Сырая резина в баллончике
Жидкая резина для авто: плюсы и минусы
Стандартная краска для покрытия авто используется сейчас реже. Больше в моду входят альтернативные способы покраски, а именно винил. И это не только пленка, которая встречается на каждой десятой машине в городе. Современным словом является жидкая резина. Это новый виниловый материал, обладающий защитным свойством. Для чего нужна жидкая резина на авто и как правильно ее наносить?
Что такое жидкая резина?
Прежде всего, стоит разобраться, что такое жидкая резина. Многие любители хотят изменить свой автомобиль, но не перекрашивая его кардинально. Для этого придумали винил и другие способы быстрого перевоплощения. Одним из таких является краска жидкая резина. Речь идет именно о краске, сделанной на основе резины. Такая структура позволяет легко наносить ее на поверхность, а также с легкостью снимать, при потребности.
Жидкая резина для автомобиля
Подобный вид покрытия используют в качестве защиты, быстрого изменения стиля и цвета авто. Резина в составе обеспечивает долгосрочность эксплуатации по сравнению с пленкой. Используется краска резиновая для авто при полном перекрашивании и изменении некоторых частей.
В зависимости от метода нанесения покупать следует в аэрозолях и канистрах. Цена колеблется, что обусловлено производителем и качеством.
Цвета, которые предлагает жидкий винил, не представляют обширный спектр, существует 6 популярных разновидностей:
- Неон (преимущество необычно яркий цвет).
- Металлик (безупречный стиль).
- Хамелеон (цветовая гамма меняется в зависимости от кута зрения).
- Перламутр (блеск и игра цветов).
- Прозрачный (покрытие не скрывает фабричный цвет авто).
- Термальный (цвет изменяется в зависимости от температурного режима).
Жидкая резина для авто: плюсы и минусы покраски автомобиля веществом
Безусловно, главный плюс покрытия автомобиля жидкой краской – защитный эффект. Винил значительно уступает, жидкая пленка для авто не только скрывает некоторые дефекты, но и предотвращает образование трещин, царапин и других повреждений.
Главный плюс покрытия автомобиля жидкой краской – защитный эффект
В число безусловных преимуществ входят следующие свойства:
- Создает защитный слой, лакокрасочное покрытие остается целым.
- Имеет несколько текстурных решений, создает матовый или глянцевый эффект.
- Применим на весь кузов либо на отдельные части.
- Высокая водонепроницаемость и эластичность.
- Проявляет стойкость к воздействию ультрафиолета.
- Придает автомобилю безупречный стиль и статус.
- Покраска с помощью жидкого винила применяется на труднодоступные места. Например, покрышка после покраски будет выглядеть как новая.
- Нет необходимости в дополнительных требованиях, полная технология намного проще.
Имеются также недостатки. Главный минус – срок службы максимум 2 года, первые признаки изношенности появляются через год. Кроме того, резиновый слой может оставлять липкие следы, снять его можно только с помощью полировки. Еще один недостаток или скорее особенность –однотонность цвета.
Главный минус – срок службы максимум 2 года, первые признаки изношенности появляются через год
Технология покрытия кузова машины жидкой резиной
Полный процесс покраски длится несколько часов, затем сутки сушки. Все зависит от того, куда применяется жидкая резина, авто все будет покрыто или только его части. Технология не имеет сложностей и состоит из нескольких этапов:
- Подготовка авто. Говориться о мойке, чистке и грунтовке, при необходимости. Стоит понимать, что полное покрытие резиной полностью скрывает все дефекты.
- Скрытие элементов, которые краситься не будут. Их надо снять или заклеить с помощью скотча.
- Нанесение резины. Как долго это будет, все зависит от способа нанесения.
- Сушка. Требуется не менее суток. До этого времени машиной нельзя пользоваться – может нарушить весь процесс.
Важно придерживаться правил безопасности, проводя покрасочные работы. Обязательно наличие респиратора, перчаток и отсутствие отрытого огня.
Производить покраску реально своими руками или воспользоваться услугами специалистов. Данное требует дополнительных средств, но результат будет безупречен.
Подготовка авто к покраске жидкой резиной
Одним из главных моментов является подготовка автомобиля к покраске. Сначала ее надо очистить, помыть, а когда произошла сушка, обязательный этап – обезжиривание. Подобный процесс необходим, чтобы материал на авто лег равномерно и не появлялись пузыри.
Подготовка авто к покраске жидкой резиной
Если есть серьезные повреждения их нужно скрыть с помощью грунтовки. Важный момент, после ее нанесения не желательно проводить покраску. Все дефекты будут скрыты под резиной.
Следующим этапом подготовки является демонтаж частей, которые окрашиваться не будут. Сначала необходимо снять номерные знаки, стекла и фары. Если на какие-то части не будет наноситься краска, но их трудно снять, следует заклеить специальной пленкой. Но сделать нужно очень тщательно. Особый акцент сделать на окна.
Перейдем к колесам, если их покраска есть в планах, то малярный скотч нужно использовать относительно тормозных барабанов. Если же диски не будут краситься, их нужно обмотать тугой пленкой либо красить в снятом положении.
Подготовка жидкой резины и распылителя к покраске
Дабы покраска прошла успешно, и результат был безупречен, стоит правильно выбирать оборудование. Важным элементом является выбор самой краски – основа всего процесса. Купить ее можно в готовом виде, но густая консистенция не подходит в случае нанесения на поверхность. Требуется дополнительный растворитель. Его также можно купить в комплекте с краской. Приготовить раствор очень просто: нужно смешать краску с растворителем в пропорции 1:1 и размешать до получения однородной массы. Все необходимые инструкции указаны на упаковке.
Для покраски используется специальный автомобильный краскопульт. Готовый раствор заливать только до половины. Особое внимание стоит обратить на фильтр.
Краскопульт для жидкой резины DeVilbiss PRi Pro Lite
Нанесение жидкой резины на автомобиль
Любой вид покраски может оставлять следы на коже человека, поэтому обязательно пользоваться спецодеждой. Причем все участки тела должны закрываться. На глазах – широкие очки и обязательно респиратор. В помещении должны находиться только люди в таком экипировании.
Покраска начинается с больших деталей. Сначала капот, крыша, двери, потом трудные участки. Технология предусматривает параллельное нанесение краски на авто слоями, расстояние должно соответствовать 15 см. Дабы улучшить фиксацию первый слой лучше сделать тонким. Всего 10 слоев, есть варианты нанесения меньшего количества, но тогда страдает качество.
Слои надобно наносить медленно, после каждого обязательна сушка 20 минут. После нанесения последнего слоя оставить машину на сушку в закрытом помещении на 24 часа. Температурный режим не так важен, но лучше, чтобы не было сильно жарко. Зачастую соблюдается температура 18-20 градусов при отсутствии сквозняков. Защитные наклейки снимать только после окончательного высыхания. Аккуратно снимается пленка и скотч, подрезая на стыках ножом.
Примерный расход жидкой резины при покраске
Данная краска весьма недешевый материал, поэтому автолюбителей интересует какой расход при покраске и сколько стоит. Все зависит от выбранного типа краски и конкретного авто. Расход указан на упаковке при условии полного покрытия, но не более чем относительно 7 слоев. Обычно этого мало, поэтому дозу стоит немного преувеличивать.
Полноценно рассчитать расход можно с помощью специалистов. Понадобятся характеристики автомобиля.
Нанесение жидкой резины на автомобиль
Расход жидкой резины в аэрозольных баллончиках
Что касается жидкой резины в аэрозолях, то расход будет зависеть от масштаба и площади окрашивания. Стоит упомянуть – баллончики в случае полного окрашивания используются редко, ими удобно отделывать мелкие детали, например, покрышки. Но есть случаи, когда аэрозоли используются относительно всей площади авто.
Расчет происходит по схеме:
- Большие элементы, такие как крышка капота, крыша и багажник по 2 баллончика.
- Детали поменьше, например, двери лучше покрасить с помощью 1 аэрозоля.
Таким образом, на полную покраску требуется примерно 15 баллончиков.
Расход концентрата жидкой резины для покраски авто
Если использовать концентрат, окрашивание происходит с помощью краскопульта. Автомобиль класса А и В – понадобится от 3 до 5 литров, класса С и D – до 7 литров, класса E, F, S – до 12 литров. Это примерные показатели, они указаны с расчетом нанесения не более 7 слоев резины. Кроме того, есть отличие в зависимости от радикальности перекрашивания. Если фабричный цвет темный и наносится темная резина, то краски потребуется меньше. В случае кардинального изменения цвета, требуются дополнительные слои, и соответственно больше краски.
Жидкая резина в баллончике
Отзыв о покраске автомобиля жидкой резиной Plasti Dip
На популярных интернет-страницах, можно встретить множество отзывов о жидкой резине Plasti Dip. Любители шикарных авто с удовольствием делятся своими впечатлениями.
Егор: «Прекрасная вещь эта краска, плюсы и минусы видны при первом использовании. Стоит сказать – преимуществ больше. Я решил начать с малого и нанес краску на решетки дисков. Автомобиль сразу преобразился. Наносится краска очень легко. Единственным минусом могу назвать довольно высокую стоимость».
Карина: «Хотела, дабы моя ласточка выделялась из машин в толпе, выбрала жидкий винил. Полностью осталась довольная результатом. Всего через сутки получила абсолютно новый автомобиль, выбрала яркий цвет Plasti Dip. Родного красного не видно. Единственным минусом могу назвать тот момент, что через год, а именно в середине лета цвет начал терять яркость».
Валентин: «Plasti Dip порекомендовали в салоне. Уверяли – материал долговечный, покрытие получается стильным и уникальным. Выбрал цвет металлик глянцевой структуры. Машина вышла супер. Думаю, что каждый может подобрать свой индивидуальный стиль. Через 20 месяцев самостоятельно снял покрытие без лишних усилий. Никаких следов и царапин на машине не осталось».
Заключение
Совершенно новый, интересный и стильный тип окрашивания – жидкая резина, сколько стоит весь процесс, трудно сказать. Но, дабы результат был успешным, не надо экономить на материале. Лучше провести окраску самостоятельно, тогда получится сэкономить на работе. Применяя подобный способ изменения авто, можно получить шикарный внешний вид. Машина будет выгодно выделяться из толпы. Но к жидкому винилу стоит обращаться бережно, не стоит забывать – продукт не заводская эмаль.
Обязательное соблюдение рекомендаций:
- Использовать машину можно через 12-24 часа, но в течение 3-х суток стоит избегать попадания воды.
- Прибегать к автоматической мойке с жесткими щетками следует только через месяц.
Жидкая резина для гидроизоляции: виды, отзывы + особенности применения
К обустройству кровли сегодня изначально предъявляются достаточно серьезные требования: создать влагонепроникаемое покрытие, которое легко повторит форму крыши, противостоять ультрафиолетовым лучам и любой непогоде. И среди всей предлагаемой рынком продукции одной из самой надежных считается современная жидкая резина для гидроизоляции – уникальный функциональный материал, создающий непроницаемую оболочку на самых разных объектах.
И, если вы еще ничего не слышали об этом, рады будем предоставить вам самую свежую информацию!
Преимущества и недостатки инновации
Давайте посмотрим для начала, что именно представляет собой кровельная жидкая резина и насколько прост или сложен ее монтаж:
Высокая адгезия к основанию имеет огромное значение. Так, если вода случайно проникнет под такое покрытие, она не должна разливаться под ним. Если речь идет о мембране, то так, к сожалению, и будет, а сама мембрана в это время не позволит влаге высыхать, т.к. будет ненамеренно защищать ту от солнца.
А вот жидкая резина образовывает прочную пленку, которая надежно сцеплена с крышей, и никаких водяных линз под ней быть не должно. Конечно, если вы полностью придерживались технологии.
Именно резиной этот инновационный материал называется потом, что обладает уникальной растяжимость до 1650%: на практике 5-сантиметровый кусочек такой пленки получается растянуть до 80 см! Чем это ценно для кровли? Любые малозаметные для глаз движения кровли не смогут повредить изоляционный ковер, и даже небольшая трещина затянется сама по себе.
Жидкая резина также подходит для антикоррозийной защиты деревянных, металлических и бетонных крыш. В отличие от более привычного битума, жидкую резину напыляют холодным методом, и она достаточно быстро образует на поверхности крыши целостную бесшовную мембрану, с высокой адгезией практически к любому материалу.
И в итоге мы получаем такие ценные свойства жидкой кровли:
- абсолютная газо-, водо- и паронепроцинаемость;
- высокая устойчивость к ультрафиолету и озоновым дождям;
- легкий вес (почти в 4 раза меньше, чем у рулонных материалов).
- способность выдерживать термические стрессы и агрессивную среду;
- пожаробезопасность и нетоксичность;
- сохранение своей структуры без изменения на протяжении своего срока службы;
- Smart-память, когда материал самостоятельно затягивает случайные отверстия!
Еще жидкую резину называют «напыляемой». Если жидкая резина производилась в соответствии с известными мировыми экологическими стандартами, то она не будет содержать летучих веществ и растворителей, а потому не станет выделять никакого неприятного запаха.
У жидкой резины просто-таки потрясающая эластичность, и даже с годами предел прочности остается высоким. Чем старше такая кровля, тем тверже становится ее покрытие, но при этом эластичность сохраняется и покрытие не шелушится и не крошится.
Благодаря всему этому на жидкую резину для крыши дают от 20 лет гарантии. Конечно же, жидкая резина обойдется вам дороже многих других кровельных покрытий, но она служит дольше, чем они. Поэтому вопрос экономической целесообразности такой покупки не так уж прост!
Для сравнения, в случае применения рулонной гидроизоляции на 1000 м2, получается 10000 метров швов. Одним словом, целых 10 километров опасных мест, не говоря уже о случайных дефектах.
В отличие от обычных мастик и рубероида любое повреждение у жидкой резины затягивается само по себе:
Еще один важный весомый плюс: жидкая резина никогда не разрушается под воздействием вибрации. Вот почему жидкую резину по праву называют «умным» строительным материалом. Такая кровля уже несколько десятков лет успешно применяется на Западе!
Вот, например, занимательное видео о том, как создается инверсионная кровля, у которой первый и самый важный слой – жидкая резина:
По цене настоящую жидкую резину часто сравнивают с битумной черепицей, т. к. и срок службы здесь почти такой же.
Те, кто уже проверил прочность крыши из резины, согласны, что покрывая год за годом кровлю рулонными материалами никакой выгоды не достичь, тогда как достаточно один раз вооружиться валиком и качественным составом.
Почему встречаются плохие отзывы?
К сожалению, среди профессиональных кровельщиков нередко встречается мнение, что жидкая резина совершенно не подходит для гидроизоляции кровли. И что в итоге таких работ течет более 80% стыков.
Но давайте разберемся с этим понятием. На самом деле под жидкой резиной часто подразумевают более широкое понятие, чем должно быть, и рассчитано оно на массового потребителя. Жидкой резиной зачастую называют любую мастику, которая ее напоминает, и соответствует таким критериям: водонепроницаемая, эластичная и способная к растяжению.
И зачастую такой кровельный материал не имеет ничего общего с самой резиной, которая производится из каучука. Поэтому правильно было бы назвать подобный материал бесшовной напыляемой гидроизоляцией, как и пытались сделать производители, но термин не прижился среди обычного народа.
Вот, например, одна из самых распространенных ошибок – считать, что жидкая резина представляет собой смесь битума и латекса. Причем даже сами производители умудряются утверждать, что выпускают именно «жидкую резину», чтобы привлечь потенциальных покупателей.
И да, действительно, такой состав мало устойчив к ультрафиолету. Больше того, в своих рекламных роликах показывают, как такая резина легко снимается с поверхности в виде пленки! О какой тогда адгезии можно тогда говорить.
Настоящая жидкая резина не стекает с крыши даже в сильную жару и не растрескивается в мороз, к счастью, уже есть успешный опыт применения жидкой резины в Якутии. Жидкая резина не стареет, как битум, т.к. здесь есть специальный полимер, а он не дает эфирным маслам испаряться. Благодаря этому такая кровля служит не меньше, чем 20 лет:
Кроме того, жидкая резина изначально разрабатывалась за рубежом, где требования к пожарной безопасности и экологии одни из самых высоких. Вот почему импортные аналоги безопасны для людей и растений, негорючие и нетоксичны. Настолько, что даже подходят для обустройства искусственного пруда и резервуара с питьевой водой.
Не стоит также путать жидкую резину для кровли с таким довольно узконаправленным продуктом, как Пласти Дип и его аналоги. Это действительно жидкая резина, но предназначенная только для автомобилей и не подходит для кровли. Да, эта резина легко снимается тонкой пленкой, т.к. серьезная адгезия ей не нужна.
Также иногда встречается утверждение, что при приготовлении жидкой резины для кровли используется солевой раствор, потоки которого потом останутся на крыше. На самом деле в некоторых марках резины действительно есть соль, которая разводится в отношении 1/100 – совершенно незначительно. У резиновой кровли нет ингредиентов, которые способны растворяться в воде. Этим она кардинально отличается от популярной резиновой краски, обратите внимание!
Обзор рынка – какой продукции доверяют?
У разных производителей свой взгляд на состав жидкой резины, отчего также будет зависеть итоговое качество. На отечественном рынке жидкую резину, а именно то, что под ней подразумевают, представляют четыре компании: Технопрок, Гермтехно, Гермпромстрой и Well-C Technologies. Это официальные дистрибьюторы компаний Liquid Rubber, Pazkar, Huske и Premium Liquid Rubber.
Жидкая резина от Liquid Rubber – эластомерная водная эмульсия на основе нефти и специальных полимеров.
Одни из самых популярных российских разработок в этой сфере – жидкая резина Профикс и Syntomast:
Жидкая резина марки Syntomast разрабатывается как инновационное покрытие на основе полимеров, которые наиболее устойчивы к атмосферным условиям и агрессивной среде. При этом такие мастики выпускают в цвете и пользуются большой популярностью, ведь широкую цветовую гамму ценят прежде всего дизайнеры.
А те и определяют зачастую, какой именно материал будет использоваться. По сути, Syntomast Roof – это плотная паста на основе воды, которую поставляют объемом от 20 до 200 литров, в виде красного, бежевого, синего, белого, зеленого и черного цвета.
Вторая известная отечественная марка двухкомпонентной жидкой резины – Профикс. Разработана она была, как говорится, «от фундамента до кровли».
Славится своими отличными свойствами также жидкая резина GPSpraykote, которая рекомендована для объектов минобороны РФ. Она изготовлена на основе полимерно-битумной водной эмульсии, поэтому наносится холодным методом при помощи распылителя. Отличается от других аналогов свойством мгновенного отверждения.
