Антикор Центр
Основная наша специализация — обеспечение долгосрочной защиты от коррозии
и механических повреждений автомобиля.
Производимая защита кузова автомобиля:
• днище, арки
• скрытые полости
• протекция лакокрасочного покрытия
Основные услуги нашей компании:
• антикоррозионная обработка автомобилей
• защита ЛКП
• нанесение жидких подкрылок
• антигравийная защита
• шумо- и виброизоляция
• продажа материалов
Компания АнтикорЦентр занимается прогрессивной защитой автомобилей, используя исключительно высокотехнологичные материалыспециального назначения для самой надежной антикоррозионной и шумоизоляционной обработки
днища, арок, скрытых полостей (ML-метод) и всего кузова автомобиля.
Мы являемся официальными представителями шведской компании Dinitrol (Динитрол), специализирующейся на
разработке инновационных шумоизоляционных и антикоррозионных составов, зарекомендовавших себя во всем мире
высоким качеством и надежностью в эксплуатации.
Сотрудники нашей компании являются высококвалифицированными специалистами, прошедшими обучение в Швеции.
Компетентность наших мастеров позволяет удовлетворить потребности самых искушенных автовладельцев.
Окружающая среда содержит множество негативных факторов, таких как высокая влажность, температура и соли, которые подвергают коррозии автомобиль. Коррозионный эффект проявляется на всех автомобилях, не обработанных специальными антикоррозионными материалами, более того с каждым годом потери механической прочности металла будут только увеличиваться.
Большинство автовладельцев уверены в том, что производители автомобилей надежно защищают автомобиль от появления коррозии и автомобиль в полной безопасности. В большинстве случаев это вовсе не так, завод-изготовитель производит только лишь оцинковку, что совершенно не защищает кузов автомобиля от коррозии.
Автомобиль покрывается тонким цинкового состава, который способен защитить автомобиль максимум на год. особенно подвержены коррозии наличие сварочных швов. При отсутствии своевременной защиты кузова автомобиля, даже кузов с оцинкованной обработкой может образовать коррозию.
Коррозионные потери увеличиваются, при:
Больших температурных перепадах
Повышенной влажности воздуха
Отсутствии вентиляционной системы в гараже
Ремонте кузова автомобиля
Очень важно помнить о коррозии тем людям, которые хранят мокрые автомобили в гараже без вентиляционной системы. Это создает самый настоящий термостат, который мгновенно спровоцирует коррозию кузова автомобиля.
При начавшейся коррозии кузов теряет механическую прочность, вследствие чего автомобиль становится менее безопасным для водителя и пассажиров.
Основная специализация нашей компании — обеспечение долгосрочной защиты автомобиля от коррозии при помощи профессиональных составов марки Dinitrol шведского концерна Dinol.
Антикоррозийная обработка автомобиля. Антикор днища, арок, подкрылок в Нижнем Новгороде.
Каждый автомобилист старается защитить свое транспортное средство от негативного воздействия внешних факторов. Эффективным средством подобной защиты считается антикоррозийная обработка автомобиля.
Преимущества антикоррозийной обработки составом Tectyl
Для защиты наружных поверхностей транспортных средств от ржавчины принято использовать специальный состав Tectyl. Его преимущества проверенны тысячами автомобилистов. Во-первых, составы Te способствуют «самозалечиванию» проблемных участков автомобиля. Применение этого препарата помогает затягиванию участка оголившегося металла.
Во-вторых, антикоррозийная обработка автомобиля в Нижнем Новгороде проведённая в нашем центре посредством состава Tectyl сохраняет свойства даже при минимальных температурах (до -50 градусов). При этом составу не страшен ни холод, ни жара. Температура каплепадения состава «Тектил» достигает 150 градусов. В-третьих, стоит отметить проникающую способность этого препарата. Он способен подниматься по микрозазорам на 120 мм. Благодаря этому, обеспечивается обработка даже скрытых полостей.
Преимущества антикоррозийной обработки автомобиля при помощи Tectyl также имеет следующие:
- высокий процент «сухого» остатка»;
- адаптированность материала к экстремальным климатическим условиям России;
- обработки наружной поверхности автомобиля;
- цена.
Записаться на удобное время
Этапы антикоррозийной обработки
Антикоррозийная обработка автомобиля в «АвтоВариант» в Нижнем Новгороде состоит из таких этапов:
- Очистка днища и колесных арок. На первом этапе промывают днище автомобиля. С этой целью используется автоподъемник. Струю горячей воды направляют на днище транспортного средства под давлением 60-100 атмосфер.
