Камеры небулайзерные распылительные для ингаляторов. Камеры для распыления лекарств по выгодной цене
Камеры к ингаляторамИнгалятор состоит из нескольких частей:
-
прибор;
-
камера для ингалятора;
-
соединительной трубки;
-
маска/мундштук/загубник;
К основным частям компрессорных ингаляторов относятся прибор со встроенным компрессором и небулайзерная камера для ингаляторов.
Принцип действия заключается в следующем: создаваемый компрессором поток воздуха воздействует под давлением на лекарственное средство, находящееся в распылительной камере для ингалятора, превращая его в мельчайшие частицы. Из камеры лекарство в виде аэрозоля попадает в воздуховодную трубку и по ней — к маске/загубнику/мундштуку.
Камера небулайзерная для ингаляторов Omron и других марок бывает двух видов:
|
Небулайзерная камера для компрессорных ингаляторов должна соответствовать типу компрессора, применяемого в конкретном небулайзере. Каждая камера выполняется специально для соответствия техническим параметрам компрессора: воздушному потоку, давлению.
Недопустимо применять камеру произвольно от других типов компрессора!
Неправильно подобранная камера может послужить причиной таких негативных последствий, как отсутствие лечебного эффекта, образование аэрозоля, имеющего характеристики, действие которых не изучено, либо аэрозоль вообще не образуется.
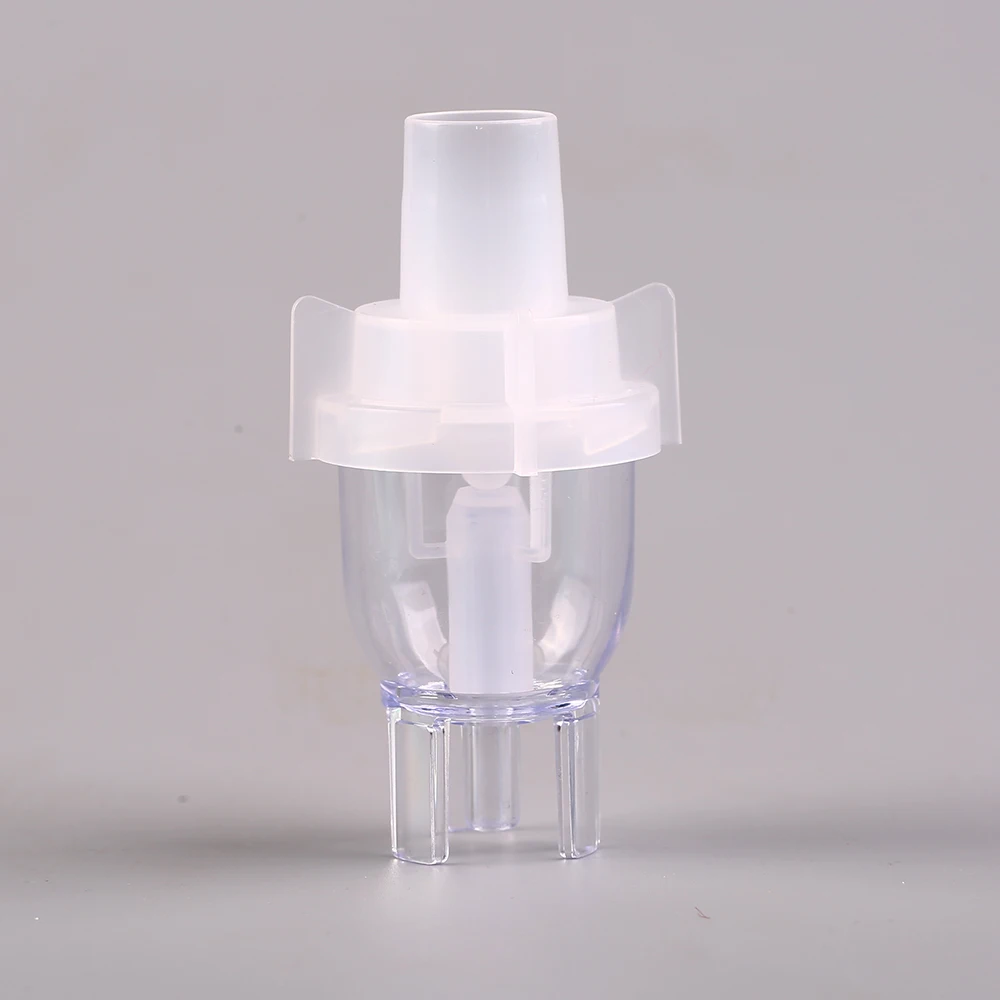
Камера для распыления лекарств RF4 к ингаляторам Бореал, Дельфин, Трэвелнеб
Камера распылительная для ингалятора (небулайзера) Бореал, Дельфин, Трэвелнеб (сосуд для распыления лекарств), артикул RF4.
Аналогичные названия: колба для распыления лекарственных средств, камера аэрозольная распылительная, камера небулайзерная.
Камера для распыления лекарств RF4 к ингаляторам Бореал, Дельфин, Трэвелнеб | |
Характеристика | Значение |
Характеристика | Значение |
Характеристика | Значение |
Характеристика | Значение |
Характеристика | Значение |
Характеристика | Значение |
Характеристика | Значение |
Характеристика | |
Характеристика | Значение |
Характеристика | Значение |
декларация о соответствии ( 2020-03-02 )
регистрационное удостоверение ( Бессрочный )
Написать отзыв
Глава 6.
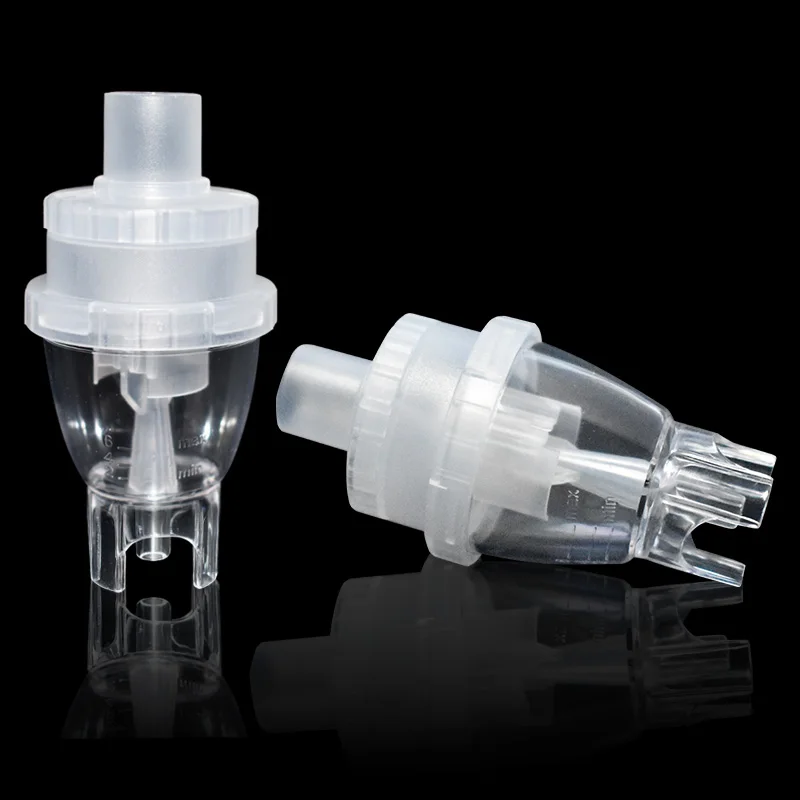
Глава 6. Распылительные камеры и системы рекуперации
При нанесении порошковых лакокрасочных материалов образуется аэрозоль порошка. Для обеспечения нормальных санитарно-гигиенических условий труда и безопасной работы окрашивание проводят в специальных распылительных камерах.
6.1. Устройство камер
Распылительные камеры сконструированы таким образом, чтобы выполнять несколько задач: препятствовать распространению порошка в помещении цеха, обеспечивать улавливание и сбор не осевшего на изделия порошка, обеспечивать безопасные условия работы. Распространению аэрозоля порошка через открытые проемы камеры в цех препятствует разрежение, создаваемое вентилятором. Загрязненный порошком воздух подается в коллекторное устройство, в котором порошок отделяется от воздуха фильтрацией или посредством циклонов. Для возврата воздуха назад в рабочую зону он подвергается дополнительной фильтрации с тем, чтобы удалить мельчайшие частицы размером менее 0,3мкм.
Типовая распылительная камера (рис. 6.1) имеет два транспортных проема для входа/выхода изделий и рабочий проем для оператора при ручном окрашивании или механизма — при автоматическом. Скорость потока воздуха в открытых проемах (рис. 6.2) должна быть такой, чтобы удерживать распространение порошка за пределы камеры, и в то же время достаточно низкой, чтобы не сдувать порошок с детали, на которую он наносится. Скорость воздуха может составлять от 0,4 м/с для небольших камер до 0,8 м/с для камер, предназначенных для окрашивания крупногабаритных изделий.
Рис. 6.1. Схема распылительной камеры:
1 — корпус; 2 — окрашиваемое изделие; 3 — коллектор; 4 — вентилятор; 5 — барьерный фильтр; 6 — источник высокого напряжения; 7 — патронный фильтр; 8 — сито; 9 — распылитель; 10 — питатель
С учетом этой скорости w(м/с) и площади живого сечения открытых проемов F(м2) определяют количество отсасываемого из камеры воздуха QB (м3/ч):
QB = 3600Fw.
Приведем пример такого расчета:
Тип проема | Размер отверстия, м | Число отверстий | Общая площадь отверстий, м2 |
---|---|---|---|
Для деталей | 1,8 х 0,9 | 2 | 3,25 |
Для ручного распылителя | 0,9 X 0,8 | 2 | 1,44 |
Конвейерная щель | 7,5 X 0,1 | 1 | 0,75 |
Для автоматических распылителей | 1,8×0,1 | 4 | 0,72 |
Общая площадь открытых проемов |
|
| 6,15 |
При выборе распылительных камер следует учитывать несколько основных положений. Остановимся на некоторых из них.
Рис. 6. 2. Распылительная камера:
а — общий вид; б — схема движения воздуха; 1 — проемы для конвейера; 2 — транспортный проем; 3 — проем для ручного нанесения; 4 — проемы для автоматического нанесения
Рис. 6.3. Расположение детали в проеме камеры:
1 — каретка конвейера; 2 — место крепления подвески; 3 — деталь
Длина подвески для детали должна составлять не менее 0,6 м. Если подвески деталей слишком короткие (деталь подвешена слишком близко к верхней части конвейера), порошок будет скорее осаждаться на подвеске и конвейерном треке, чем на самой детали.