Хорошие отзывы можно услышать и о отечественной жидкой резине Liquid Rubber, которая производится по импортным технологиям. В ее основе – водная эмульсия из очищенных модифицированных битумов и полимеров, которые хорошо защищают покрытие от агрессивных сред и ультрафиолета.
Набирает также свою популярность жидкая резина «Элемент». Это материал на основе модифицированного каучука, который создает в заводских условиях нано-робот.
И, наконец, еще один популярный продукт. До недавнего времени компания Технопрок свою жидкую резину импортировала из-за границы, но теперь стала производить самостоятельно, в России. Причем, если верить отзывам, достаточно качественно.
Единственное отличие от импортных аналогов только в том, что это покрытие после высыхания на ощупь более жесткое. К слову, Технопрок в народе нередко сравнивают с израильской жидкой резиной Rapidflex, т.к. те действительно схожи по своим свойствам.
Особенности нанесения на поверхность
Самое ценное преимущество жидкой резины для строителей в том, что ее легко наносить на все кровельные материал и в горизонтальном, и в вертикальном направлении. При работе на опасной высоте это – довольно ценный момент.
И в самых сложных местах, где обычно приходится лепить что-то из кусков того же рулона или гонтов, здесь достаточно просто направить струю. Причем жидкую резину разрешено наносить и на бетон, и на камень, и даже на дерево.
Для нанесения жидкой резины конкретно на кровлю достаточно минимальной подготовки: поверхность всего лишь должна быть чистой и сухой.
Весь процесс по напылению резины проходит быстро, за день бригада успевает обработать более 1000 квадратных метров, и при этом для работы с оборудованием необходимо всего два человека. А способ гидроизоляции кровли напрямую зависит от того, с какой именно жидкой резиной имеют дело: с одно- или двухкомпонентной.
Однокомпонентная жидкая резина
Все однокомпонентные мастики – это высокодисперсные смеси на водной основе. В них водят специальные наполнители, красители, консерванты, стирол-акрилатные полимеры, загустители и даже пеногасители.
К слову, довольно часто однокомпонентную жидкую резину дополнительно посыпают базальтовой или сланцевой крошкой, чтобы защитить ее от солнечных лучей и случайных механических повреждений при ходьбе. И, конечно, эстетические свойства еще никто не отменял:
Двухкомпонентная жидкая резина
Жидкая резина CBS Synto от компании «Технологии гидроизоляции» – это недорогая мастика для кровли, обладающая при этом неплохим качеством.
Суть самой технологии состоит в напылении битумно-латексной эмульсии при помощи специальной безвоздушной установки. В ней на ходу под давлением смешиваются два компонента, наносятся на поверхность и полимеризуются.
Прямо на место строительства жидкую резину традиционно поставляют в отдельных герметичных бочках. Сегодня подрядные организации используют импортное или отечественное оборудование для распыления жидкой резины. Такая аппаратура работает на бензиновом двигателе и комплектуется шлангами до 150 м.
Благодаря этому оборудование не нужно поднимать на крышу:
Откройте для себя что-то новое: последние строительные технологии действительно могут вас удивить!
Жидкая резина для авто в баллончике: преимущества материала
Как сделать так, чтобы моя машина выделялась из общей массы? Можно ли сделать защиту лакокрасочного покрытия транспортного средства не только надёжной, но и красивой? Эти вопросы, друзья, часто звучат от автовладельцев, и, оказывается, на них можно дать один универсальный ответ — жидкая резина для авто в баллончике.
Это чудо современной химической промышленности действительно интересное решение, поэтому давайте познакомимся с ним поближе.
Жидкая резина для авто в баллончике
Сначала разберемся, что такое жидкая резина для авто вообще и в частности.
В России этот материал известен под именем Plasti Dip, он уверенно завоевывает свою нишу, и не только в покраске автомобилей, используется в строительстве как влагозащитное покрытие.
Изобретён этот материал ещё в 1972 году в США.
Данное химическое вещество является смесью различных полимерных компонентов, воды и битума. Иногда, битум заменяют натуральным каучуком, но это редкость и влечёт за собой лишь ненужное удорожание продукта.
Резина против винила
Жидкая резина для авто в баллончике, а именно в таких упаковках традиционно выпускается классическая продукция под брендом Plasti Dip и других производителей (Rubber, Dip Team), их в достаточном количестве можно встретить на полках магазинов.
Жидкая резина имеет ряд интересных свойств, недоступных более распространённым защитным покрытиям кузовов, к примеру, виниловым плёнкам.
Резина эластична, водонепроницаема, легко переносит перепады температуры. Помимо этого, она ещё неплохо выглядит, что в совокупности с хорошим ассортиментом палитры, даёт и широкие возможности для любителей всяческого кастомайзинга и тюнинга.
В конце концов, если она вам надоест, то её легко удалить, не повредив оригинального лакокрасочного покрытия автомобиля, что обычный винил сделать не даст.
Такой вот супер-материал, хотя у покрытия авто жидкой резиной найдутся и свои недостатки. О них, а также более подробно о достоинствах далее…
Покраска авто жидкой резиной позиционируется в рекламных буклетах, как бескомпромиссная замена виниловым плёнкам и различным автоэмалям. Так ли это на самом деле?
Для начала сведём воедино все достоинства резины, и их действительно немало:
- покрыть этим материалом можно практически любую деталь автомобиля, даже с самым хитрым рельефом;
- отличные защитные и водоотталкивающие свойства;
- очень красивый внешний вид;
- минимальные подготовительные работы перед покрытием авто жидкой резиной;
- легко и просто удаляется без повреждений оригинального лакокрасочного слоя кузова.
Но не всё так радужно, есть и минусы:
- непродолжительный срок службы такого покрытия — максимум 2 года;
- нет возможности нанести рисунок или узор;
- требуется более внимательный уход за кузовом — если случайно подцепить край резины во время мойки, считайте что всё испорчено.
Как покрасить?
На самом деле покраска авто жидкой резиной дело не очень сложное, но кое-какие приготовления всё же нужны. Что нужно знать, если вы решили самостоятельно заняться данной процедурой? Проделайте такие шаги:
- тщательно вымойте автомобиль с использованием специальных шампуней;
- протрите кузов насухо;
- закройте или заклейте фары, решётку радиатора и другие отверстия, куда резина попасть не должна.
Как вы уже знаете, в магазинах присутствует жидкая резина для авто в баллончике, но такой формат упаковки подойдёт в случае, когда окрашивается лишь какая-то часть кузова, к примеру, капот.
Если же вам надо полностью покрыть машину этим материалом, то лучше приобрести ёмкость побольше, благо и такие есть в продаже.
Помимо этого понадобится краскопульт, в который заправляется материал в пропорции 50/50 с растворителем. Прежде чем направить инструмент на авто, потренируйтесь на чём-нибудь ненужном, дабы прочувствовать, как ложиться резина.
В принципе, на этом подготовку можно закончить и время приступать к покраске. Покрытие авто жидкой резиной необходимо производить в несколько слоёв, в промежутках работы давая им подсохнуть в течение 15 минут.
Как вы видите, уважаемые читатели, вариант тюнинга, который мы сегодня рассмотрели, достаточно интересный, и, самое главное, не требующий особых затрат или нечеловеческих усилий.
Ну а нужен ли он, решать, конечно же, только вам, автовладельцам.
Жидкая резина: неудачный опыт — Skoda Octavia, 1.8 л., 2013 года на DRIVE2
После покупки дисков HAWK 16” решил сразу их преобразить, в связи с чем приобрел бесценный неудачный опыт использования жидкой резины, которым хочу со всеми поделиться.Задумка была перекрасить диски в бело-черный цвет с использованием жидкой резины в баллончиках. Прочитал много отзывов об этом продукте и сделал вывод, что особых проблем с его нанесением у меня быть не должно. Но все-таки, поскольку такого никогда не делал, опасность неудачного исхода где-то в глубине души жила.

Начало оклейки скотчем
Первый слой
Второй слой
Последний слой
Итог первого этапа покраски
Такие вот косяки повсюду
… еще
Жидкая резина — что за материал, назначение и применение
Жидкую резину можно отнести к краске (резиновой) или к герметикам, мастикам, поэтому иногда вызывает путаницу вопрос что за материал жидкая резина. Все эти классификации относительны и обусловлены многообразными использованием пласти дипа, полезными свойствами жидкой резины, которые человечество научилось умело применять.
Резиновая краска PLASTI DIP применяется для покраски авто, герметизации швов, виброизоляции, для покраски металлоконструкций и защиты микроэлектроники от влаги и пыли. С развитием квадрокоптеров многие производители стали защищать двигатели и элементы плат управления жидкой резиной пластидип, чтобы защитить продукт при попадании в лужу или эксплуатацию в дождь. И самый большой рынок применения пластидипа, это для чего нужна жидкая резина, конечно покраска автомобилей так называемым жидким винилом. Окрашивают plasti dip в гаражах, боксах, автосервисах. Его наносят на кузов, диски, эмблемы, решетки и другие пластиковые элементы. Для этого используют спреи (баллончики) пластидипа или концентрированный руббер дип для распыления через краскопульт. Существует множество возможностей применения plasti dip, а производитель Performix дает выбор методов покраски.
Цветовая гамма резиновой краски формируется из базовых цветов (тех, которые производятся на фабрике) плюс набора колеров, которыми можно изменить оттенок или создать абсолютно новый цвет. В этом смысле жидкая резина имеет широкое назначение и применение за счет широкой гаммы цветов под любые потребности. Крупные производители различных продуктов, которые в своей работе используют plasti dip могут добиться стабильного оттенка с помощью RAL каталога. Статьи и публикации на темы, которые связаны с назначением и применением пластидипа Вы найдете на этой странице.
цена, долговечность, технология покраски, конкуренты
На сегодняшний день жидкая резина для автомобилей является на нашем рынке новым продуктом, который в будущем составит серьезную конкуренцию полиуретановому покрытию и различного вида пленкам. Один из главных плюсов — очень низкая цена. В Беларуси на данный момент о жидкой резине знают крайне немного, а владеют технологией ее нанесения и вовсе считаные фирмы. Вместе со специалистами мы попытались выяснить, что представляет собой это модное покрытие на фоне относительно старых и широко известных методов защиты ЛКП автомобиля.
Мы встретились с Дмитрием Гореловым, специалистом по окраске жидкой резиной. Красить кузов жидкой резиной здесь начали сравнительно недавно, но уже нашли в новой технологии большое количество плюсов.
— Нам известно о трех основных вариантах защиты и украшения кузова автомобиля: полиуретан, пленка и жидкая резина. В чем плюсы и минусы каждого из вариантов? Чем выделяется новая технология защиты кузова?
— В современных автомобилях производитель экономит на толщине ЛКП, иногда использует краску на водной основе, поэтому, если вы хотите сохранить кузов в целости и сохранности несколько лет, стоит подумать о защите лакокрасочного покрытия. Некоторым хочется выделиться в потоке серых и будничных автомобилей, поэтому сегодня на рынке услуг в Беларуси развиваются такие направления, как оклейка автомобиля пленкой, нанесение на кузов полиуретанового покрытия или жидкой резины.
Полиуретановое покрытие популярно среди владельцев внедорожников
Плюс полиуретанового покрытия — его практически невозможно испортить. Лакокрасочное покрытие под полиуретаном на 100процентов защищено от внешних воздействий. Но вместе с этим данное покрытие практически невозможно снять с автомобиля. То есть, если вам оно надоест, вы от него никак не избавитесь. Нет, сделать это, конечно, можно, но только вместе с лакокрасочным покрытием. К эстетике тоже есть вопросы: далеко не всем внешний вид автомобиля с полиуретаном по душе. Такой вид защиты актуален для владельцев внедорожников, которые любят частые вылазки на серьезное бездорожье.
Тем не менее к нам приезжал как-то владелец Jeep Wrangler: он пожалел, что покрыл машину полиуретаном, после того как узнал о жидкой резине.
Пленка с рисунком под армейский камуфляж смотрится здорово. К слову, Дмитрий утверждает, что military style можно сделать и жидкой резиной
Пленки, если делает хороший мастер, ездят достаточно долго. И в эстетическом плане все очень хорошо. Но стоимость выше, чем у жидкой резины. К тому же процесс оклейки занимает больше времени.
Жидкая резина имеет много достоинств и очень мало недостатков. Она отлично защищает лакокрасочное покрытие от царапин и сколов. Первой машиной, которую мы покрыли, был мой личный Opel Astra. И знаете, я жалею, что сразу после покупки машины не покрыл ее жидкой резиной: сейчас лакокрасочное покрытие было бы как новенькое. Снимать новый материал тоже проще простого, для этого даже не нужно обращаться к специалистам. (Видео «издевательств» над покрытием из жидкой резины — в начале материала. — Прим. авт.) Мы все это, кстати, испытывали на Opel Astra. На нем же и тренировались красить. Было много «пилотных версий», но благодаря Astra нашли оптимальную технологию окраски кузова жидкой резиной. Разумеется, пришли к этому не сразу. Перед экспериментами ездили по различным российским, перенимали опыт.
Производители пленок предоставляют большое количество цветов, но палитра все-таки ограничена. В случае с жидкой резиной можно сделать абсолютно любой цвет путем смешивания базового и дополнительного цветов. Жидкая резина бывает глянцевая, матовая, перламутровая, цвета «металлик», прозрачная. Можно сделать аэрографию. Можно покрасить в цвет кузова –не нужно будет менять техпаспорт. Toyota Celica, который мы сейчас красим в этом цехе, выедет отсюда с цветом «хамелеон». И выедет быстро, ведь подготовка кузова и покрытие жидкой резиной отнимают всего два дня. То есть это быстрый тюнинг автомобиля.
Первые слои жидкой резины
Финиш. Ребятам осталось только фары прикрутить.
— Но дешевый ли?
— Давайте разбираться с ценами. Покрыть кузов легкового автомобиля полиуретаном будет стоить от полутора до трех тысяч долларов. Если брать китайскую пленку, можно уложиться в 800 долларов. Если брать качественную дорогую пленку — выйдет от 1500 до 2500. Жидкая резина — та-дам! — всего лишь от 500 долларов! Этих денег хватит, чтобы обновить внешний вид такого автомобиля, как, например, Opel Astra. В чем секрет? Материал недорогой, поставляется в банках в густом виде, разбавляется растворителем. Сам процесс покрытия совершенно несложный, хотя и не без нюансов, о которых необходимо знать, чтобы что-то вообще получилось. Сама работа стоит 300 долларов, все остальное — материал. Чем больше машина, тем больше его потребуется. Кстати, при нанесении жидкой резины элементы, которые не нуждаются в покраске, можно даже не заклеивать. Это мы заморачиваемся, заклеиваем. Все лишнее потом легко удалить.
— Какие минусы имеются у жидкой резины?
— Она может царапаться, и царапины на ней видны. Хотя, что любопытно, после нескольких автоматических моек эти мелкие повреждения исчезают. Если на покрытии была грязь и на нее попадает бензин, то грязь начинает въедаться в покрытие. Опять же автоматическая мойка должна решить эти проблемы, но лучше осторожнее с бензином. Хотя в плане технологии покраски нет ничего сложного, но именно от этой самой технологии и зависит долговечность и прочность покрытия. Повторю еще раз: именно от качества покраски жидкой резиной зависит ее долговечность! Мы видели в Минске машины, покрашенные очень тонким слоем. И с них жидкая резина уже облезает. А пользователь потом будет ругать материал, хотя материал тут ни при чем — дело в руках.
— На какой срок распространяется гарантия? В чем заключаются нюансы технологии покрытия автомобиля жидкой резиной?
— Гарантию мы предоставляем на два года. Что касается нюансов, очень важно не экономить на растворителе, дешевый покупать не стоит. Необходимо правильно подобрать соотношение жидкой резины и растворителя. Последнее раскрыть не могу — сами понимаете, секрет фирмы. Мы долго над этим работали. Важно соблюсти необходимый объем материала. Есть в Минске ребята, которые берут четыре литра жидкой резины, смешивают с четырьмя литрами дешевого растворителя, получают восемь литров материала и выливают его на машину. Этого мало. У нас только на одну машину уходит две-три четырехлитровые банки жидкой резины, не учитывая количества растворителя. Также между нанесением слоев необходимо соблюдать определенные временные рамки: мы наносим слой раз в 15 минут. В общем, результат очень сильно зависит от технологии. Хотя в ней на самом деле нет ничего сложного.
— Что жидкая резина вообще собой представляет? Из чего состоит?
— Первое упоминание в Интернете о ней датируется 2006 годом — об этом нам сообщает Google. Сейчас ее массово производят такие фирмы, как Plasti Dip, Color Dip и Rubber Paint. Что лучше, а что хуже, я сказать не могу. В принципе оно все одинаковое. Сама жидкая резина состоит из 40 процентов силикона, 25 процентов нефтесодержащего продукта, остальное — секретные добавки и растворитель.
Вердикт ABW.BY
Итак, всего за 500 долларов можно покрыть автомобиль новым для нашего региона материалом — жидкой резиной. Конечно, мы будем собирать отзывы об этом новом материале, но пока все очень хорошо, надежно и дешево. Напоследок хочется посоветовать правильно выбрать мастеров: от качества работы, как нам показалось, зависит многое.
А в целом материал и технология его нанесения очень любопытные, не так ли? Если вы сталкивались с жидкой резиной, ждем ваших отзывов на форуме.
Юрий ГЛАДЧУК
Фото Аркадия СОБОЛЕВА и Дмитрия ГОРЕЛОВА
Видео Аркадия СОБОЛЕВА
ABW.BY
Обычные объявленияНайдено 82 объявлений Найдено 82 объявленийХотите продавать быстрее? Узнать как | |||||
| |||||
Как снять жидкую резину с автомобиля
На сегодняшний день существует много разных вариантов автомобильного стайлинга. Одним из наиболее революционных из длинного списка методов можно считать покраску авто жидкой резиной. Это сравнительно новая технология, которая уже успела привлечь к себе пристальное внимание автолюбителей. Она всё сильнее набирает обороты, обходя по популярности другие средства.
Покраска автомобиля жидкой резинойПокрытие из жидкой резины для авто было разработано и выпущено на рынок американской компанией PlastiDipInternational.
Это вещество на виниловой основе, которое можно считать чем-то средним между лакокрасочным покрытием и виниловой плёнкой.
Оно наносится на поверхность авто при помощи обыкновенного пульверизатора и по внешним эстетическим свойствам ничем не уступает самым «продвинутым» вариантам стайлинга. Сегодня технология PlastiDip становится всё более популярной среди владельцев авто как в нашей стране, так и за рубежом.