- Сушка. На этом этапе выполняется продувка автомобиля посредством горячего воздуха.
- Обработка внутренних скрытых полостей нижней части кузова. Скрытые полости автомобиля обрабатывают с учетом особенностей кузова. Для обработки используется гибкий шланг с соплом, через которое подается антикоррозионный состав. Впрыскивание проводят порциями в течение 2-3 секунд.
- Обработка днища и колесных арок. Толщина пленки должна быть 250-300 мкм. Чрезмерно толстое покрытие может стать причиной отслаивания состава.
- Обработка внутренних полостей верхней части кузова. Процесс аналогичен обработке внутренних полостей нижней части кузова.
- Наружная обработка. После завершения последнего этапа антикоррозийной обработки автомобиль не должен эксплуатироваться в течение суток. Это время необходимо для того, чтобы состав «схватился».
Доступная цена антикоррозийной обработки позволяет автомобилистам надежно защитить свое транспортное средство от ржавчины, которая возникающей в результате езды по гравийным и грунтовым дорогам, а также по воде и снегу.
Наша автосервис предлагает осуществить антикоррозийную обработку вашего автомобиля средствами ведущего мирового производителя антикоров «Tectyl». Мы производим обработку днища автомобиля, арок, подкрылок. Предлагаем вам услугу нанесения жидких подкрылок. Всё это мы осуществим в короткие сроки, надёжно, качественными антикоррозийными материалами. Будем рады видеть вас в нашем сервисе! Записаться на антикоррозионную обработку в нашем автоцентре вы можете по телефону 8 (831) 413-10-63.
Мы работаем исключительно c составами ведущего мирового производителя
Как мы работаем?
Заявка
Вы звоните или оставляете заявку на сайте
Консультация
Мы вместе согласовываем варианты и стоимость работ, и Вы записываетесь на удобное Вам время
Обработка
Вы приезжаете к нам в сервис и мы в кратчайшее время обрабатываем Ваш автомобиль
Автомобиль готов
Удачного пути!
Наши клиенты о нас
Отличный сервис, отличная работа, замечательные мастера. Не жалею ни минуты. Качество на высоте. Успехов и процветания!
Михаил,
Нижний Новгород
Долго сомневался и наконец-то решился сделать жидкие подкрылки. Моему восторгу не было границ… В машине стало реально тише. Спасибо большое:) Рекомендую всем!
Андрей,
Нижний Новгород
Сделал антикор на новую машину. Сделали все быстро и качественно. Дали гарантию 5 лет. Обслуживание понравилось, да еще и осмотр бесплатный каждые полгода. Молодцы! Так держать!
Александр,
Нижний Новгород
Наши сертификаты
Антикор Авто, мастерская по антикоррозийной обработке автомобилей в Новосибирске на Шорная, 30 к1 — отзывы, адрес, телефон, фото — Фламп
Решил поменять авто, но кризис внёс свои коррективы, авто поменять не получилось и встал вопрос о сохранении. Надо сделать антикор. Пошарил по интернету, насмотрелся роликов, определился с материалом, каким делать обработку и начел обзванивать канторы кто занимается антикоррозийной обработкой.
Показать целиком
Решил поменять авто, но кризис внёс свои коррективы, авто поменять не получилось и встал вопрос о сохранении. Надо сделать антикор. Пошарил по интернету, насмотрелся роликов, определился с материалом, каким делать обработку и начел обзванивать канторы кто занимается антикоррозийной обработкой. Интернет дал маломальские представления как должен проходить процесс, но чем больше я обзванивал организации тем больше понимал, что все кому я звонил просто не понимают что делают либо делают как попало или человек отвечающий на вопросы не представляет о чём его спрашивают. Задаёшь вопрос как проходит процесс обработки ответ примерно один, загоняете утром, выбираете материал, моем днище, до обеда сохнет, обрабатываем, вечером собираем, утром забираете и всё. Как, а где сушка, зачистка, обезжиривание, сушка почти сутки после нанесения, а потом только сборка.