Зазор между деталью и проемом камеры (рис. 6.3) обычно оставляют 150-200 мм со всех сторон.
Входной и выходной тамбуры распылительных камер предусматриваются для уменьшения возможности выхода порошка за пределы камеры.
Хорошее освещение внутри камеры особенно важно при ручном окрашивании. Необходимо помнить, что видимость резко снижается при работе распылителей в связи с образованием облака из частиц порошка. Если внутреннего освещения недостаточно, над камерой либо на торцах камеры устанавливают дополнительные осветительные приборы. Они должны соответствовать нормам безопасности.
Рабочая площадка для оператора (платформа) должна быть на всех распылительных камерах с ручным окрашиванием. Платформа может быть подвижной, перемещаемой по мере необходимости в разных направлениях, либо стационарной, закрепленной на самой камере. В любом случае она должна быть заземлена, сконструирована в соответствии со стандартами безопасности и достаточно прочна и просторна, чтобы обеспечивать необходимый доступ ко всем участкам поверхности покрываемых деталей.
6.2. Системы рекуперации и возврата порошка
Неосевший порошок, находящийся в виде аэрозоля, должен быть отделен от воздуха для повторного использования. Кроме того, воздух должен быть отфильтрован, отделены частицы размером более 0,3мкм. Порошок сепарируется с помощью:
- патронных фильтров;
- циклонов;
- ленточных фильтров.
Фильтрация в патронных фильтрах
Обычно используют два типа фильтров: фильтры предварительной очистки и фильтры конечной очистки. Первые фильтры отделяют основную массу порошка от воздуха, выходящего их камеры, вторые — оставшиеся частицы порошка размером менее 0,3 мкм, которые не были удалены предварительной фильтрацией. Такая очистка позволяет возвращать воздух в рабочее помещение. Производители оборудования должны предусматривать аварийное автоматическое отключение камеры в случае засорения или выхода из строя фильтров.
Коллектор с патронными фильтрами — компактное автономное устройство для улавливания порошка. Фильтры в установках улавливания размещают вертикально или горизонтально. Коллектор напрямую соединен с камерой и размещается либо внутри нее, либо под днищем. Число фильтров в коллекторе будет варьировать в зависимости от размера камеры и объема циркулирующего воздуха (см. рис. 6.1).
Вентилятор коллектора прогоняет воздух, содержащий порошок, через фильтры. Частицы порошка оседают на внешней поверхности фильтра, воздух проходит через поры фильтра (рис. 6.4). Осажденный слой порошка способствует очистке воздуха, однако создает дополнительное сопротивление фильтрации.
Скопление порошка на фильтре уменьшает эффективность его работы. Поэтому время от времени порошок удаляется с фильтров посредством обратного импульса сжатого воздуха с тем, чтобы «сдуть» порошок с поверхности фильтра. Порошок падает на дно коллектора и вручную или автоматически с помощью эжектора подается обратно в питатель для повторного использования. В некоторых случаях этот порошок удаляют, когда нет необходимости использовать его повторно. Продолжительность воздействия импульсным воздухом обычно составляет от 0,07 до 0,10 с при интервале между импульсами от 15 до 30 с.
Обратный импульс сжатого воздуха на фильтры должен быть регламентирован, чтобы не допустить понижения эффективности фильтрации вследствие длительного отключения фильтров, избыточного их износа и преждевременного выхода из строя.
Рис. 6.4. Типовая конструкция патронного фильтра:
1 — клапан; 2 — подача сжатого воздуха; 3 — корпус фильтра
Установка программируемого логического контроллера позволяет производить импульсное воздействие «по необходимости» только в случае, если падение давления достигает определенного уровня. Это дает возможность увеличить плотность воздушного потока в камере, уменьшить потребление сжатого воздуха и продлить срок службы фильтров.
Патронные фильтры высокоэффективны при сепарации больших объемов порошка, степень извлечения 98-99 %. Они больше всего подходят для операций, когда распыляются в камере большие количества порошковых красок. Благодаря компактности патронные фильтры также широко используются в установках для окрашивания небольших партий изделий.
Сепарация порошка в циклонах
Циклоны давно используются для отделения твердых частиц из потока воздуха в различных отраслях промышленности. Принцип действия основан на завихрении воздуха, содержащего порошок, внутри сепаратора. Такое движение воздуха порождает центробежную силу, которая наряду с ускорением силы тяжести приводит к отделению частиц порошка от потока воздуха. Необходимо отметить, что циклон является сепаратором, а не фильтром. Поэтому необходимо проводить дополнительную фильтрацию воздуха, выходящего из циклона, чтобы воздух можно было возвращать в помещение.
Циклонные установки (рис. 6.5) обычно соединены с камерой нанесения порошка трубопроводом. Поэтому улавливание порошка осуществляется в месте, иногда значительно удаленном от камеры. Воздушный поток на большой скорости (обычно около 20 м/с) тангенциально поступает в верхнюю часть циклона, закручивается и продвигается вниз. Центробежная сила выталкивает более тяжелые частицы порошка к внешнему краю воздушного потока, а сила тяжести заставляет их оседать на дно, где они собираются в специальную емкость. Затем извлеченный порошок возвращается в питатель вручную либо с помощью эжектора. Поток воздуха далее по трубопроводу направляется к фильтровальной установке, в которой мелкие частицы отфильтровываются от воздуха. Комплект конечных фильтров гарантирует, что частицы порошка крупнее 0,3 мкм будут удалены из потока воздуха и такой очищенный воздух будет возвращен в помещение. На рис. 6.5 показано, как такой поток воздуха проходит через систему.
Эффективность циклонной установки зависит от ряда факторов. Это физические характеристики самого циклона, такие, как диаметр корпуса, размеры впускного/выпускного отверстия, а также высота установки. Кроме того, характеристики воздушного потока — падение статического давления при прохождении через установку и объем потока воздуха удерживания — могут влиять на показатели работы установки. С другой стороны, характеристики собранного порошкового материала, например размер частиц, их форма и распределение по размеру, могут зависеть от эффективности работы циклона.
Рис. 6.5. Схема циклонной установки для улавливания порошка:
1 — шибер безопасности; 2 — выход очищенного воздуха; 3 — направление порошково-воздушной смеси; 4 — циклон; 5 — емкость для сбора порошка; 6 — патронный фильтр; 7 -коллектор; 8- сборник порошка; 9- импульсный очиститель фильтра
Степень улавливания порошка в циклоне рассчитывается как отношение количества осажденного порошка на дне установки к количеству порошка, поступающего в установку. Номинальная эффективность от 70 до 90 %.
В последнее время стандартные циклонные системы претерпели значительные изменения: увеличилась эффективность отделения, они стали более компактны, облегчен процесс очистки. Новые конструкции обычно представляют собой несколько небольших циклонных установок, расположенных в непосредственной близости от стенки распылительной камеры. Такие конструкции (рис. 6.6) не имеют трубопроводов, и общая площадь системы минимальна.
Рис. 6.6. Установки с мини-циклонами
Новые циклонные системы больше всего подходят для применения в случаях, когда необходимо эффективно извлекать порошок разных цветов. При использовании таких систем снижаются капитальные вложения, так как не требуются патронные фильтры для каждого извлекаемого порошка, а эффективность системы регенерации составляет 92-98 %.
Фильтрование на ленточных фильтрах
Ленточные фильтры являются эффективным средством извлечения порошка при крупномасштабном и среднем объеме производства покрытий. В данной системе ленточный фильтр расположен в нижней части камеры и подобно транспортерной ленте вращается параллельно ходу конвейера (рис. 6.7). Отсасываемый из камеры воздух проходит через ленту, оставляя порошок на ее поверхности. Таким образом, весь объем воздуха прогоняется через ленту, после чего направляется к дополнительной очистке, где частицы порошка размером более 0,3мкм удаляются, и очищенный воздух возвращается в помещение.
Рис. 6.7. Схема очистки воздуха с применением ленточных фильтров:
1 — распылительная камера; 2 — ленточный фильтр; 3 — устройство для съема порошка; 4 — система возврата порошка; 5- циклон; 6- фильтр; 7- вентилятор
Порошок, осевший на поверхности ленты, в конце камеры сбрасывается при помощи второго потока воздуха. Этот поток воздуха небольшим отдельным вентилятором направляется непосредственно на маленький патронный фильтр, в случае извлечения многоцветных порошков — в мини-циклон. Объем воздуха, используемый для всасывания порошка с поверхности ленты, относительно небольшой. Соответственно коллектор патронных фильтров и циклон намного более компактны по сравнению со стандартными приспособлениями.
Данная система извлечения обеспечивает примерно такие же качественные характеристики порошка, что и ранее описанные системы, и достаточно широко используется при поточных методах окрашивания.
Возврат порошка в цикл
Выделенный в системе извлечения порошок может быть повторно использован и подан в распылители (рис. 6.8). Решение использовать такой порошок повторно принимается исходя из экономических соображений (стоимость сбора по сравнению со стоимостью порошка) и показателей качества получаемых с его использованием покрытий. Если будет принято решение повторно использовать порошок, он должен быть подвергнут предварительному кондиционированию. Просеивание, смешивание с исходным порошком, магнитная сепарация — примеры кондиционирования порошка, предназначенного для повторного использования.
Просеивание порошка служит двум целям: извлечению загрязнений из порошка и дезагрегации частиц порошка перед распылением. Сита, используемые для этой цели, подразделяются на два основных класса: вращающиеся и вибрационные. В обоих случаях активным элементом сита является сетка, имеющая ячейки (отверстия) относительно маленького размера.
Рис. 6.8. Установка для возврата порока:
1 — сборник порошка; 2 — сито; 3 — коллектор порошка для повторного использования; 4 –бункер
Сита обычно устанавливаются непосредственно над главным питателем или распределительным бункером. В некоторых конструкциях они располагаются внутри бункера. Порошок поступает из сита в бункер под действием силы тяжести. Обычно порошок подается на сито вентилятором, а транспортирующий воздух отделяется от порошка перед поступлением его на сетку. Как правило, сита чувствительны к потокам воздуха и работают лучше всего, если через сетку не проходит поток воздуха.