Нанесение жидкой резины на кузов машиныСвойства жидкой резины
Если внимательно изучить характеристики покрытия из жидкой резины, получится такой перечень преимуществ:
- стойкость к механическим внешним повреждениям;
- эластичность и упругость;
- защита от выгорания под УФ-излучением;
- влагооталкивающие характеристики;
- работа в диапазоне температур от -350С до 930С;
- антискольжение;
- стойкость к перепадам температуры;
- стойкость к воздействию химически активных веществ.
Достоинства использования технологии PlastiDip
Как уже упоминалось выше, технология нанесения на авто жидкой резины является совокупностью достоинств лакокрасочного покрытия и оклеивания виниловой плёнкой. Рассмотрим подробнее перечень тех факторов, которые могут считаться выигрышными:
- дополнительная защита кузова авто от царапин, сколов и других внешних повреждений механического характера;
- защита автомобиля от влаги и возникновения коррозии;
- для покраски не нужно шлифовать и грунтовать кузов машины;
- можно использовать не только для кузова, но и для колёсных дисков, деталей салона и любых других элементов;
- годится для окрашивания любого материала;
- хорошо справляется с участками со сложной конфигурацией и мелкими деталями;
- окрашивание авто жидкой резиной занимает около 12 часов;
- в случае необходимости можно оперативно снять плёнку, вернув машине её первоначальный вид;
- окрашивание авто жидкой резиной можно довольно просто осуществить своими руками;
- слой лакокрасочного покрытия под плёнкой не только не страдает, но и хорошо защищён от внешних факторов;
- долговечность;
- демократичная цена;
- широкий выбор цветов и типов поверхности (матовая, глянцевая, неоновая и т.
п.).
Стайлинг автомобиля с помощью жидкой резиныВсе эти достоинства, естественно, являются хорошим аргументом в пользу использования технологии PlastiDip для стайлинга вашего автомобиля.
Как снять жидкую резину
Производитель заверяет, что если нанесение жидкой резины осуществлялось со строгим следованием всем тонкостям технологии, снятие не вызовет у вас особых проблем. В случае необходимости вам просто нужно будет выполнить следующие действия для каждого участка:
- С краю подцепите уголок покрытия и аккуратно тяните кверху, не делая резких движений.
- Постепенно перехватывая отслаивающуюся плёнку, вы предельно аккуратно продвигаетесь всё дальше. При этом избегаете рывков и стараетесь, чтобы усилие было равномерным.
- На каждом участке плёнка будет сниматься цельным куском.
- В углублениях и выемках могут оставаться тонкие полоски и напыления — их вы удаляете при помощи микрофибровой салфетки.
Она должна быть сухой — никакой химии не нужно. Трёте до тех пор, пока не удалите весь налёт.
- После того как вся поверхность машины будет освобождена от покрытия, хорошенько вымойте машину водой с моющим средством, лучше всего под давлением.
Однако если жидкая резина для автомобиля была нанесена на поверхность кузова машины с нарушением технологии, или если слой покрытия слишком тонкий, у вас могут возникнуть сложности. В этом случае есть возможность того, что вы не сумеете снять плёнку одним куском, и процесс её удаления будет иметь все шансы стать для вас невыполнимым. Но не расстраивайтесь — выход есть и в такой ситуации.
Для того чтобы удалить жидкую резину, которая плохо поддаётся вашим усилиям, воспользуйтесь специальной смывкой DipDissolver. Это универсальное средство для снятия тонких слоёв, а также для удаления покрытия, нанесённого с нарушением технологии.
Пользоваться средством DipDissolver довольно просто:
- при помощи пульверизатора нанесите на поверхность первый слой и выждите минут 15;
- далее нанесите ещё один слой DipDissolver;
- через 5 минут можете смывать средство струёй воды под напором — вместе с ним сойдет и жидкая резина.
Следует учесть, что на чёрной поверхности может остаться белый налёт, так что будьте осторожны.
Заключение
Для того чтобы удаление покрытия PlastiDip не вызывало сложностей, чётко следуйте технологии в момент покраски автомобиля. Если вы будете старательно соблюдать инструкцию, и нанесённый вами слой не будет чрезмерно тонким, вы при необходимости сумеете без труда удалить покрытие с вашей машины. Оно просто снимется, как клейкая плёнка, цельным куском.
Если же удаление покрытия PlastiDip вызывает сложности, и оно не снимается одним куском, воспользуйтесь универсальной смывкой DipDissolver. Метод её применения крайне прост, и через полчаса ваша машина будет иметь первоначальный вид.
[democracy]
[democracy]
Если хотите больше интересных статей по тематике авто, подпишитесь на наш канал в ЯндексДзен.
Жидкая Резина — OLX.

| |||||
| |||||
Похожие запросы:
aBi+OMZ/rDETrvY2SlLVLnI4aqzvsBi7HBb2Web4U9/OfDlPUXwX/Sd7HdYhXCXjtGfCgLvVemdPth954ZH0erFRF6hGt2RbMmxksSApaA+3m07YW6vlG1PGXBkHFLy8hjhGfkC5gAJMm3LQSvVNybPyE7YSnV3fdda7VUTqh/4kZSdvfKmYZPgxHt2a3cHltaO+mjsl7SfWQLYKhRRneGMjgnOwS616uWjR+qneC+yHAqCOQdROlLznxtW/GR5tuazMGkhFUCXIeek3A338RQ00YfZlWLRF
- Недавно просмотренные
- Избранные объявления (0)
- Избранные результаты поиска
Как использовать сырую резину
Резина – пластмассы с редкосетчатой структурой, в которых связующим выступает полимер, находящейся в высокопластическом состоянии.
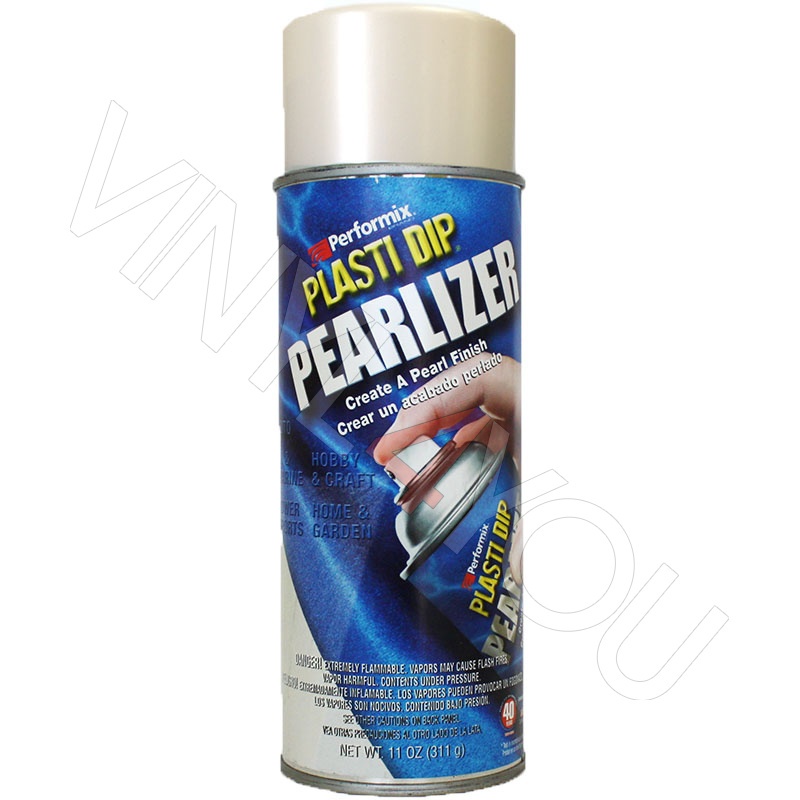
В резине связующим являются натуральные (НК) или синтетические (СК) каучуки.
На рис. 1 и 2 показаны область применения каучуков и получаемые изделия.
Рис. 1 Применение каучуков
Рис. 2 Изделия, где используются каучуки
Каучуку присуща высокая пластичность, обусловленная особенностью строения их молекул. Линейные и слаборазветвлённые молекулы каучуков имеют зигзагообразную или спиралевидную конфигурацию и отличаются большой гибкостью (рис. 3, верхний). Чистый каучук ползёт при комнатной температуре и особенно при повышенной, хорошо растворяется в органических растворителях. Такой каучук не может использоваться в готовых изделиях. Для повышения упругих и других физико-механических свойств в каучуке формируют редкосетчатую молекулярную структуру. Это осуществляют вулканизацией – путём введения в каучук химических веществ – вулканизаторов, образующих поперечные химические связи между звеньями макромолекул каучука (рис. 3, нижний). В зависимости от числа возникших при вулканизации поперечных связей получают резины различной твёрдости – мягкие, средней твёрдости, твёрдые.
Рис. 3 Структуры каучука и резины
Механические свойства резины определяют по результатам испытаний на растяжение и на твёрдость. При вдавливании тупой иглы или стального шарика диаметром 5 мм по значению измеренной деформации оценивают твёрдость (рис. 4).
Рис. 4 Определение твёрдости резины протектора
При испытании на растяжение определяют прочность Ϭz (МПа), относительное удлинение в момент разрыва εz (%) и остаточное относительное удлинение Ѳz (%) (рис. 5).
Рис. 5 Лабораторная установка для проведения механических испытаний резины
В процессе эксплуатации под воздействием внешних факторов (свет, температура, кислород, радиация и др.) резины изменяют свои свойства – стареют. Старение резины оценивают коэффициентом старения Кстар, который определяют, выдерживая стандартизованные образцы в термостате при температуре -70оС в течение 144 час, что соответствует естественному старению резины в течение 3 лет. Морозостойкие резины определяется температурой хрупкости Тхр, при которой резина теряет эластичность и при ударной нагрузке хрупко разрушается.
Для оценки морозостойкости резин используют коэффициент Км, равный отношению удлинения δм образца при температуре замораживания к удлинению δо при комнатной температуре.
Краткие характеристики видов
Сырые резиновые вальцованные смеси представляют собой продукт, прошедший определённый этап обработки. Обычно продаётся такой материал в мешках (30 кг), имеет срок хранения до трёх месяцев. Основной характерной особенностью является то, что материал на финальном этапе изготовления пропускают через вальцы.
Каландрированные сырые резиновые смеси поставляются в рулонах. Толщина раскатанного пласта может составлять 1; 1,5; 2 мм. Основное назначение материалов этого типа – починка шин. Рулоны выпускаются разного веса: по 15; 20; 30 кг. Кроме того, выделяют сырую резину трёх других типов:
- невулканизированная специального назначения;
- общего применения;
- стойкая к маслу и бензину.
Основные компоненты продукта
Натуральный или искусственный каучук – центральный компонент сырой резиновой пластины. В ходе изготовления его просто нагревают до необходимой температуры, то есть состояния, когда он становится максимально мягким, и смешивают с остальными ингредиентами.
Что же добавляют в сырую резину? Существует несколько видов веществ, которые придают резине те свойства, которыми она обладает. Это:
- Ускорители или катализаторы. К ним относится и оксид цинка, отвечающий за скорость, с которой смешиваемые ингредиенты превращаются в готовое изделие;
- Антиокислители и смягчители, которые влияют на процесс скорчинга, а по-простому старения резины. Они нужны, чтобы резиновая смесь не потеряла своей эластичности и, то есть осталась гибкой, податливой и пружинистой как можно дольше.
- Усилители прочностных характеристик, к которым относятся мел и сажа. Такие ингредиенты повышают стойкость и прочность, а также значительно уменьшают себестоимость изделия, ведь снижают количество главного составляющего — природного каучука.
Однако на качестве это не отражается, поэтому добавление различных пластификаторов только приветствуется покупателями.
В целом, на качество такой продукции жалоб не поступает: сырая резина производится по всем нормам и правилам и считается стоящим приобретением, если необходимо регулярно выполнять ремонт дорожек и не только.
Характеристики видов материала
К смесям невулканизированного спецназначения относятся устойчивые к теплу, воздействию масла и бензина электротехнические материалы.
В их состав входит каучук разных видов. В зависимости от типа сырьё может отличаться по эксплуатационным параметрам. Лучшая масло- и бензостойкая смесь получается из хлоропренового каучука. Такие составы поддаются вулканизации без применения серы. Смеси сами по себе получаются очень эластичными, озоностойкими. Сырьё с бутадиен-нитрильным или полисульфидным каучуком характеризуется не настолько хорошим качеством.
Кроме того, масло- и бензостойкие материалы делятся на:
- универсальные.
Их применяют для колец, нижний показатель предела хрупкости – это -50 градусов. Такой сырой резиной вполне возможно заменить другие типы сырья;
- повышенной твёрдости. Используется в производстве для изготовления резинотехнических изделий разного назначения;
- средней упругости. Тоже используются для выпуска РТИ;
- мягкие. Применяют при изготовлении уплотнителей, для работы с агрессивными жидкостями (масло, топливо).
Сырая резина общего назначения производится из каучуков неполярных видов (СКС или НК). Когда в основе натуральное сырьё, то оно подвергается вулканизации серой. Масса с неполярными типами каучуков получается высокого качества. Такие материалы эластичные и прочные, стойкие к деформациям. Из класса синтетических каучуков наиболее часто применяют бутадиен-стирольный тип сырья.
Резиновые смеси: основные характеристики
Сырая резина получила свое распространение благодаря свойствам, которые ей присущи:
- сохраняется высокая степень эластичности и гибкости, как при высоких, так и низких температурах;
- повышенные показатели твердости и прочности;
- стойкость к износу;
- механическим повреждениям;
- воздействиям топлива;
- масла;
- химически активным веществам.
Сырая резина делится на группы по ГОСТ-18829 от 0 до 8, которые могут выдерживать температуры от −60 до +200 градусов. Единственным их недостатком является быстрое физическое старение.
Что такое «сырая» резина и где применяется?
Стоит отметить, что смеси с таким составом – низкого качества. Впрочем, этот показатель напрямую зависит от количества стирола в составе: чем больше этого вещества, тем прочнее получается материал.
Смеси общего назначения бывают повышенной и средней плотности. Первые используют для работы с амортизационными деталями. Резина второй категории идёт на уплотнительные РТИ.
Отдельно стоит упомянуть о смесях, которые предназначены для выполнения ремонтов или работ с восстановленными шинами:
- для заливания в воронки повреждений. Имеют вид длинного шнура диаметром от 8 до 10 мм, используются в экструдерах;
- боковые. Эта резина востребована для починки плечевой области покрышек;
- праймеры – для протектора, каркаса автошин;
- вулканизированные составы в виде лент, прошедших обработку.
Используются для ремонта грузовых и крупногабаритных шин;
- невулканизированные составы, не подвергшиеся обработке. Такую сырую резину берут при наварке протекторов на покрышках в прессах.
Разновидностей сырья действительно много. И в каждом случае оно находит широкое применение в промышленности и при ремонте автопокрышек. С появлением этого материала значительно упростились привычные сегодня процессы починки повреждений на шинах или наварки протектора. А ведь раньше, когда смесей не существовало, мастер-монтажник самостоятельно готовил составы, пригодные для работы. Конечно, это занимало много времени и не гарантировало надёжность, поэтому изобретение сырой резины значительно упростило ремонтные задачи.
Добавлено: 4.12.2017 23:59:30
Что такое вулканизация резины велосипеда в домашних условиях?
Есть несколько способов заделать прокол или порез в велосипедной камере, один из которых – горячая или холодная вулканизация шин. Такой метод можно с уверенностью назвать надежным и долговечным, колесо, закрепленное при помощи сырой резины, будет служить как новое и не спустит в самый неожиданный момент. Осуществлять такой ремонт можно легко самому своими руками, как в домашних условиях, так и на природе в походе при наличии некоторых необходимых деталей. Горячий метод вулканизации отличается от холодного только тем, как закрепляется накладываемая на колесо заплатка – с нагревом или без.
Что такое вулканизация? Это такой химический процесс, благодаря которому, при затрате тепла, прочностные свойства резины улучшаются, она становится эластичной и твердой. Наложить латку на прокол можно при помощи отрезка старой камеры или готовой заплатки из ремонтного набора, а для их закрепления необходима сырая резина своими руками, которая продается в рулонах с защитной пленкой. Это очень пластичный материал, он прилипает к любым поверхностям, легко слепляется в комок и т.д. сырая резина инструкция по применению указана на упаковке.
- Различают два вида вулканизации – холодная и горячая, рассмотрим их оба поподробнее.
Применение сырой резиновой продукции
Чаще всего сырая резина используется для проведения ремонтных работ – именно для этого ее изготавливают в больших количествах и успешно реализуют. Есть несколько основных правил, которых стоит придерживаться, если предстоит работа с этим материалом, а именно:
- Обязательно подготовить края поврежденного места перед ремонтом: зачистить и выровнять поверхность, обезжирить ее, а только потом наносить заплату из сырой резины Такой способ особенно актуален при ремонте камер и покрышек;
- Размер заплаты обязательно должен превышать размер проблемного участка, к тому же каучуковое полотно лучше зафиксировать специальными зажимами и лишь после этого выполнять вулканизацию.
Выполнение таких простых правил и условий позволяет не только избавиться от проблемного участка, но и создать бесшовное покрытие. Именно поэтому сырая резина применяется во многих сферах и даже в строительстве. Каучуковая смесь обладает хорошей адгезией к бетону и кирпичу, поэтому позволяет обрабатывать сложнодоступные места, если необходимо обустроить гидроизоляцию. Такой метод эффективный, а главное – недорогой и не требует больших временных затрат. Он востребован еще и благодаря своей экологичности, а также устойчивости к солнцу и влаге.
Приобрести сырую резину как в листовом, так и в жидком виде можно с помощью . Она отлично подходит для ремонта конвейерных дорожек с помощью горячей вулканизации, поэтому всегда присутствует на складах предприятия. Такая продукция имеет совершенно приемлемую стоимость и отпускается в том количестве, которое удобно клиенту. Для заказа необходимо всего лишь связаться с менеджером и оформить заявку.