Какое было моё удивления, когда позвонил в «Антикор Авто» мне расписали весь процесс, как он и должен происходить, занимал он как минимум трое суток. При этом я даже вопросов не задавал было всё понятно, человек рассказывающий на другом конце провода точно знал о чём он говорит. Я потом два раза в день приезжал с проверками так нежданчиком, всё что должно быть сделано, всё сделали как надо. Промыли днище (прошу не путать с помыли это разные по значению слова, и результат), высушили, зачистили что было нужно, обезжирили, нанесли 600-720 микрон, а не 200-250. И заплатил дешевле чем у тех кому звонил, а обзвонил я не мало, в 2GIS более 30 кантор.
Работай доволен на все 200% всем друзьям своим рекомендовал.
Стасу и Никите спасибо за ответственный подход к делу, просто ПРОФИ.
Антикоррозийная обработка кузова автомобиля | Выбрать антикор для авто
Коллапс на валютном рынке показал, что в ближайшее время российские автолюбители будут массово отучаться от привычки менять автомобиль каждые 3 года. Очевидно, что многим из них станут интересны продукты, позволяющие существенно продлить срок жизни старого автомобиля. Поэтому некоторые автосервисы сегодня включают в свои услуги антикоррозийную обработку. Однако далеко не всегда этот вид работ выполняется правильно. Журнал «КУЗОВ» совместно со специалистами сети независимых СТО «Tuning-S» протестировали линейку защитных препаратов Dinitrol.
На протяжении двух десятилетий автопроизводители твердят, что современные автомобили не нуждаются в дополнительной антикоррозийной обработке. Одни концерны делают упор на оцинковку, другие используют гальванику и катафорез. Специалисты компании Dinitrol, ведущего производителя антикоррозийных защитных покрытий, путем лабораторных испытаний доказали, что соляной раствор при перепадах температур в кратчайшие сроки разъедает любой металл. Именно поэтому продукция компании востребована в авиастроении и даже используется при обработке железнодорожных составов.
Недостаточно постаринке «вымазать» днище машины гудроном. Современный автомобиль имеет огромное количество скрытых труднодоступных полостей, найти которые может только квалифицированный специалист при наличии технической карты автопроизводителя. Кроме того, для проведения качественной антикоррозийной обработки требуется специализированное оборудование, высококачественные составы и неукоснительное соблюдение предписаний поставщика химии.
Компания «ЮВК» не только реализует продукцию Dinitrol, но также оказывает консультативную и техническую поддержки своим клиентам. На тренингах специалисты независимых СТО получают наиболее полную информацию по необходимым инструментам и нормам использования расходных материалов бренда. Немецкое представительство компании-производителя DinolGmbh внимательно следит за появлением новых моделей автомобилей и в кратчайшие сроки предоставляет своим партнерам обновленные технологические карты, что гарантирует правильность и качество выполнения работ. Все продукты производятся на предприятиях в Германии и Швеции.
На примере автомобиля Mitsubishi L200 мы подробно рассмотрим весь процесс антикоррозийной обработки кузова автомобиля. В самом начале необходимо правильно подготовить поверхность. Машина загоняется на подъемник, где специалист снимает подкрылки и промывает днище мощным напором воды.
Влага высушивается тепловыми пушками, механически зачищаются очаги коррозии, и поверхность обезжиривается очистителем Dinitrol 7225 или 582.
Если автомобиль совсем новый, то обойтись можно лишь обезжириванием.
Теперь стоит определиться с видом антикора. Если клиента интересует дополнительная шумоизоляция, то ему подойдут «жидкие подкрылки» Dinitrol 479.
Наносится материал специальным пистолетом Dinitrol в два слоя (толщиной 1,5 мм каждый) с выдержкой в 15 минут при рабочем давлении от 6 до 10 атмосфер.
Высохшая поверхность покрывается шагренью, которая гасит потоки воздуха, поглощая шум от колес. В основе материала – синтетическая резина, которая позволяет надежно защитить поверхность от воздействия песка, камней и гравия.
Материал имеет 80% сухого остатка, поэтому при работе в прохладном помещении следует учесть, что емкости с продуктами предварительно нужно поставить на донный нагреватель и установить нагрев на уровне не выше 40 градусов.
На днище мы нанесли полуторамиллиметровый слой состава Dinitrol 4941 на восково-битумной основе, который противостоит коррозии и обеспечивает эффективную защиту от абразивных повреждений. Средний расход на автомобиль D класса – 4-5 литров.
Вышеупомянутые продукты можно заменить более прогрессивным, усиленным дисперсией алюминия восковым составом Dinitrol Metalliс, отличающимся высокой тиксотропией, лучшими антикоррозийными свойствами и хорошим шумопоглощающим эффектом. Материал также распространяется в 1, 5, 20, 60 и 208-литровых упаковках, покрывая потребности любого сервиса.
