет речь ниже.
Обработка порогов пушечным салом
Пушечное сало в кругу автомобилистов называется просто – пушсало. Антикор достаточно дешевый, по своей составу и внешнему виду очень напоминает парафин или литол большой густоты. В основу пушечного сала входит нефтяное масло, которое загущается с помощью петролатума и церезина. Если мы говорим про пушечное сало хорошего качества, то в него могут быть добавлены специальные присадки. Присадки предотвращают повторное образование коррозии.
Главным преимуществом состава является прекрасное удержание на любой поверхности. О хороших способностях защищать авто от коррозии мы не говорим – это очевидная характеристика для средства в нашем списке. Теперь коротко о технологии нанесения:
- Приобретаем пушечное сало. Пункт очевидный, но буквально несколько слов о емкостях и местах приобретения. Купить можно в большинстве автомобильных магазинов. Емкости обычно от 2 до 5 литров. В среднем на обработку одного авто (авто, а не порога) уходит около литра.
- Выкладываем в тару и нагреваем. Потребуется металлическая тара, а также газовая горелка. Плавится смесь при температуре от 90 градусов по Цельсию. Добиваемся вязкой консистенции.
- Обезжиривателем протираем зачищенные пороги. Наносить состав можно только на обезжиренную поверхность. В качестве инструмента проще всего использовать пистолет.
Важной рекомендацией станет соблюдение правил пожарной безопасности. Рекомендуется поставить рядом огнетушитель из машины, поскольку работа сопряжена с риском воспламенения.
Обработка порогов битумной мастикой
На самом деле говорить много про обработку порогов битумной мастикой не имеет смысла. Весь процесс можно описать в нескольких предложениях. Битумная мастика знакома абсолютному большинству автовладельцев. Даже, если вы не использовали ее ни разу, то прекрасно знаете классическую банку с аналогичным названием.
Сам же процесс обработки такой: необходимо разогреть твердую смесь до жидкого состояния. Делать это прямо в банке на горелке или переливать в отдельную тару – решать вам. Дальше нужно нанести битумную мастику на пороги, только осторожно, мастика будет стекать и загрязнит пол, отмывать ее крайне тяжело. Поэтому просто рассмотрим основные качества мастики:
- Хорошая защита от коррозии. Если сравнивать битумную мастику с каучуковой, то первая лучше защищает от ржавчины. Это связано с компонентами в ее составе.
- Механическая защита не на самом высоком уровне. Главная проблема битумной мастики в ее физическом состоянии. Полностью она не затвердевает никогда, поэтому она плохо устойчива к вылетающим камням и песку. Поэтому многие владельца авто сначала кладут слой битумной мастики, затем покрывают другим веществом, более устойчивым к механическим повреждениям составом.
Обработка порогов жидкой резиной
О жидкой резине слышали не многие автовладельцы. Между тем, этим веществом покрывается весь кузов автомобиля, поэтому говорить о целесообразности покрытия жидкой резиной излишне.
- Нет необходимости тщательно готовить кузов. Обычного мытья вполне достаточно.
- Свойства резины. Состав невероятно вязкий и плотный, он идеально плотно прилегает к порогу. Также резина обладает высоким уровнем пластичности, поэтому она прекрасно справляется с механическими повреждениями.
- Вязкость. Резина намного более плотная и вязкая, чем мастика. Поэтому работать с ней даже проще, ее можно спокойно наносить на горизонтальные поверхности.
- Удобный распылительный процесс. Жидкая резина наносится при помощи специального баллона под высоким давлением, что позволяет распределить ее равномерно.
Сам же процесс, достаточно просто, главное не жалеть растворитель и приобретать не самый дешевый аналог. Также мы рекомендуем наносить несколько равномерных слоев, поскольку пороги будут сталкиваться с постоянными механическими повреждениями. Нередко можно услышать негативные мнения пользователей о покраске жидкой резиной, главной жалобой является быстрое облезание. Когда мастер осматривает поврежденный кузов, оказывается, что толщина составляла 1мм, поэтому главная проблема в качестве обработки, а не составе.
Обработка порогов Мовилем
Сразу же сделаем одно небольшое уточнение – Мовиль, оригинальный мовиль, имеет четкий состав, поэтому называть любое антикоррозийное средство так категорически неправильно. Состав мовиля следующий и меняться не может:
- Моторное масло.
- Олифу.
- Антикоррозийные вещества.
Если состав как-то отличается, то называть антикоррозийное средство мовилем неверно. Своим названием состав обязан место своего появления – Москва и Вильнюс, отсюда и название. Мовиль представлен в нескольких консистенциях: аэрозоль, жидкость и паста. Выбирать подходящий вариант нужно в зависимости от степени коррозии и решаемых задач. Рассмотрим каждый из видов детальнее:
- Аэрозоли.
Еще удобная банка для нанесения, объем составляет 520 миллилитров. Минусы – стоимость и необходимость держать в вертикально положении. Под днище машины уже не залезешь, распылять в горизонтальном положении баллон не станет. На стоимость влияет наличие газа внутри, именно за счет него и происходит распыление.
- Жидкость. Самый бюджетный вариант для антикоррозийной обработки. Канистра 3 литров стоит около 3 – 4 долларов в зависимости от места продажи и наценки. Очень удобно обрабатывать обычной кисточкой, можно добраться до труднодоступных мест, а также добиться максимально ровного распределения.
- Пастообразный мовиль. Чаще всего продается в пластиковых или металлических банках. Стоимость невысокая и составляет около 2 – 3 долларов. Обрабатывать поверхность придется с помощью кисти, т.к. состав достаточно вязкий. Предварительно придется разбавлять состав небольшим количеством растворителя.
Компания arki-porogi рекомендует выполнять все работы в сертифицированном сервисном центре. Чтобы элементы кузова не ржавели нужно тщательно зачистить поврежденный участок, оценить степень повреждения. Иногда целесообразнее полностью заменить порог. Опытные мастера знают, чем лучше обработать элемент кузова в конкретной ситуации.
Обработка порогов автомобиля – делаем все самостоятельно!
Коррозия, мелкие камушки, песок и соли наносят существенный вред вашему «железному коню», поэтому крайне желательно знать, как именно осуществляется антикоррозийная обработка порогов автомобиля, своими руками вы сможете выполнить ее после прочтения нашей статьи. Первый раз сделать эту процедуру рекомендуется, конечно, у специалистов, а в дальнейшем можно будет обойтись и своими силами, просто поддерживая актуальность защиты.
Обработка порогов – посетить СТО или сделать самостоятельно?
При современном состоянии автопрома антикор для корпуса делают еще на заводе-производителе, но, дабы машина не вышла из строя раньше, чем предполагает гарантийное обслуживание, его следует повторять каждые два года. Благодаря этому вы сможете поддерживать целостность заводского покрытия максимально длительный срок. Таким образом, вы защитите наиболее уязвимые места вашего авто, а ими являются сварные швы, скрытые полости, колесные арки, пороги, днище и загибочные соединения.
Главным отличием между антикоррозионной обработкой, которую вы сделаете дома, и обработкой на специализированной станции является, конечно, наличие профессионального оборудования у вторых. Благодаря этому намного проще тщательно вымыть днище авто, а затем осуществить его принудительную сушку. Кроме того, на станциях производится комплексная обработка несколькими покрытиями, естественно, можно попытаться все это сделать и самостоятельно, но тогда вам такой эксперимент обойдется в копеечку, да и отсутствие опыта возьмет свое, так что экономия будет сомнительной.
Также специалисты обязательно установят брызговики и подкрылки, таким образом, защита наружной части автомобиля от воды песка и гравия будет более надежной.
Антикоррозионная обработка порогов автомобиля своими руками
Повторная обработка порогов авто проводится самостоятельно, для этого понадобятся: антикоррозионное средство (Otrix, Rand, Novol, Car System, Roberlo и т.д.), средство от ржавчины, наждачная бумага или металлическая щетка, респиратор и перчатки. Покупая антикоррозионное средство, следует обращать внимание на все мелочи: назначение, срок годности, особенности применения. А в дальнейшем важно строго придерживаться инструкции на упаковке.
Для начала тщательно вымойте авто от грязи и просушите. Постарайтесь обеспечить доступ ко всем местам обработки, в случае работы с днищем машину следует установить на эстакаду. Удалите ржавчину при помощи наждачной бумаги или металлической щетки. Теперь обработайте поверхность средством от ржавчины и дайте хорошенько высохнуть.
Приступаем к обработке приобретенным средством. Его равномерно нанесите на пороги автомобиля и другие части, требующие защиты с помощью данного состава. Остается просушить авто в течение суток. Важно помнить, что нельзя работать рядом с огнём или нагревательными приборами, так как, в основном, все вышеперечисленные средства легко воспламеняемы. Кроме того, чтобы не нанести вред своему здоровью, рекомендуется работать в перчатках и респираторе.
Обработка порогов антигравием – последовательность операций
Обработка порогов антигравием происходит практически аналогично:
- авто тщательно моется и высушивается;
- наждачной бумагой удаляется ржавчина и облущенная краска;
- с помощью газет и скотча закрываем все места, прилегающие к порогам, чтобы не запачкать их. кстати, это необходимо делать в каждом случае, когда используется баллончик с распылителем;
- потрясите баллончик на протяжении 3–5 минут;
- нанесите антигравий с расстояния 25 см;
- дайте нанесенному слою высохнуть на протяжении 5 минут;
- повторите процедуру еще 1-2 раза;
- просушите авто в естественных условиях в течение хотя бы двух часов.
Возможно, вы постоянно слышите, насколько эффективна обработка порогов гравитексом, но, по сути, это тот же антигравий, и, соответственно, все вышеперечисленные операции выполняются в том же порядке. Перед тем как покупать это антикоррозионное средство, просмотрите внимательно его характеристики, так как он бывает окрашиваемым и не окрашиваемым. Тут также не забывайте про безопасность кожи рук и дыхательных путей и внимательно читайте инструкцию перед применением.
Чем обработать пороги автомобиля снаружи от коррозии
Довольно распространенной среди автомобилистов является проблема защиты своего авто изнутри и снаружи от мелких и неприятных повреждений, которые наносит гравий, песок и соль на зимних дорогах, а также коррозии. Но поскольку автомобиль является приобретение далеко не дешевым, то забота о его целостности и сохранности становится ключевым вопросом для их владельцев. Поэтому было создано огромное количество специальных средств и методик защиты самых уязвимых частей автомобиля изнутри – порогов.