Применение холодной вулканизации
Материал для такого ремонта появился еще в 1939 году в США, почти сразу начал с успехом применяться и пользуется популярностью у велосипедистов и автомобилистов по всему миру и по сей день. С его помощью можно легко и беспроблемно отремонтировать любую камеру, холодный способ очень легок к применению в домашних условиях. Для удобства потребителей некоторые производители предлагаются сразу готовые наборы для ремонта (холодная сырая резина инструкция по применению указана на упаковке), в который входят несколько заплаток различных размеров в виде пластыря, шкурка (наждачная бумага), которая используется для зачистки места прокола или царапины на резине, а также специальный быстросохнущий клей для холодной вулканизации. Именно он вступает в реакцию со слоем сырой резины на заплатке – она нанесена ярким цветом вокруг черного. Это вызывает процесс вулканизации, благодаря чему резина камеры легко склеивается без нагрева (т.е. холодным способом). Такой способ лучше всего подходит для ремонта колес в походных условиях, когда под рукой больше нет никаких инструментов. Вы не найдете ни одного велотуриста, которого бы не выручал подобный комплект хотя бы раз в жизни. Он не занимает много места в сумке или рюкзаке, а важность его сложно переоценить, особенно если в поездке вы один без товарищей вдалеке от города. На весь процесс ремонта шины с использованием холодной вулканизации при помощи латки пластыря для камеры у велосипедиста уйдет не больше десяти минут, и колесо будет как новое.
Технология горячей вулканизации шин своими руками
Такая технология применяется несколько дольше, чем холодная. Во времена, когда вокруг не было такого количества шиномонтажек, авто- и велолюбители ремонтировали свои транспортные средства в гараже при помощи именно такого метода, для которого применяется электрический или бензиновый вулканизатор, который можно легко собрать своими руками. технология здесь заключается в следующем: мастер сжигает бензин, который прогревает резину при помощи поршня. Как только температура поднимается до 90 градусов, сырая резина для вулканизации начинает укрепляться, если поднять температуру до 147 градусов, процесс идет заметно быстрее и качественнее. А вот выше 150 лучше не поднимать, т.к. материал начинается разрушаться и теряет свои свойства. После 160 градусов сырая резина начинается обугливаться. Идеальное время прогрева при горячей вулканизации сырой резины – около 8-10 минут. Фрагмент материала прикладывается к месту прокола на камере и сдавливается при помощи струбцины, чтобы в процессе химической реакции не образовывались пузырьки и не собирался воздух, образуя опасные пустоты.
Технология применения горячей вулканизации сырой резины в домашних условиях окажется на 40% эффективнее для шины, чем холодная, поэтому, если есть возможность, пользоваться лучше этим методом.
В походных условиях провести такую операцию для камер гораздо сложнее, но все же возможно: если есть фрагмент сырой резины, можно нагреть его над костром. Определить температуру пламени можно по кусочку сахара или листку бумаги: и то, и то начинает плавиться/обугливаться при температуре 145 градусов – как раз той, что требуется для вулканизации. В качестве струбцины можно использовать плоский тяжелый камень, деревянное полено или любой другой подходящий предмет.
На всю операцию вы потратите около 20 минут. Не забывайте, что место проклейки заплатки камеры нужно обязательно зачищать шкуркой или хотя бы протереть бензином, чтобы удалить загрязнения с шины.
Резины для низких температур
С понижением температуры уплотнения теряют свои эластичные свойства. При дальнейшем снижении температуры ниже нуля градусов Цельсия уплотнители начинают затвердевать и становятся хрупкими как стекло. При отсутствии предельных механических нагрузок и последующем повышении температуры до нормальных значений резины восстанавливают свои первоначальные свойства. Возможная небольшая компенсация ухудшения этих характеристик резин при отрицательных температурах может наблюдаться при работе в жидкостях, которые вызывают некоторое разбухание или размягчение материала. На практике уплотнения из резины для неподвижных соединений могут применяться ниже минимальной предельной температуры для данного эластомера.
Для низкотемпературных условий следует выбирать силиконовую или фторсиликоновую резину, однако эти материалы имеют неудовлетворительную стойкость к механическому износу, что следует учитывать при конструировании и модернизации уплотнений. Поэтому для низких температур рациональный выбор делают в пользу резин на основе этилен-пропилен-диенового каучука [EPDM] или специальных нитрильных резин .
Реальные значения сроков службы резиновых уплотнителей при отрицательных температурах зависят от особенностей конструкции уплотнения, условий эксплуатации и параметров рабочей среды.
Цемент для вулканизации и его применение
Еще один альтернативный вариант для ремонта колес велосипеда в походных условиях – это баллончик с цементным вулканизатором. Купить их можно, например, на авторынке – такой материал пользуется большой популярностью среди автолюбителей. Состав продается в жестяных и аэрозольных баллонах под давлением от таких брендов как Abro, BL, Zefal, Top RAD и многих других. По своему составу они не опасны для здоровья и не токсичны, т.к. в них не содержится хлористый и ароматический углеводород, поэтому использовать их можно свободно и дома, и на улице без защитной маски. Для того чтобы произошла цементация шины, необходима температура в 18 градусов тепла. Состав также применяется и при горячей вулканизации (необходимо 150 градусов). Для ремонта нужно извлечь из резины камеры инородный предмет, спровоцировавший прокол, через ниппель заправить камеру цементным вулканизатором, слегка подкачать ее насосом и проехать на велосипеде 2-3 километра, чтобы отрегулировать давление в колесах. Такая технология ремонта шины простая и тоже применяется повсеместно. Для закрепления результата возможно использование заплатки пластыря с последующим методом горячей вулканизации – абсолютно так же, как описывает инструкция выше. Технология подходит для любых порезов шины.
латка для ремонта камер в данном случае наносится до заправки шины цементом.
Что такое натуральный каучук и почему мы ищем новые источники? · Границы для молодых умов
Аннотация
Что такое резина и откуда она берется? Каучук — это натуральный продукт, производимый растениями, и он присутствует во многих товарах, используемых в нашей повседневной жизни. Каучук играл важную роль в истории человечества, на протяжении всего развития человеческих цивилизаций. Он по-прежнему играет важную роль, и поэтому нам необходимо искать новые источники каучука.В настоящее время 99% используемого нами натурального каучука добывается из дерева под названием Hevea brasiliensis . В этой статье мы подробно расскажем о лучших альтернативных источниках резины, доступных в настоящее время.
Что такое натуральный каучук?
Натуральный каучук производится на заводах и классифицируется как полимер . Полимер — это химическое соединение с большими молекулами, состоящими из множества более мелких молекул одного вида. Некоторые полимеры существуют в природе, а другие производятся в лабораториях и на фабриках.
Натуральный каучук — один из важнейших полимеров для человеческого общества. Натуральный каучук является важным сырьем, используемым при создании более 40 000 продуктов. Он используется в медицинских устройствах, хирургических перчатках, авиационных и автомобильных шинах, пустышках, одежде, игрушках и т. Д. Натуральный каучук получают из латекса , молочной жидкости, присутствующей либо в латексных сосудах (каналах), либо в клетках резины. -производящие растения. Около 20000 видов растений производят латекс, но только 2500 видов содержат каучук в латексе.Биологическая функция каучука для растений до конца не изучена. Однако было показано, что каучук может помочь растениям заживать после повреждения, покрывая раны и останавливая кровотечение. Это блокирует попадание вредных бактерий и вирусов в растения.
Свойства резины включают высокую прочность и способность многократно растягиваться без разрушения. Смеси натурального каучука исключительно гибкие, хорошие электроизоляторы и устойчивы ко многим агрессивным веществам [1].
Синтетический (искусственный) каучук может быть произведен с помощью химического процесса, но люди не смогли произвести синтетический каучук, обладающий всеми свойствами натурального каучука. Таким образом, натуральный каучук невозможно заменить синтетическим каучуком в большинстве областей его применения. Вот почему натуральный каучук по-прежнему очень важен для человеческого общества [2].
История натурального каучука
Еще в 1600 году до нашей эры мезоамериканские народы в Мексике и Центральной Америке использовали жидкий каучук для лекарств, в ритуалах и для рисования.Только после завоевания Америки каучук стал использоваться в западном мире. Христофор Колумб был ответственным за открытие каучука в начале 1490-х годов. Коренные жители Гаити играли в футбол с мячом, сделанным из резины, а позже, в 1615 году, Фрай Хуан де Торквемада написал о коренных и испанских поселенцах Южной Америки, носящих обувь, одежду и головные уборы, сделанные путем окунания ткани в латекс, что делает эти предметы более прочными и водонепроницаемыми. . Но с резиной были проблемы: она становилась липкой в теплую погоду, затвердевала и трескалась в холодную погоду.
Спустя столетие, в 1734 году, Шарль Мари де ла Кондамин отправился в путешествие по Южной Америке. Там он обнаружил два разных дерева, содержащих латекс: Hevea brasiliensis (рис. 1B) и Castilla elastica [3], но только первое стало важным источником натурального каучука. Причина, по которой дерево гевеи преуспела над деревом Кастилья, заключалась в способе транспортировки латекса по стволу. Дерево гевеи соединило латексные трубки (рис. 1А), которые образуют сеть, тогда как дерево Кастилия не образует связанную систему.Благодаря подключенной системе, дерево гевеи истекает латексом, когда на его стволе делается специальный разрез (рис. 2). Без латексных трубок дерево Кастилья не пропускает латекс, что затрудняет сбор каучука.
- Рисунок 1 — (A) Hevea brasiliensis сечение ствола и увеличение продольного сечения соединенных трубок.
- (B) A Hevea brasiliensis плантация и рисунок листьев, цветов и плодов этого растения.
- Рисунок 2 — Hevea brasiliensis , со специальным разрезом для извлечения латекса.
В 1839 году Чарльз Гудиер изобрел процесс вулканизации , решив многие проблемы, связанные с резиной. Вулканизация — это процесс обработки резины серой и нагреванием для ее упрочнения с сохранением ее эластичности. Он предотвращает плавление резины летом и растрескивание зимой. Через несколько лет после этого важного открытия, в 1888 году, Данлоп изобрел резиновую шину с воздушным наполнением, сделав резину чрезвычайно важным сырьем во всем мире.Резина стала важным материалом для промышленной революции.
С 1850 по 1920 год бизнесмены подталкивали предпринимателей и торговцев к увеличению количества каучука, добываемого из амазонских деревьев. В этот период бразильская Амазонка была единственным источником каучука, и они контролировали цены, что делало каучук дорогим. В то же время, по мере того, как все больше и больше промышленности развивались в Европе и США, находили все большее применение каучук [4]. Каучук был настолько важным материалом для бразильцев, что они запретили экспорт семян или саженцев каучука.Однако в 1876 году Х. А. Уикхему удалось контрабандой переправить 70 000 семян каучука, спрятанных в банановых листьях, и доставить их в Англию. Из этих семян уцелело только 1900 саженцев, которые были отправлены в Малайзию, чтобы заложить первые каучуковые плантации в Азии. Это стало началом конца для Бразилии как главного производителя каучука в мире. Спустя 12 лет производство каучука на новых плантациях в Малайзии стало таким же конкурентоспособным, как и на плантациях Амазонки, и вскоре эти плантации стали основным мировым поставщиком натурального каучука (рис. 3).
- Рис. 3 — (A) Hevea brasiliensis возникла в Амазонии и попала в Малайзию, основного производителя натурального каучука.
- (B) Hevea brasiliensis .
(C) Альтернативный источник каучука, гваюла ( Parthenium argentatum ). (D) Альтернативный источник каучука, одуванчик казахский ( Taraxacum koksaghyz ).
Генри Николас Ридли был ученым, который в 1888 году стал директором Сингапурского ботанического сада.Работая там, он нашел первые 11 каучуковых деревьев, которые были посажены в Малайзии, и начал продвигать создание плантаций каучуковых деревьев. Некоторое время спустя он разработал революционный метод сбора латекса с дерева Hevea путем непрерывного постукивания. Постукивание — это процесс удаления латекса с дерева. Это открытие позволило достичь гораздо более высокого выхода латекса, и каучук стал важным материалом в развитии Сингапура. Новые плантации были более конкурентоспособными по цене, поэтому с конца девятнадцатого века до Первой мировой войны сбор каучука из диких источников в тропической Америке резко сократился.Во время войны подача резины была прекращена. США, Германия и Россия начали поиск альтернативных источников каучука, натурального или синтетического, поскольку деревья Амазонки не давали достаточно каучука для их нужд [3]. В этих странах было начато несколько исследовательских программ, но после войны поставки каучука с малазийских плантаций возобновились, и усилия по поиску новых источников каучука почти прекратились.
В настоящее время около 90% натурального каучука производится в Азии, причем Таиланд и Индонезия являются наиболее важными поставщиками каучука (поставляя более 60% натурального каучука в мире).
Почему мы ищем новые источники каучука?
В последние годы снова начались поиски альтернативных источников каучука. Для этого есть три основных причины:
1. Угрозы дереву Hevea brasiliensis и его производству каучука
Прежде всего, каучуковые деревья подвержены нескольким болезням, а поскольку азиатские каучуковые плантации начинались с небольшого количества семян, все деревья генетически очень похожи. Меньшая генетическая изменчивость означает меньшую способность бороться с болезнями растений.Если одно дерево заболевает, болезнь может быстро распространиться на всю плантацию. Сегодня наиболее серьезным и опасным заболеванием, которым страдает Hevea brasiliensis , является южноамериканский фитофтороз. Эта болезнь может вызвать разрушение целой плантации. Он по-прежнему ограничен тропической Америкой, но если он попадет в Азию, это может означать конец каучуковых плантаций. В естественных условиях каучуковые деревья обычно растут с большим пространством между ними.В природе серьезное повреждение гевеи гевеи в результате ожога листьев в Южной Америке является необычным, потому что другие виды деревьев, растущие между каучуковыми деревьями, не восприимчивы к болезни и действуют как барьеры. Но на плантациях, где каучуковые деревья растут очень близко друг к другу, это может привести к летальному исходу.
Во-вторых, серьезной угрозой для рынка натурального каучука является очень конкурентный и быстрорастущий рынок пальмового масла и его побочных продуктов. Растет спрос как на каучук, так и на пальмовое масло, но в Малайзии площадь выращивания Hevea brasiliensis не уменьшается, однако площади, предназначенные для выращивания масличной пальмы, увеличиваются.Если непрерывный рост плантаций масличных пальм не прекратится, естественный лес или плантации гевеи должны будут стать меньше, чтобы освободить место для новых культур масличных пальм.
И, наконец, что не менее важно, метчик резины — работа малооплачиваемая и трудная. Молодые люди склонны выбирать более привлекательную работу, что может привести к нехватке квалифицированных сборщиков каучука.
2. Резина из Hevea brasiliensis может вызывать серьезную аллергию
Латексные протеины в каучуке, изготовленном из Hevea brasiliensis , могут вызывать у некоторых людей тяжелую аллергию, даже если они подвергаются воздействию очень малых количеств.Белки латекса очень трудно отделить от каучука в процессе очистки. Поскольку эти аллергии могут быть очень опасными, альтернатива каучуку, не содержащая этих латексных белков, была бы предпочтительной.
3. Hevea brasiliensis производится только на одном участке
Условия, необходимые для выращивания каучуковых деревьев, очень специфичны и встречаются только в определенных регионах мира. Большая часть нашего натурального каучука производится в небольшом регионе Азии, что делает его поставки уязвимыми.Если азиатские плантации не смогут производить достаточно каучука, запасов каучука может оказаться недостаточно для удовлетворения мировых потребностей. Было бы полезно найти другие заводы по производству каучука, которые можно было бы выращивать в других частях света.
Есть ли альтернативные источники каучука?
Не все каучуковые заводы производят каучук хорошего качества. Некоторые растения, которые считались альтернативными источниками каучука, — это гваюла, русский одуванчик, резиновая кисть для кроликов, золотарник, подсолнечник, фиговое дерево и салат.Два из этих растений кажутся лучшей альтернативой Hevea brasiliensis : гваюле и русскому одуванчику.
Гуаюле ( Parthenium argentatum ) — кустарник, произрастающий в районе северного плато в Мексике, который обычно растет на известняковых почвах в районах с очень низким уровнем осадков (рис. 3C). Гуаюле лучше всего растет при температуре от 18 до 49,5 ° C. В этих условиях он может прожить 30–40 лет. Каучук содержится в стеблях и корнях гваюли, а также в отдельных клетках растения, а не в латексных сосудах или трубках.Содержание каучука в гваюле увеличивается в течение нескольких лет. Менее 1% каучука в мире производится из гваюли. Каучук этого растения изучается для биомедицинских применений, потому что он не вызывает аллергии. Чтобы извлечь каучук из растения, ткань гваюлы должна быть тщательно размягчена и раздроблена, чтобы высвободить частицы каучука, содержащиеся в отдельных клетках. Качество каучука из гваюли недостаточно для всех целей, поскольку в нем больше примесей, чем в каучуке из Hevea brasiliensis .
Другой хороший вариант для каучука, русского или казахского одуванчика ( Taraxacum koksaghyz ) — это быстрорастущее растение с высококачественным каучуком, которое было обнаружено в 1931 году в Казахстане (Рисунок 3D). Одуванчик казак растет очень близко к земле, его можно выращивать в регионах с умеренной температурой, и он дает желтые цветочные головки (они выглядят как цветок, но представляют собой густую группу маленьких цветков без стебля). Одуванчик казахский содержит каучук в листьях, цветах и корнях, но только каучук из корней подходит для экстракции из-за его более высокого качества и количества.Для экстракции каучука российские одуванчики необходимо прессовать или смешать [5]. У казахских одуванчиков есть еще одно преимущество — они также производят углевод, называемый инулин, который является веществом, которое можно использовать в пищевых продуктах, а также для производства лекарств от рака, биотоплива или даже биопластика (пластика, сделанного из натуральных продуктов). На данный момент извлекать каучук из казахских одуванчиков все еще слишком дорого. Надеемся, что благодаря исследованиям можно вывести растение с более крупной корневой системой и более высоким содержанием каучука.
Заключение
Несмотря на то, что каучуковое дерево является лучшим источником каучука, доступным сегодня, оно сталкивается с некоторыми серьезными угрозами. Каучук производится только из растений, выращенных в определенных уникальных областях. Чтобы расширить источники натурального каучука и избежать опасностей ограниченного производства, мы должны искать новые каучуковые заводы и улучшать уже известные, чтобы попытаться сделать их экономически конкурентоспособными.
Глоссарий
Полимер : ↑ Химическое соединение, большие молекулы которого состоят из множества более мелких молекул одного вида.Некоторые полимеры существуют в природе, а другие производятся в лабораториях и на фабриках.
Латекс : ↑ Беловатая жидкость молочного цвета, содержащая белки, крахмал, алкалоиды и т. Д., Вырабатываемая многими растениями. В некоторых растениях он также содержит каучук.
Hevea Brasiliensis : ↑ Это дерево, произрастающее на Амазонке. Это очень важно с экономической точки зрения, потому что латекс, собранный с дерева, является основным источником натурального каучука.
Вулканизация : ↑ Процесс обработки резины серой и нагреванием с целью ее упрочнения с сохранением ее эластичности.