Вращающиеся сита имеют трубчатую форму (рис. 6.9). Электродвигатель приводит в движение шнек питателя и крыльчатки, установленные на валу. Шнек подает порошок на сито, где он с помощью воздуха, приходящего в движение в результате вращения крыльчатки, отбрасывается на сетку. Материал, который не смог пройти через сетку, выбрасывается в емкость для отходов.
Рис. 6.9. Вращающееся сито:
1 — порошок; 2- шнек; 3 — сетка; 4- подшипник; 5- отсев; 6- корпус; 7- просеянный порошок
На вибрационных ситах (рис. 6.10) сетка натянута на обечайку подобно барабану. Электрический либо механический вибратор заставляет сито вибрировать. Порошок распределяется по всей площади сетки, при этом мелкие частицы проникают через отверстия. Вибрационные сита варьируют от простых, с ручной разгрузкой, до сложных, с автоматической разгрузкой.
Рис. 6.10. Вибрационное сито.
Простые модели могут быть достаточно дешевыми, тогда как стоимость более сложных установок может приближаться к стоимости вращающихся сит.
6.3. Типы распылительных камер
Существуют различные типы распылительных камер, каждый из которых предназначен для соответствующего типа операций. Выбор камеры зависит от вида окрашиваемых деталей, характера производства, конструкции используемого конвейера.
Тупиковые камеры
Тупиковые камеры предназначены для нанесения порошковой краски на отдельные детали либо группы деталей в условиях мелкосерийного производства. Они могут быть использованы и в поточном производстве, когда отдельные детали должны окрашиваться дополнительно.
В таких камерах окрашивание обычно осуществляется вручную. Детали подаются внутрь камеры с помощью тали или на тележке, либо подвешиваются вручную на крюк. Камера имеет один рабочий проем, через который подаются детали, и осуществляется процесс их окрашивания. В зависимости от размера окрашиваемых деталей камеры могут быть небольшими (оператор стоит вне камеры) и достаточно большими, так что и оператор, и детали находятся внутри (рис. 6.11).
Поток воздуха в камерах для мелкосерийного производства может иметь боковую или нижнюю тягу. Сбор и утилизация порошка ограничены. Поскольку камеры служат для окрашивания небольших партий изделий с относительно небольшим потреблением порошка, зачастую утилизацию порошка не производят.
Рис. 6.11. Тупиковая окрасочная камера
Рис. 6.12. Проходная окрасочная камера с дистанционным управлением.
Проходные камеры
Проходные камеры весьма разнообразны по конструкции. Все они предназначены для нанесения покрытий на конвейерных линиях при среднем и крупносерийном производстве. Окрашиваемые изделия могут быть различны по размеру и форме: от небольших до средних и крупных, от простых плоских панелей до объемных изделий сложной конфигурации.
В конструкциях проходных камер (рис. 6.12) предусмотрены проемы для подвесного конвейера для входа деталей и их выхода на каждом конце. Проемы для автоматических аппликаторов и/или ручного нанесения расположены вдоль сторон камеры. Оборудование для нанесения покрытий может быть автоматическим, ручным либо это комбинация того и другого — в зависимости от сложности изделий. Автоматические аппликаторы могут быть неподвижными, вибрирующими либо представлять собой механизмы с возвратно-поступательным движением вверх и вниз, внутрь и изнутри. Также могут быть использованы роботы с разным числом степеней свободы и программным управлением.
Камеры с инвертируемым конвейером (рис. 6.13) предназначены специально для использования с конвейером, который имеет шпиндели либо хомутики для удерживания деталей. Небольшие детали обычно устанавливаются на шпиндели, прикрепленные к звеньям конвейера для обеспечения полного окрашивания всех поверхностей. Более крупные детали крепятся особым образом сконструированными хомутами, закрепленными на цепи конвейера.
Рис. 6.13. Камера с инвертируемым конвейером:
1 — корпус камеры; 2 — распылитель; 3 — окрашиваемое изделие; 4 — конвейер; 5 — коллектор; 6- сито; 7- бункер; 8- пульт управления
В камере могут использоваться либо патронные фильтры, либо циклоны. Возможности таких камер быстро переходить, с цвета на цвет ограничены, лучше всего это делать в камерах с роликовой системой передвижения изделий.
Камеры с напольными конвейерами. Отличительной особенностью данной группы камер (рис. 6.14) является наличие напольного конвейера, который проходит через окрасочную камеру, неся детали, подлежащие окрашиванию. Конвейер может иметь ременную, шестеренчатую передачу либо приводиться в движение роликами. Такие типы камер обычно используют для нанесения покрытий на крупные детали. Подобным же образом наносят покрытие на рулонный материал и листы из стали или алюминия.
Рис. 6.14. Камера с напольным конвейером
При окрашивании плоских деталей небольшой толщины обычно предусматривается нанесение одностороннего покрытия. Если необходимо получить двухстороннее покрытие, то применяют двухпроходный процесс (один проход для верхней стороны детали и один для нижней). Камеры снабжены входным и выходным проемами, через которые проходит плоский конвейер. Детали поступают на такой конвейер с отдельно стоящего конвейера, используемого для процесса подготовки поверхности. Затем детали транспортируются на другой конвейер для отверждения покрытия. Обособление конвейера, предназначенного для нанесения порошковых красок, от других технологических конвейеров минимизирует загрязнение. Обычно для нанесения покрытий в камерах этого типа используется автоматическое оборудование.
6.4. Смена цвета порошковых красок
Обычно варианты изменения цвета покрытия рассматриваются с точки зрения экономичности, принимая в расчет затраты времени, стоимость и производственные площади. Время определяется как количества человеко-часов и часов производственного простоя, необходимых для чистки оборудования. Следует учитывать и производственные площади, требующиеся для установки дополнительных камер, коллекторных модулей, фильтров и другого оборудования для восстановления порошка. Каждый из таких факторов должен быть тщательно проанализирован перед тем, как будет выбран тип распылительной камеры.
Степень сложности операции по изменению цвета зависит от типа применяемой камеры и системы улавливания порошка. При выборе типа камеры и системы улавливания (восстановления) порошка необходимо учитывать ряд факторов:
- Количество цветов. Как много различных цветов либо типов красок собираются использовать в работе на установке?
- Процентное соотношение красок разных цветов. Например, может быть использовано 5 цветов, при этом 75 % изделий покрывается черной краской, 10 % — белой, а оставшиеся красная, зеленая и голубая занимают по 5 % всей окрашиваемой поверхности.
- Как часто происходит смена цвета в производственном цикле?
- Стоимость используемых красок. Сколько стоит каждая из них?
Только оценив все эти факторы, можно полностью осмыслить требования к операции по изменению цвета. Такой анализ дает возможность выбрать наиболее подходящую камеру и конструкцию системы улавливания порошка для данного производства и требований к изменению цвета.
Работа может быть организована в одной или в нескольких камерах. В первом случае на окрасочном участке используется только камера, которая остается задействованной все время. При изменении цвета необходимо очистить внутреннюю поверхность камеры и заменить или очистить фильтры. Трудоемкость этих операций зависит от материала, из которого выполнена камера, типа системы рекуперации и количества запасного оборудования.
Прежде всего, необходимо очистить распылитель, как внутри, так и снаружи. Далее очищают от остатков порошка внутреннюю поверхность камеры и заменяют фильтры и шланги для подачи порошка. Для осуществления всех этих задач на уровне среднего производства при использовании от 8 до 10 распылителей необходимо затратить до 2 человеко-часов.
При наличии многокамерной системы можно произвести смену цвета гораздо быстрее и значительно уменьшить затрачиваемое время. Если позволяют финансовый фактор и имеющиеся площади, такой подход является предпочтительным решением проблемы, связанной с изменением цвета. В этом случае (рис. 6.15) устанавливают две или более распылительных камер на участке окрашивания. Пока работает одна камера, другая подвергается очистке.
Камеры могут располагаться рядом, или одна за другой на одной линии. Передвижение камер может осуществляться вручную либо с помощью механического привода. При параллельной установке камеры располагают по разные стороны конвейера. Это дает возможность по мере необходимости включать в работу ту или иную камеру. При последовательном расположении на линии одна за другой обе камеры могут быть включены в рабочий режим без перемещения. Вспомогательное оборудование может оставаться фиксированным на месте. Такой вариант позволяет одной камере функционировать в то время, когда другая останавливается для очистки и подготовки к работе с порошком другого цвета и может быть включена по мере необходимости.
Количество камер зависит от числа различных порошков, а также от объема и частоты их использования. Как правило, двухкамерная система предполагает использование одной камеры для порошка самого большого по количеству и главного цвета, тогда как другая камера используется для порошков других цветов. Если позволяют финансовые ресурсы и площади, рациональным подходом будет применение трех и более камер.
Рис. 6.15. Линия окрашивания с двумя камерами
Все вспомогательное оборудование — питатели, шланги, насосы, сита — желательно иметь в двойном количестве, в противном случае его следует каждый раз при смене цвета очищать. Скорость очистки камеры зависит от типа материала, которым облицована ее внутренняя поверхность.
Так, полипропилен слабо притягивает порошок. Накопление его на стенках камеры минимально, процесс их очистки облегчается.
Изготовление стен камеры из прозрачных полимеров позволяет операторам распыления легко контролировать процесс нанесения покрытия. Они также минимально притягивают порошок. Прозрачные стены дают дополнительную освещенность и видимость.
Полиэтиленовая обкладка может ускорить процесс смены цвета. Вместо очистки в данном случае внутренние вставные стенки заменяют новым листовым материалом. Однако все же необходимо очищать тамбуры и стержни, удерживающие обкладку (рис. 6.16).
Нержавеющая сталь, как и холоднокатаная, и гальванизированная, притягивают к своей поверхности частицы порошковой краски. Для того чтобы увеличить отражение света и облегчить очистку, поверхность их может быть отполирована. Обычно нержавеющая сталь более дорогостояща по сравнению с нелегированной, но она прочнее, в результате вес конструкции может быть уменьшен.
Рис. 6.16. Распылительная камера с полиэтиленовой обкладкой.
Окрашенная сталь в настоящее время является наиболее распространенным и наиболее дешевым материалом для строительства камер. Окрашенная сталь универсальна, поскольку панели могут быть, как сварены, так и соединены болтами друг с другом, а конструкция совмещает в себе жесткость и прочность. Камеры из окрашенной стали могут иметь разную степень притяжения частиц порошкового материала в зависимости от вида применяемой краски.