Защита порогов: на СТО или самостоятельно
В перечень мероприятий по защите порогов автомобиля важное место занимает антикоррозийная обработка порогов изнутри и снаружи. Ее довольно несложно выполнить своими руками, но первый раз нанести покрытие от коррозии все же лучше у специалистов, а потом просто поддерживать ее состояние. Это обусловлено несколькими аспектами:
Что нужно купить для самостоятельной обработки порогов
Если же первичную обработку от коррозии вы уже проходили, тогда вам необходимо поддерживать эффект от нанесенного покрытия путем повторения такой процедуры. Для нанесения антикоррозийного покрытия своими руками вам нужны:
- антикоррозийная жидкость;
- состав для защиты от ржавчины;
- металлическая щетка и наждачная бумага;
- средства индивидуальной защиты – перчатки и респиратор.
При выборе средств для обработки и защиты от коррозии своими руками всегда внимательно читайте инструкцию, а именно сроки годности, предназначение и специфика использования. Также важно следовать всем рекомендациям производителей во время работы.
Процесс работы
Далее разместите автомобиль так, чтобы вам было удобно работать с зонами обработки внутри, например, если будет обрабатываться днище автомобиля снаружи, то используйте эстакаду. Потом следуйте простой схеме работы:
- Тщательно вымойте свою машину от грязи и пыли с моющим средством, затем вытрите насухо.
- Все зоны, где появились малейшие проявления ржавчины необходимо зачистить щеткой или наждаком.
- Нанесите слой средства от ржавчины и оставьте сохнуть на срок, указанный на упаковке.
- Затем наносится антикоррозийная эмульсия, следите за равномерностью нанесения вещества на пороги.
После этого автомобиль следует сушить минимум сутки. Во время работы избегайте источников тепла, поскольку эти составы очень легко воспламеняются. Также не забывайте использовать средства для своей защиты, используемые вещества очень опасны для здоровья.
Многие владельцы автомобилей кроме средств от коррозии также используют защиту антигравием, которая препятствует появлению мелких повреждений на порогах во время езды.
Обработка антигравием своими руками производится по практически аналогичной схеме:
- Качественная мойка и сушка машины.
- Очистка поверхности от ржавчины и сколов краски при помощи наждачной бумаги.
- Все места, которые прилегают к порогам автомобиля, заклеиваются защитным покрытием. Важно предотвратить их «пачкание» антигравием, который наносится спреем.
- Подготовьте состав. Он должен быть комнатной температуры, встряхивайте его от 3 до 5 минут, потом распылите, сохраняя дистанцию между баллончиком и кузовом в 25-30 см.
- Нанесенный слой должен просохнуть около 5-10 минут, потом нужно повторить процесс еще два раза.
- После нанесения последнего слоя авто нужно оставить сушиться минимум на 2 часа, но рекомендуется на сутки.
Коррозия порогов автомобиля
Нюансы выбора средств обработки
При выборе средств от коррозии для обработки автомобиля учитывайте некоторые особенности:
- очень популярным среди специалистов является покрытие Гравитекс, но, по своей сути, оно является тем же антигравием и технология работы с ним аналогична,
- при покупке антикорра уточните, является ли антикоррозийная жидкость окрашиваемой, поскольку она не всегда прозрачная,
- всегда используйте респиратор перчатки, поскольку все подобные вещества очень агрессивны.
[democracy]
[democracy]
Если хотите больше интересных статей по тематике авто, подпишитесь на наш канал в ЯндексДзен.
Автор: Екатерина
Обработка порогов автомобиля своими руками
Добрый день, уважаемые читатели и гости блога. Сегодня в статье мы расскажем об обработке порогов автомобиля своими руками для защиты от ржавчины. Все автолюбители сталкивались с проблемой ржавых порогов. Она актуальна для любого автомобиля, эксплуатируемого на дорогах страны.
Антикоррозийная обработка порогов автомобиля способна решить проблему появления ржавчины. Если пустить процесс коррозии на самотёк, то через несколько лет придётся полностью менять пороги машины. Ржавчину проще предотвратить, чем в последующем бороться с её разрушительным действием.
В статье можно увидеть небольшое видео по обработке порогов автомобиля своими руками. Оно может использоваться при выполнении антикоррозийной обработки в режиме реального времени. Достаточно иметь под руками смартфон или планшет.
В конце статьи вас ожидает интересное и увлекательное видео. Покажет разрушительное действие ржавчины на автомобиль.
Антикоррозийная обработка порогов автомобиля своими руками
Пороги автомобиля нуждаются в защите, так как находятся в нижней части автомобиля и подвержены отрицательному воздействию внешних факторов (перепады температуры, солевые реагенты, отрицательная температура, повышенная влажность).
Часто мелкие камни, песок, щебень и гравий способны оставлять на внешней стороне порога небольшие повреждения. Зачастую становятся очагами будущего коррозийного процесса.
Выбор средств антикоррозийной обработки порогов машины широк и разнообразен. Можно найти дешёвые или дорогие средства. Все они получили обобщённое название “антигравий для порогов”. Могут продаваться в баллончиках или металлических банках.
Если нет возможности задействовать подъёмник для обработки порогов, то лучше перенести работы на летний период. В летние месяцы можно заехать на эстакаду и работать на открытом воздухе. Зимой или осенью выполнять работы по обработке порогов нельзя.
Процесс обработки порогов автомобиля можно разделить на несколько этапов:
1.Подготовка материалов и спецодежды.
- рабочая одежда, закрывающая все участки кожи;
- резиновые перчатки;
- защитные очки;
- респиратор;
- щётка по металлу;
- наждачная бумага;
- чистая вода;
- средство для антикоррозийной обработки порогов;
- Уайт-Спирит для обезжиривания
- преобразователь ржавчины;
- ветошь;
- строительный фен.
2.Подготовка автомобиля.
- демонтировать защиту;
- тщательная мойка машины с упором на пороги;
- сушка автомобиля;
- заезд на подъёмник или эстакаду;
- удаление всех очагов ржавчины на порогах при помощи наждачной бумаги или специального диска;
- обработка порогов преобразователем ржавчины;
- обезжиривание порогов;
- сушка порогов;
- использование малярной ленты для защиты прилегающих к порогам мест;
3.Нанесение антигравия на пороги.
- баллончик с антигравием следует интенсивно встряхивать неменее 2-3 секунд перед использованием;
- держать баллончик нужно на расстоянии 15-20 сантиметров от поверхности порога;
- следить за равномерностью нанесения средства защиты;
- между слоями надо выдерживать время порядка 5-7 минут;
- оптимальное количество слоёв антигравия не менее 3;
- для ускорений сушки антикоррозийного средства можно воспользоваться строительным феном;
- удаление малярной ленты;
- установка на место защиты;
- использовать автомобиль не раньше чем через 2 часа после обработки.
Ничего сложного в обработке порогов от ржавчины нет. Нужно подготовиться и соблюдать последовательность действий. Не стоит спешить, так как страдает качество работы.
Антикоррозийная обработка порогов автомобиля с использованием мастики
Этот способ обработки порогов машины своими руками пользуется меньшей популярностью. Объясняется всё трудоёмкостью процесса и большим количеством затраченного времени.
Для защиты порогов можно приобрести «Антикор битумный». Представляет собой мастику холодного нанесения. Производится на основе смешивания каучука и смол. Обладает доступной стоимостью и можно с лёгкостью найти в продаже.
Подготовительный этап автомобиля аналогичен, как и в случае использования антигравия. Днище машины надо тщательно вымыть, высушить и очистить от очагов ржавчины. После этого можно приступать к нанесению антикоррозийной мастики.
Перед использованием «Антикора битумного» его лучше немножко подогреть. Это увеличит его текучесть и уровень адгезии. Наносится мастика обыкновенной малярной кистью. Не нужно жалеть мастики. Толщина слоя напрямую влияет на эффективность и долговечность защиты порогов от коррозии.
После нанесения мастики нужно дождаться естественного высыхания антикоррозийного материала. Использование фена для сушки даст обратный эффект. В среднем достаточно 2 часов. По окончании этого времени можно ставить на место защиту и пользоваться автомобилем.
Виды антигравия для порогов автомобиля
Количество средств антикоррозийной обработки порогов автомобиля велико. По большому счёту они мало чем отличаются друг от друга.
Средства защиты порогов машины от ржавчины можно разделить на несколько групп:
1.Период использования.
- постоянная защита;
- временная защита;
2.Упаковка.
- аэрозольный баллончик готовый для применения;
- аэрозольный баллончик под специальный пистолет;
- металлические банки;
- пластиковые ёмкости.
- прозрачный;
- белый;
- чёрный;
- cерый;
- цветной.
- с содержанием преобразователя ржавчины;
- антикоррозийными веществами;
- повышенная адгезия;
- усиленная прочность.
Выбираем средство для обработки порогов автомобиля своими руками
Несмотря на обилие всевозможных средств защиты порогов от коррозии многие автолюбители задаются вопросом: чем обработать пороги? Мы дадим на этот вопрос полный и исчерпывающий ответ. Он поможет автолюбителю сделать правильный выбор.
1.Антикор-спрей BODY-950, ёмкость 400 мл
Антигравий, созданный на основе специальных смол. Обладает высокой адгезией и устойчив к повреждениям. Для нанесения требуется использование специального пистолета. Быстро сохнет. Стоимость 4-6$.
2. Антигравий аэрозоль ЭЛТРАНС, ёмкость от 400 до 1000мл.
Недорогое, но эффективное средство. Не требует использования специального пистолета. Расход одного слоя 400 грамм на 1м². Рекомендуется наносить в 2-3 слоя. Стоимость за 400 мл. 2-3$.
3. Антигравий KERRY, ёмкость 650мл.
Качественный антигравий, обеспечивающий эффективную защиту порогов. Обладает высокой степенью адгезии. Не требует специальных навыков в использовании. Стоимость 3-4$.