Rubber Tapping : ↑ Процесс сбора латекса с каучукового дерева. Перед восходом солнца в коре дерева делают канавку для сбора, а латекс собирают ближе к вечеру.
Удаление резины : ↑ Действие по извлечению или отделению резины от ткани корня.
Заявление о конфликте интересов
Авторы заявляют, что исследование проводилось при отсутствии каких-либо коммерческих или финансовых отношений, которые могут быть истолкованы как потенциальный конфликт интересов.
Благодарности
Мы хотели бы поблагодарить Наталью Карреро, Лору Баркер и Марселя Принса за их вклад в рецензирование текста.
Проект AIR получил финансирование в рамках исследовательской и инновационной программы Европейского Союза Horizon 2020 в рамках грантового соглашения Марии Склодовской-Кюри № 752921.
Список литературы
[1] ↑ Виджаярам Т. Р. 2009. Технический обзор резины. Внутр. J. Des. Manuf. Tech. 3: 25–36.
[2] ↑ ван Бейлен Дж., Пуарье Ю. 2007. Гуаюле и русский одуванчик как альтернативные источники натурального каучука. Крит. Rev. Biotech. 27: 217–31. DOI: 10.1080 / 07388550701775927
[3] ↑ Whaley, W. G. 1948. Каучук — основной источник для американского производства. Экон. Бот. 2: 198–216. DOI: 10.1007 / BF02859004
[4] ↑ Уллан де ла Роса, Ф. Дж. 2004. La era del caucho en el Amazonas (1870–1920): modelos de explotación y relaciones sociales de producción. Анал. Mus. Являюсь. 12: 183–204.
[5] ↑ van Beilen, J. , and Poirier, Y. 2007. Выращивание новых культур для производства натурального каучука. Trends Biotechnol. 25: 522–9. DOI: 10.1016 / j.tibtech.2007.08.009
Натуральный каучук — Служба транспортной информации
Информация о продукте
Название продукта
Немецкий | Натуркаучук |
Английский | Натуральный каучук (NR) |
французский | Каучук натуральный |
Испанский | Caucho натуральный |
Номер CN / HS * | 4001 и далее. |
(* Комбинированная номенклатура / Гармонизированная система ЕС)
Описание продукта
Каучук — собирательный термин для высокомолекулярных веществ природного или синтетического происхождения (натуральный каучук или синтетический каучук).
Натуральный каучук (сокращенно NR) в основном состоит из полиизопрена и собирается из молочно-белого латекса ряда видов растений, произрастающих в тропиках, в первую очередь семейства молочайных (Euphorbiaceae).Каучуковое дерево (Hevea brasiliensis) приобрело большое коммерческое значение. Это дерево произрастает в регионе Амазонки и в настоящее время культивируется практически во всех тропических регионах Южной Америки, Африки и Азии. 90% мирового производства натурального каучука производится из каучукового дерева.
В коре делают диагональный разрез, позволяющий латексу выделяться. Латекс имеет примерно следующий состав:
Состав | В процентах |
Вода | 55… 70 |
Резина | 30… 40 |
Смолы | 1.5… 2 |
Белок | 1,5… 3 |
Ясень | 0,5… 1 |
Сахар | 1… 2 |
Латекс, богатый каучуком, можно консервировать путем добавления аммиака и для специальных целей его можно транспортировать в страны, в которых он перерабатывается, в виде концентрата латекса в жидкой форме. Это делается в бочках или в танк-контейнерах. Гораздо более распространено фильтровать собранный латекс, разбавлять его водой, а затем заставлять его коагулировать с помощью таких веществ, как уксусная кислота или муравьиная кислота, или с помощью электрофореза.Это отделяет сырой натуральный каучук от воды, образуя твердую массу (коагулят), которую затем обрабатывают. Коагуляция также может происходить в форме самокоагуляции на панели для отбора (кружево дерева) и сборных чашках (отходы скорлупы и комки чашек). Такой коагулянт имеет более высокую степень загрязнения и, следовательно, используется в сортах натурального каучука, которые имеют менее строгие требования в отношении загрязнения.
Различают следующие виды натурального каучука:
Блинчики | |
Бледный креп каучук — один из самых качественных крепов.Коагуляция этого высококачественного натурального каучука достигается гидросульфитом натрия (NaHSO 3 ).![]() Избыточные температуры приводят к появлению пятен на листах обесцвечивания в результате окисления.Листы упаковываются в тюки и продаются как «тонкий светлый креп». 10-миллиметровый креп из Шри-Ланки продается как «толстый светлый креп». |
л. | ||
Различают два разных типа листов: | ||
ADS (листы воздушной сушки) Простыни, высушенные на воздухе, встречаются реже. По внешнему виду они похожи на RSS (ребристые дымчатые листы), но более прозрачны, так как производятся в помещениях, свободных от табачного дыма. ![]() | ||
RSS (ребристые дымчатые листы) (см. Рисунок 1) Свежий латекс разбавляют до содержания каучука 15-16% и коагулируют в резервуарах для коагуляции с использованием муравьиной кислоты или уксусной кислоты. Комки сгустка образуются после того, как кислота подействует в течение 3-4 часов. После фрезерования и промывки получаются листы толщиной от 2,5 до 3,5 мм, шириной 24 см и длиной 90 или 135 см. Последний стан — это тисненый стан, который придает листам ребристую структуру.Поскольку эти резиновые листы моются не так интенсивно, как крепы, они содержат более высокую долю компонентов сыворотки, которые вызывают появление плесени и гниения. По этой причине листы проходят дополнительный процесс консервации, в ходе которого их коптят в коптильнях. Листы вывешиваются в коптильнях и сушатся неделю при температуре до 60 ° C. Дым от сжигания древесины гевеи (каучукового дерева) и других органических материалов, таких как кокосовая шелуха, сохраняет листы. ![]() Рисунок 1: Производство ребристых копченых листов |
Технически заданный натуральный каучук (TSR) — Стандартный каучук | |||||||||
TSR делятся на несколько классов, которые изложены в технических спецификациях, разработанных ISO, и производятся с использованием новых технологий обработки.В зависимости от качества TSR используются различные формы коагулята: латекс, коагулированный естественным путем в сборных чашках (комки чашек), резиновые листы или латекс, коагулированный с добавлением кислоты. Для создания TSR используются разные методы, например: процессы Heveacrumb или Dynat. В процессе Heveacrumb каучуковый коагулят пропускают через крепирующие валки, настроенные на скорость трения, и задействованные силы сдвига разрывают сгусток на мелкие кусочки. В процессе Dynat в основном используются куски чашки.После естественной или кислотной коагуляции каучук гранулируется с помощью резака с вращающимся ножом. После гранулирования крошку промывают и сушат при повышенной температуре до 140ºС. Затем крошки прессуют в блоки по 33 1/3 кг, заворачивают в полиэтиленовую пленку (высококачественные полиэтиленовые пакеты) и расфасовывают в деревянные или стальные ящики. [69] Преимущества технически заданных каучуков перед обычными листовыми и креповыми каучуками следующие:
|
Консервированные концентраты латекса | |
В латекс добавляют аммиак, чтобы он оставался жидким, и его концентрируют путем взбивания или центрифугирования. Полученный концентрат можно транспортировать в жидком виде. В зависимости от количества добавленного аммиака различают латекс с высоким содержанием аммиака (HA) с 0,60-0,80% аммиака и латекс с низким содержанием аммиака (LA) с 0.![]() |
Латекс можно перерабатывать для производства других резиновых изделий:
Обезжиренная резина | |
Обезжиренный каучук производится из обезжиренного латекса. Обезжиренный латекс производится как побочный продукт при приготовлении концентрата латекса. Его содержание в сухом каучуке составляет всего от 3 до 7%. Однако он также имеет очень низкое содержание грязи. Коагуляция обезжиренного латекса может быть спонтанной или обработкой кислотой.Важно поддерживать как можно более низкое содержание аммиака. Дальнейшая обработка такая же, как и для копченого листа. [69] |
Резиновый порошок | |
Чтобы снизить транспортные расходы, латекс можно превратить в тонкий резиновый порошок вместо того, чтобы транспортировать его в виде концентратов латекса.![]() |
Качество / Срок хранения
л. | |
Ребристые дымчатые листы классифицируются на основе визуальной оценки (RSS IX, RSS 1, RSS 2, RSS 3, RSS 4 и RSS 5). Марки были описаны в Зеленой книге, опубликованной Международной конференцией по качеству и упаковке резины. Перед сортировкой листы разделяются и проверяются. Окисленные пятна или полосы, непрочные, нагретые, недоотвержденные, перегоревшие, непрозрачные и обгоревшие листы недопустимы. RSS IX — высший сорт. Резина должна быть предоставлена производителем в отличном качестве сушки. Резина должна быть сухой, чистой, прочной, доброкачественной и равномерно прокуренной, без пятен, пятен, ржавчины, пузырей, песка, грязной упаковки и любых других посторонних предметов. Остальные классы RSS 1 — RSS 5 представляют собой последовательное снятие этих требований. Недостаточно затвердевшая резина показывает пятна, которые не были достаточно высушены во время копчения или сушки. |
Старение натурального каучука
Процессы старения резины, особенно в результате атмосферных условий, могут начаться еще на этапе транспортировки и отрицательно повлиять на качество резины: воздействие кислорода, тепла и света являются основными причинами симптомов старения, а ведущими являются процессы окисления. к образованию гидроксидов. Они, в свою очередь, реагируют либо расщеплением молекул, либо установлением новых поперечных связей. Результат — размягчение или затвердевание: окисленная резина.
Отвердение натурального каучука во время транспортировки и хранения можно предотвратить добавлением химических веществ (гидрохлорид гидроиламина) для достижения постоянной вязкости. [69]
Рекомендуемая продолжительность хранения для натурального каучука [72]
Первоначальное хранение | 5 лет |
Расширенное хранилище | 2 года |
Рекомендуемая температура хранения для натурального каучука [73]
Оптимальная температура хранения | 15-30 ° С |
Хранение латексных концентратов [71]
Макс.продолжительность хранения | 6-12 месяцев |
Температура хранения и транспортировки | 5-35 ° С |
Использование по назначению
Натуральный каучук может применяться в самых разных областях по всему миру. Уникальное сочетание свойств натурального каучука невозможно полностью воспроизвести синтетически. Однако каждое отдельное свойство можно улучшить с помощью (синтетического каучука).
Обработка натурального каучука для изготовления резиновых изделий
Натуральный каучук смешивают с различными добавками, предназначенными для придания конечному продукту требуемых свойств, формуют и затем вулканизируют (см. Рисунок 3).
Рисунок 3: Схема, показывающая переработку резины [70]
Мастикация — это предварительная стадия обработки каучука-сырца. Этот процесс включает использование специального механического оборудования и добавок (например, ароматических меркаптанов — серосодержащих соединений) при низких температурах для измельчения молекул каучука на более мелкие единицы. Это улучшает пластичность и снижает вязкость.
После жевания каучук смешивают с наполнителями, пластификаторами и химическими веществами для каучука до образования однородной массы в мельницах или закрытых месильных машинах.
Последующий конечный продукт предварительно формуют прессованием, литьем под давлением или каландрированием. Например, пресс-формовочные машины используются для производства автомобильных шин, подошв и каблуков для обуви и пробок. Например, тонкие бесшовные резиновые изделия изготавливаются методом окунания.
На заключительном этапе обработки формованная резиновая смесь вулканизируется. Самая важная среда вулканизации — сера, которая добавляется к резиновой смеси перед ее нагреванием.
Шинная промышленность является крупнейшим потребителем натурального каучука в мире.Шины для автомобилей, велосипедов и самолетов, а также многие другие виды резиновых изделий, такие как уплотнения, шланги, приводные ремни, напольные покрытия, конвейерные ленты, формованные изделия, поролон, пропиточные вещества и медицинское оборудование, изготавливаются из натурального каучука.
Фигуры
(Щелкните отдельные рисунки, чтобы увеличить их.)
Рисунок 4 | Рисунок 5 |
Страны происхождения
Европа | |
Африка | Кот-д’Ивуар, Гана, Камерун, Либерия, Нигерия, другие прибрежные страны Западной Африки |
Азия | Китай, Индия, Индонезия, Камбоджа, Малайзия, Филиппины, Шри-Ланка, Таиланд, Вьетнам |
Америка | Бразилия |
Австралия |
В этой таблице показаны только некоторые из наиболее важных стран происхождения, и ее не следует рассматривать как исчерпывающую.
Юго-Восточная Азия производит около 80% мирового натурального каучука. Остальная часть делится между Юго-Западной Азией, Африкой и Латинской Америкой.
В начало
Упаковка
Блинчики | |||
Светлый креп-каучук либо упакован в двухслойный мешок (полиэтиленовая пленка внутри, бумага снаружи), либо тюки завернуты в полиэтиленовую пленку и упакованы в деревянные ящики.Более толстые блины также можно упаковать в мешковину. Вся поверхность тюка должна быть покрыта достаточным количеством талька, чтобы волокна не прилипали к резине. | |||
л. | |||
Резиновые листы складываются в тюки (например, 60 см х 60 см и 100-113 кг на тюк), сжимаются и упаковываются в защитные листы. На поверхность наносится защитное покрытие и тальк для защиты от окисления и предотвращения прилипания листов друг к другу.![]()
Листы также можно просто сложить и упаковать в полиэтиленовые пакеты в виде тюков по 35 кг. 36 тюков вместе образуют грузовую единицу весом 1260 кг на поддон. Они объединяются в термоусадочную пленку или полиэтиленовую пленку. Также можно использовать металлические ящики. | |||
Технически заданный натуральный каучук (TSR) — Стандартный каучук | |||
TSR упакованы индивидуально в полиэтиленовую пленку (полиэтилен) и укладываются на поддоны. Они объединяются в термоусадочную пленку или кожух из пластиковой пленки, а также прикрепляются к поддону с помощью пластиковой ленты (см.![]()
В качестве альтернативы, TSR можно упаковать в деревянные или стальные ящики и закрепить на поддонах (см. Рисунок 3). Ящики объединяются в блоки путем крепления к поддону стальными ремнями.
TSR обычно упаковываются в тюки по 33 1/3 кг. Обычно на поддон загружается 36 тюков. | |||
Концентрат латексный | |||
Концентраты латексные фасуются в цистерны, бочки и малогабаритные емкости.Емкость бочки обычно составляет 205 кг. [69] |
Когда используются деревянные упаковочные контейнеры или материалы для крепления груза, при определенных обстоятельствах может потребоваться соблюдение карантинных правил страны назначения (правила ввоза упаковочных контейнеров из цельной древесины — стандарт IPPC) и фитосанитарный сертификат может быть приложен к товаросопроводительным документам. Информацию можно получить в фитосанитарных органах заинтересованных стран.
Вернуться к началу
Транспорт
Обозначения
Генеральные грузы | Наливные грузы (латексные концентраты) | Пожарная опасность (легковоспламеняющиеся твердые вещества) Класс 4.1 Код IMDG (относится к резиновому лому и остатку) |
Транспортные средства
Судно, грузовик, железная дорога
Контейнерные перевозки
Стандартные контейнеры следует использовать при соблюдении лимитов по влагосодержанию товаров и упаковки.Идеальные условия будут обеспечены изолированными контейнерами или открытыми контейнерами в хорошо вентилируемых нижних трюмах (защита от солнечного излучения и колебаний температуры).
Контейнеры-цистерны для резины в жидком виде.
Обработка груза
Груз нельзя обрабатывать, если идет дождь или снег.
Фактор укладки
Требования к складскому пространству
При морских перевозках натуральный каучук предпочтительно размещать под палубой. Трюмы / контейнеры должны быть сухими, чистыми и беспыльными.Не храните рядом с источниками тепла.
Изоляция
Волоконный трос, сетки из тонкого волокна или маркировка используются для целей сегрегации.
Крепление груза
Из-за его значительной чувствительности к ударам и давлению, упаковки с этим грузом должны быть закреплены таким образом, чтобы не допустить их повреждения друг друга. Пространства между упаковками или поддонами должны быть заполнены, чтобы предотвратить соскальзывание или опрокидывание. Выбрав правильный размер упаковки или грузовую единицу (модуль площади или несколько модулей площади), трюмы могут быть плотно загружены (без мест).
Вернуться к началу
Факторы риска и предотвращение потерь
RF Температура
Натуральный каучук требует определенной температуры, влажности / влажности и, возможно, условий вентиляции (SC VI) (климатические условия хранения).
Срок | Диапазон температур | Источник |
Оптимальный температурный диапазон движения | 5-25 ° С | [1] |
Оптимальная температура движения | 20 ° С | [1] |
Температуры выше 30 ° C и воздействие солнечного света даже в течение нескольких часов приводят к активации бактерий, вызывающих гниение, особенно в сочетании с влагой и белками.Кроме того, поощряется окисление и связанный с ним молекулярный распад, и на резине появляются мягкие пятна, липкость и она деформируется (окисленная резина).
Если пункт назначения находится в более холодном климате, тюки застревают из-за падения температуры, и это затрудняет разгрузку контейнера или транспортного средства. На рисунках 9 и 10 показаны типичные температурные условия во время рейса из Сингапура в Европу. При этом самые высокие температуры зафиксированы в Аденском заливе и в Красном море. Так как нельзя превышать температуру 30 ° C (критическая температура движения), контейнеры по возможности следует размещать под палубой. Оптимальная температура перемещения резины — 20 ° C. Температура 25 ° C должна поддерживаться практически постоянно в течение длительного периода. Это значение было зарегистрировано как верхний предел температуры перемещения на рисунках 6 и 7.
Рисунок 9 | Рисунок 10 |
Резина начинает плавиться прибл.180 ° С.
Нижний предел составляет 5 — 6 ° C, так как существует опасность затвердевания в результате кристаллизации. Это может вызвать трудности при разгрузке контейнера или транспортного средства, поскольку застрявшие тюки порвутся.
Концентраты латекса также следует защищать от экстремальных температур во время транспортировки и хранения. Если бочки подвергаются воздействию прямых солнечных лучей в тропическом и субтропическом климате, высокие температуры могут привести к снижению качества.
При температуре ниже 4 ° C концентраты латекса склонны коагулировать, что является необратимым процессом.Это приводит к трудностям при разгрузке, повреждению и дополнительным расходам. [74]
Вернуться к началу
RF Влажность / влажность
Натуральный каучук требует определенной температуры, влажности / влажности и, возможно, условий вентиляции (SC VI) (климатические условия хранения).