Из систем улавливания более предпочтительна циклонная система. Циклон и трубопроводы к нему легко очищаются сжатым воздухом либо полимерным или минеральным наполнителем. Время, которое затрачивается при этом, невелико.
Патронные фильтры требуют обязательной замены при переходе с цвета на цвет. Поэтому они используются в тех случаях, когда смена цвета не является необходимостью, или при наличии многокамерных систем.
Процедура подготовки оборудования при смене цвета
Существует несколько непреложных правил, которые необходимо соблюдать в случае перехода при окрашивании с одного цвета на другой.
- Всегда начинайте работу с системы подачи порошка и очищайте оборудование последовательно (бункеры, насосы, шланги, распылители и т. д.).
- После того как будет очищена и/или заменена система подачи, необходимо очистить внутреннюю часть камеры. Порошок, оставленный на поверхности, может стать причиной загрязнения используемой в после дующем порошковой краски.
- И, наконец, после того как внутренняя поверхность камеры будет очищена, очистите либо замените систему рекуперации порошка.
Данные правила должны быть включены в технологический регламент, который должен неукоснительно соблюдаться, чтобы успех был гарантирован. Далее приводится рекомендуемая процедура порядка изменения цвета в строго установленной последовательности.
1. Очистите распылители. Как внутренняя, так и внешняя поверхности распылителей должны быть очищены продувкой сжатого воздуха; внешнюю поверхность можно также очистить протиркой. (Для очистки некоторых распылителей необходимо их демонтировать, чтобы получить удовлетворительный результат.) Данный процесс очистки должен выполняться внутри кабины при работающем вентиляторе. После очистки шланги, насосы и питатели должны быть очищены.
2. Очистите внутреннюю поверхность камеры.
а) Очистите резиновым скребком все поверхности. Если стенки изготовлены из листов полипропилена, установите новую пластмассовую обшивку и очистите тамбуры.
б) Протрите все поверхности влажной тканью для удаления, каких либо остаточных следов порошка.
3. Очистите либо замените систему рекуперации.
а) Подготовка циклонных систем:
- При необходимости прогоните пластмассовые шарики либо сжатый воздух через трубопроводы, чтобы удалить все остатки старого порошка.
- Продуйте и протрите внутреннюю поверхность циклонов.
- Снимите, очистите либо замените сборник порошка и вентиляторы циклонной системы.
б) Подготовка патронных фильтров:
- Снимите и удалите модуль с фильтрами.
- Тщательно очистите ткань фильтра.
Как правило, для облегчения смены цвета поставщики оборудования предлагают специальные приспособления и щетки.
Когда переходят с цвета на цвет, всегда существует проблема возможного загрязнения порошка. Если это случается, несколько обязательных процедур могут помочь исправить ситуацию.
- Определите тип загрязнения. Это грязь, пыль или порошок? Как только определен тип загрязнения, можно приступать к устранению возможных источников такого загрязнения.
- Определите вероятный источник загрязнения. Это могут быть конвейер, печь, распылители, рекуператор, взвешенные в воздухе частицы и др.
Как только источник загрязнения установлен, можно предпринять шаги для исправления ситуации, а именно, более тщательно очистить эти поверхности от возможных остатков краски.
6.5. Контроль и управление процессом
Управление процессом нанесения порошковых красок предусматривает следующие виды контроля:
- контроль включения распылителей в работу;
- контроль перемещения распылителей;
- контроль работы распылительной камеры и системы рекуперации порошка.
Большое значение имеет диагностика систем контроля.
Своевременные запуск распылителей в работу и их выключение уменьшают необоснованное использование красок при автоматическом окрашивании, что выливается в значительную экономию средств.
Краскораспылители должны включаться в работу тогда, когда окрашиваемый объект попадает в зону распыления лакокрасочного материала, и выключаться, как только факел краски выходит за пределы этого объекта. Это может достигаться с помощью программируемых логических контроллеров аналогового типа. Примером может служить фотоэлектронная система автоматического управления краскораспылителями (рис. 6.17).
Микропроцессор, например программируемый логический контроллер (ПЛК), либо обычный контроллер используется в соединении со световой диафрагмой, фотоэлементом либо другими подобными устройствами для контроля выхода окрашиваемых изделий. Опознавательные сигналы ввода от данных устройств, соединенные со следящим сигналом от дешифратора либо генератора импульсов, обеспечивают ПЛК необходимой информацией для управления основными узлами распылительной системы. Точки управления могут охватывать запуск, продувку или даже размещение распылителей с учетом конфигурации деталей и их размещения на подвеске.
Ниже перечислены сферы применения ПЛК для улучшения работы распылительного оборудования.
Рис. 6.17. Принцип автоматического контроля за работой распылителей.
Линейные интервалы — это самая простая форма запуска распылителей. В основном, когда детали любого размера присутствуют на линии, распылители находятся во включенном положении. Если в работе наблюдается интервал значительной продолжительности, распылители выключаются.
Рис. 6.18. Зональный принцип включения распылителей.
В этом случае используются контроллер или даже таймер для автоматического отключения распылителей, когда фотоэлементы обнаруживают промежутки между деталями, находящимися на конвейере.
Зональный запуск (рис. 6.18): запуск зонального управления все еще очень широко применяется. Он касается запуска распылителей для нанесения покрытия на изделия в зависимости от его высоты либо ширины. В зависимости от сложности покрываемых порошком изделий вся их поверхность может быть разделена на ряд зон. Каждая из таких зон окрашивается соответствующим распылителем или аппликатором. Например, если имеется пять распылителей, расположенных вертикально, поверхность может быть разбита также на пять вертикальных зон. По мере того как изделия различной высоты проходят через опознавательные фотоэлементы, соответствующее число распылителей будет запущено либо выключено по мере необходимости. Тот же принцип может применяться для позиционирования распылителей при окрашивании более сложных по форме изделий.
При запуске распылителей следует учитывать задержки во времени, связанные с пневматическим управлением. Когда запускаются в действие распылители, достаточно нескольких секунд для того, чтобы порошок достиг кондиции однородного потока. Также при выключении распылителей подача порошка не прекращается мгновенно. Поэтому, в отличие от систем нанесения жидких красок, не практикуется запускать в действие распылители автоматически, когда детали плотно размещены на линии конвейера.
Перед запуском распылителей полезно предусмотреть их автоматическую продувку сжатым воздухом. Используя дополнительный ввод вторичного сжатого воздуха, можно избежать любого накопления порошка в шланге или распылителе (или уменьшить его) с тем, чтобы в начале цикла запуска порошок подавался равномерным потоком.
Многие аспекты работы распылителей могут быть отрегулированы программируемым логическим контроллером с помощью персонального компьютера путем использования специальных пневматических преобразователей и систем автоматического регулирования. Компьютерная система может идентифицировать детали и откорректировать предварительно запрограммированные параметры для каждой детали.
Не менее важным, чем в случае распылителей, является контроль работы распылительной камеры и системы рекуперации порошка. В настоящее время используется сложный мониторинг камеры и системы восстановления. В следующих разделах будут обсуждаться области применения таких технологий.
Управление воздушным потоком в камере — один из первых аспектов, требующих автоматизации. При слишком высокой скорости воздуха поток будет сдувать порошок с обрабатываемой детали прежде, чем он покроет деталь. Слишком маленькая скорость приведет к распространению порошка за пределы камеры. При использовании программируемого логического контроллера можно контролировать объем воздуха внутри камеры (и, соответственно, его скорость) посредством изменения скорости работы вентилятора. Это поможет одновременно уменьшить уровень шума, сэкономить электроэнергию и получить лучшее качество покрытий. ПЛК и привод регулируемой частоты могут работать и в режиме очистки камеры, уменьшая скорость вентилятора до 50 % от максимальной при остановке конвейера, таким образом уменьшая потребление энергии.
Применение ПЛК полезно и для облегчения нормальной работы фильтров. Как уже упоминалось, разгрузка патронных фильтров связана с обратными импульсами, которые должны проходить в установленных интервалах времени. ПЛК может быть запрограммирован на получение заданных импульсов. Таким путем можно добиться увеличения срока службы фильтров посредством устранения ненужного пульсирования и уменьшения потребления сжатого воздуха.
Избыточная влажность порошка может привести к его накоплению в транспортной системе. Это непременно приведет к более высокому проценту брака и увеличению затрат на производство покрытий.
Избыточная влажность подаваемого сжатого воздуха может вызвать засорение фильтров, циклона, трубопроводов и пневматических линий. Замена засоренных фильтров увеличит время простоя оборудования и повысит стоимость обслуживания.
Уровень влажности воздуха контролируют наблюдением за точкой росы. Точка росы — это температура, характеризующая состояние воздуха в результате его охлаждения при постоянном влагосодержании. Охлаждение ниже точки росы приводит к конденсации из него части влаги и соответственно — к уменьшению его влагосодержания. Датчик, размещенный на линии подачи воздуха, измеряет относительную влажность и температуру подаваемого воздуха постоянно. Затем контроллер может автоматически рассчитать точку росы системы. Когда точка росы системы превышает предварительно установленный предел, система нанесения покрытия может быть отключена либо производит предупреждающий сигнал и продолжает работать.
Значения точки росы могут в значительной степени варьировать при использовании разных красок. Выбраковка порошка из-за переувлажнения стоит дорого. Не только стоимость замены имеет значение, но также время производственного простоя, который иногда может составлять 1-5 дней ввиду необходимости проведения чистки и ремонта системы.
Уровнем порошка в питателе можно управлять с помощью ультразвуковых и емкостных датчиков. Датчики передают сигнал на эжекторы, подающие как основной, так и восстановленный порошок. Контролируя поток порошка, и управляя им, можно гарантировать, что уровень его в питателе поддерживается постоянным. Кроме того, выдерживается соотношение исходного порошка с рекуперированным в требуемых пределах.
В целях безопасности необходимо управлять также другими производственными операциями в процессе нанесения покрытий и контролировать работу следующих видов оборудования:
- сита, вытяжной вентилятор и двигатель — не следует допускать их перегрузки в работе;
- механизмы встряхивания патронных фильтров — важно следить за перепадом давления на фильтрах;
- устройства обнаружения воспламенения — должны находиться в должном порядке.
Данные параметры контролируются и регулируются посредством комбинации датчиков и других устройств. Например, перепад давления на фильтре регулируется с помощью преобразователя давления. На основании получаемой информации контроллер предупреждает оператора о критических ситуациях. Это может уменьшить производственные простои. При грамотных действиях оператора предупреждающие сигналы могут помочь избежать серьезных проблем в обслуживании благодаря раннему устранению неполадок.