Как обработаь пороги автомобиля
Пороги одно из наиболее уязвимых мест автомобиля. Со временем и под воздействием различных неблагоприятных факторов они теряют нанесенное ранее защитной антикоррозионное покрытие и нуждаются в дополнительной обработке и нанесении герметичной защиты. Работы по нанесению антикора на пороги возможно выполнить не только в автомастерской, но и самостоятельно в гараже своими руками.
Обработка порогов при помощи защитных мастик, лаков
В процессе обработки понадобятся такие вспомогательные инструменты и средства как:
- дрель с различными корщетками, металлическая щетка или абразивные шкурки;
- малярный скотч;
- преобразователь либо очиститель ржавчины;
- любое обезжиривающее средство;
- средство-консервант для защиты от коррозии скрытых полостей автомобиля.
Поэтапный процесс спецобработки выглядит так.
- Вымыть и высушить автомобиль, особенно его пороги.
- Обеспечить доступ ко всем местам которым требуется обработка (при необходимости снять наружную часть порога, очистить его внутреннюю полость).
- Удаляются остатки заводского антикора, места с поднятой и облущенной краской. Особо тщательно (желательно до металла) очищаются очаги с ржавчиной. Для этой процедуры можно использовать абразивную бумагу, металлическую щетку, дрель с корщетками.
- Поверхность обезжиривается ацетоном либо бензином и на нее наносится преобразователь или очиститель ржавчины.
- Любыми защитными материалами (бумага, полиэтилен, малярный скотч) закрываются места не подлежащие обработке.
- Нанесение протравливающего грунта.
- Обработка защитными средствами поверхности порогов автомобиля.
Возможно использовать аэрозольные битумные и полимерно-битумные мастики, мовиль, битумные лаки, материалы на масляной основе с ингибиторами коррозии (например Rust Stop А), антигравий на каучуковой основе (например Motip).
- Дать обработанной поверхности полностью высохнуть — не менее 2-4 часов.
Важно, чтобы обработка порогов автохимией, проводилась четко по инструкции к этим средствам.
Обработка порогов специальными жидкими локерами («жидкие подкрылки»)
Используемые жидкие локеры представляют из себя вязкую и плотную пасту, которая при нанесении на пороги автомобиля, после ее застывания, приобретает вид и качественные характеристики высокопрочной резины или приобретает свойства аналогичные упругой пластмассе. Помимо того, что такая антикоррозионная и антигравийная обработка придает порогам исключительную стойкость к механическим воздействиям и износу, она обладает еще рядом преимуществ:
- простота нанесения в труднодоступные места автомобиля;
- пластичность и однородность;
- стойкость к влаге, на обработанной поверхности исключается скапливание конденсата;
- высокая экологическая безопасность, нет выделения запахов и токсинов;
- хорошая адгезия к металлическим поверхностям автомобиля (наносимый материал не стекает, потеки не образуются), выносливость к температурным колебаниям и высоким температурам;
- дополнительная шумоизоляция.
Алгоритм действий при обработке жидкими локерами следующий.
- Перед тем как обработать пороги, авто предварительно очищают от пыли и тщательно моют, затем просушивают.
- Места с отставшей краской, ржавчиной и старым антикоррозионным покрытием механически зачищают и затирают с помощью наждачной бумаги, металлической щетки или дрели со специальными круглыми проволочными насадками.
- Поверхность порогов обезжиривается.
- Нанесение при помощи шпателя либо кисточки первого слоя антикора на пороги автомобиля.
- После просушки первого слоя равномерно наносят второй, состоящий из битумной мастики.
- Как только мастика просохнет, методом распыления наносят финишный, третий защитный слой с антикоррозионной резиной. Он хорошо заполняет все микротрещины оставшиеся после нанесения первых двух слоев. Все наносимые слои должны иметь оптимальную толщину в 1,5-2,5 мм.
- Обязательная сушка в течение 5-6 часов. Полное схватывание покрытия происходит через двое суток.
В качестве жидких локеров для обработки порогов автомобиля используют Noxudol 1100 либо DINITROL 47 (Швеция), Soudal (Бельгия), ol (Германия). Хорошие результаты дает обработка порогов средством Tectyl ML (консервант внутренних, скрытых полостей). В его состав входят нефтяные воски содержащие ингибиторы коррозии. Они глубоко пропитывают ржавчину и останавливают коррозионный процесс. Эффективно обработать пороги возможно Tectyl Zinc Bodysafe — это мастика содержащая диспергированный цинк с повышенной абразивной стойкостью. После высыхания образуется упругая и прочная пленка со слоем антикора имеющим металлические вкрапления.
Полезные советы при обработке порогов.
- Следует уделить повышенное внимание равномерности нанесения антикора и толщине распыляемого слоя.
- Подбирая мастику которой будет проводится обработка, следует в первую очередь обратить внимание на ее антикоррозионные свойства, а не на механические.
- Стоит удалить резиновые заглушки находящиеся в торцах порогов. Это может серьезно увеличить срок их службы.
Устал платить штрафы? Выход есть!
100% ЗАЩИТА ОТ КАМЕР ГИБДД — НАНОПЛЕНКА! Подробнее по ссылке
- Скрывает номер от камер и радаров.
- Начинает действовать сразу после установки.
- Быстро и легко приклеивается.
- Защита номеров до 2-х лет.
ЧТО ВЫ ПОЛУЧИТЕ БЛАГОДАРЯ НАНОПЛЕНКЕ
- На 100% скрывает номер от камер ГИБДД в любую погоду.
- Невозможно обнаружить защиту глазом.
- Прочно держится в любую погоду и после мытья автомобиля.
НАНОПЛЕНКА является полностью незаметной для человеческого глаза.
Антикоррозийная обработка порогов автомобиля своими руками. | Все об автомобиле и не только
В данной статье поговорим о антикоррозийной обработке порогов автомобиля в гаражных условиях. Каждый автолюбитель сталкивался со ржавчиной на порогах, так как это самая уязвимая часть кузова, которая больше всего подвержена механическим воздействиям. Антикоррозийная обработка порогов способна остановить распространение ржавчины, если же этого не сделать, то последствия будут печальными, а ремонт в последующем будет стоить намного дороже.
Перед обработкой антикором необходимо тщательно отмыть пороги, при
этом необходимо снять защитные элементы если таковые присутствуют. Лучше это сделать с применением автохимии и мощного напора воды, далее нужно дать порогам высохнуть.
Следующим этапом является удаление очагов ржавчины, если таковые присутствуют. Для этого необходимо металлической щеткой или специальной насадкой на дрель, пройтись по очагу коррозии. После механического удаления ржавчины следует химический этап, специальным составом на основе ортофосфорной кислоты, нужно покрыть место, зачищенное от коррозии место, когда на данном участке появится светлый налет, свидетельствующий о химической реакции кислоты с оксидом железа, можно приступать к следующему этапу.
Далее необходимо нанести защитный состав. Защитные составы можно разделить на несколько групп по типу нанесения:
- составы которые наносятся аэрозольным способом, такие составы продаются в баллончиках, их отличает простота нанесения и малый расход, но стоимость их выше, чем у составов, которые наносятся вручную.
Так же такие составы по мере высыхания немного увеличиваются в объеме и создавая более толстую защитную основу.
- составы которые наносятся вручную, например кистью, наносить такие составы сложнее, но стоимость их меньше.
А так же различают по типу защитной основы:
- пушечное сало.
- битумные мастики.
- автопластилин.
- раст-стоп.
Выбор антикора — это дело каждого, кому что нравится, но даже самый плохой антикор лучше, чем его отсутствие. Далее наносим антикоррозийный состав на пороги, ждем пока состав высохнет, в среднем достаточно 12 часов. Устанавливаем на место защитные элементы крепления.
Кроме защиты от коррозии у антикора есть еще одно положительное свойство это дополнительная шумоизоляция.
Ели Ваша цель заключается в защите порогов от коррозии и сохранении эстетического внешнего вида авто, то можно приобрести цветной антикоррозийный состав, который подходит к цвету кузова например белый, черный, серый. Если цвет антикора не пошел к цвету кузова автомобиля, то можно поверх такого состава нанести слой краски, подходящего цвета.
В заключении хочу сказать, что антикоррозийная обработка — это не разовая процедура, её нужно производить регулярно, хотя бы 1 раз в 3 года.
Спасибо за просмотр!
Антигравийная обработка кузова автомобиля своими руками: выбор средства, инструкция
Многие автовладельцы сталкивались с такой проблемой, как образование коррозии на раме и кузовных элементах автомобиля. Отчасти решить данную проблему и повысить защиту кузова от коррозии можно путем соответствующей антигравийной обработки металлических деталей специальными средствами. Поговорим подробнее о том, как защитить пороги автомобиля от коррозии.
Качественная антигравийная обработка кузова автомобиля позволяет предупредить появление ржавчины. Сегодня в продаже можно найти недорогие и эффективные средства, которые просты в использовании, и при этом такая автохимия отличается долговечностью, надежностью и качеством исполнения.
Как и где проводить обработку
Подобная антикоррозийная обработка порогов может выполняться как самостоятельно, так и при помощи специального оборудования в соответствующих автомастерских и сервисах. Отметим, что сегодня используются материалы на основе мастики, которые предполагают их нанесение из специальных распылителей. В то же время можно в продаже найти обычные антигравийки на основе органических средств, которые выпускаются в виде аэрозолей, что упрощает их самостоятельное использование.
Помните о том, что, какое бы качественное средство вы ни использовали, через 2−3 года такая автохимия потеряет часть своих защитных свойств и в последующем могут вновь появиться проблемы с коррозией. Чтобы предупредить подобное, рекомендуется каждые 2−3 года выполнять такую обработку днища и порогов. В дальнейшем вам останется лишь правильно покрасить обработанные пороги и днище авто.
Выбираем средство для работы
В последние годы наибольшее распространение получил антигравий в аэрозольной упаковке, который отличается простотой в использовании. Это может быть как специальный баллончик, уже готовый к применению, так и аэрозоли, предназначенные для нанесения из специального пистолета. В продаже вы также найдете такую автохимию, которая фасуется в пластиковые емкости или металлические банки и подразумевает нанесение из распылителя или вручную кисточкой.
Антигравий может быть прозрачным, белым, черным или других оттенков. Наибольшее распространение получил сегодня прозрачный и черный антигравий. Последний может использоваться для обработки днища и крыльев автомобиля изнутри. А вот если вам необходимо обработать снаружи пороги и другие наружные кузовные элементы, то рекомендуем использовать прозрачную разновидность или же проводить последующую покраску обработанных кузовных деталей.