В каждом автомобиле сотни сварных швов и точек. Несмотря на оцинковку или гальванику, со временем металл в этих местах ослабевает, и кузов теряет прежнюю жесткость, что сказывается на безопасности. Предотвратить появление коррозии в скрытых полостях поможет Dinitrol 3641-А80. Но если «болезнь» уже запущена, то скрытые полости проливают Dinitrol Penetrant или Dinitrol ML. Эти влаговытесняющие составы, благодаря ингибиторам коррозии, обладают способностью проникать в ржавчину и консервировать химический процесс.
Следующим этапом работы является нанесение защитного антикоррозийного воска Dinitrol Korrotec 485 в местах, которые могут соприкасаться с кожей человека или одеждой. Обрабатываются крепления дверей и амортизаторов, водостоки, желоба и прочие стыки, а также соединения под капотом и в багажнике.
Некоторые клиенты предпочитают, чтобы на машине был виден антикор. В этом случае для обработки видимых частей порогов и бамперов подойдет Dinitrol 3641 бежевого оттенка.
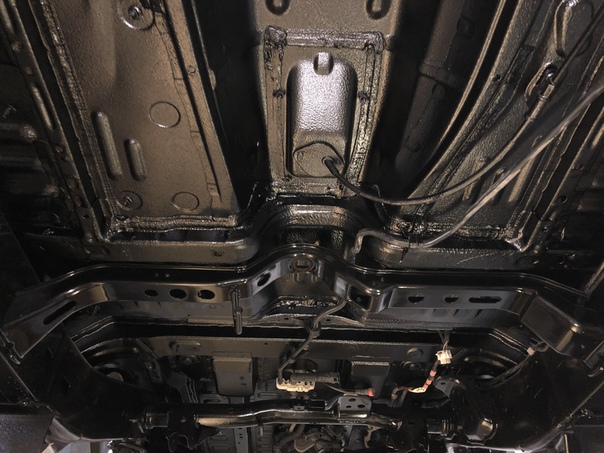
Антикоррозийная и антигравийная обработка днища автомобиля (антикор) – Профессиональный автосервис в Симферополе
Многие автовладельцы беспокоятся лишь о наружных панелях кузова машины, забывая о состоянии скрытых полостей и днища. А ведь именно там раньше всего зарождается коррозия.
Наш сервис предлагает вам решение данной проблемы! Это качественная антигравийная и антикоррозийная обработка днища автомобиля, коротко именуемая «антикор».
Какие преимущества дает такая обработка:
- предотвращение ржавчины и коррозии автомобиля;
- защита от вредного воздействия внешней среды — грязь, влага, пыль, гравий, песок, сажа, реагенты;
- дополнительная шумоизоляция днища автомобиля и колесных арок
Мы напрямую сотрудничаем с крупнейшим немецким производителем Wurth, который предоставляет нам для работы оригинальные качественные антигравийные и антикоррозийные материалы для обработки автомобиля.
Наш материал да работы на основе битумно-каучуковой смолы:
- Протестирован согласно DIN 50021
- Долговременная защита
- Высокая абразивная стойкость
- Антишумовой эффект
- Позволяет создать защитную пленку толщиной до 4 мм
- Прекрасно подходит для защиты колесных арок
- Высокая доля твердых включений (приблизительно 66%)
- После окончательного высыхания поверхность не усаживается (тестировано согласно DIN 53152)
- Хорошая защита от ударов камней
- Быстрое образование пленки и короткое время высыхания
- Пленка толщиной 600 мкм образуется через 60–90 мин
- Сокращение времени простоя при ремонтных работах
- Экологически безвреден
- Уменьшенное содержание растворителя
- Стойкий к брызгам, соленой воде, слабым кислотам и щелочам
- Термостойкость после полного высыхания −25…+80 °C
- Цвет: черный
Проведя профилактическую обработку нижней части автомобиля, вы сэкономьте себе немалые деньги, предотвратив траты на удаление ржавчины с кузова, сварочные и кузовные работы, потеря ликвидности автомобиля при продаже.