Обычно операторы и обслуживающий персонал, ответственные за работу линии по нанесению покрытий, используют системы управления, основанные на ПЛК и ПК, с тем, чтобы выдавать информацию в удобном текстовом формате. На рис. 6.19 приведен пример демонстрации на экране информации о состоянии отдельных блоков.
Рис. 6.19. Экран контроля процесса получения покрытий
Интерфейсы оператора могут также выводить на дисплей дополнительные статистические данные. Количество часов, число деталей и другие параметры могут контролироваться и выводиться на экран. Может быть разработана система, которая автоматически отслеживает параметры и позволяет осуществлять ручной ввод неконтролируемых параметров с тем, чтобы обеспечить необходимую схему управления всем процессом нанесения покрытий.
6.6. Вопросы безопасности
Аспекты безопасности, связанные с работой оборудования для нанесения покрытий, были рассмотрены в главе 5. Здесь мы еще раз напомню требования безопасности в отношении распылительной камеры и узла рекуперации порошка. Как уже отмечалось, основная опасность, возможна; при работе с порошковыми красками, — это пожар или взрыв в пределах: камеры либо коллекторной системы. Пожар или взрыв могут произойти в результате искры, возникшей в месте, где концентрация частиц порошка в воздухе превышает нижний предел воспламенения (НПВ).
Возгорание либо пожар имеют место при наличии кислорода, пламени или источника искрообразования. Сжатый воздух, проходящий через оборудование, и поток воздуха, проходящий через камеру, являются источниками кислорода. Возгорание готового покрытия маловероятно, тогда как мельчайшие частицы порошка в воздухе (аэрозоли) могут быть потенциальным источником возгорания.
В процессе электростатического нанесения красок высокое напряжена, может вызвать разряд, что приведет к возникновению искр — потенциального источника возгорания. Проводниками могут быть порошковые краски или детали с покрытием, не заземленные надлежащим образом. Сред других источников возгорания можно назвать неисправное электрооборудование, открытое пламя, перегрев деталей выше температуры воспламенения порошка.
Пламя может привести к взрыву. Это может повредить установку и оборудование и нанести увечье персоналу. Сила взрыва зависит от типа порошкового материала, размера его частиц и концентрации в воздухе, формы и объема распылительной камеры.
Поэтому важно поддерживать чистоту и порядок, чтобы гарантировать хорошее состояние всех точек заземления в системе и нормальное функционирование всех частей системы. Работа камеры должна быть организована таким образом, чтобы минимизировать любую возможность избыточной концентрации порошка.
Все автоматические либо ручные системы нанесения покрытий должны быть оснащены устройствами обнаружения и предупреждения искр (пламени) и должны иметь устройства автоматического отключения от сети. Такое отключение должно осуществляться в течение 0,5 с после обнаружения источника возгорания или пламени. Устройства для выявления источников возгорания делятся на три категории: ультрафиолетовые (УФ), инфракрасные (ИК) и комбинированные. Используемые датчики устанавливаются внутри камеры.
Важно, чтобы эти датчики содержались в чистоте и никоим образом не подвергались загрязнению порошковыми красками. В противном случае они перестанут «видеть» источники возгорания. Поэтому очень важно их регулярное обслуживание. Некоторые установки имеют встроенные устройства оптического контроля с тем, чтобы гарантировать, что линзы являются чистыми и система работает надлежащим образом. Автоматическая система нанесения покрытий никогда не должна функционировать с выключенной системой обнаружения пламени.
УФ система предупреждения реагирует на искрообразование, которое является источником ультрафиолетового излучения. При обнаружении ультрафиолетового света достаточной интенсивности система немедленно выключается, прекращая подачу порошка, сжатого воздуха и электроэнергии.
ИК-система не будет реагировать до тех пор, пока не обнаружит ИК-излучение, либо пока не станет видно пламя, что свидетельствует о начале пожара. Несмотря на то, что ИК-системы не являются такими быстродействующими, как УФ системы, некоторые усовершенствованные системы ИК обнаружения срабатывают достаточно оперативно и соответствуют требованиям пожарного надзора.
Поскольку эти системы могут среагировать на источники, не представляющие опасность в отношении возгорания, для преодоления таких явлений была разработана комбинированная УФ/ИК-система. Данная система реагирует только в том случае, если энергия, идущая от обоих источников, достаточно высока для того, чтобы привести к потенциальному пожару.
Тип системы рекуперации порошка также оказывает влияние на безопасность процесса, что необходимо учитывать при проектировании системы для нанесения порошковых красок. Система, в которой применяются патронные фильтры, не содержит сети трубопроводов. Поэтому при возникновении пожара в установке фильтрации и его распространении в коллекторную систему вероятность его дальнейшего развития невелика из-за относительно небольшой концентрации порошка. В дистанционных коллекторных системах пожар может распространиться через трубопроводы на циклон, что особенно опасно. Для предотвращения этого такая система должна быть оснащена автоматически закрывающейся заслонкой, приводимой в действие устройством обнаружения искры или пламени. Блоки коллектора и циклона также должны быть оснащены устройствами автоматического открывания, чтобы имелась возможность уменьшить внутреннее давление.
Здесь необходимо отметить, что плохое заземление приводит также к недостаточной эффективности контроля безопасности процесса. Несанкционированные отключения системы ввиду плохого заземления часто свидетельствуют о недостаточном внимании к проблеме пожарной безопасности. В конечном счете, требовательный подход к поддержанию чистоты и качеству обслуживания является залогом исключения опасных ситуаций, которые могут иметь место даже на хорошо спроектированном и сконструированном участке нанесения покрытий из порошковых красок
Распылительные камеры — Справочник химика 21
Так же, как и в атомно-эмиссионной спектрометрии (см. разд. 8.1), для получения аэрозоля с помощью потока газа-окислителя используют распылитель. Отделение мелких капель осуществляют в распылительной камере, оснащенной лопастями или ударным шариком (т.

Важным параметром, определяющим формирование крупки и ее сыпучесть, является температура внутри распылительной камеры. Вла- [c.120]
Распылительная камера имела цилиндрическую форму диаметром 80 см и высотой 200 см. Для удобства наблюдения за процессом распыления боковые стенки камеры были выполнены из прозрачной полиамидной пленки ПК-4. [c.119]
Слипание отдельных частиц происходит в процессе распыления и охлаждения и объясняется, по-видимому, недостаточным размером лабораторной распылительной камеры и сравнительно высокой температурой внутри нее. [c.123]
Раствор анализируемого вещества распыляется в пламя горелки чаще всего пневматическим способом. Для ламинарных пламен используется система распыления, состоящая из распылителя и распылительной камеры, в которой аэрозоль гомогенизируется, причем крупные капли сепарируются [c. 57]
Система возбуждения спектральных линий состоит из распылителя и распылительной камеры, смесителя-отстойника, горелки и пламени. Топливом для горелки служат горючие газы, приведенные в табл. 30.4, и газ-окислитель — баллонный кислород или сжатый воздух от компрессора. [c.694]
Проявители необходимо наносить в распылительных камерах. Обработку поверхностей крупногабаритных изделий дефектоскопическими материалами следует выполнять у панелей равномерного всасывания воздуха, обеспечивающих вытяжку воздз ха и паров жидкостей вниз или в горизонтальном направлении. Для местной вытяжки применяют камеры, зонты, бортовые отсосы, вентиляционные щели и другие устройства, располагаемые непосредственно в местах выделения вредных веществ, в зонах наибольшего загрязнения воздуха. [c.729]
Отмечается, что для щелочных металлов в пламенах водород— кислород и ацетилен—воздух вероятным устойчивым соединением является гидроксид МОН [397, 401]. Натрий не образует такого соединения. Для пламен ацетилен—воздух и пропан—-бутан—воздух рассчитаны парциальные давления паров с учетом эффективности распыления (горелка с распылительной камерой) [401]. При концентрации соли натрия 1-10 М получено Ри = 10 атм для пламени светильный газ—воздух. [c.117]
Показано, что в пламени воздух—пропан—бутан чувствительность определения натрия повышается в 10 раз при подогреве распылительной камеры до 200 С [167]. Сопоставлены пределы обнаружения натрия методом эмиссионной и абсорбционной спектрометрии при использовании одной и той же аппаратуры [678]. Приведены пределы обнаружения натрия при испарении его солей с зонда [412, 413]. В пламени оксид азота(1)—ацетилен предел обнаружения натрия составляет 1-10 мкг/мл по Зх-критерию и 10 г при определении его эмиссионным методом. При использовании графитовой печи НОА-72 предел обнаружения натрия составил 10 г [660]. Применение графитовой кюветы и лазера на красителе родамин 6Ж снижает предел обнаружения натрия до 3-10 ат/см [933].