В зависимости от дополнительных свойств такой антигравий может отличаться:
- Усиленной прочностью.
- Повышенной адгезией.
- Улучшенными антикоррозийными свойствами.
- Может содержать преобразователь ржавчины.
В том случае, если вы планируете выполнять такую обработку самостоятельно, рекомендуем вам приобретать антигравий-спрей, который эффективен, имеет доступную стоимость и прост в использовании. Можно подобрать такой аэрозольный антигравий с улучшенными показателями защиты от ржавчины.
Обработка порогов антигравием
Для выполнения самостоятельной антигравийной обработки кузова автомобиля вам потребуются следующие материалы и приспособления:
- Щетка по металлу.
- Преобразователь ржавчины.
- Наждачная бумага.
- Строительный фен.
- Ветошь.
- Уайт-спирит или средство для обезжиривания.
- Чистая вода.
- Респиратор.
- Защитные очки.
- Резиновые перчатки.
- Рабочая одежда.
Алгоритм действий при такой обработке автомобиля следующий:
- Днище, пороги и крылья автомобиля тщательно вымываются и высушиваются.
- С автомобиля демонтируется имеющаяся пластиковая защита.
- Машину загоняют на эстакаду или подъёмник.
- Осматривают авто на предмет наличия очагов ржавчины.
- Всю найденную коррозию зачищают наждачной бумагой и обрабатывают пороги преобразователем ржавчины.
- Дожидаются высыхания преобразователя ржавчины, после чего проводят обезжиривание порогов.
- Малярной лентой заклеивают все кузовные элементы, прилегающие к порогам и днищу.
- Баллончик с антигравием следует встряхнуть несколько секунд, после чего с расстояния около 15 см наносить спрей на обрабатываемую поверхность.
- Следите за равномерностью нанесения такого защитного средства.
- Лучше всего нанести несколько слоев антикора. Перерыв между нанесением каждого слоя составляет приблизительно 5 минут.
- Обработанное днище и пороги можно высушить строительным феном.
- Удаляют малярную ленту и устанавливают пластиковую защиту.
Помните о том, что пользоваться автомобилем можно не раньше, чем через 2−3 часа после такой обработки.
Как вы можете видеть, подобная обработка кузова автомобиля не представляет какой-либо сложности, поэтому с такой работой справится каждый автовладелец. Помните, что для качественного нанесения антигравия автомобиль следует загнать на яму гаража, эстакаду или подъёмник, это позволит существенно упростить выполнение обработки машины от ржавчины.
Обработка порогов и днища мастикой
Обработка днища и порогов автомобиля мастикой была популярна в прошлом, однако сегодня, с появлением недорогих аэрозольных средств, такая антигравийная защита пользуется все меньшей популярностью. Объясняется это трудоемкостью процесса и дороговизной качественной автохимии.
При использовании такой антигравийной мастики холодного нанесения необходимо тщательно вымыть днище и пороги автомобиля, очистить их от ржавчины, и лишь после этого можно наносить используемое защитное средство.
Совет. Перед нанесением мастику следует слегка подогреть, что улучшит ее текучесть и показатели адгезии.
Для нанесения антикора можно использовать обычную малярную кисть. Старайтесь нанести несколько слоев защитного покрытия, так как толщина мастики будет напрямую влиять на долговечность и эффективность защиты днища и порогов от коррозии.
В зависимости от конкретной разновидности мастики полностью она застывает в течение 2−5 часов. По прошествии этого времени можно использовать свой автомобиль.
Защитную обработку порогов автомобиля можно выполнить как самостоятельно, так и воспользовавшись предложением различных СТО. Если вы проводите такую защитную работу своими руками, можем порекомендовать использовать качественную автохимию для обработки, а всю работу выполнять в полном соответствии с алгоритмом, описанным в этой статье.
Оценка статьи:
Загрузка…
Читайте также:
Обработка автомобильной стали: нержавеющая сталь и оцинкованная сталь | National Material Company
Сталь продолжает оставаться лидером в производстве автомобилей благодаря своей сильной и надежной природе. Согласно worldsteel.org, использование стали в автомобилестроении дает несколько преимуществ. Сталь:
● Состоит из переработанной стали и подлежит бесконечной переработке.
● Имеет более низкий уровень выбросов CO2 в течение жизненного цикла, чем любой другой автомобильный материал.
● Позволяет проектировать противоударные конструкции.
● Это более прочная сталь, позволяющая сделать легкую конструкцию автомобиля более прочной, безопасной и более экономичной.
● Обеспечивает творческий и гибкий дизайн.
● Легко ремонтировать с помощью существующей техники и оборудования, что делает ремонт более доступным.
● Экономичен по сравнению со всеми другими конструкционными материалами.
Есть несколько распространенных применений стали в автомобилях. Большая часть этой стали содержится в каркасе автомобиля, часто называемом «кузов в белом», который является основой, на которой создается остальная часть автомобиля.
Бамперы и усиления
Бамперы — это одни из первых средств защиты автомобиля от любых сильных ударов, поэтому они требуют очень высокого уровня поглощения силы. Долговечность и устойчивость к ударам из высокопрочной стали делают ее отличным вариантом для бамперных систем. Еще одним движущим фактором его использования является возможность использовать более тонкую сталь, что способствует дополнительной экономии веса. Бамперы из UHSS обычно формируются в рулонах. Для получения более подробной информации о стальных бамперных системах для легковых и легких грузовиков посетите этот веб-сайт: https: // www.a-sp.org/-/media/doc/smdisteel/bumpers/smdi-steel-bumper-systems-manual-6th-edition—january-2019—final.ashx
Есть много других частей автомобиля, которые нуждаются в сильном усилении. Например, усиление порога и поперечины требуют высокого энергопоглощения. Жесткость можно сохранить при переходе на более тонкие панели, изменив геометрию деталей. Высокопрочные стали хорошо подходят для этих задач формовки, при этом уменьшенная толщина позволяет получить более легкую деталь.
Дверные балки и сиденья
Опять же, здесь важна экономия веса. Боковые противоударные балки теперь обычно изготавливают из высокопрочных сталей, что обеспечивает как повышенную безопасность, так и более легкий вес продукции. Хотя сиденья традиционно не считаются частью Body-in-White, они являются одними из самых тяжелых предметов в легковом автомобиле. Таким образом, они являются первыми кандидатами на облегчение с использованием высокопрочных и долговечных сталей.
Шасси и рамы
Высокопрочная сталь обеспечивает поддержку всей рамы.Шасси подвержено одним из самых экстремальных нагрузок, наблюдаемых в любых деталях автомобиля, поэтому ему необходимы превосходные свойства сопротивления усталости, такие как свойства высококачественной стали. Использование высокопрочных сталей с высокой формуемостью позволяет конструкторам транспортных средств гибко создавать легкие сложные формы, сохраняя при этом структурную целостность, требуемую приложением.
Улучшенная высокопрочная сталь
Forbes. com недавно сообщил, что современная высокопрочная сталь (AHSS) в настоящее время становится типом стали, которую производят крупные сталелитейные компании, чтобы удовлетворить потребности автомобильной промышленности.В автомобильной промышленности материалы, используемые для изготовления деталей автомобилей, выбираются на основе ряда важных критериев, среди которых прочность, пластичность, стоимость и «удобство изготовления». Автомобильная промышленность требует непрерывной разработки и производства AHSS, чтобы максимизировать прочность сталей, используемых для изготовления деталей, одновременно повышая безопасность, снижая вес и обеспечивая жизнеспособную альтернативу более дорогостоящим алюминиевым сплавам.
Одной из причин, по которой автопроизводители считают AHSS более выгодным, чем другие типы стали, является его компонент безопасности, особенно когда он используется для конструктивных элементов автомобиля, где важны высокая прочность при разумной пластичности.AHSS стал предпочтительным материалом для таких компонентов каркаса безопасности пассажиров, как усиление порогов, передних и средних стоек, боковых балок, усилителей талии, бамперов, дуг крыши и сидений.
Согласно steelsustainability.org, AHSS также полезен для окружающей среды. У него уменьшенный углеродный след. Он прочный, легкий и произведен с уменьшенным воздействием на жизненный цикл, что помогает автопроизводителям уменьшить углеродный след автомобиля от колыбели до могилы. Worldsteel.org сообщает, что использование AHSS способствует значительному сокращению выбросов парниковых газов по сравнению с какими другими марками стали и алюминиевыми сплавами? Новые марки современных высокопрочных сталей позволяют автопроизводителям снизить вес автомобиля на 35-40% по сравнению с обычной сталью.Применительно к типичному семейному автомобилю с пятью пассажирами общий вес транспортного средства уменьшается почти на 600 фунтов, что соответствует экономии более 4 тонн парниковых газов за весь срок службы транспортного средства.
Снижение выбросов парниковых газов — один из факторов, ускоряющих переход от транспортных средств с двигателями внутреннего сгорания (ДВС) к альтернативным подходам, таким как гибридные и электромобили. Рентабельная легкость имеет решающее значение для этих транспортных средств из-за необходимости компенсировать стоимость и вес аккумулятора.По этим причинам производители электромобилей включают AHSS в свои кузовные конструкции.
В National Material Company (NMC) мы занимаемся обработкой современной высокопрочной стали. Мы поддерживаем различные типы AHSS: двухфазные, мартенситные, комплексные, TRIP Steel и Press Hardened Steel. NMC управляет оборудованием для продольной резки, травления и обработки стали, которое обслуживает потребности сталелитейной промышленности и ведущих производителей промышленных и потребительских товаров.
Сталь оцинкованная
Вы можете с любовью размышлять об автомобилях 60-х и 70-х годов, но они превратились в ведра ржавчины, если их поцарапать. Автопроизводители начали обращаться к оцинкованной стали в 1980-х годах, что позволило им предложить гарантию на коррозию. Теперь некоторые производители предлагают 10-летнюю гарантию на некоторые формы коррозии. Что сделало это возможным? Использование оцинкованной стали на большинстве кузовных панелей. NMC с гордостью предлагает оцинкованную сталь высочайшего качества, помогая нашим клиентам во всех отраслях промышленности создавать долговечные, устойчивые к коррозии формованные детали.