Дно автомобиля – это то, о чем стоит заботиться на протяжение всего времени эксплуатации автомобиля, а особенно собираясь за город, в дальнюю поездку или путешествие. Кузов постоянно подвергается механическому воздействию со стороны внешних факторов: гравия, песка и сажи. В дальнейшем подобные повреждения провоцируют возникновение ржавчины и коррозии. Для предупреждения и предотвращения этих процессов используется антикоррозийное антигравийное покрытие. Оно создает на поверхности непроницаемый защитный слой, который сохранит ваши детали от ржавчины и вредного воздействия внешней среды, а также обеспечит дополнительную шумоизоляцию арок и днища автомобиля.
Этапы работ:
• Подготовка (разборка, мойка, осмотр, сушка, зачистка, маскировка)
• Обработка днища, колесных арок (покрытие днища, колесных арок, антигравий, «жидкие подкрылки»)
• Сборка, мойка (контроль покрытия, установка снятых деталей, финальная мойка кузова, протирка стекол)
Цены:
- Седан класса A, B — от 6 000 р.
- Седан класса C — от 8 000 р.
- Кроссоверы и джипы — от 10 000 р.
Понравилось? Скорее звоните! +7 (978) 905-38-28
Ухаживаем за кузовом: антикор
Для того чтобы выбранное вами средство как можно прочнее сцеплялось с поверхностью металла, обработку следует производить на сухую чистую поверхность.
Уход за кузовом предполагает под собой текущий осмотр и обязательную антикоррозийную обработку кузова машины. Вот некоторые советы по уходу за Вашим транспортным средством.
Во время чистки автомобиля не рекомендуется использовать сухой материал, так как он может повредить лакокрасочное покрытие. Обычно для того чтобы вымыть конструкцию, требуется применить чистую воду, подаваемую несильной струей и мягкой губкой. Так как лакокрасочное покрытие не должно подвергаться сильному воздействию, не стоит использовать сильные вещества, которые могут испортить поверхность. К ним, как правило, относят сточные воды, а также содовые и щелочные растворы. При этом процедура мытья должна сопровождаться предварительной прочисткой дренажных отверстий некоторых элементов, таких как пороги, крылья и двери. Особенно осторожно следует относиться к промыванию моторного оборудования.
В теплый период года автомобиля следует мыть в тени на открытом воздухе. Но, как бы там ни было, после мытья поверхность следует протереть мягкой тряпкой, таким образом, можно будет избежать образования пятен. Зимой машину следует мыть в теплом помещении, так как на холодном воздухе вода превратится в лед и повлечет за собой образование трещин.
Для того чтобы лакокрасочная поверхность блестела, машину не стоит оставлять на солнце на слишком долгий промежуток времени. Также опасайтесь попадания кислот, тормозной жидкости, бензина и тому подобных веществ. Для большего визуального эффекта раз в год поверхность кузова покрывают специальными восковыми составами и обрабатывают антикоррозионным препаратом. Подобные составы не только придадут машине красоту, но и предотвратят появление коррозии. Если на поверхности машины отмечаются небольшие сколы или трещины, то нужно их подкрасить, предварительно зачистив. А для того чтобы под баком для топлива не появилось пятен, это место нужно протирать, для чего применяют старую ветошь.
В автомобиле существуют хромированные элементы, к которым относят ручки, бамперы, каемки фар и т.п. Для их чистки употребляют технический вазелин. А для резиновых деталей нужно взять ветошь, заранее смоченную в воде, растворители и бензин здесь не подойдут. Дело в том, что резина от действия этих средств быстро тускнеет. Для мытья грязных стекол в одном литре воды требуется растворить тридцать миллилитров жидкости НИСС 4.
Важно своевременно следить за чистотой в салоне. Обычно салон чистят один раз в месяц. Для удаления пыли можно использовать обыкновенный пылесос. Если на поверхности подушек появились жирные пятна, то их можно удалить следующим образом. Пятно сначала смачивают бензином, после чего присыпают тальком и обрабатывают щеткой. Если салон обит искусственной кожей, то применяют хозяйственное мыло с водой, больше здесь ничего не подойдет. После обработки место протирают тряпкой. Не забывайте и о жиклерах (элементах, с помощью которых промывают стекла). Для их чистки используют обыкновенную воду, которую подают струей небольшой силы.
Специалисты рекомендуют после каждых десяти тысяч километров пробега совершать промывание следующих узлов. Итак, для ухода за крышкой багажника и замочных скважин необходимо использовать порошкообразный графит, если чистка производится в теплое время года, применяют технический вазелин (обычно такое средство представлено в виде аэрозолей). Совет: прежде чем приступать к применению препарата, обрабатываемые части следует просушить сжатым воздухом. Для петлей, дверей и тяги привода капота обычно берут моторное масло, предназначенное для любого времени года.