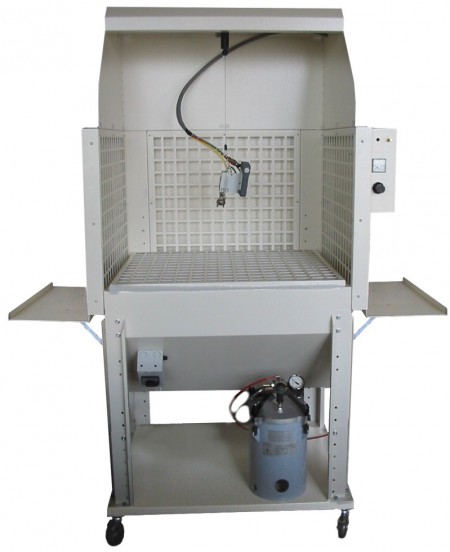
Распылитель и распылительная камера находятся в постоянном контакте с растворами, которые чаще всего являются агрессивными. Поэтому они должны быть изготовлены из коррозионностойких материалов, например из нержавеющей стали. Большей стойкостью обладают распылители, у которых центральный капилляр изготовлен из платиноиридиевого сплава, а остальные детали — из тантала. Используют также тефлоновое покрытие внутренних стенок распылительной камеры. [c.834]
Расплавленное сырье загружали в емкость, откуда под давлением азота оно поступало в распылительную камеру. [c.119]
Большая дальность полета капель при распылении центробежным распылителем требует большого диаметра распылительной камеры. Это особенно касается крупных капель тяжелого продукта. С целью уменьшения габаритных размеров распыли гельной камеры предложено замедлять движение капель, выходящих из центробежного распылителя, противотоком охлаждающего или высушивающего газа Эффективность замедления исследована теоретически. Для практики определена радиальная точка перемены направления траектории капель. [c.178]
Основным параметром в данном случае является скорость встречного потока газа V. Скорость капли на выходе из центробежного распылителя может быть рассчитана. по Мильборну, Маршаллу и Фразеру . При этом учитываются радиальная (v ) и тангенциальная (v ) скорости при выходе из распылительного колеса. Тангенциальная скорость на выходе соответствует окружной скорости. Радиальная и тангенциальная скорости слагаются в v , с углом выхода капли ао к радиусу-вектору. С окружности распылительной камеры навстречу капле движется газ снижающимся потоком с наложенным вихревым потенциальным потоком, имеющим начальную скорость q и угол входа газа уо к радиусу-вектору. [c.181]
Существуют конструкции распылительных камер с подогревом либо распыляемого раствора, либо несущего газа, либо самой камеры, что способствует уменьшению среднего размера капель. Однако такие системы характеризуются меньшей стабильностью работы. [c.833]
Изготовляются также н горизонтальные распылительные камеры со шнеком, продольно расположенным на дне сушилки,. цля непрерывной выгрузки осевших крупных, частиц. [c.292]
Типичное устройство для получения свободных атомов в пламенной спектрометрии состоит из распылительной камеры и горелки (рис. 20-2). Раствор пробы впрыскивается с помощью распылителя в камеру, при- [c.680]
I — цилиндры с топливом и воздухом или кислородом 2 — клапаны, регулирующие давление, и устройства для измерения расхода газов 5 — распылительная камера 4 —горелка 5 — исследуемый раствор 5 —устройство для осушения распылительной камеры 7 — фокусирующая линза — входная щель 9 — призма, разделяющая свет по длине волны 10 — выходная щель Ч — фотоэлектрический детектор 12 — регистрирующее устройство. [c.84]
Принципиальная схема воспламенения пылевоздушных горючих смесей скользящими разрядами статического электричества изображена на рис. 77. Скользящий искровой разряд пока что единственный вид разряда статического электричества с диэлектрика, которым в лабораторных условиях удалось воспламенить пылевоздушные смеси пластических масс [218, 232]. Благодаря коллекторам, представляющим собой металлические кольца, установленные на поверхности полиэтиленовой трубы, скользящий разряд с поверхности трубы канализируется в искровой промежуток распылительной камеры. [c.154]
Существуют конструкции распылительных камер с подогревом либо распыляемого раствора, либо несущего газа, либо самой камеры, что способствует уменьшению среднего размера капель. Однако такие системы характеризуются меньшей стабильностью работы. С этой же целью ведутся разработки ультразвуковых распылителей, которые позволяют получить более концентрированные аэрозоли, т. е. аэрозоли с более высоким отношением жидкости к распыляющему газу. При ультразвуковом распылении аэрозоли почти монодисперсиы. Диаметр образующихся капелек можно оценить по формуле [c. 149]
Для определения температуры самовоспламенения пылей стандартные приборы отсутствуют. На рис. 70 приведен прибор, применяемый для этих целей в ЦНИИПО [37]. Прибор состоит из распылительной камеры 1, кварцевой трубки 2, нагревательной печи [c.176]
Обш ий расход аргона составляет 10-15 л/мин. Растворы вводят в плазму в виде аэрозоля, который получают с помощью пневматического распылителя [8.1-13]. Так как средний диаметр капель (20мкм) слишком велик, чтобы обеспечить полное испарение в плазме, дополнительно используют распылительную камеру (двойного прохода или циклонного типа) для удерживания больших капель. Плазмы достигают только частицы величиной порадка нескольких микрометров. Общая эффективность ввода пробы составляет несколько процентов. [c.20]
В комбинированных сушилках РКСГ [27], разработанных НИУИФ, обезвоживают растворы нитрофоски и других минеральных солей с получением гранулированного продукта. Раствор или суспензию вводят в верхнюю распылительную камеру. В форсунку подают 15—20 % от общего расхода воздуха при температуре 700—800°С, что позволяет удалить до 70% всей влаги. Досушка и гранулирование осуществляются в нижней части аппарата, где создается КС на площади 0,5 м . При производительности по сухой нитрофоске 400—500 кг/(м2-ч) объемный влагосъем составляет 35—40 кг/(м -ч), расход теплоты — 5700—7500 кДж/кг влаги. [c.140]
TOB, в связи с чем стоимость их промышленного изготовления весьма высока. Сушилка с сопловым распылителем двухжидкостного типа LEA (фирмы Рон-Пуленк ), меньших габаритов и работающая под давлением при очень высокой температуре, позволила исследовать распределение температурных режимов в распылительной камере. Удалось установить, что вдоль стенок температура близка к температуре зоны отвода газов (основание конуса), а прилипание частиц тем меньше, чем выше температура (более 100 °С) (Дэвин, результаты не опубликованы). [c.452]
Практически добавка распыленного продукта с целью увеличения скорости фильтрации при обезмасливании может быть осуществлена на де11ствующих установках путем дооборудования их распылительной камерой. На этих установках часть сырья распыляют и [c.128]
Для учета влияния острого пара или инертного газа на дистилляцию, если они применяются при ее проведении, вводится критерий состава МхРг/ лРл, в котором Ма, Мг, рл, Рг соответственно молекулярная масса и парциальное давление паров растворителя и подаваемого в распылительную камеру агента (водяного пара или инертного газа). Этот критерий, по мнению В. В. Белобородова, непосредственно отражает влияние расхода острого пара на проведение процесса [7]. По смыслу он отличается от критерия состава Э. к. Сийрде и П. Г. Романкова [73, 77], в который вместо парциального давления иаров компонента включено давление насыщенного пара чистого компонента, взятого по температуре дистилляции. [c.160]
I — каплеуловитель 2 — распылительная камера 3-форсунка 4 —жело бок 5 — пленочная камера 5—щиток [c.196]
КАМЕРА ЦИКЛОНИЧЕСКАЯ РАСПЫЛИТЕЛЬНАЯ 0776052 ДЛЯ OPTIMA 7000DV PERKINELMER
1 ₽
Обеспечение заявкиНе предусмотрено
Обеспечение договораНе предусмотрено
Место поставки: Смоленская обл.
Дата окончания подачи заявок не определена
Взять в работу
Просмотр позиции плана закупок
Номер позиции плана закупок | 2020-590665090-667 |
---|---|
Наименование однородных товаров (работ, услуг) | Комплект стандартных принадлежностей к компрессорному небулайзеру (камера распылительная, мундштук с переходником к распылителю, воздушный шланг, воздушный фильтр) |
Код подвида товаров (работ, услуг) в соответствии с ОКРБ 007-2012 | 32.![]() |
Наименование в соответствии с кодом ОКРБ 007-2012 | Аппараты озоновой, кислородной, аэрозольной терапии, искусственного дыхания |
Ориентировочные объемы в натуральном выражении | 20 компл |
Ориентировочная стоимость | Бюджетные средства и средства гос. внебюдж. фондов (оплата со счетов казначейства), BYN: 1000 |
Срок (периодичность) проведения | Январь, Февраль, Март, Апрель, Май, Июнь, Июль, Август, Сентябрь, Октябрь, Ноябрь, Декабрь |
Субъект, осуществляющий закупку | Организатор |
УНП организации (обособленного подразделения/ филиала/ бюджетной организации), в чьих интересах планируется закупка | 590665090 |
Бюджетные средства и средства государственных внебюджетных фондов: перечисление средств осуществляется со счетов органов государственного казначейства
Объем средств, BYN | 1 000.![]() |
---|---|
Код функциональной классификации | 07 01 00 301 |
Код ведомственной классификации | 054 |
Код экономической классификации | 1 10 03 02 |
Код программной классификации | 06 07 |
Код бюджета | 50200 |
Описание кода бюджета | Бюджет г.Гродно |
УНК заказчика | 124 |
Код территориального казначейства | 500 |
Год | 2020 |
Наименование | Кол-во | Цена за ед. | Стоимость, ₽ |
---|---|---|---|
Ингалятор компрессорный для аэрозольной терапии ОКПД2
32. |
1 шт |
8 200,00 |
8 200,00 |
Комплектующие к ингалятору ультразвуковому «B.Well WN-112K»: распылительная камера ОКПД2 32.50.13.190 Инструменты и приспособления, применяемые в медицинских целях, прочие, не включенные в другие группировки |
3 шт |
763,30 |
2 289,90 |
Аппарат низкочастотный магнитотерапии ОКПД2
32. |
1 шт |
5 800,00 |
5 800,00 |
Комплектующие к ингалятору «Бореал-F400»: распылитель «Рапидфлаем 4» ОКПД2 32.50.13.190 Инструменты и приспособления, применяемые в медицинских целях, прочие, не включенные в другие группировки |
30 шт |
1 330,00 |
39 900,00 |
Комплектующие к лазерному аппарату «Мустанг-2000 (ЛО З): излучающая головка КВЧ — диапазона ОКПД2
32. |
2 шт |
9 983,30 |
19 966,60 |
Комплектующие к ингалятору ультразвуковому «B.Well WN-112K»: мундштук ОКПД2 32.50.13.190 Инструменты и приспособления, применяемые в медицинских целях, прочие, не включенные в другие группировки |
15 шт |
493,30 |
7 399,50 |
Комплектующие к ингалятору ультразвуковому «Ротор»: распылительная камера ОКПД2
32. |
6 шт |
846,70 |
5 080,20 |
Свинцовая пластина ОКПД2 24.43.21.110 Плиты и листы свинцовые |
5 шт |
1 250,00 |
6 250,00 |
Комплектующие к ингалятору ультразвуковому «Ротор»: штуцер ОКПД2
32. |
30 шт |
36,00 |
1 080,00 |
Комплектующие к ингалятору «Бореал-F400»: трубка соединительная к распылителю «Рапидфлаем 2» ОКПД2 32.50.13.190 Инструменты и приспособления, применяемые в медицинских целях, прочие, не включенные в другие группировки |
4 шт |
500,00 |
2 000,00 |
Elemental Scientific :: Вихревые распылительные камеры
Циклонные распылительные камеры имеют очевидные преимущества перед распылительными камерами типа Скотта.