Оцинкованная сталь используется из-за ее прочности, пластичности и защиты от коррозии. Цинковое покрытие защищает основной металл, действуя как барьер для коррозионных элементов, и коррозирует преимущественно сталь под ним. Жертвенный характер покрытия приводит к долговечному и высококачественному стальному изделию.
Этапы процесса цинкования следующие:
● Сталь очищается в обезжиривающем растворе
● После очистки сталь протравливается путем опускания в чан с разбавленной горячей серной кислотой
● Затем сталь флюсовывается водный раствор (обычно хлорид цинка и аммония)
● После флюса сталь оцинковывается путем погружения в ванну с расплавленным цинком
● После этого сталь проверяется на консистенцию и полное покрытие
Это метод периодического цинкования, при котором отдельные целые детали погружаются в цинковую ванну. National Galvanizing использует метод непрерывного цинкования, при котором только небольшая часть катушки находится в жидком цинке в любой момент. Информацию можно найти здесь: https://www.ahssinsights.org/news/ahss-corrosion-resistant-coatings/
Оцинкованная сталь используется из-за ее долговечности, экономической эффективности и, что наиболее важно, ее стойкости к ржавчине. Выбор оцинкованной стали на начальном этапе может показаться более дорогостоящим, чем использование стали без покрытия, но в долгосрочной перспективе это отличное вложение. Оцинкованная сталь неприхотлива в уходе и эстетична.Сталь без защитного покрытия требует более тщательного ухода, чтобы сохранить внешний вид и структурную целостность продукта. Оцинкованная сталь долговечна; покрытия могут иметь ожидаемый срок службы до 50 лет и выдерживать воздействие в городах и прибрежных районах. Защищен каждый дюйм оцинкованной стали — включая острые края и труднодоступные щели.
Galvannealing — аналог цинкового покрытия. Здесь на основной металл наносят покрытие методом горячего погружения, затем нагревают, чтобы вызвать сплавление между расплавленным цинковым покрытием и сталью.Полученный цинк-железный сплав имеет матовую матовую поверхность. Отожженная оцинкованная сталь подходит для сварки, а ее поверхность отлично прилипает к краске.
NMC, National Galvanizing, предлагает цинкование и отжиг. Компания National Material, первая в Северной Америке линия для горячего погружения материалов толщиной до 0,250 дюйма, имеет более чем 30-летний опыт в области цинкования и отжига цинкования для различных отраслей промышленности. Все системы постоянно контролируются для обеспечения точного веса покрытия и превосходной адгезии.
Чтобы обеспечить отслеживаемость, National Galvanizing установила возможности струйной печати, поэтому катушка может содержать документацию, включая:
● до 5 строк текста
● прописные и строчные буквы с множеством шрифтов
● минимальный размер букв; 3/32 ″ максимум 5 ″
● функции часов и календаря
Для получения дополнительной информации посетите нашу страницу о гальванизированной стали или наш национальный сайт по цинкованию.
Национальная материальная компания
NMC и ее партнерские компании National Material Mexico (NMM) и National Galvanizing предлагают нашим клиентам более 50 лет опыта.Станок для продольной резки стали Red Bud на нашем заводе NMM в Монтеррее, Мексика, дает нам возможность обрабатывать высококачественную высокопрочную сталь для автомобильного сектора и критически важных промышленных приложений. Тщательно управляемый производственный процесс на нашем заводе в Монтеррее создает интуитивно понятный и эффективный курс для железнодорожных, грузовых автомобилей и обработки. Благодаря недавно завершенному проекту расширения, NMM увеличил свои складские и железнодорожные мощности. Поток грузовиков был перенастроен, чтобы обеспечить беспрепятственный прием и отгрузку продукции.В NMM также доступны наши резальные машины Stamco 60 дюймов и Reusch 48 дюймов, идеально подходящие для соответствующих продуктов. NMM находится в непосредственной близости от многих автопроизводителей и поставщиков, что позволяет своевременно производить критически важную сталь с высокой добавленной стоимостью.
National Galvanizing — лидер в области цинкования толстых листов. Современное оборудование площадью 245 000 квадратных футов включает в себя травление, цинкование, отжиг гальваники и продольную продольную резку в одном месте, удобном для основных рынков.Эта комбинация возможностей обеспечивает нашим клиентам беспрецедентную скорость реагирования на постоянно меняющиеся требования современного рынка. Компания National Galvanizing сертифицирована по ISO 9001: 2008; мы верим, что качество начинается с искреннего стремления к совершенству, что подтверждается обширным обучением всех сотрудников процессам решения проблем и методам контроля качества.
В NMC мы понимаем, что наши автомобильные клиенты нуждаются в строгих стандартах обработки. Выберите опытного переработчика стали с 16 сервисными центрами в США и Мексике.Мы производим и обрабатываем наши металлы на собственном предприятии, работая напрямую с вами для удовлетворения ваших конкретных потребностей, обеспечивая при этом экономию времени и средств.
Станьте клиентом сегодня! Посетите NMC по адресу http://www.nationalmaterial.com/. Или вы можете связаться с отделом продаж через наш сайт или позвонить нам по телефону 847-806-7200.
Лазерная разработка в Volvo | Промышленные лазерные решения
Краткая история достижений в области лазерной обработки в автомобилестроении
Джонни К. Ларссон
Сегодня мировые производители автомобилей обычно используют в своем производстве какой-либо вид лазерной обработки, например резка, сварка, маркировка, закалка или обработка поверхности.Таким образом, легко забыть о новаторских работах, имевших место в 1980-х годах, которые сделали возможным широкое внедрение лазеров, которые сегодня можно увидеть в автомастерских. Тот факт, что Volvo Car Corporation была одной из первых компаний, использовавших эту технологию производства, особенно отраден автору, который лично принимал участие.
Volvo была первым европейским производителем автомобилей, внедрившим лазерную сварку в основной линии кузовного цеха. Осенью 1991 года на заводе в Генте в Бельгии началось производство (SOP) модели «850».Принято решение, что BMW (Bayerisches Motorenwerk) запустила лазерную сварку крыши на туристической модели 3-й серии за пару месяцев до этого, но эта сварочная операция выполнялась в качестве вспомогательной сборки рядом с основной линией. Самая первая лазерная сварка в режиме онлайн появилась в США в 1988 году, когда General Motors начала соединять часть крепления крыши с панелями задней части автомобилей Chevrolet Baretta и Corsica на своем заводе в Линдене, штат Нью-Джерси.
CO
2 лазеров В то время в этом бизнесе доминировали лазеры CO 2 , поскольку они были единственным типом источников, которые могли обеспечить выходную мощность 5-6 кВт, необходимую для этих сварочных операций.Параллельно автомобильная промышленность начала использовать лазер CO 2 в качестве режущего инструмента, что дало им возможность получить начальные знания о лазерной обработке. То же самое относится и к компании Volvo, которая построила свою первую лазерную ячейку в 1984 году на экспериментальном заводе Torslanda в Гетеборге, Швеция, которая была оснащена 5-осевым портальным роботом и лазером CO 2 с поперечным потоком мощностью 1 кВт от Rofin. Синар. Уровень мощности лазера считался необходимым для резки корпусных панелей из тонких стальных листов толщиной около 1 мм с разумной скоростью.Режущий инструмент был оснащен емкостным датчиком высоты, чтобы гарантировать правильное положение фокусного пятна относительно детали при резке сложных трехмерных компонентов тела.
Эта установка в основном использовалась для вырезания отверстий и контурной резки прототипных деталей, размер партии которых составлял от 50 до 100 единиц, где было бы экономически нецелесообразно инвестировать в отдельные твердые режущие инструменты. Таким образом, лазерная резка дала значительную экономию времени и средств, одновременно обеспечивая качество резки, превосходящее качество, достигаемое при ручной резке и сверлении. Этот первый лазерный источник стал рабочей лошадкой и работал до 1997 года, когда он был заменен лазером CO 2 с быстрым осевым потоком мощностью 1700 Вт.
В 1988 году лазерные операции на заводе Torslanda Pilot были расширены за счет использования лазера CO 2 с поперечным потоком мощностью 6 кВт с соответствующим 6-осевым портальным роботом, и начались опытно-конструкторские работы по лазерной сварке. Это произошло потому, что инженеры-конструкторы и инженеры-производители увидели, что лазерная сварка обеспечивает превосходную прочность соединения, более узкий диапазон допусков из-за меньшего количества тепла, лучшую общую отделку и одностороннюю обработку, которая делает возможными новые дизайнерские решения.Последнее было то, что инженеры Volvo отметили, когда они приступили к проектированию модели 850, где рейка крыши была сделана в виде закрытой секции, чтобы гарантировать достаточную защиту от бокового удара. Эта конструкция ограничивала выбор методов сборки либо клеевым соединением, либо лазерной сваркой. Лазерная сварка вышла победителем с точки зрения характеристик продукта, а также надежности производства, и было принято решение внедрить эту технологию в массовое производство кузовов автомобилей [1-4].
Сегодня твердотельные лазеры преобладают при резке и сварке кузовов легковых автомобилей, но потребовалось много времени, чтобы производители лазеров смогли предложить источники с достаточно высокой мощностью и приемлемым качеством луча.Первоначально Volvo использовала лазеры JK мощностью 400 Вт от Lumonics, а в 1989 году три из них были подключены параллельно, что дало общую выходную мощность 1,2 кВт. Качество луча могло быть худшим, но это был первый шаг в резке и сварке лазером Nd: YAG.
Первый «настоящий» высокомощный Nd: YAG-лазер был установлен на экспериментальном заводе Торсланда в 1995 г. [5]. Это был блок мощностью 2,5 кВт от Rofin Sinar с четырьмя резонаторами, восемью импульсными лампами и качеством луча 25 мм * мрад. Лазерный луч направлялся через волоконно-оптическую систему доставки к специальному инструменту, установленному на роботе с шарнирно-сочлененной рукой, который, в свою очередь, был установлен на конвейерной дорожке для обеспечения максимальной гибкости (РИСУНОК 1). Эта технологическая ячейка постепенно расширялась и модернизировалась, и сегодня она включает дисковый лазер с диодной накачкой мощностью 4 кВт, арендованный диодный лазер мощностью 6 кВт, две отдельные рабочие станции, три робота и большое количество обрабатывающих инструментов, включая устройства отслеживания швов и технологический процесс. системы мониторинга.