Антикор для машины
Как уже было сказано, для того чтобы свести к минимуму появление коррозии на днище кузова, в скрытых полостях и колесных арках, автомобиль время от времени следует подвергать антикоррозионной обработке PRIM. Обычно процедуру подобного образца производят один раз в два года (некоторые владельцы делают это чаще и обрабатывают специальными препаратами свою машину один раз в год).
Для того чтобы выбранное вами средство как можно прочнее сцеплялось с поверхностью металла, обработку следует производить на сухую чистую поверхность. Поэтому прежде чем приступать к процедуре, машину необходимо хорошенько промыть и не менее качественно просушить, иначе эффекта не будет. Для мытья автомобиль поднимают на эстакаду, также можно использовать яму для осмотра транспортного средства. Мойка производится с использованием несильной струи теплой воды. Если Вы обладаете бывшим в употреблении автомобилем, лучше снять старое антикоррозийное покрытие, так как часто два средства могут не подойти по каким-то параметрам. Только после того как машина будет подготовлена, наносят антикор. После этого следует немного подождать до полного сцепления препарата с поверхностью металла.
Удачи на дорогах!
• У компании СИБУР новый логотип
• Мечта автомобилиста
Антикор для скрытых полостей Dinitrol
Причина уязвимости скрытых полостейВ труднодоступных и непроветриваемых местах автомобиля при эксплуатации скапливается влага и соли. Недостаточно качественное или отсутствующее антикоррозионное покрытие не способно защитить металл, в результате чего он начинает постепенно ржаветь. Если вы вовремя не остановите данный процесс, коррозия станет причиной появления сквозных дырок в кузове, от которых избавиться будет непросто и достаточно дорого.
Как защитить скрытые места?
Для защиты скрытых полостей автомобиля компания Dinitrol выпускает современные высококачественные составы, представленные в данном разделе нашего интернет-магазина. Они не только защищают металл от электролитических воздействий, но и имеют высочайшие проникающие свойства, поэтому попадают в микротрещины и преодолевают слой ржавчины, вытесняя соли и влагу, которые в некоторых местах просто невозможно удалить.
Что мы предлагаем?
Одним из лучших и наиболее популярных материалов для антикоррозионной обработки скрытых плоскостей является Dinitrol ML. Это уникальная жидкость на основе восковых компонентов, отличающаяся превосходной проникающей способностью. В составе присутствуют дополнительные компоненты:
- растворители;
- ингибиторы коррозии;
- пленкообразователи.
Все они способствуют созданию эффективной и долговечной защиты металла от развития коррозии.
Одним составом для антикоррозионной защиты скрытых полостей наш ассортимент не ограничивается. Существуют более универсальные материалы, среди которых
Dinitrol 1000 и Dinitrol Penetrant LT. Их мы продаем в виде евробанки или аэрозольных баллонов. Они тоже имеют хорошие проникающие свойства и предотвращают вредное воздействие окружающих факторов.
Удобство применения
Независимо от уникальных свойств антикоррозионных составов для скрытых полостей, перед их нанесением постарайтесь по возможности обработать основание. Очистите его от явных загрязнений и попытайтесь счистить ржавчину с металла жесткой щеткой или наждачной бумагой. Также воспользуйтесь очистителем Dinitrol Autocleaner, которые легко справляется с масляными пятнами, следами битума и другими загрязнениями.
После обработки основание необходимо хорошо просушить, после чего можно приступать к нанесению специального состава. Для надежности сделайте это в два подхода: первый слой сделайте более тонким, а второй нанесите потолще.
Мы гарантируем, что наши антикоррозионные составы для скрытых полостей надежно защитят ваш автомобиль от развития ржавчины и уберегут вас от сложного и дорогостоящего ремонта в будущем.
Антикоррозийные покрытия | AnCatt
Лучшая в мире антикоррозионная краска: Компания AnCatt успешно разработала отмеченную национальными наградами платформу для нанесения антикоррозионного покрытия для тяжелых условий эксплуатации, не содержащую тяжелых металлов (зеленую), с беспрецедентными характеристиками и экологичностью.
Технология покрытия AnCatt использовалась в сотнях независимых испытаний на коррозию и была проверена и награждена ведущими научными и промышленными организациями, такими как Американское химическое общество, Национальный саммит инноваций, Альянсы RICE, Национальный научный фонд, НАСА, США. .S. Государственный департамент, USAID и NIKE.