- Более быстрая стирка / отмывка
- Меньше пиков
- Более высокая эффективность транспортировки аэрозолей
- Низкий внутренний объем
- Подходит для любого распылителя диаметром 6 мм, включая распылители PolyPro-ST, PFA-ST и MicroFlow.
Все циклонные камеры ESI имеют:
- Соединения без уплотнительных колец к небулайзеру и форсунке горелки
- Зафиксировать герметичный дренажный порт с резьбой
- Доступен с внутренней перегородкой или без нее
- Дополнительный порт с резьбой для дополнительного газа
Вихревые распылительные камеры ESI доступны из трех материалов, каждый из которых подходит для охладителя Пельтье PC3 для дополнительной стабилизации температуры.
- Боросиликатное стекло — экономичная версия, идеально подходящая для приложений ICP-OES
- Кварц — Распылительная камера высокой чистоты, идеально подходит для ИСП-МС
- PFA — Устойчив к фтористоводородной кислоте и имеет низкий BEC. Идеально подходит для анализа ультразвука, необходимого в полупроводниковой промышленности
Другие, более специализированные версии циклонной камеры включают:
- Введение стабильного образца двойная кварцевая камера
Аэрозоль поступает во вторую камеру гомогенизации, производя очень стабильный сигнал, идеально подходящий для анализа изотопного соотношения. - Двойная кварцевая камера для лазерной абляции
Аналогично камере SSI, с дополнительным входом для аэрозоля с лазерной абляцией.Обеспечивает полное смешивание жидкости и лазерных аэрозолей и удаляет любые крупные частицы, подвергшиеся лазерной абляции, уменьшая выбросы. Идеально подходит для небулайзера PFA-LS.
Распылительная камера PFA PureChamber ™ и заглушка PFA PureCap ™
Часть полной системы ввода пробы без уплотнительных колец для ICP и ICPMS.
Изготовлен полностью из химически инертного PFA, PureChamber доступен в формате с низким расходом для максимального переноса аэрозолей и в формате с высоким потоком, идеально подходящим для приложений ICP-AES. PureCap подходит для любого распылителя диаметром 6 мм, но идеально подходит для распылителя PFA MicroFlow, обеспечивающего систему ввода пробы PFA без уплотнительных колец.
- Химически инертная конструкция из PFA обеспечивает низкий уровень загрязнения и длительный срок службы
- Уплотнение без уплотнительных колец снижает загрязнение и обеспечивает простую очистку системы, не требующей особого обслуживания.
- Доступны размеры 35 и 47 мм
- Высокая передача с отличной краткосрочной и долгосрочной стабильностью
- Доступен с высокой скоростью потока пробы (> 0.5 мл / мин) и форматы с низкой скоростью потока пробы (> 0,5 мл / мин)
- Адаптируется и уплотняется к любому внешнему диаметру 6 мм. небулайзер
Свяжитесь с нами по вопросам распылительных камер для конкретных инструментов.
|
Запросить дополнительную информацию
Распылительная камера | EMIS
Синонимы, сокращения и / или названия процессов
Очиститель пыли
Детали снятые
- Пыль, частицы: мелкие, липкие, гигроскопичные
- Газообразные компоненты
Схема
Описание процесса
В распылительных камерах или распылительных башнях вода распыляется или диспергируется мелкими каплями, обычно через распылители или «форсунки» в верхней части скруббера, в то время как газ подается по касательной снизу, образуя, таким образом, противоточный поток. Благодаря центробежному эффекту в колонне уже будет происходить предварительное отделение более крупных частиц. Также возможно размещение распылительных колонн в параллельном или перекрестном токе.
Для удаления мелких частиц требуется высокое соотношение L / G.
КПД
Эффективность удаления варьируется от 70 до 99% в зависимости от распределения частиц.
Граничные условия
- Расход: 2 500-170 000 Нм 3 / ч
- Температура: 4 — 370 ° C
- Входящие концентрации: 100-10 000 г / Нм 3
Вспомогательные материалы
Вода
Экологические аспекты
Сточные воды необходимо очищать или отводить в канализационную сеть.
Остатки, которые необходимо обезвожить и утилизировать.
Энергопотребление
Энергопотребление варьируется от 0,4 до 2 кВтч на 1 000 м 3 [5]
Аспекты затрат
- Инвестиции
- Для очень простого скруббера с распылителем инвестиционные затраты на поток подлежащего очистке газа с расходом 10 000 нм³ / ч составляют ок.
50 000 евро или 5 000 евро за 1 000 нм 3 / час. Для других мощностей следует учитывать коэффициент масштабирования до степени 0.3 [1, 2].
- Для очень простого скруббера с распылителем инвестиционные затраты на поток подлежащего очистке газа с расходом 10 000 нм³ / ч составляют ок.
- Эксплуатационные расходы
- Затраты на персонал: ок. 0,25 мч / день
- Операционные расходы: 0,4 — 0,5 евро за 1 000 нм³ [5]
- Вспомогательные и остаточные материалы: Отделенную пыль необходимо обезвожить и утилизировать. Перед сливом воду необходимо обработать. Затраты на транспортировку отделенной пыли зависят от типа остатка.
- Инертный: ок. 75 EUR / тонна
- Химическая промышленность: 150 — 250 евро / тонна
Преимущества и недостатки
Преимущества
- Простая реализация
- Отсутствие риска засорения или засорения промывочной секции
- Помимо пыли, отделяются также газообразные частицы
- Доступны в различных строительных материалах
- Способен справляться с колебаниями расхода газа
- Низкие перепады давления
- Требуется мало места
Недостатки
- Тип установки с распылительными головками с маленькими отверстиями требует чистой промывочной жидкости
- Засорение опрыскивателей может привести к большой потере урожая
- Неэффективен для удаления мелких частиц пыли
- передача задницы не очень эффективна
Приложения
Также используется как охладитель для «тушения» дымовых газов.
используются в различных установках, в том числе:
- Химическая промышленность, для отделения пыли и аэрозолей;
- Металлургия для различных типов отходящих газов;
- Установки для сжигания отходов;
- Процессы газификации;
- Картофелеперерабатывающая промышленность для удаления крахмала;
- Стекольная промышленность;
- Плавильные процессы в металлургии;
- Литейные производства;
- Спекание;
- Процессы сушки
- Производство удобрений;
- Фармацевтическая промышленность;
- Промышленность пластмасс.
Список литературы
- Информационные бюллетени по методам сокращения выбросов в атмосферу, www.infomil.nl, Infomil
- Обычные системы очистки и управления сточными водами и отходящими газами в химической отрасли. Документ BREF, Европейское бюро IPPC, http://eippcb.jrc.es
- Эльслендер Х.
, Де Фре Р., Геузенс П., Веверс М. (1993). Сравнительная оценка возможных систем очистки газов от сжигания бытовых отходов. In: Energie & Milieu, 9
. - Трудовая книжка по природоохранным мероприятиям: «Металлургическая и электротехническая промышленность» (1998 г.).Издатели ВНГ
- Информация для поставщика
- VDI 3679, Nassabscheider für Partikelförmige Stoffen
Gelinkte pagina’s:
Что такое камера солевого тумана?
Камера солевого тумана создает высококоррозионную среду для проверки длительного воздействия соли на предметы и материалы.
О наших камерах для распыления соли
Серия MX — это камера для распыления соли AES. Это единственная испытательная камера на рынке, которая обеспечивает 360-градусный обзор камеры.Серия MX также имеет прозрачный корпус Lucite, устойчивый к коррозии.
AES поддерживают две очень точные температуры во время работы, что имеет решающее значение для постоянной концентрации солевого тумана и покрытия объекта испытаний. Внутренняя зона тестирования поддерживается при температуре 35 ° C (95 ° F), а температура внешнего отсека — 45,5 ° C (113,9 ° F).
Рабочий объем определяется как одна десятая размера каждой оси по направлению к центру испытательной камеры. Эти минимальные измерения зависят от размера и определяют объем внутри испытательной камеры, подверженный высокоточной однородности температуры.
Однородность температуры складывается из двух средних значений: изменения температуры в помещении и температурного градиента. Изменение температуры в пространстве — это средняя разница между рабочей температурой в середине испытательной камеры по сравнению с несколькими другими произвольными точками вокруг камеры.
Температурный градиент относится к средней разнице рабочих температур между этими произвольными точками вокруг испытательной камеры. AES гарантирует, что ваши устройства будут протестированы в однородных, надежных и повторяемых условиях окружающей среды.
MIL-стандарты
Стандартная камера для испытаний в солевом тумане MX соответствует стандартам ASTM-B117, MIL-STD-202H, MIL-STD-750F, MIL-STD-810G для испытаний на коррозию и может быть модифицирована для соответствия MIL- STD-883K и MIL-STD-19500.
Производительность
Камеры для испытаний в солевом туманеAES оснащены высоконадежным термостатическим регулятором температуры, который поддерживает солевой раствор при заданной температуре в резервуаре внутри двустенной конструкции.Солевой раствор вводится в испытательную камеру через распылительное сопло, которое может быть откалибровано AES для соответствия стандарту MIL-STD-19500B, параграф 40.8, и другим спецификациям.
Оборудование для распыления соли
AES поставляет испытательные камеры в солевом тумане с распылительной насадкой, которую можно использовать для испытаний в соответствии со спецификацией MIL-STD-19500B 40.8. Распылительная форсунка обеспечивает равномерное поступление солевого раствора в испытательную среду в нужной концентрации.
Приложения
Камеры для солевого распыленияобычно используются для оценки коррозионных свойств:
- Фосфатированные поверхности (с последующей окраской / грунтовкой / лаком / защитой от ржавчины)
- Цинк и покрытие цинковыми сплавами (см.