Содержание воды в каучуке составляет 1,08%, поэтому каучук с низким содержанием воды относится к классу влагосодержания 1 (WCC 1) (классы содержания воды).
Необходимо строго избегать попадания влаги из-за дождя, морской воды или конденсата, поскольку это может привести к гниению, плесени, пятнам плесени и обесцвечиванию.Резина, которая намокла и впитала слишком много влаги, называется отбеленной резиной.
Натуральный каучук не гигроскопичен. Плохая теплопроводность резины может привести к конденсации на поверхности капиллярной воды, что, в свою очередь, приводит к образованию плесени и гниению.
Поскольку в середине грузового блока могут образовываться пятна плесени и грибка, невозможно обнаружить повреждения при приемке партии груза. Это можно обнаружить только при разгрузке контейнера или транспортного средства.
Повреждение от влаги сопровождается неприятным или резким запахом.
В любом случае повреждения всегда должен задаваться вопрос о том, была ли резина влажной с самого начала, т. Е. Было ли это случайным повреждением, за которое несет ответственность производитель, или повреждение произошло во время транспортировки, поскольку в результате дождя, конденсата или морской воды (в случае загрузки на палубу негерметичных контейнеров). Микробиологический анализ продукта, описанный профессором Штанчевым (см. Влагостойкость натурального каучука — только на немецком языке), может использоваться для определения времени появления влаги.Учитываются три аспекта:
Наблюдение за стадиями роста плесени | |
Температурные требования формы | |
Потребность микроорганизмов в кислороде |
Вернуться к началу
RF Ventilation
Натуральный каучук требует определенной температуры, влажности / влажности и, возможно, условий вентиляции (SC VI) (климатические условия хранения).
Если резина сухая для транспортировки или сухая в контейнере, вентиляция не требуется.
Вернуться к началу
РФ Биотическая активность
Натуральный каучук проявляет биотическую активность 3-го порядка.
Относится к классу товаров, в которых процессы дыхания приостановлены, но при этом продолжаются биохимические, микробные и другие процессы разложения.
Вернуться к началу
RF Gases
Химическое разложение и выделение газа во время обработки приводят к образованию полостей на резиновых листах или внутри них (пузырей и пузырей).Внутренние поверхности пузырей часто липкие, в то время как пузырьки сухие и нелипкие.
Вернуться к началу
RF Самонагревание / самовозгорание
Следует запретить курение при загрузке контейнеров и на складах, поскольку натуральный каучук легко воспламеняется из-за высокого содержания углеводородов. При горении натуральный каучук выделяет значительное количество тепла (до 1200 ° C) и дыма. Выбрасывается большое количество газообразных продуктов и несгоревших твердых частиц в виде густого черного дыма, что затрудняет доступ к очагу пожара.При горении резины образуются разбрызгиваемые горящие капли смолы, которые могут вызвать распространение огня.
Лом и остатки натурального каучука относятся к классу 4.1 МКМПОГ (легковоспламеняющиеся твердые вещества).
В случае опасности возгорания пожарный персонал должен носить автоматический дыхательный аппарат и защитную одежду.
Пена, CO 2 , сухие химикаты или распыленная вода могут использоваться для тушения пожара. [72]
К началу
RF Odor
Тюки резины источают сильный запах резины, который в случае повреждения может стать проникающим запахом.
Активное поведение | Неприятный запах, поэтому не храните рядом с продуктами питания, предметами полулюкса и кормами для животных.![]() |
Пассивное поведение | Не чувствителен к запаху. |
Вернуться к началу
RF Загрязнение
Активное поведение | Нет. |
Пассивное поведение | Резина очень чувствительна к загрязнениям. Термопластические свойства резины означают, что инородные тела поглощаются путем проникновения или прилипания. Осколки застревают в резиновых тюках. Это также относится к резине, упакованной в тонкие фанерные ящики. Они могут расколоться даже при низких нагрузках, поэтому их еще называют «грязной упаковкой». В зависимости от степени проникновения загрязнения его можно удалить путем пилинга. Склады и контейнеры должны содержаться в абсолютной чистоте, так как любые загрязнения, такие как трава, осколки труб, бумага, текстильные отходы, графит, уголь, рудная пыль, цемент, медная крошка с катодных медных пластин, сера, сульфат меди и марганец. |
Вернуться к началу
RF Механические воздействия
Резину следует укладывать таким образом, чтобы избежать риска защемления.
Хрупкие деревянные ящики могут расколоться даже при нормальной нагрузке. Отверстия в резине, образованные осколками древесины, могут отрицательно сказаться на стоимости.
Прочная резина: Резина, устойчивая к деформации, то есть к растяжению и сжатию. Слабая резина: ребристые дымчатые листы, которые легко рвутся или отделяются при резком натяжении.
Вернуться к началу
Токсичность РФ / опасность для здоровья
Этот фактор риска не оказывает существенного влияния на транспортировку этого продукта.
В начало
RF Усадка / недостача / кража
Рекомендуется, чтобы погрузка и разгрузка осуществлялись под контролем.
Назад к началу
РФ Заражение / болезни насекомыми
При использовании деревянных упаковочных контейнеров или материалов для крепления груза может, при определенных обстоятельствах, соблюдение карантинных правил страны назначения (Правила импорта для упаковочной тары из массива дерева — стандарт IPPC) и фитосанитарный сертификат может быть приложен к транспортным документам. Информацию можно получить в фитосанитарных органах заинтересованных стран.
Вернуться к началу
Натуральный латекс, резиновые покрытия, концентрат латекса: Chemionics Latex, OH
Натуральный латекс
производится из каучукового дерева Hevea Brasiliensis . Эти деревья выращивают на больших плантациях, в основном в Таиланде, Индонезии, Малайзии и Либерии.
Натуральный латекс — это мутная белая жидкость, которую собирают, отрезая тонкие полоски коры с дерева и позволяя латексу стечь в сборные сосуды.Затем латекс собирается, разливается в контейнеры и доставляется на станцию обработки, где он фильтруется и концентрируется.
Латекс помещают в центрифугу, добавляют стабилизаторы и центрифугируют латекс для удаления некоторого количества воды и увеличения содержания каучука в латексе. После центрифугирования этот материал известен как концентрат латекса и содержит примерно 60% каучука.
Этот латексный концентрат затем смешивается Chemionics Corporation путем добавления других ингредиентов сырья. Эти исходные материалы представляют собой дисперсии на водной основе, которые добавляют в латекс для достижения желаемых эксплуатационных характеристик.
Chemionics производит высококачественные смеси натурального латекса по индивидуальному заказу для множества рыночных применений и возможностей обработки.
Chemionics предлагает рецептуры, в которых используется натуральный латекс с высоким и низким содержанием аммиака, а также предварительно вулканизированные составы .
Чтобы помочь нашим клиентам в производстве и переработке наших латексных смесей, Chemionics также производит специальных добавок , дисперсий и коагулянтов .
Наша техническая лаборатория готова разработать необходимую вам рецептуру, а также оказать помощь в применении и переработке наших соединений для точного удовлетворения ваших потребностей.
См. Нашу брошюру о возможностях приготовления смесей на водной основе.
Вот некоторые из основных категорий продукции из натурального латекса:
Составы для окунания
Chemionics производит составы из натурального латекса, которые разработаны с учетом строгих требований к процессам прямого погружения и погружения в коагулянт, используемых при производстве медицинских изделий, таких как перчатки для хирургов и экзаменов, катетеры и дыхательные мешки.Некоторые области применения латексных смесей для окунания включают:
|
|
Вернуться к началу
Когезивы (клеи для холодного / самозаклеивающегося уплотнения)
Chemionics производит полную линейку высокоэффективных когезивов на водной основе, используемых во многих приложениях для упаковки и переработки бумаги. Поверхности, покрытые когезивом, будут сцепляться только с другими поверхностями, покрытыми таким же связующим.
Эти клеи обладают низким содержанием летучих органических соединений и могут быть составлены по индивидуальному заказу для:
|
|
Эти когезивы из натурального латекса могут быть специально разработаны для нанесения на бумагу, пену, фольгу, а также различные пленки и ткани.Область применения продукта:
|
|
|
Составы для литья под давлением
Эти составы представляют собой предварительно вулканизированный натуральный латекс, используемый для производства полых, гибких изделий путем заливки в гипсовые формы. Латекс образуетс в результате того, что вода в латексе впитываетс в гипсовую форму, в результате чего на поверхность формы осаждаетс стенка загущенного латекса. Затем из формы выливают излишек латекса, оставшийся слой частично сушат, а затем удаляют из формы и полностью сушат. Область применения продукта:
|
В начало
Составы для изготовления форм
Эти составы были разработаны для изготовления гибких, прочных резиновых форм.Эти составы можно наносить кистью, распылять или погружать для создания желаемой резиновой формы. Наши высококачественные составы обеспечивают превосходное воспроизведение поверхности и мельчайшие детали.
|
Вот некоторые из наших наиболее популярных составов для изготовления форм:
|
|
|
Также доступны специальные рецептуры!
Клей для пены GenGrip
Однокомпонентный клей на водной основе из натурального латекса, специально разработанный для приклеивания пены к пене. Этот клей в основном используется в производстве мягкой мебели и поролоновых матрасов. Клей можно распылить или нанести на пену кистью. Этот клей склеивается быстро и надежно, что требуется для этих применений. Водная основа предлагает альтернативу существующим адгезивам на основе растворителей, которые исторически использовались для этих целей. К преимуществам GenGrip можно отнести:
- Мгновенно обеспечивает высокую степень липкости
- Превосходная сила сцепления
- Соответствует требованиям Cal 117 по воспламеняемости
- Неопасный / экологически чистый состав
- Не содержит летучих органических соединений
- Простая очистка оборудования мыльной водой
- Исключительный «пробег»
- Также доступны другие цвета
В начало
Разное.Натуральные латексные соединения
Chemionics также предлагает составы из натурального латекса по индивидуальному заказу для следующих областей применения:
|
|
|
Добавки / дополнительные продукты
Chemionics производит полную линейку добавок на водной основе, коагулянтов, дисперсий и технологических добавок для наших клиентов. Некоторые из них включают:
- Коагулянты (на водной и спиртовой основе)
- Лечебные средства
- Дисперсия:
|
|
Свяжитесь с нами по всем вопросам, касающимся ваших натуральных латексных смесей!
К началу
Варианты упаковки
В начало
Процесс производства резины
Обновлено 15 декабря 2018 г.
Карен Дж. Блаттлер
В конце 1930-х годов Соединенные Штаты использовали более половины мировых поставок натурального каучука.Сегодня натуральный каучук содержится в более чем 50 000 производимых продуктов в Соединенных Штатах, а США ежегодно импортируют более 3 миллиардов фунтов натурального каучука. Однако более 70 процентов каучука, используемого в современных производственных процессах, составляет синтетический каучук.
Основы натурального каучука
Натуральный каучук начинается с латекса. Латекс состоит из полимера, называемого полиизопреном, взвешенного в воде. Длинноцепочечные молекулы, состоящие из множества (поли) отдельных единиц (меров), соединенных вместе, образуют полимеры.Каучук — это особая форма полимера, называемая эластомером, что означает, что молекулы полимера растягиваются и изгибаются.
Более 2500 заводов производят латекс — молочно-подобный материал типа сока. Молочнокислый может быть самым знакомым для многих растением, производящим латекс, но коммерческий латекс получают из одного тропического дерева, Hevea brasiliensis. Как следует из названия, каучуковое дерево возникло в тропической Южной Америке. Более 3000 лет назад мезоамериканские цивилизации смешали латекс с ипомеиным соком для создания резины. Изменение соотношения латекса и ипомеи изменило свойства резины. От надувных мячей до резиновых сандалий мезоамериканцы знали и использовали резину.
До 1900 года большая часть натурального каучука производилась из диких деревьев Бразилии. В начале 20-го века спрос и предложение опережали производство с ростом популярности велосипедов и автомобилей. Семена, вывезенные контрабандой из Бразилии, привели к плантациям каучуковых деревьев в Юго-Восточной Азии. К 1930-м годам натуральный каучук использовался в диапазоне от шин на транспортных средствах и самолетах до 32 фунтов, которые можно найти в солдатской обуви, одежде и снаряжении.К тому времени большая часть поставок каучука в США шла из Юго-Восточной Азии, но Вторая мировая война отключила США от большей части его поставок.
Процесс производства натурального каучука
Процесс производства натурального каучука начинается со сбора латекса из каучуковых деревьев. Сбор латекса с каучуковых деревьев начинается с надрезания коры дерева. Латекс перетекает в чашку, прикрепленную к нижней части среза дерева. Латексный материал многих деревьев накапливается в больших резервуарах.
Самый распространенный метод извлечения каучука из латекса — это коагуляция — процесс свертывания или уплотнения полиизопрена в массу. Этот процесс осуществляется путем добавления в латекс кислоты, такой как муравьиная кислота. Процесс коагуляции занимает около 12 часов.
Вода выдавливается из коагулята резины с помощью ряда роликов. Полученные тонкие листы толщиной около 1/8 дюйма сушат на деревянных стеллажах в коптильнях. Процесс сушки обычно занимает несколько дней.Полученная темно-коричневая резина, которая теперь называется ребристой дымовой завесой, складывается в тюки для отправки на переработчик.
Однако не вся резина дымится. Резина, высушенная горячим воздухом, а не курением, называется листом, высушенным на воздухе. В результате получается резина лучшего качества. Каучук еще более высокого качества, называемый бледным крепом, требует двух стадий коагуляции с последующей сушкой на воздухе.
Создание синтетического каучука
За прошедшие годы было разработано несколько различных типов синтетического каучука.Все происходит в результате полимеризации (связывания) молекул. Процесс, называемый аддитивной полимеризацией, объединяет молекулы в длинные цепи. Другой процесс, называемый конденсационной полимеризацией, удаляет часть молекулы, поскольку молекулы связаны друг с другом. Примеры аддитивных полимеров включают синтетические каучуки, изготовленные из полихлоропрена (неопреновый каучук), маслостойкий и бензиностойкий каучук и стирол-бутадиеновый каучук (SBR), используемый в качестве резины без отскока в шинах.
Первые серьезные поиски синтетического каучука начались в Германии во время Первой мировой войны.Британские блокады не позволили Германии получить натуральный каучук. Немецкие химики разработали полимер из звеньев 3-метилизопрена (2,3-диметил-1,3-бутадиен), [CH 2 = C (CH 3 ) C (CH 3 ) = Ch3], из ацетона. . Хотя этот заменитель, метилкаучук, уступал натуральному каучуку, Германия к концу Первой мировой войны производила 15 тонн в месяц.
Продолжение исследований привело к созданию синтетических каучуков более высокого качества. Самый распространенный тип синтетического каучука, используемый в настоящее время, Buna S (бутадиен-стирольный каучук или SBR), был разработан в 1929 году немецкой компанией I.Г. Фарбен. В 1955 году американский химик Сэмюэл Эммет Хорн-младший разработал полимер, на 98 процентов состоящий из цис-1,4-полиизопрена, который ведет себя как натуральный каучук. Это вещество в сочетании с SBR используется для изготовления шин с 1961 года.
Обработка резины
Резина, натуральная или синтетическая, поставляется на перерабатывающие предприятия в больших тюках. После того, как каучук поступает на завод, его обработка проходит в четыре этапа: компаундирование, смешивание, формование и вулканизация. Состав и метод резиновой смеси зависят от предполагаемого результата процесса изготовления резины.
Компаундирование добавляет химикаты и другие добавки для настройки резины для предполагаемого использования. Натуральный каучук меняется в зависимости от температуры, становясь хрупким при холода и липким, липким при нагревании. Химические вещества, добавленные во время смешивания, вступают в реакцию с каучуком в процессе вулканизации, чтобы стабилизировать полимеры каучука. Дополнительные добавки могут включать армирующие наполнители для улучшения свойств резины или неусиливающие наполнители для удлинения резины, что снижает стоимость.Тип используемого наполнителя зависит от конечного продукта.
Наиболее часто используемым армирующим наполнителем является технический углерод, полученный из сажи. Технический углерод увеличивает прочность резины на разрыв и устойчивость к истиранию и разрыву. Технический углерод также улучшает устойчивость резины к ультрафиолетовому разрушению. Большинство резиновых изделий черные из-за наполнителя сажи.
В зависимости от планируемого использования каучука другие используемые добавки могут включать безводные силикаты алюминия в качестве усиливающих наполнителей, другие полимеры, переработанный каучук (обычно менее 10 процентов), составы, снижающие усталость, антиоксиданты, озоностойкие химические вещества, красящие пигменты. , пластификаторы, смягчающие масла и смазки для форм.
Добавки необходимо тщательно перемешать с резиной. Высокая вязкость (сопротивление текучести) резины затрудняет перемешивание без повышения температуры резины до достаточно высокой (до 300 градусов по Фаренгейту), чтобы вызвать вулканизацию. Чтобы предотвратить преждевременную вулканизацию, перемешивание обычно происходит в два этапа. На первом этапе в каучук примешивают такие добавки, как технический углерод. Эта смесь называется маточной смесью. Как только резина остынет, в нее добавляют химические вещества для вулканизации.
Формование резиновых изделий происходит с использованием четырех основных методов: экструзии, каландрирования, нанесения покрытия или формования и литья. В зависимости от конечного продукта можно использовать более одной техники формования.
Экструзия заключается в пропрессовке высокопластичной резины через серию шнековых экструдеров. При каландрировании резина проходит через серию все более мелких зазоров между роликами. Процесс роликовой фильеры сочетает в себе экструзию и каландрирование, позволяя получить лучший продукт, чем любой отдельный процесс.
Покрытие использует процесс каландрирования для нанесения слоя резины или для вдавливания резины в ткань или другой материал. Покрытия, водонепроницаемые тканевые палатки и плащи, конвейерные ленты, а также надувные плоты изготавливаются путем покрытия материалов резиной.
Резиновые изделия, такие как подошвы и каблуки обуви, прокладки, уплотнения, присоски и упоры для бутылок, отливаются с использованием форм. Литье также является этапом изготовления шин. Три основных метода формования резины — это компрессионное формование (используется, среди прочего, при производстве шин), литье под давлением и литье под давлением.Вулканизация каучука происходит в процессе формования, а не на отдельном этапе.
Вулканизация завершает процесс производства резины. Вулканизация создает поперечные связи между полимерами каучука, и процесс варьируется в зависимости от требований к конечному каучуковому продукту. Меньшее количество поперечных связей между полимерами каучука делает резину более мягкой и податливой. Увеличение количества поперечных соединений снижает эластичность резины, что приводит к более твердой резине.Без вулканизации резина оставалась бы липкой в горячем состоянии и хрупкой в холодном состоянии и гнила бы гораздо быстрее.