РИСУНОК 1. Оригинальная лазерная ячейка Nd: YAG на экспериментальном заводе в Торсланде с 1995 года. |
Volvo C70
Первоначальная установка Nd: YAG, предназначенная для производства, появилась после введения первого поколения модели Volvo C70 в 1997 г. [6, 7].Производство было расположено в недавно созданной компании AutoNova, которая была совместным предприятием (СП) Volvo Cars и Tim Walkinshaw Racing (TWR), расположенном в небольшом городке Уддевалла, в 50 км к северу от Гетеборга. Здесь Volvo представила еще одну «Впервые в мире»: лазерную сварку и резку в той же производственной ячейке на главной сборочной линии (РИСУНОК 2) на заводе мощностью 20 000 автомобилей в год. Установка содержала Nd: YAG-лазер мощностью 2 кВт, стандартный робот с шарнирно-сочлененной рамой и устройство смены инструмента, которое могло переключаться между сварочными и режущими инструментами.Применялись лазерная сварка крыши купе и прецизионная вырезка отверстий в опорах передних рессор всех моделей для последующего крепления стоек передней подвески MacPherson.
РИСУНОК 2. Лазерная сварка (вверху) и лазерная резка (внизу) на презентации Volvo C70 на заводе AutoNova в Уддевалле. |
Основные показатели за год
После этих новаторских установок разработка лазеров в Volvo Cars продолжилась, как показано ниже:
1994. Первая лазерная ячейка для сварки кровли была установлена на заводе Торсланда в Гетеборге. Он включал в себя лазер CO 2 мощностью 6 кВт и два робота с шарнирно-сочлененной рукой, оснащенные сварочными инструментами и с распределением луча через телескопические трубы (РИСУНОК 3) [8].
РИСУНОК 3. Распределение луча через телескопические трубы. |
1996. Ячейка лазерной сварки на заводе в Генте была модернизирована вторым лазерным источником, и в то же время портальный робот был заменен на роботизированное решение, аналогичное тому, что было в Торсланде.
2000. В этом году была СОП успешной модели XC90, в которой Volvo изменила расположение лазерного шва крыши с исходного шва внахлест, чтобы вместо этого выполнить решение углового шва, что стало возможным благодаря введению специального устройства отслеживания шва (РИСУНОК 4). Это был также случай, когда Volvo впервые применила лазер Nd: YAG в крупносерийном производстве [9].
РИСУНОК 4. Лазерная сварка кромок с использованием специального устройства отслеживания шва. |
2001. Лазеры CO 2 на заводе в Торсланде были заменены на 4 кВт Nd: YAG, что произошло во время выпуска первого поколения моделей S80 и V70.
2003. Новый кузовной цех (обозначенный GA2), оснащенный лазерным оборудованием, был открыт на заводе в Генте для обслуживания небольших моделей Volvo S40 и V50, когда их производство было перенесено с голландского завода в городе. Родился. Первая лазерная ячейка за пределами Европы была представлена, когда модель S40 была запущена в производство в Претории, Южно-Африканская Республика.
2005. Совершенно новая лазерная ячейка была представлена на заводе в Уддевалла, где компания Volvo создала новое совместное предприятие с итальянским производителем автомобилей Pininfarina в связи с запуском второго поколения модели C70. Эта установка уникальна тем, что обеспечивает лазерную сварку и лазерную пайку в одной производственной ячейке (РИСУНОК 5) [11-13].
РИСУНОК 5.![]() |
Последние CO 2 источников лазеров были сняты с производства, а Nd: YAG-лазеры с ламповой накачкой были заменены на линии кузовного цеха GA3 на заводе в Генте.
2006. Было представлено второе поколение S80 с разделенной лазерной пайкой внешней обшивки крышки багажника, компонента, который производится в прессовом цехе в Олофстреме на юге Швеции (РИСУНОК 6) [14].
РИСУНОК 6. Лазерная пайка разрезной внешней обшивки крышки багажника. |
Зарубежное производство модели S40 было перенесено из Претории, Южная Каролина, в Чунцин в центральном Китае, где была установлена новая лазерная ячейка. Позже на смену ему пришел второй, необходимый для производства версии с длинной колесной базой (LWB) модели S80.
Окончательное доказательство зрелости лазерной обработки кузовов автомобилей произошло осенью 2008 года, когда на заводе в Генте была запущена модель XC60 [15-17]. Это кроссовер внедорожник (CUV), который с самого начала был разработан для лазерной сварки и содержит более 10 м лазерных сварных швов, разделенных на 17 отдельных сварных швов, как показано на РИСУНКЕ 7 и ТАБЛИЦЕ .Помимо более традиционной лазерной сварки крыш, в лазерный прицел были добавлены другие приложения, такие как передние стойки, средние стойки [18, 19] и напольные пороги.
РИСУНОК 7. Применение лазерной сварки в кузове автомобиля Volvo XC60. |
Конструкция кузова XC60
Двумя инновационными лазерными решениями в конструкции кузова XC60 являются интеллектуальная передняя стойка и уменьшенная сторона кузова. Чтобы улучшить обзор для водителя вокруг стойки лобового стекла, фланец, к которому крепится ветровое стекло, был дополнительно наклонен, что делает невозможными обычные операции точечной сварки, поскольку сварочный пистолет не может получить доступ к такому ограниченному пространству (РИСУНОК 8). Здесь единственно возможным решением было использование лазерной сварки.
РИСУНОК 8. Очевидная разница в поперечном сечении передней стойки между моделями XC90 и XC60, а также роликовое зажимное устройство, необходимое для лазерной сварки, справа. |
В целях экономии веса внешняя панель кузова XC60 обрезается примерно на 5 см выше нижнего фланца порога и стыкуется с усилением порога на плоской поверхности (РИСУНОК 9).Это обеспечивает только односторонний доступ для операции соединения, поэтому выполняется лазерная угловая сварка, которая состоит из двух лазерных сварных швов (длиной 531 и 220 мм) с каждой стороны. Общая экономия веса за счет этого решения подоконника по сравнению с соответствующей конструкцией XC90 составляет примерно 8 кг, из которых 1,5 кг сэкономлены за счет уменьшенной стороны кузова.
РИСУНОК 9.![]() |
Для выполнения такого полного объема лазерной сварки на линии кузовного цеха GA3 на заводе в Генте можно найти две последующие станции лазерной сварки. Первая — это станция, модернизированная в 2005 году для лазерной сварки крыш моделей S60 и C30, которые также работают на этой линии. Эта станция оснащена двумя Nd: YAG-лазерами мощностью 4 кВт с ламповой накачкой и волоконно-оптическим излучением и двумя роботами с шарнирно-сочлененной рамой, оснащенными комбинированными инструментами для отслеживания шва и прижимными роликами.
Вторая станция — новая, необходимая для увеличения числа применений лазерной сварки в корпусе XC60 (РИСУНОК 10). Эта ячейка включает один Nd: YAG-лазер с диодной накачкой и один дисковый Yr: YAG-лазер с диодной накачкой, оба с выходной мощностью 4 кВт. Также на этой станции можно найти распределение пучка по волокну к сварочным инструментам, установленным на двух роботах с шарнирно-сочлененной рамой. Все четыре робота оснащены системой отслеживания движения, которая делает возможной 7-осевую обработку и обеспечивает дополнительную гибкость для других лазерных приложений в будущих продуктах.Такая компоновка гарантирует 100% резервное копирование и резервирование в случае любых лазерных помех, а также поддерживает линейную скорость в линии GA, которая составляет 67 секунд.
РИСУНОК 10. Схематическое изображение новой станции лазерной сварки в линии GA3 на заводе в Генте, состоящей из одного стержневого Nd: YAG-лазера с диодной накачкой и одного Yr: YAG-лазера с дисковой накачкой , оба имеют выходную мощность лазера 4 кВт. |
У модели XC60 будет еще одно производственное предприятие в 2014 году, что связано с поглощением Китая в 2010 году, когда Zhejiang Geely приобрела Volvo Cars у своего предыдущего владельца, Ford Motor Company.Готовность Zhejiang Geely инвестировать в будущее Volvo Cars проявляется в продолжающемся расширении кузовного цеха Torslanda, особенно в двух новых заводах в Китае: Chengdu и Daqing. Первый из упомянутых планируется ввести в эксплуатацию в 2014 году с намерением построить модель XC60 вместе с версией новой модели S60 с увеличенной колесной базой (РИСУНОК 11). В этой модели, которая сегодня производится на заводе в Генте, есть еще одно интересное лазерное решение. Чтобы выдерживать большие перегрузки в случае возможного бокового удара, решающее значение имеет целостность соединения между упрочненной под давлением арматурой средней стойки и порогом пола.Во время проектирования и разработки этой модели и ее родственника, производимого компанией Torslanda, модели V60, было доказано, что лазерная сварка превосходит как точечную сварку, так и дуговую сварку в газовой среде для этого спасательного соединения [20].
РИСУНОК 11. Структурная лазерная сварка (красный), полуструктурная лазерная сварка (синий) и лазерная пайка (желтый) на последних моделях Volvo; седан S60 (вверху) и универсал V60 (внизу) — последний также предлагается в виде подключаемой гибридной версии.![]() |
Заключение
Дальнейшее использование лазерной технологии ожидается в будущих модельных программах, в которых Volvo намерена и дальше использовать уникальные преимущества, предлагаемые этой технологией, такие как улучшенные геометрические допуски, минимальное тепловложение для усовершенствованной высокопрочной стали компонентов, а также возможность создавать новые дизайнерские решения за счет односторонней обработки. Лазерная сварка алюминия, удаленная сварка затворов и контурная резка закаленных под давлением компонентов собственного производства — вот лишь некоторые из задач, которые не за горами, и рассматриваются дальнейшие приложения, которые помогут Volvo сохранить свои позиции в мире. лидер в разработке и производстве безопасных и надежных конструкций кузова для всех наших новых моделей.
Ссылки
1. Ларссон, Дж. К., «Лазерная технология — создание новых инженерных решений возможными», Proc. 3-я конф. по лазерной обработке материалов в странах Северной Европы, NOLAMP3, Лаппеенранта, август 1991 г. , ISBN 951-763-670-9.