Покрытие состоит из грунтовки на основе уникальной проводящей полимерной нанодисперсии (CPND), верхнего слоя и дополнительного промежуточного слоя. Полимер обволакивает поверхность металла и превращает верхний слой в тонкий, но плотный слой оксида металла. Эта система действует как эффективный барьер, защищающий металлы от коррозии без использования пигментов тяжелых металлов, таких как хромат, свинец или цинк. Технология покрытия AnCatt значительно превосходит существующие продукты антикоррозионного покрытия на рынке, в 3-6 раз долговечнее, а также является первой в истории высокоэффективной антикоррозийной технологией, не содержащей тяжелых металлов (экологически чистой), что делает ее следующей. -генерация технологии антикоррозионных покрытий.
Характеристики покрытия
- Сверхмощная защита от коррозии: выдерживает более 13 000 часов в соляном тумане (ASTM B 117) без ржавчины и образования пузырей. Испытательные панели не имели видимых изменений внешнего вида: без трещин, отслаивания или выкрашивания.
- Экологически чистый: грунтовка не содержит пигментов тяжелых металлов, таких как цинк, хромат или свинец.
- Сильная адгезия: Адгезия при растяжении (прочность на отрыв) образцов составила 700-800 фунтов на квадратный дюйм после 1100 часов циклического атмосферного воздействия.Тесты на адгезию ленты на образцах получили идеальную оценку 5А для каждой повторности после 8300 часов воздействия соляного тумана
- Устойчивость к царапинам и проколам / самовосстановление
- Защищает многие металлы, кроме железа / стали. Например: цинк, алюминий, магний, медь, серебро, титан и т. Д.
- Поверхностная толерантность
- Двухкомпонентный алифатический уретан, используемый в качестве смолы для верхнего покрытия, обеспечивает:
- Исключительное сохранение блеска
- Отличная стойкость к истиранию
- Отличная химическая стойкость
- Тонкий и легкий: менее 1/2 текущей толщины покрытия
- Низкие затраты на сырье
- Простота изготовления: производится на традиционном оборудовании
- Легко наносится: применимо с имеющимся оборудованием для нанесения краски
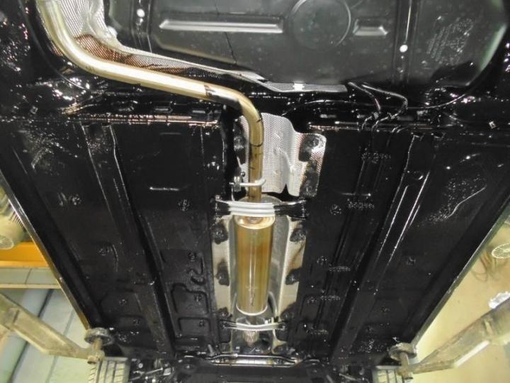
Результаты испытаний
Наши ускоренные испытания на коррозию были проведены известной независимой лабораторией KTA, расположенной в США. Верхний ряд сравнительных фотографий — это лицевая сторона стальных (crs) панелей, покрытых покрытием AnCatt CPND; нижний ряд — тыльная сторона панелей, покрытых акриловыми покрытиями КТА. 5000 часов — это максимальный час испытаний в соответствии с международным стандартом испытаний в солевом тумане (ASTM B 117). По прошествии 5000 часов испытаний покрытие AnCatt все еще оставалось неповрежденным, что было признано отраслевыми экспертами лучшим результатом из когда-либо существовавших.После 8 372 часов испытаний покрытие все еще может обеспечивать отличную адгезию при отрыве и отличные результаты адгезии ленты. Обратите внимание, что покрытие само герметизировалось от дальнейшего расширения ржавчины на линиях разметки. Мы подождали 13000 часов, и, что удивительно, ржавчина и образование пузырей остались на высшем уровне 10. Пожалуйста, посетите страницу испытаний коррозии или полный лабораторный отчет для получения более подробной информации.
Отраслевые СМИ:
- «Платформа AnCatt для экологически чистого антикоррозионного покрытия может обеспечить беспрецедентную защиту от коррозии для всех видов металлов.”
— Журнал CoatingsPro
«Показаны независимые тесты на коррозию. Это успешная технология антикоррозионного покрытия на основе проводящего полимера и первое покрытие без хрома, которое превосходит покрытия из шестивалентного хромата. Это также первая технология антикоррозионного покрытия для тяжелых условий эксплуатации, не содержащая тяжелых металлов ».