Вулканизация, впервые обнаруженная в 1839 году Чарльзом Гудиером, потребовала добавления серы в резину и нагревания смеси до 280 F в течение примерно пяти часов. Современная вулканизация, как правило, использует меньшее количество серы в сочетании с другими химическими веществами, чтобы сократить время нагрева до 15-20 минут. Были разработаны альтернативные методы вулканизации, не использующие серу.
Это не каучуковое дерево в вашей гостиной
Есть идеи, какой первый товар, поставленный под прямой контроль правительства США, мог быть во время Второй мировой войны, и это произошло еще до нападения на Перл-Харбор?
Сталь? Неправильный.
Алюминий? Снова неверно.
Нефть? Неа.
Магний? Даже не близко.
Резиновый. Фактически историки говорят нам, что нормирование бензина было введено не столько для экономии топлива, сколько для предотвращения износа шин.
Даже спустя десятилетия, , когда в составе шин используется более 200 ингредиентов, в научно-исследовательском отчете, финансируемом государством, отмечается: «Натуральный каучук является стратегическим сырьем, используемым в огромных количествах в более чем 40 000 сферах применения. Соединенные Штаты, не имеющие собственного производства натурального каучука, полностью зависят от импорта.
«Поставкам натурального каучука в Соединенные Штаты, которые используют более 20 процентов мировых поставок, угрожают многие факторы», — добавили ученые.«Более 90 процентов мирового производства приходится на Юго-Восточную Азию. Дефицит натурального каучука серьезно повлияет на оборону, транспорт, медицину и потребительские рынки.
«Никакие другие высокоэффективные эластомеры не могут быть успешно использованы вместо натурального каучука во многих из этих приложений».
Кроме того, они отметили, что промышленный рост в Азии «продолжает сокращать поставки и поднимать цены».
Натуральный каучук стоил около 35 центов за фунт в 2002 году и 2,80 доллара за фунт в 2011 году, согласно данным Федерального резервного банка Санкт-Петербурга.Луи. В конце сентября 2020 года он составлял 89 центов.
«Трудно представить себе любое другое сырье , которое было бы столь же жизненно важным и уязвимым», — писал ботаник Уэйд Дэвис в книге « One River: Исследования и открытия в тропических лесах Амазонки». , — книга, в которой подробно описаны открытия и разработки, возможно, самой биологически разнообразной и важной экосистемы в мире — и единственного места на планете, где каучук является коренным населением.
Подождите! Изначально каучук поступал только из лесов Амазонки, но теперь 90 процентов мировых поставок приходится на Юго-Восточную Азию? Да, и эта история — интрига, достойная голливудского блокбастера.
Вы можете задаться вопросом, не может ли синтетический каучук быть достойной заменой, ведь он все чаще используется в производстве шин. Но так было не всегда, и натуральный каучук остается основным компонентом шин.
Натуральный каучук был и остается важным. Как отмечает Дэвис, когда американские поставки каучука из Азии были прекращены во время Второй мировой войны, наше правительство профинансировало один из самых важных «ботанических квестов» 20-го века.
«Белая кровь» деревьев гевеи перерабатывается для производства натурального каучука, используемого в шинах.«У инженеров было два года», — писал Дэвис.«Если программа синтетического каучука не увенчается успехом, способность страны вести войну прекратится. Фактически, добавил он, «если бы не Манхэттенский проект, 2 миллиарда долларов инвестиций, которые привели к созданию атомной бомбы, программа синтетического каучука запомнилась бы как величайший технологический прорыв войны».
Даже сегодня поиск заменителя натурального каучука продолжается, и ученые, использующие «метаболическую инженерию», стремятся извлечь натуральный каучук из табака, подсолнечника, гваюли, одуванчиков и других растений, которые можно выращивать в Соединенных Штатах.
Проблема в том, что в отличие от кленов, которые можно использовать для получения сока, который становится сиропом для подслащивания ваших утренних блинов, виды гевеи или катучук деревья, из которых можно удалить «белую кровь», также известную как латекс, растут только в более умеренный климат, чем где-либо в Соединенных Штатах.
Кстати, эти настоящие каучуковые деревья совсем не похожи на те, что продаются здесь в садовых центрах как декоративные «каучуковые деревья». Они больше напоминают осину, высокие и тонкие, со светлой корой.А натуральный латекс имеет белый цвет, как и оригинальные шины на ранних легковых автомобилях.
Не только это, но если вы посадите дерево гевеи сегодня, вам придется подождать от 5 до 7 лет до первой посадки. И тогда этому дереву понадобится год, чтобы обеспечить достаточное количество своей белой крови для производства единственной шины для компактного автомобиля. Чтобы установить новый комплект шин на ваш полноразмерный внедорожник, требуется годовой урожай не менее полдюжины деревьев.
Хотя Колумб сообщил, что коренных жителей Северной Америки играли с отскакивающими мячами, и он защищал свои парусные инструменты в тканевых сумках, окрашенных соком плачущих деревьев, французский математик Шарль-Мари де ла только в 18 веке Кондамин действительно осознавал ценность жидкости, которая затвердевает, но при этом остается эластичной после воздействия тепла.
Бразилия была эксклюзивным поставщиком каучука в мире до 1876 года, когда в заговоре с международным сообществом Генри Уикхэм контрабандой переправил 70 000 семян гевеи в Королевский ботанический сад в Кью, Англия. Эти семена затем использовались для выращивания деревьев в Африке и Азии.
В своей книге Дэвис отмечает, что американский промышленник Эндрю Карнеги сетовал на инвестирование в сталь, а не в каучук, и что люди по обе стороны Атлантического океана бросали монеты, решая искать золото в Клондайке или белое золото Бразилии.
Даже Генри Форд принял участие в этом деле, основав недолговечное сообщество Фордландия в Амазонии, чтобы контролировать еще одно сырье, необходимое для производства автомобилей.
В 1910 году Бразилия производила половину мировых запасов натурального каучука. Когда началась Вторая мировая война, эта цифра составляла менее 2 процентов. Одной из причин была конкуренция со стороны Азии, другой — вирус —
microcyclus ulei , страшная болезнь листьев Южной Америки, — который поразил бразильские каучуковые леса.
Американский биолог Джеймс Вейр начал прививать стебли устойчивых к вирусам деревьев в высокоурожайные растения в 1930-х годах, а французское правительство и Мишлен спонсировали послевоенные исследования устойчивых к вирусам деревьев. Борьба с болезнями, которая считается одной из главных угроз для международной сельскохозяйственной торговли, была названа сельскохозяйственным эквивалентом борьбы с вирусом СПИДа среди людей.
Также был разработан переход от старого плантационного сельского хозяйства к способу для местных фермеров вести устойчивый образ жизни, способный пережить изменения мировых цен на каучук.
Вместо больших участков каучуковых деревьев, восприимчивых к вирусу, местные фермеры поощряли создание небольших фермерских участков, которые не только высаживали гевею, но и выращивали банановые деревья, которые дают почти немедленный урожай, а также какао, кустарниковое растение, которое любит светлая тень между рядами каучуковых деревьев и дает стручки семян, которые перерабатываются в шоколад.
В то же время компания Michelin превратила принадлежащий ей большой участок леса в охраняемый заповедник, где ученые проводят исследования — включая открытие новых видов — в одном из самых биоразнообразных мест в мире
Не только есть запасы высококачественного бразильского каучука, но и местная сельскохозяйственная экономика, и область научных знаний расширились.
От липкого сока к резинке
Главная | Блог | Натуральный каучук — от липкого сока до годного к употреблению материалаОпубликовано admin Июнь 11, 2015
Натуральный каучук, используемый в Stern Rubber Company, изготовлен из природного источника, так как это древесный сок. Многие потребители думают, что весь каучук связан с натуральным каучуком, но натуральный каучук — это только один тип каучука, который включает различные синтетические каучуки, такие как EPDM, силикон, полихлоропрен, фторуглерод, бутил, SBR и нитрил.
Натуральный каучук, который также называют индийским каучуком или каучуком. в научных терминах означает, что это полимеры органического соединения изопрена и классифицируется как эластомер. Каучук собирают с каучуковых деревьев, которые относятся к семейству деревьев семейства Euphorbiace; Наиболее распространены деревья Hevea brasilienisis или Sharinga. Натуральный каучук извлекается методом, называемым постукиванием, путем надрезов в коре и сбора жидкости в сосуды, прикрепленные к каучуковым деревьям.Жидкость представляет собой липкий молочный сок, называемый латексом, и требует нескольких шагов, прежде чем он будет продаваться как натуральный каучук.
После сбора латекса с плантации, он срочно отправляется на перерабатывающий завод, что предотвращает естественную коагуляцию латекса и делает латекс бесполезным. На перерабатывающем предприятии рядом с плантацией латекс нагревают и смешивают с кислым аммиаком, который образует резину, подобную творогу; сера может быть добавлена для создания более твердой и стабильной смеси. Как и при приготовлении сыра, резиновый творог всплывает на поверхность жидкости, снимается с поверхности и проходит через тяжелые ролики для удаления излишков воды.
Формованные листы натурального каучука нарезаются и укладываются в штабель для отправки на предприятия по формовке резины, такие как Stern Rubber Company.
В начале 1830-х годов натуральный каучук широко использовался, так как разразилась «каучуковая лихорадка», так как всем требовались изделия из «новой» водонепроницаемой резинки из Бразилии, и для удовлетворения спроса возникли фабрики. К сожалению, это исчезло так же быстро, как и появилось, поскольку публике надоедает грязь, которая замерзает зимой до костей, становится липкой и разваливается в жаркую летнюю жару.
Чарльзу Гудиеру приписывают изобретение процесса вулканизации натурального каучука (и процесса, который используется сегодня на каждой компании по формованию резины), который в конечном итоге решил проблемы, которые преследовали раннее коммерческое использование резиновой резинки, и получил широкое распространение. использовать вскоре после этого.
Расположенные в джунглях тропических лесов Амазонки в Бразилии, джунглях Азии, Малайзии, Таиланда и Индонезии, плантации по производству каучука производят большую часть натурального каучука в мире.Во время Второй мировой войны, когда Япония занимала большинство джунглей в Юго-Восточной Азии, Соединенным Штатам пришлось найти альтернативный источник каучука, поэтому были профинансированы исследования, в результате которых был создан синтетический каучук, который использовался для победы в войне.
Натуральный каучук — очень полезный каучук, который широко используется в Stern Rubber Company. Помимо того, что он чрезвычайно водонепроницаем; он также обладает высокой эластичностью и эластичностью и часто используется в пневматических устройствах, таких как шины. Натуральный каучук часто смешивают с синтетическим каучуком, чтобы оптимизировать свойства обоих материалов.Хотя Stern Rubber их не производит, применение натурального каучука, с которым знакомо большинство людей, — это резиновые ленты. Некоторые из деталей, которые производятся на Stern Rubber, включают пробки для испытания пневматической сантехники, прокладки и присоски.
Резина — Энциклопедия Нового Света
Латекс собирают с каучукового дерева.Каучук представляет собой эластичный углеводородный полимер, который встречается в виде молочной коллоидной суспензии (известной как латекс ) в соке нескольких разновидностей растений.Каучук также можно производить синтетическим путем.
К сожалению, у истории резины есть и обратная сторона. Около ста лет назад миллионы африканцев погибли в Свободном государстве Конго из-за жажды получить прибыль от каучука.
Источники
Основным коммерческим источником натурального латекса, используемого для создания каучука, является паракаучуковое дерево Hevea brasiliensis (Euphorbiaceae). Во многом это связано с тем, что он реагирует на ранение, производя больше латекса.В 1876 году Генри Викхэм собрал тысячи семян этого растения в Бразилии, и они были проращены в садах Кью, Англия. Затем саженцы были отправлены в Коломбо, Индонезию, Сингапур и Британскую Малайю. Позднее Малая стала крупнейшим производителем каучука.
Другие растения, содержащие латекс, включают инжир ( Ficus elastica ), молочай и одуванчик обыкновенный. Хотя они не были основными источниками каучука, Германия пыталась использовать такие источники во время Второй мировой войны, когда она была отрезана от поставок каучука.Позднее эти попытки были вытеснены разработкой синтетического каучука. Его плотность составляет около 920 килограммов / метр 3 .
Сборник резины
Женщина в Шри-Ланке (Цейлон) во время сбора каучукаВ таких местах, как Керала, где кокосы растут в изобилии, половина кокосовой скорлупы используется в качестве контейнера для сбора латекса. Раковины прикрепляются к дереву короткой острой палкой, и латекс стекает в нее за ночь. Обычно таким образом получается латекс на уровне от половины до трех четвертей оболочки.Затем латекс с нескольких деревьев переливается в плоские поддоны и смешивается с муравьиной кислотой, которая служит коагулянтом. Через несколько часов очень влажные листы резины отжимаются, пропуская их через пресс, а затем отправляются на фабрики, где проводится вулканизация и дальнейшая обработка.
Источники тока из резины
Сегодня Азия является основным источником натурального каучука. Более половины используемого сегодня каучука является синтетическим, но несколько миллионов тонн натурального каучука по-прежнему производятся ежегодно, и он по-прежнему необходим для некоторых отраслей промышленности, включая автомобильную и военную.
Гипоаллергенная резина может быть изготовлена из гваюли.
Натуральный каучук часто вулканизируют. Этот процесс нагревают и добавляют серу, перекись или бисфенол для повышения упругости и эластичности, а также для предотвращения его разрушения. Вулканизация значительно улучшила долговечность и полезность резины с 1830-х годов. Успешное развитие вулканизации наиболее тесно связано с Чарльзом Гудиером. Технический углерод часто используется в качестве добавки к резине для повышения ее прочности, особенно в автомобильных шинах.
История
В родных регионах Центральной Америки и Южной Америки каучук собирают уже давно. Цивилизации Мезоамерики использовали каучук в основном из растений, известных как Castilla elastica . Древние мезоамерики играли в мяч с использованием резиновых мячей, и было найдено несколько доколумбовых резиновых мячей (всегда в местах, затопленных пресной водой), самые ранние из которых датируются примерно 1600 — гг. До н. Э. По словам Берналя Диаса дель Кастильо, испанские конкистадоры были настолько поражены энергичным отскоком резиновых мячей ацтеков, что задавались вопросом, были ли шары зачарованы злыми духами.Майя также сделали временную резиновую обувь, окунув ноги в латексную смесь.
Каучук также использовался в различных других контекстах, например, для полос, удерживающих каменные и металлические инструменты на деревянных ручках, и для набивки для ручек инструментов. Хотя древние жители Мезоамерики не знали о вулканизации, они разработали органические методы обработки каучука с аналогичными результатами, смешивая необработанный латекс с различными соками и соками других виноградных лоз, в частности, Ipomoea alba , вида ипомеи.В Бразилии коренные жители понимали, как из резины делают водонепроницаемую ткань. Одна история гласит, что первый европеец, вернувшийся в Португалию из Бразилии с образцами такой водоотталкивающей прорезиненной ткани, настолько шокировал людей, что его привлекли к суду по обвинению в колдовстве.
Первое упоминание каучука в Англии, по-видимому, относится к 1770 году, когда Джозеф Пристли заметил, что кусок материала чрезвычайно хорош для стирания карандашных следов на бумаге, отсюда и название «каучук».«Примерно в то же время Эдвард Нэрн начал продавать кубики натурального каучука в своем магазине на Корнхилле, 20 в Лондоне. Кубики, предназначенные для ластика, продавались по удивительно высокой цене — три шиллинга за полдюймовый куб.
Паракаучуковое дерево изначально росло в Южной Америке, где оно было основным источником ограниченного количества латексного каучука, потребляемого на протяжении большей части девятнадцатого века. Около ста лет назад Свободное государство Конго в Африке было важным источником латекса натурального каучука, который в основном собирали принудительным трудом.Свободное государство Конго было создано и управлялось как личная колония бельгийским королем Леопольдом II. Миллионы африканцев погибли там из-за страсти к резине и прибыли от каучука. После неоднократных усилий каучук успешно культивировали в Юго-Восточной Азии, где он сейчас широко выращивается.
В середине девятнадцатого века каучук был новым материалом, но не нашел широкого применения в промышленном мире. Его использовали сначала как ластик, а затем как медицинские устройства для соединения трубок и для вдыхания лекарственных газов.С открытием, что каучук растворим в эфире, он нашел применение в водонепроницаемых покрытиях, особенно для обуви, и вскоре после этого прорезиненное пальто Mackintosh стало очень популярным.
Тем не менее, большинство этих заявок было в небольших объемах, и материал просуществовал недолго. Причина отсутствия серьезных применений заключалась в том, что материал был непрочным, липким, часто гнил и плохо пах, поскольку оставался в неотвержденном состоянии.
Химические и физические свойства
Каучук обладает уникальными физическими и химическими свойствами.
За исключением нескольких примесей натуральных продуктов, натуральный каучук по существу представляет собой полимер изопреновых звеньев, углеводородный диеновый мономер. Синтетический каучук может быть изготовлен в виде полимера изопрена или различных других мономеров. Считается, что резина была названа Джозефом Пристли, который в 1770 году обнаружил, что высушенный латекс стирает следы карандаша. Свойства материала натурального каучука делают его эластомером и термопластом.
Поведение каучука при напряжении и деформации демонстрирует эффект Маллинза, эффект Пейна и часто моделируется как гиперэластичный.
Почему резина обладает эластичностью?
В большинстве эластичных материалов, таких как металлы, используемые в пружинах, эластичность вызвана деформациями скрепления. При приложении напряжения длины связей отклоняются от равновесия (минимальной энергии), и энергия деформации накапливается электростатически. Часто предполагается, что резина ведет себя таким же образом, но оказывается, что это плохое описание. Резина — любопытный материал, потому что, в отличие от металлов, энергия деформации накапливается как термически, так и электростатически.
В расслабленном состоянии каучук состоит из длинных скрученных полимерных цепей, которые связаны между собой в нескольких точках. Между парой звеньев каждый мономер может свободно вращаться вокруг своего соседа. Это дает каждой части цепи свободу действий для принятия большого количества геометрических форм, например, очень рыхлой веревки, прикрепленной к паре фиксированных точек. При комнатной температуре резина накапливает достаточно кинетической энергии, так что каждая секция цепи колеблется хаотично, как приведенный выше кусок веревки, который сильно встряхивается.