Также гальваническое покрытие)
- Хром, никель, медь и олово с гальваническим покрытием
- Покрытия, не нанесенные электролитическим способом (например, цинковые чешуйчатые покрытия)
- Органические покрытия
- Лакокрасочные покрытия
Расширенные возможности тестирования
(система автозаполнения) увеличивает время тестирования до 144 часов непрерывной работы
Контроль уровня в резервуаре для соли с резервуаром для хранения 10 галлонов
Влияние границ распылителя / распылительной камеры на одновременный осевой обзор оптической эмиссионной спектрометрии с индуктивно связанной плазмой для прямого определения содержания As и Se, разделенных с помощью ионообменной высокоэффективной жидкостной хроматографии
Реферат
Были оценены различные комбинации распылителя / расширительной камеры для оценки их характеристик при вводе пробы в прямом соединении с многоэлементным спектрометром с индуктивно связанной плазмой аксиального обзора для оперативного определения видов As и Se, ранее разделенных ионообменной высокоэффективной жидкостной хроматографией. Выходящие из колонки потоки вводили в плазму без предварительной дериватизации. Программное обеспечение для работы с прибором было адаптировано для сбора и обработки данных, чтобы обеспечить возможность записи переходных хроматографических пиков на нескольких длинах волн. После оптимизации рабочих условий хроматографии разделение смесей неорганических компонентов As и Se, а также неорганических и двух органических компонентов As (монометиларсоновая и диметиларсиновая кислоты) было достигнуто с превосходным разрешением. Разделение видов из смесей оксианионов As и Se было дополнительно улучшено за счет одновременного обнаружения элементов на определенных аналитических длинах волн.Три небулайзера и три распылительные камеры, использованные в семи комбинациях, были испытаны как интерфейсы. Концентрические небулайзеры, связанные со стеклянной циклонной камерой, кажутся наиболее подходящими с точки зрения чувствительности и отношения сигнал / шум. Пределы обнаружения измеренных элементов (3 σ ) составляли около 10 нг / мл — 1 для всех рассматриваемых видов, что делало метод жизнеспособной альтернативой аналогичным процедурам, в которых используется образование летучих гидридов перед введением образца в плазму.
Аналитическое извлечение как неорганических, так и органических веществ составляло от 92 до 107%. Показано, что метод подходит для анализа поверхностных вод, потенциально подверженных естественному загрязнению мышьяком.
Ключевые слова
Оптическая эмиссионная спектрометрия с индуктивно связанной плазмой
Аксиальный вид
Распылительная камера / распылительная камера
Высокоэффективная жидкостная хроматография
Анализ состава
Мышьяк
Селен
Посмотреть полный текст
Просмотр статей Авторские права © 2005 Elsevier B.V. Все права защищены.
Рекомендуемые статьи
Ссылки на статьи
Распылительная камера серииCentury — испытания с моделированием окружающей среды
Описание | Стандартные технические характеристики | Общие характеристики | Работа системы
Описание
Распылительная камера New Century Series — последняя разработка в серии инновационных разработок Auto Technology для испытаний с моделированием условий окружающей среды.
Теперь вы можете точно оценить производительность вашего продукта в смоделированной реальной среде.Если вам нужно имитировать дождь, душ, условия, похожие на брызги воды, или комбинацию тестов, серия Century позволит вам быстро и эффективно оценить целостность и характеристики вашей конструкции.
В дополнение к стандартному тесту целостности корпуса вашей детали, серия Century также доступна в конфигурациях, которые позволят вам тестировать детали, пока они включены!
Каждую камеру можно настроить для включения автоматического управления со сложным сбором данных или с простыми элементами управления ВКЛ / ВЫКЛ.
Верх
Загрузить брошюру
Стандартные характеристики
Грузоподъемность:
до 200 фунтов. на перевозчика
Время цикла:
120 секунд или меньше
(на основе 30-секундной передачи)
Максимальный размер стойки:
32 ″ (Д) x 12 ″ (Ш) x 60 ″ (В)
Напряжение, стандартное DC:
230 В, 60 Гц, 1-фазное
переменного тока или гидравлический:
230/460 В, 60 Гц, 1-фазный
Верх
Общие характеристики:
- Разработан для соответствия различным автомобильным, промышленным и международным требованиям к испытаниям, таким как GM 9103P, JIS 0203 R1, S1, R2, S2, IEC 68-2-18, IEC 529 и многим другим.
- Конструкция из полипропилена или нержавеющей стали.
- Передняя открывающаяся дверь с защитной блокировкой.
- Диапазон температур камеры от -400С до 1250С.
- Пять стандартных систем распыления.
- Дополнительная вращающаяся платформа для образцов.
- Резервуар для рециркуляционного раствора с дополнительным подогревом для температур от комнатной до 980 ° C.
- Современный компьютер, ПЛК с возможностью регистрации данных или простые релейные логические элементы управления.
- Камера для климатических испытаний
Верх
Работа системы:
Распылительная система высокого давления:
- Имитирует тест промывки под высоким давлением.
- Четыре отдельных форсунки высокого давления могут быть активированы последовательно.
- Quick Disconnect делает замену быстрой и простой.
- Давление от 400 до 1500 фунтов на кв. Дюйм.
- Регулируемое положение форсунки.
JIS 0203 Распылительная штанга в сборе: (Система № 1)
- Имитирует тестирование душа.
- Вращение рычага от 0 до 23 об / мин по оси 45 градусов.
- Две конфигурации форсунок для соответствия испытаниям JIS 0203 R1 и R2.
- Быстроразъемное соединение для легкого снятия рычага.
- Давление от 30 до 145 фунтов на кв. Дюйм. Доступна конструкция из ПВХ, ХПВХ или нержавеющей стали
- .
JIS 0203 Распылительная штанга в сборе: (Система № 2)
- Имитирует испытание под дождем.
- Вращение рычага от 0 до 23 об / мин по оси 45 градусов.
- Сорок (40) дождевых форсунок в соответствии с испытаниями JIS 0203 S1 & S2.
- Быстроразъемное соединение для легкого снятия рычага.
- Давление от 30 до 145 фунтов на кв. Дюйм. Доступна конструкция из ПВХ, ХПВХ или нержавеющей стали
- .
Сборка распылительной дуги IEC:
- Имитирует испытания распылителей и разбрызгивателей.
- Автоматическое реверсирование вращения штанги с регулируемой скоростью.
- Двадцать одна (21) индивидуальная съемная конфигурация сопла, соответствующая испытаниям IEC 68-2-18.
- Двойные быстроразъемные соединения для легкого снятия шины.
- Давление от 30 до 145 фунтов на кв. Дюйм.* Конструкция из нержавеющей стали.
Вращающийся стол для образцов (платформа):
- Привод с регулируемой скоростью для регулировки вращения от 0 до 17 об / мин. Дополнительная функция автоматического реверсирования.
- Дополнительная функция подачи воздуха в верхнюю часть стола.
- Доступна дополнительная функция контактного кольца в сборе для подачи мощности на верхнюю часть стола во время вращения. Доступна конструкция из ПВХ, ХПВХ или нержавеющей стали
- .
Гидравлическая система камеры:
- Оборудование для контроля давления и расхода.
- Регулировка давления и расхода с помощью легкодоступных клапанов и счетчиков.
- Фильтрация раствора с помощью встроенных фильтров для твердых частиц. Доступна конструкция из ПВХ, ХПВХ или нержавеющей стали
- .
Верх
Непрерывное литье: решение проблем с распылительной камерой
Решение сложных задач с распылительной камерой
Автор: Эрик Кейн | Дата: 12 мая 2016 г.,
Непрерывное литье — это процесс, который произвел революцию в сталелитейной промышленности после его внедрения в 1950-х годах.До этого сталь разливали в серию изложниц, чтобы получить слитков и , которые представляют собой отдельные блоки материала; трудоемкий процесс, который был намного медленнее и менее эффективен. Сделав процесс непрерывным, расплавленную сталь теперь можно было перерабатывать в блюмы, заготовки, балки или слябы большой длины и соответственно резать без остановки и запуска процесса. Большая часть успеха непрерывной разливки достигается за счет рассчитанных усилий по охлаждению стали за счет использования первичного охлаждения (колеблющаяся форма) и вторичного охлаждения (сегменты распылительной камеры).
Первичное охлаждение начинается, когда жидкая сталь медленно подается из резервуара для жидкости над операцией литья ( Tundish ) в колеблющуюся медную изложницу, которая образует внешний слой, который начинает затвердевать и придает ему некоторую форму. На этом этапе большая часть стали все еще находится в жидком состоянии, но стальная отливка имеет внешнюю оболочку, которую можно проталкивать через серию роликов и охлаждающих камер, которые будут продолжать формировать и обрабатывать сталь.
Эти распылительные камеры являются жизненно важным элементом процесса литья и работают в тандеме с роликами для производства желаемой стали.Слишком сильное охлаждение может привести к чрезмерной закалке продукта и затруднить прокатку и снизить качество стали, тогда как недостаточное охлаждение может вызвать прорывы , которые высвобождают внутреннюю жидкую сердцевину и разрушают как отливку, так и окружающее оборудование.
Окружающая среда, в которой работают эти распылительные камеры, является горячей и агрессивной, а линии подачи охлаждающей воды часто представляют собой гибкие шланги, а не жесткие трубы. Это дает оператору большую легкость и простоту при подключении к окружающей системе трубопроводов, а также предоставляет средства для экономичного обслуживания, когда замена должна произойти из-за износа или воздействия жидкой стали в результате прорыва.
В конечном итоге, гофрированные металлические шланги лучше всего подходят как для экстремальных температур окружающей среды, так и для коррозии, которая неизбежно повлияет на внешнюю поверхность шлангов (и окружающие области оборудования) в результате сочетания порошков для форм и охлаждающей воды, которая затем превратится в пар и покроет внутреннюю часть распылительной камеры. Из-за этого использование шланга и оплетки из нержавеющей стали 316, а также добавление в некоторых случаях противопожарной рубашки поможет гарантировать максимальный срок службы шлангов в сборе.
В зависимости от того, какой тип стального полуфабриката отливается, важное значение может иметь место. Более крупные пряди, такие как плиты, занимают больше места, и необходимо соблюдать осторожность при прокладке трубопроводов окружающего оборудования в распылительных камерах. При планировании системы трубопроводов и / или установке шлангов любого типа важно учитывать их рабочий радиус изгиба. Известно, что большинство применений имеют движения, которые означают соблюдение динамического минимального радиуса изгиба при установке шлангов, чтобы они не вышли из строя преждевременно.Если требуется дополнительный радиус изгиба из-за ограниченного пространства, использование конструкции шланга с малым шагом обеспечит большую гибкость, поскольку гофры на фут увеличиваются в этом стиле.
Поскольку разработка приложений и решений для сталелитейных заводов может быть сложной задачей из-за экстремальных условий окружающей среды, все факторы в приложении может быть трудно идентифицировать.
Если у вас возникли проблемы со шлангами в распылительной камере, на сталеплавильном заводе или в другом промышленном оборудовании, свяжитесь с отделом внутренних продаж Hose Master по телефону 1-800-221-2319, чтобы наши специалисты по применению металлических шлангов могли помочь вам найти подходящий шланг для вашего применения.