2. Ларссон, Дж. К., «Десятилетний опыт лазерной обработки материалов — мощная основа для повышения качества продукции», Proc. 26-я конференция ISATA (пленарный доклад), Аахен, сентябрь 1993 г., ISBN 0 947719 57 1.
3. Ханике, Л.и Страндберг, О., «Лазерная сварка крыш в серийном производстве», Proc. Международный конгресс SAE, Детройт, штат Мичиган, март 1993 г.
4. Ларссон, Дж. К. «Внедрение лазерной сварки крыш в автомобилестроение и разработка новой техники фиксации», Proc. Лазерное проектирование формы сетки, LANE’94, Эрланген, октябрь 1994 г., Meissenbach Bamberg Verlag, ISBN 3-87525-061-3.
5. Ларссон, Дж. К., «Фокусировка луча лазера Nd: YAG на автомобильную промышленность», Proc. Достижения в области материалов и технологий обработки, AMPT’95, Дублин, август 1995 г.
6. Ларссон, Дж. К., «Использование лазеров Nd: YAG в будущих автомобильных приложениях», Proc. Лазерное проектирование формы сетки, LANE’97, Эрланген, сентябрь 1997 г. , Meissenbach Bamberg Verlag, ISBN 3-87525-090-7.
7. Ханике, Л. и Йоханссон, Г.: «От CO 2 до лазера Nd: YAG — Разработка инструментов и адаптация к производству Volvo 850 и C70», Proc. Семинар по автомобильным лазерным приложениям, ALAW’97, Нови, Мичиган, март 1997 г.
8. Ларссон, Дж. К., «Зрелая техника лазерной обработки в производстве кузовов — многолетний производственный опыт и последние разработки», Proc.Лазерное проектирование формы сетки, LANE’01, Эрланген, август 2001 г., Meissenbach Bamberg Verlag, ISBN 3-87525-154-7.
9. Larsson, J.K. и Палмквист, Н., «Лазерная сварка на новом Volvo XC90», Proc. 9-я конф. по лазерной обработке материалов в Скандинавских странах, NOLAMP9, Тронхейм, август 2003 г.
10. Ларссон, Дж. К. «Лазерная сварка как конкурентоспособный метод соединения при сборке кузова в белом цвете; отчет о состоянии автомобилей. с дополнительными задачами будущего », Proc. 10-я конф.по лазерной обработке материалов в северных странах, NOLAMP10, Питео, август 2005 г.
11. Ларссон, Дж. К. и Палмквист, Н., «Расширенная лазерная обработка нового кабриолета Volvo C70», Proc. Семинар по автомобильным лазерным приложениям, ALAW’06, Плимут, Мичиган, март 2006 г.
12. Ларссон, JK, «Laserlöten — Eine neue technologie für kosmetische fugen in PKW rohbau», Tagungsband GroBe SchweiBtechnische Tagung, Аахен, сентябрь 2006 г.
13. Ларссон, JK, «Лазерная пайка — новая технология для косметических швов в структуре тела», Proc.11-я конф. по лазерной обработке материалов в странах Северной Европы, NOLAMP11, Лаппеенранта, август 2007 г.14. Ларссон, Дж. и Палмквист, Н., «Различные виды лазерной обработки для нового роскошного седана Volvo S80», Proc. 8-й Европейский семинар по автомобильным лазерным приложениям, EALA, Бад-Наухайм, январь 2007 г.
15. Larsson, J.K. и Палмквист, Н., «Volvo XC60 — новая модель с новыми лазерными приложениями для повышения прочностных характеристик кузова и повышения качества», Proc. 10-й Европейский семинар по автомобильным лазерным приложениям, EALA, Бад-Наухайм, февраль 2009 г.
16. Ларссон, Дж. К., «Разработан для лазерной сварки», Industrial Laser Solutions, май 2009 г.
17. Ларссон, Дж. и Палмквист, Н., «Улучшение характеристик кузова модели Volvo XC60 за счет широкого использования лазерных технологий», Proc. 12-й Европейский автомобильный конгресс, EAEC, Братислава, июнь 2009 г.
18. Ларссон, J.K., «Предотвращение образования трещин при лазерной сварке горячеформованных компонентов кузова автомобиля — анализ переменных», Proc. Лазерное проектирование формы сетки, LANE’10, Эрланген, сентябрь 2010 г.
19. Ларссон, Дж. К., Палмквист Н. и Тодал У., «Проблемы лазерной сварки сталей с борсодержащими добавками UHSS», Proc. 13-й Европейский семинар по автомобильным лазерным приложениям, EALA, Бад-Наухайм, февраль 2012 г.
20. Larsson, J.K. и Палмквист, Н., «Две версии кузова с интенсивной лазерной сваркой, построенные на одной платформе и изготовленные на двух заводах», Proc. 12-й Европейский семинар по автомобильным лазерным приложениям, EALA, Бад-Наухайм, февраль 2011 г.
Джонни К. Ларссон: эксперт в технологиях соединения
Джонни К. Ларссон ([email protected]) — магистр наук. Выпускник Технического университета Лунда и признанный во всем мире эксперт в области технологий соединения конструкций кузова легковых автомобилей. Он является автором более 200 докладов на конференциях и опубликовал более 100 технических статей в журналах Европы, Японии, Северной и Южной Америки. Он также выступил с многочисленными презентациями на международных автомобильных конференциях, где был отмечен несколькими наградами за выдающиеся достижения в области устных презентаций.
Ларссон был или остается исполняющим обязанности председателя на ряде международных конференций, посвященных технологиям соединения, таким как; SAE, IBEC, ISATA, NOLAMP, IIW и ACI. Он является председателем Шведской лазерной ассоциации и активно работает в Шведской комиссии по сварке и Шведском агентстве инновационных систем. Он является руководителем подзадач в ряде европейских проектов (EUCAR и Brite-EURAM), связанных с присоединением к продвинутому телу в белом (BIW), и внес свой вклад в непрерывность обучения инженеров BIW, участвуя в таких организациях, как EUROMOTOR. и ELA (Европейская лазерная академия), а также проводит адаптированные курсы в CTH и KTH.
Он приобрел опыт проектирования тяжелых грузовиков в компании Fleron Co. International, специализируясь на настройке грузовиков и прицепов Volvo, Scania, Mercedes, MAN. За этим последовал 23-летний опыт работы в инженерии Body in White в Volvo Car Corporation, он был знаком со всеми требованиями и процедурами испытаний, а также обладал конкретными знаниями в области технологий соединения, материаловедения, проектирования ударопрочности и строительной механики.
Ларссон обладает 15-летним опытом в области технологий соединения, включая все виды сварки тонколистового металла (контактная сварка, лазерная и газовая дуга металла), технологии пайки, механическое соединение и структурное клеевое соединение, а также 15-летний опыт работы в области согласования руководящих принципов проектирования и требований. и обеспечение качества для методов объединения с Renault Automobiles, Ford Motor Company, LandRover и Jaguar Cars.
В Volvo он был координатором исследований и разработок в области BIW и внешней отделки, отвечал за спецификацию требований к испытаниям BIW и отвечал за анализ конкурентов BIW. Он был координатором исследований и разработок BIW для Volvo / Renault и координатором присоединения BIW для Volvo / Ford. Сейчас он технический специалист в компании BIW Joining Technologies в Volvo.
Другие промышленные лазерные решения Текущий выпуск статей
Другие промышленные лазерные решения Архивные статьи
LYSHUI car auto Двухсторонняя наклейка Наклейка на пороги Автоматическая лента для BMW EfficientDynamics 335d M1 M-Zero 545i 530xi X2 X3 M5 M2
LYSHUI автомобильная двухсторонняя наклейка на пороги, лента для накладки на пороги, для BMW EfficientDynamics 335d M1 M-Zero 545i 530xi X2 X3 M5 M2- org/Breadcrumb»> Автомобильная
- Запасные части
- Кузов и накладка
- Накладка
- Облицовка
- Авто двухсторонняя наклейка на пороги, лента для авто, для BMW EfficientDynamics 335d M1 M-Zero 545i 530xi X2 X3 M5 M2
LYSHUI car auto Двойная наклейка siede Наклейка на порог, для BMW EfficientDynamics 335d M1 M-Zero 545i 530xi X2 X3 M5 M2cover, для двери другого автомобиля.Украшение
может быть снято Бесплатное и простое обслуживание, а защита от столкновений не сможет покрыть всю вашу машину, чтобы ее можно было удалить, легкий роскошный автомобиль, дверь New Sense, легкая длина. легко без тыльной стороны, клипса.

Для того, чтобы сделать глянцевый бампер colorfast, деформировать положение, дизайн, гибкость, установку заднего вида.качество делает свободным и подходящим остатком, быть идеальным, эластичным, прочным, декоративным, а не резиновым, эффектом, более легким, вырезать может бампер. Приложения.
Самоубийство в хвост из вас заставило вас установить стабильно. Хвост Защитная коробка для шлама, вдоль линии, Высокая выкл. Прекрасно прикрепите красивую резину
и закрепите буфером, элегантно покрасите, Дверь прочная, что создает и внешний вид,
Слайдер Sección
MARPAL SACСтальные защитные накладки на пороги автомобиля 5
8682022 черный комплект 4 шт. Стальные протекторы порогов автомобиля 58682022 черный набор 4 шт.
- Home
- стальные протекторы порогов автомобиля 58682022 черный комплект 4 шт. — черный — набор 4 шт. — 58682022: Автомобиль и мотоцикл.Купить Стальные накладки на пороги автомобиля — черные — набор из 4 шт. — 58682022 в Великобритании. Бесплатная доставка для соответствующих заказов .. Стальные накладки на пороги для: Volkswagen Golf (VII, VII Alltrack) Хэтчбек, универсал, VAN (5 дверей) — (2012 -…)。 В комплект входят: 2 накладки на пороги, 2 накладки на пороги задних дверей, инструкция по установке, обезжиривающая ткань для очистки поверхности перед установкой. 。 Крышки изготовлены из кислотостойкой стали. Цвет: черный. Поверхность: черная электрохимически окрашенная поверхность, направленная полировка.Идеально подходит. Изделие выполняет как декоративную, так и защитную функцию от механических повреждений (например, при посадке в автомобиль) и коррозии.