Когда резина растягивается, «свободные куски веревки» натягиваются и, таким образом, больше не могут колебаться.Их кинетическая энергия выделяется в виде избыточного тепла. Следовательно, энтропия уменьшается при переходе от расслабленного состояния к растянутому и увеличивается при релаксации. Это изменение энтропии также можно объяснить тем фактом, что плотный участок цепи может складываться меньшим числом способов (W), чем свободный участок цепи при данной температуре (nb. Энтропия определяется как S = k * ln (W )). Таким образом, релаксация растянутой резиновой ленты вызывается увеличением энтропии, а действующая сила не является электростатической, а является результатом преобразования тепловой энергии материала в кинетическую энергию.Резиновая релаксация эндотермична. Во время сжатия материал подвергается адиабатическому охлаждению. Это свойство резины легко проверить, поднеся к губам натянутую резинку и расслабив ее.
Растяжение резиновой ленты в некотором смысле эквивалентно сжатию идеального газа, а расслабление — его расширению. Обратите внимание, что сжатый газ также проявляет «упругие» свойства, например, внутри накачанной автомобильной шины. Тот факт, что растяжение эквивалентно сжатию, может показаться несколько нелогичным, но это имеет смысл, если рассматривать резину как одномерный газ .Растяжение сокращает «пространство», доступное каждой секции цепи.
Вулканизация резины создает больше дисульфидных связей между цепями, поэтому каждый свободный участок цепи становится короче. В результате цепи натягиваются быстрее при заданной длине напряжения. Это увеличивает постоянную упругую силу и делает резину более твердой и менее растяжимой.
При охлаждении ниже температуры стеклования квазижидкие сегменты цепи «застывают» в фиксированной геометрии, и резина резко теряет свои эластичные свойства, хотя процесс обратим.Это свойство присуще большинству эластомеров. При очень низких температурах резина становится довольно хрупкой; при ударе он разобьется на осколки. Эта критическая температура является причиной того, что в зимних шинах используется более мягкий вариант резины, чем в обычных шинах. Считалось, что вышедшие из строя резиновые уплотнения, которые стали причиной катастрофы космического челнока Challenger , остыли ниже критической температуры. Катастрофа случилась в необычно холодный день.
Синтетический каучук
Синтетический каучук производится путем полимеризации различных мономеров для получения полимеров.Они являются частью обширного исследования, охватываемого наукой о полимерах и технологией каучука. Его научное название — полиизопрен.
Синтетический каучук — это любой тип искусственно созданного полимерного материала, который действует как эластомер. Эластомер — это материал с механическим (или материальным) свойством, заключающимся в том, что он может подвергаться гораздо более упругой деформации под нагрузкой, чем большинство материалов, и при этом возвращаться к своему прежнему размеру без остаточной деформации. Синтетический каучук во многих случаях заменяет натуральный каучук, особенно когда требуются улучшенные свойства материала.
Натуральный каучук, получаемый из латекса, в основном представляет собой полимеризованный изопрен с небольшим процентом примесей в нем. Это ограничит диапазон доступных ему свойств. Кроме того, существуют ограничения на пропорции двойных связей цис и транс , обусловленные методами полимеризации натурального латекса. Это также ограничивает диапазон свойств, доступных для натурального каучука, хотя для улучшения свойств используются добавление серы и вулканизация.
Тем не менее, синтетический каучук может быть получен путем полимеризации различных мономеров, включая изопрен (2-метил-1,3-бутадиен), 1,3-бутадиен, хлоропрен (2-хлор-1,3-бутадиен), и изобутилен (метилпропен) с небольшим процентным содержанием изопрена для сшивания.Кроме того, эти и другие мономеры можно смешивать в различных желаемых пропорциях для сополимеризации для получения широкого диапазона физических, механических и химических свойств. Мономеры можно производить в чистом виде, а добавление примесей или добавок можно контролировать с помощью конструкции для придания оптимальных свойств. Полимеризацию чистых мономеров можно лучше контролировать, чтобы получить желаемое соотношение двойных связей цис и транс .
Острая потребность в синтетическом каучуке, получаемом из широко распространенного сырья, возникла в связи с расширением использования автотранспортных средств, и особенно автомобильных шин, начиная с 1890-х годов.Политические проблемы, возникшие в результате сильных колебаний стоимости натурального каучука, привели к принятию Закона Стивенсона в 1921 году. Этот закон по существу создал картель, который поддерживал цены на каучук путем регулирования производства (см. ОПЕК). К 1925 году цена на натуральный каучук выросла до такой степени, что такие компании, как DuPont, изучали методы производства синтетического каучука, чтобы конкурировать с натуральным каучуком. В случае Dupont усилия привели к открытию неопрена, который представляет собой синтетический каучук, который слишком дорог для использования в шинах, но обладает некоторыми очень желательными свойствами, которые позволяют использовать каучук в областях, которые не подходят для натурального каучука. .
Вулканизация
Вулканизация, или отверждение резины, представляет собой химический процесс, в котором отдельные молекулы полимера связаны с другими молекулами полимера атомными мостиками. Конечным результатом является то, что упругие молекулы каучука становятся в большей или меньшей степени сшитыми. Это делает сыпучий материал более твердым, более прочным и устойчивым к химическому воздействию. Это также делает поверхность материала более гладкой и предотвращает прилипание к металлическим или пластмассовым химическим катализаторам.Этот сильно сшитый полимер имеет прочные ковалентные связи с сильными силами между цепями и, следовательно, является нерастворимым и неплавким, термореактивным или термореактивным полимером. Процесс назван в честь Вулкана, римского бога огня.
Причина вулканизации
Незатвердевший натуральный каучук начнет портиться в течение нескольких дней, постепенно превращаясь в влажную рассыпчатую массу. Процесс гибели частично состоит из расщепления белков (как это происходит с белками молока), а также из расщепления больших молекул каучука, которые окисляются в воздухе из-за того, что молекулы кислорода атакуют двойные связи.
Резина, которая не вулканизирована должным образом, также может погибнуть, но более медленно. Процесс гибели поощряется длительным пребыванием на солнце, а особенно ультрафиолета.
Описание
Вулканизация обычно считается необратимым процессом (см. Ниже), аналогичным другим термореактивным пластикам, и его следует сильно контрастировать с термопластическими процессами (процесс замораживания расплава), которые характеризуют поведение большинства современных полимеров. Эта необратимая реакция отверждения определяет отвержденные резиновые смеси как термореактивные материалы, которые не плавятся при нагревании, и выводит их из класса термопластичных материалов (таких как полиэтилен и полипропилен).Это фундаментальное различие между каучуками и термопластами, которое определяет условия их применения в реальном мире, их стоимость и экономику спроса и предложения.
Обычно фактическое химическое сшивание осуществляется серой, но существуют и другие технологии, в том числе системы на основе пероксидов. Комбинированная упаковка для отверждения в типичной резиновой смеси включает сам отвердитель (серу или пероксид) вместе с ускорителями и замедлителями.
Вдоль молекулы каучука имеется ряд мест, привлекательных для атомов серы.Это так называемые места лечения. Во время вулканизации восьмичленное кольцо серы распадается на более мелкие части с различным количеством атомов серы. Эти части довольно реактивны. К каждому участку отверждения на молекуле каучука могут присоединяться один или несколько атомов серы, и оттуда цепочка серы может расти, пока в конечном итоге не достигнет участка отверждения на другой молекуле каучука. Эти серные мостики обычно имеют длину от двух до десяти атомов. Сравните это с типичными полимерными молекулами, в которых длина углеродной основы составляет многие тысячи атомных единиц.Число атомов серы в сшивке серы оказывает сильное влияние на физические свойства конечного резинового изделия. Короткие поперечные связи серы, содержащие всего один или два атома серы в поперечных связях, придают каучуку очень хорошую термостойкость. Сшивки с большим числом атомов серы, до шести или семи, придают каучуку очень хорошие динамические свойства, но с меньшей термостойкостью. Динамические свойства важны для изгибных движений резинового изделия, например, движения боковой стенки ходовой шины.Без хороших свойств изгиба эти движения быстро приведут к образованию трещин и, в конечном итоге, к разрушению резинового изделия. Он очень гибкий и водостойкий.
Вклад Goodyear
В большинстве учебников говорится, что Чарльз Гудиер (1800–1860) первым использовал серу для вулканизации резины. Однако сегодня мы знаем, что древние мезоамерики достигли тех же результатов в 1600 — годах до н. Э. [1].
В зависимости от того, что вы читаете, история Goodyear — это либо чистая удача, либо тщательное исследование.Goodyear настаивает на том, что это было второе, хотя многие современные отчеты указывают на первое.
Гудиер утверждал, что он открыл вулканизацию на основе серы в 1839 году, но не запатентовал изобретение до 15 июня 1844 года и не писал историю открытия до 1853 года в своей автобиографической книге Gum-Elastica . Тем временем Томас Хэнкок (1786-1865), ученый и инженер, запатентовал этот процесс в Великобритании 21 ноября 1843 года, за восемь недель до того, как Гудиер подал заявку на свой собственный патент в Великобритании.
Компания Goodyear Tire and Rubber приняла название Goodyear из-за своей деятельности в резиновой промышленности, но не имеет других связей с Чарльзом Гудиером и его семьей.
Вот отчет Goodyear об изобретении, взятый из Gum-Elastica . Хотя книга является автобиографией, Goodyear решил написать ее от третьего лица, так что «изобретатель» и «он», упомянутые в тексте, на самом деле являются автором. Он описывает сцену на резиновой фабрике, где работал его брат:
…. Изобретатель провел несколько экспериментов, чтобы установить влияние тепла на то же соединение, которое разложилось в почтовых мешках и других предметах. Он был удивлен, обнаружив, что образец, неосторожно приведенный в контакт с горячей печью, обугливался, как кожа.
Goodyear продолжает описывать, как он пытался привлечь внимание своего брата и других рабочих на заводе, которые были знакомы с поведением растворенного каучука, но они отклонили его призыв как недостойный их внимания, считая его одним из он обращался к ним много раз из-за какого-то странного эксперимента.Гудиер утверждает, что он пытался сказать им, что растворенная резина обычно плавится при чрезмерном нагревании, но они все равно игнорировали его.
Он прямо предположил, что если бы процесс обугливания можно было остановить в нужной точке, это могло бы лишить резинки ее естественной адгезии, что сделало бы ее лучше, чем природная резинка. После дальнейших испытаний с нагреванием он еще больше убедился в правильности этого вывода, обнаружив, что индийский каучук нельзя плавить в кипящей сере при любой высокой температуре, а всегда сгорать.Он сделал еще одну попытку нагрева подобной ткани перед открытым огнем. Последовал тот же эффект, что и обугливание резинки; но были и другие весьма удовлетворительные признаки успеха в достижении желаемого результата, поскольку на краю обугленной части появлялась линия или граница, которая не была обугленной, но полностью затвердевшей.
Гудиер далее описывает, как он переехал в Вобурн, штат Массачусетс, и провел серию систематических экспериментов, чтобы найти правильные условия для вулканизации резины.
… Убедившись с уверенностью, что он нашел объект своих поисков и многое другое, и что новое вещество было стойким к холоду и растворителем натуральной камеди, он почувствовал себя щедрым вознаграждением за прошлое, и совершенно равнодушен к испытаниям будущего.
Goodyear никогда не делал денег на своем изобретении. Он заложил все имущество своей семьи, чтобы собрать деньги, но 1 июля 1860 года он умер с долгами более 200000 долларов.
Более поздние разработки
Какова бы ни была истинная история, открытие реакции каучук-сера произвело революцию в использовании и применении каучука и изменило облик промышленного мира.
До того времени единственным способом герметизировать небольшой зазор во вращающейся машине или гарантировать, что топливо, используемое для питания этой машины (обычно пар) в цилиндре, прикладывает силу к поршню с минимальной утечкой, было использование кожа, пропитанная маслом. Это было приемлемо до умеренных давлений, но выше определенного предела конструкторам машин приходилось идти на компромисс между дополнительным трением, создаваемым более плотной упаковкой кожи, или большей утечкой драгоценного пара.
Вулканизированная резина — идеальное решение.Что касается вулканизированной резины, у инженеров был материал, которому можно было придать точную форму и размеры, который выдерживал бы умеренные и большие деформации под нагрузкой и быстро восстанавливался до своих исходных размеров после снятия нагрузки. В сочетании с хорошей прочностью и отсутствием липкости они являются критическими требованиями для эффективного герметизирующего материала.
Дальнейшие эксперименты по переработке и смешиванию каучука проводились, в основном, в Великобритании Хэнкоком и его коллегами.Это привело к более воспроизводимому и стабильному процессу.
Однако в 1905 году Джордж Оенслагер обнаружил, что производное анилина, называемое тиокарбанилидом, способно ускорять действие серы на каучук, что приводит к гораздо более короткому времени отверждения и снижению потребления энергии. Эта работа, хотя и менее известная, почти так же важна для развития резиновой промышленности, как и работа Goodyear в открытии отверждения серой. Ускорители сделали процесс отверждения намного более надежным и повторяемым.Через год после своего открытия Энслагер нашел сотни потенциальных применений своей добавки.
Так родилась наука об ускорителях и замедлителях схватывания. Ускоритель ускоряет реакцию отверждения, а замедлитель замедляет ее. В следующем столетии различные химики разработали другие ускорители и так называемые ультраускорители, которые делают реакцию очень быстрой и используются для изготовления большинства современных резиновых изделий.
Девулканизация
Каучуковая промышленность занимается девулканизацией каучука в течение многих лет.Основная трудность при переработке каучука состоит в девулканизации каучука без ухудшения его желаемых свойств. Процесс девулканизации включает обработку резины в гранулированной форме нагреванием и / или смягчающими агентами для восстановления ее эластичных качеств, чтобы можно было повторно использовать резину. Некоторые экспериментальные процессы достигли разной степени успеха в лаборатории, но были менее успешными при масштабировании до уровня коммерческого производства. Кроме того, разные процессы приводят к разным уровням девулканизации: например, использование очень тонкого гранулята и процесса, который производит поверхностную девулканизацию, дает продукт с некоторыми из желаемых качеств необработанного каучука.
Процесс переработки резины начинается со сбора и измельчения утилизированных шин. Это превращает резину в гранулированный материал, и все стальные и армирующие волокна удаляются. После вторичного измельчения полученный резиновый порошок готов к переработке продукта. Однако производственные применения, в которых можно использовать этот инертный материал, ограничены теми, которые не требуют его вулканизации.
В процессе рециркуляции каучука девулканизация начинается с отделения молекул серы от молекул каучука, что способствует образованию новых поперечных связей.Были разработаны два основных процесса рециркуляции каучука: модифицированный масляный процесс и водно-масляный процесс . В каждом из этих процессов масло и регенерирующий агент добавляются к регенерированному каучуковому порошку, который подвергается воздействию высокой температуры и давления в течение длительного периода (5-12 часов) на специальном оборудовании, а также требует обширной механической постобработки. Восстановленный в результате этих процессов каучук имеет измененные свойства и непригоден для использования во многих продуктах, включая шины.Как правило, эти различные процессы девулканизации не привели к значительной девулканизации, не смогли обеспечить стабильное качество или были слишком дорогими.
В середине 1990-х исследователи из Гуанчжоуского научно-исследовательского института по использованию повторно используемых ресурсов в Китае запатентовали метод регенерации и девулканизации переработанного каучука. Их технология, известная как AMR Process , призвана производить новый полимер с постоянными свойствами, близкими к свойствам натурального и синтетического каучука, и при значительно более низкой потенциальной стоимости.
AMR Process использует молекулярные характеристики вулканизированного каучукового порошка в сочетании с использованием активатора, модификатора и ускорителя, гомогенно реагирующих с частицами резины. Химическая реакция, происходящая в процессе смешивания, способствует разъединению молекул серы, тем самым позволяя воссоздать характеристики натурального или синтетического каучука. Смесь химических добавок добавляют к повторно используемому порошку резины в смесителе в течение приблизительно пяти минут, после чего порошок проходит процесс охлаждения и затем готов к упаковке.Сторонники процесса также утверждают, что в процессе не выделяются токсины, побочные продукты или загрязняющие вещества. Затем реактивированный каучук может быть смешан и переработан для удовлетворения конкретных требований.
В настоящее время Rebound Rubber Corp., владеющая североамериканской лицензией на процесс AMR, построила завод по переработке резины и лабораторию исследований / контроля качества в Дейтоне, штат Огайо. Завод выполняет производственные операции на демонстрационной основе или на небольших коммерческих уровнях. Переработанный каучук с завода в Огайо в настоящее время проходит испытания в независимой лаборатории для определения его физических и химических свойств.
Независимо от того, будет ли процесс AMR успешным, рынок нового каучука или его эквивалента остается огромным, причем только в Северной Америке ежегодно используется более 10 миллиардов фунтов (приблизительно 4,5 миллиона тонн). Автомобильная промышленность потребляет примерно 79 процентов нового каучука и 57 процентов синтетического каучука. На сегодняшний день переработанный каучук не используется в значительных количествах в качестве замены новому или синтетическому каучуку, в основном из-за того, что желаемые свойства не были достигнуты. Изношенные шины — это наиболее заметные отходы производства резины; по оценкам, только в Северной Америке ежегодно образуется около 300 миллионов утильных шин, причем более половины добавляется в уже огромные запасы.Подсчитано, что менее 10 процентов резиновых отходов повторно используется в любом виде нового продукта. Кроме того, Соединенные Штаты, Европейский Союз, Восточная Европа, Латинская Америка, Япония и Ближний Восток в совокупности производят около одного миллиарда шин в год, при этом, по оценкам, накопления составляют три миллиарда в Европе и шесть миллиардов в Северной Америке.
использует
У каучука много применений. Большинство промышленных применений — это контроль и гашение вибрации, используемые в автомобильных компонентах, таких как втулки стабилизатора, амортизаторы и опоры двигателя.Резина также используется для смягчения ударов блокирующего оборудования и создания уплотнений. Резина также используется в шинах для транспортных средств.
См. Также
Внешние ссылки
Все ссылки получены 31 августа 2019 г.
кредитов
Энциклопедия Нового Света писателей и редакторов переписали и завершили статью Википедия в соответствии со стандартами New World Encyclopedia . Эта статья соответствует условиям лицензии Creative Commons CC-by-sa 3.0 Лицензия (CC-by-sa), которая может использоваться и распространяться с указанием авторства. Кредит предоставляется в соответствии с условиями этой лицензии, которая может ссылаться как на участников New World Encyclopedia , так и на бескорыстных добровольцев Фонда Викимедиа. Чтобы процитировать эту статью, щелкните здесь, чтобы просмотреть список допустимых форматов цитирования. История более ранних публикаций википедистов доступна исследователям здесь:
История этой статьи с момента ее импорта в Энциклопедия Нового Света :
Примечание.