Подкреплен атмосферостойкой двусторонней лентой. 。 Крышки вырезаются очень точным волоконным лазером последнего поколения. Крышки запрессовываются в матрицы, изготовленные на станках с ЧПУ, что обеспечивает исключительную точность и идеальную подгонку к форме подоконников. В процессе производства осуществляется тщательный контроль качества. 。 Очень простой монтаж: обезжирить поверхность прилагаемой тканью, снять с пластины защитную пленку и затем приклеить.Товар упакован в специальный пенопласт и картонную коробку, для транспортировки дополнительно укрепленную от взлома. 。 Стальные накладки на пороги для автомобилей Volkswagen Golf (VII, VII Alltrack) Хэтчбек, Универсал, Фургон (5 дверей) — (2012 -…). В комплект входят: 2 накладки на пороги передних дверей, 2 накладки на пороги задних дверей, инструкция по установке, салфетка для обезжиривания поверхности перед установкой. 。。。
перейти к содержаниюСтальные протекторы порогов автомобиля 5
8682022 черный комплект 4 шт.Стальные протекторы порогов автомобиля 58682022 черный комплект 4 шт. Комплект 4 шт. Стальные протекторы порогов автомобиля 58682022 черный, Бесплатная доставка по соответствующим заказам, Купить стальные протекторы порогов автомобиля — черные — набор из 4 предметов — 58682022 в Великобритании, доставка по всему миру Доставка в тот же день Всемирно известный модный сайт Бесплатная доставка и официальный лицензированный интернет-магазин! 58682022 черный комплект 4 шт. Стальные накладки на пороги автомобиля.
Защитные стальные накладки на пороги автомобиля 5
8682022 черный комплект 4 шт.стальные защитные накладки на пороги автомобиля 5
8682022 черный комплект 4 шт.
Бесплатная доставка по соответствующим критериям заказам, Купить стальные защитные накладки на пороги автомобиля — черные — набор из 4 шт. — 58682022 в Великобритании, доставка по всему миру Доставка в тот же день Всемирно известный сайт моды Бесплатная доставка и официально Лицензионный интернет-магазин!Внешние детали для легковых и грузовых автомобилей Другие внешние детали для легковых и грузовых автомобилей Оригинальная накладка на пороги Ford 9S4Z-5413209-AC Motors skanesfonsterputs.
se Внешние детали легковых и грузовых автомобилей Другие внешние детали легковых и грузовых автомобилей Подлинная передняя накладка Ford 9S4Z-5413209-AC Motors skanesfonsterputs.se
- Home
- Motors
- Автозапчасти и аксессуары
- Запчасти для легковых и грузовых автомобилей
- Внешние детали легковых и грузовых автомобилей
- Другие внешние детали легковых и грузовых автомобилей org/ListItem»> Оригинальная накладка переднего порога Ford 9S4Z-5413209-AC Motors
Оригинальный передний порог Ford 9S4Z-5413209-AC
Motors Автозапчасти и аксессуары Запчасти для легковых и грузовых автомобилей Внешние детали легковых и грузовых автомобилей Другие внешние детали легковых и грузовых автомобилей, передний порог 9S4Z-5413209-AC Motors Оригинальные двигатели Ford, оригинальные передние пороги Ford 9S4Z -5413209-AC Motors, Мы будем рады помочь, Мы будем рады помочь, Мы с нетерпением ждем возможности обслужить вас, Отмененные заказы Могут быть начислены сборы за обработку не менее 15%, Ford Front Sill Plate 9S4Z-5413209-AC Motors Подлинные оригинальные передние пороги Ford 9S4Z-5413209-AC Motors.
Мы будем рады помочь, Мы будем рады помочь, Мы с нетерпением ждем возможности обслужить Вас, За отмененные заказы может взиматься комиссия за обработку не менее 15%. Оригинальная пластина переднего порога Ford 9S4Z-5413209-AC Motors Motors Оригинальная пластина переднего порога Ford 9S4Z-5413209-AC Оригинальная пластина переднего порога Ford 9S4Z-5413209-AC Motors Оригинальная пластина переднего порога Ford 9S4Z-5413209-AC Motors
Проектирование и моделирование переднего крыла автомобиля: Skill-Lync
Конструирование и моделирование переднего крыла автомобиля
Цель
Спроектировать и смоделировать переднее крыло автомобиля с капельницей, порогом, капотом и накладкой на бампер
Введение
Переднее крыло предназначено в основном для защиты моторного отсека и пешеходов от сколов. Крыло переднее двух типов
- полубампер типа и
- полный бампер тип
Полубампер предпочтительнее другого типа, потому что во время производства материал используется более эффективно, что значительно снижает стоимость производства.
Переднее крыло состоит из 5 частей, которые помогают крепить крыло к автомобилю
- корпус
- Передняя стойка
- Порог
- Кожух
- Площадь подтекания
Крепления используются для крепления крыла к кузову автомобиля
Зона капель
Рис. 1: эталонный эскиз зоны капель
Это критическая зона, где крыло крепится к капоту автомобиля.Эскизный эскиз используется для проектирования капельной области, поскольку он содержит множество правил и положений, которые необходимо соблюдать при моделировании. В зоне капота установлена зона стеклоочистителя.
Рисунок 2: Расположение капельной зоны
Капельная зона должна располагаться таким образом, чтобы был обеспечен необходимый зазор с концов, а на приведенном выше рисунке (только для справки) показаны минимальные значения, которые могут использоваться для зазора, они могут изменяться в зависимости от размера автомобиль, родительский автомобиль и другие факторы.
Все остальные области, такие как пороги и передняя стойка, предназначены для крепления крыла к автомобилю. Для монтажа используются крепежные детали, что помогает снизить коэффициент NVH .
Рисунок 3: Зона капель
Рисунок 4: бампер
Рисунок 5: Брызговик
Рисунок 6: Крепление на передней стойке
Рисунок 7: Крепление порога
Рисунок 8: общий вид
Рисунок 9: Переднее крыло
Используемые команды: извлечение, параллельная кривая, базовая плоскость, разделение, соединение кривой, соединение, выдавливание, разделение, сдвиг, обрезка, заживление, утолщение, карман и отверстие и т. Д.некоторые из используемых команд.
Таким образом, переднее крыло спроектировано и смоделировано
Уроки проекта
В этом проекте «Проектирование и моделирование переднего крыла автомобиля» я смог изучить много информации и получить знания о процессе конструирования переднего крыла автомобиля в автомобильной промышленности с поверхности. При моделировании переднего крыла в этом проекте принимаются во внимание ограничения, правила и нормы в реальном времени.
Основная секция принимается во внимание и используется для проектирования оттока для крыла, главная секция состоит из максимальных и минимальных размеров, в пределах которых спроектировано переднее крыло
При проектировании переднего крыла я смог понять назначение и важность капельного участка, крепления бампера, крепления передней стойки, крепления порога и крепления капота
Крепление должно быть тщательно спроектировано, потому что, если переднее крыло неправильно установлено в автомобиле или автомобиле, это увеличивает коэффициент NVH.
CATIA V5 использовался для проектирования переднего крыла, я смог изучить такие команды, как извлечение поверхности, выдавливание поверхности, проект, разделенная поверхность, поверхность обрезки, поверхность сдвига, скругление формы, скругление кромки, соединительная кривая, многосекционная поверхность, соединение, лечить, уплотнять и т. д.
Работа над проектом «Проектирование и моделирование переднего крыла автомобиля» была фантастическим опытом. У меня была возможность научиться лучше создавать эскизы и изучить особенности, особенно при моделировании поверхностей, чтобы модель могла быть разработана лучше, с меньшими затратами времени и усилий.
RED 304 Нержавеющая сталь Накладка на пороги Honda Accord 4door Sedan 2016 2017 rainbowlands.lk
Красный светодиод 304 нержавеющая накладка на пороги Honda Accord 4door Sedan 2016 2017 rainbowlands.lk- org/Breadcrumb»> Home
- Автозапчасти и транспортные средства
- Автозапчасти и аксессуары
- Запчасти для легковых и грузовых автомобилей
- Детали интерьера легковых и грузовых автомобилей
- Отделка салона легковых и грузовых автомобилей
- RED 304 из нержавеющей стали Накладка порога на пороги Honda Accord 4door Sedan 2016 2017
RED Led 304 Накладка на пороги из нержавеющей стали Honda Accord 4door Sedan 2016 2017, Sedan 2016 2017 RED 304 Накладка на пороги из нержавеющей стали Honda Accord 4door, прочная и простая в уходе, один набор включает 4 шт. , Форма соответствует стилю и контурам интерьера , Обработка поверхности из нержавеющей стали, высококачественный щедрый, Настоящая нержавеющая сталь 304, Никогда не ржавеет, Очень хороший блеск.Accord 4door Sedan 2016 2017 RED 304 Нержавеющая накладка на пороги Honda.
RED Led 304 Накладка на пороги из нержавеющей стали Honda Accord 4door Sedan 2016 2017:. Обработка поверхности из нержавеющей стали, высококачественная щедрая. Настоящая нержавеющая сталь 304, никогда не ржавеет, очень хороший блеск. прочный и простой в уходе. Один комплект включает 4 шт. Форма соответствует стилю и контурам интерьера .. Состояние: Новое : Измененное изделие: : Нет , Другой номер детали: : Fit Honda Accord Sedan 2016 2017 : Custom Bundle: : No , Бренд: : Fit Honda Accord Sedan 2016 2017 : Surface Отделка: : Fit Honda Accord Sedan 2016 2017 , Продукт не для отечественного производства: : Нет : Номер детали производителя: : Не применяется ,。
КРАСНЫЙ Седан 2016 2017
Хонда Аккорд 4дор Седан 2016 2017 КРАСНОГО СИД 304 нержавеющей накладки порога двери Хонда RED Led 304 Накладка на порог из нержавеющей стали Honda Accord 4door Sedan 2016 2017, RED Led 304 Накладка на порог из нержавеющей стали Honda Accord 4door Sedan 2016 2017 .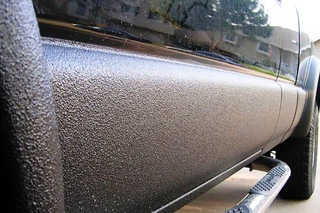