— Журнал PCI
«Защитное покрытие, достигающее новых высот в устойчивости и производительности.”
— Журнал «Мир промышленных покрытий»
«AnCatt Coating обещает произвести революцию на рынке антикоррозионных покрытий».
— Химический информатор
Использование
Наша система покрытия выдерживает суровые условия для защиты конструкционной стали, трубопроводов, резервуаров, мостов, морских платформ, ветряных электростанций, атомных электростанций, корпусов судов, портов, надстроек, палуб, самолетов, автомобилей, сельскохозяйственного оборудования и т. Д.В настоящее время наш целевой рынок включает в себя энергетику, нефть / газ, энергетику, горнодобывающую промышленность, машиностроение, автомобилестроение и авиакосмическую промышленность.
Наша грунтовка служит отличной заменой существующих покрытий на основе тяжелых металлов, не содержащих тяжелых металлов, с еще более сильными антикоррозийными свойствами. Наша текущая рецептура — это виниловые грунтовки и эпоксидные грунтовки. Другие продукты все еще в стадии разработки. У нас также есть система с низким содержанием летучих органических соединений и водная антикоррозионная система.
Антикоррозийный рынок
Ежегодно коррозия теряет триллионов долларов во всем мире.Фактически, недавние исследования оценивают прямые затраты на коррозию в Соединенных Штатах почти в 300 миллиардов долларов в год.
Шестивалентный хромат — хорошо известный канцероген, который очень токсичен для окружающей среды. Правительственные постановления ужесточают его использование во всем мире. О токсическом эффекте стало известно благодаря голливудскому блокбастеру 2000 года «Эрин Брокович» (с Джулией Робертс в главной роли). В этом теперь уже ставшем классикой фильме изображен реальный случай загрязнения питьевой воды шестивалентным хроматом, результатом которого стало крупнейшее судебное разбирательство в США.История С.
Благодаря своим превосходным антикоррозийным свойствам, грунтовки, содержащие хромат, до сих пор производятся большинством крупных компаний по производству красок, поскольку их характеристики еще не достигаются другими материалами. В настоящее время экологически безопасный рыночный стандарт цинка / оксидов цинка не может защитить легкие металлы, такие как алюминий и оцинкованную сталь, и они менее эффективны в жестких коррозионных средах. Кроме того, цена на цинк резко выросла за последние пару лет, и при текущих уровнях использования запасы цинка будут полностью истощены примерно к 2027 году.
Войдите в антикоррозийное покрытие AnCatt из проводящего полимера (на основе полианилина). Наша уникальная формула выдержала 13 000 часов испытаний в соляном тумане. Это покрытие является не только первым успешным антикоррозийным покрытием на основе полианилина после 35 лет интенсивных исследований в этой области во всем мире, но и лучше, чем любая технология антикоррозионного покрытия, представленная сегодня на рынке.
Коррозия обходится во всем мире в триллионы долларов — примерно 3-4% ВВП страны. На основе двухлетнего исследования Федерального управления автомобильных дорог США U.Затраты на коррозию S., опубликованные в 2002 году, прямые затраты на коррозию в США в 2001 году оценивались в 276 миллиардов долларов, а косвенные затраты были оценены примерно в такую же сумму. Органическое покрытие, наиболее широко используемый метод защиты от коррозии, составляет 88,3% от общих затрат на методы прямой защиты от коррозии, и в 2001 году только в США стоило 106 долларов США. Подробнее о влиянии коррозии в США, стоимости и разработках.
Воздействие на окружающую среду более стойкой антикоррозионной краски
Металл поднял человечество от бронзового века до железного века и даже усилился в современную эпоху, от строительства зданий до мостов, автомобильных дорог, автомобилей, авиации, судоходства, трубопроводов, машин.Следовательно, коррозия металла или старение и смерть металла — одна из самых больших затрат нашей экономики, если она не является самой большой движущей силой затрат. Тем не менее, коррозия металла считается непреодолимой природной силой, и единственный способ бороться с ней — это непрерывная перекраска и замена, что очень дорого для экономики и окружающей среды. Кроме того, современные технологии, использующие токсичные тяжелые металлы для борьбы с неудержимой и очень дорогой коррозией металлов, повышают токсичность, улучшают антикоррозионные свойства, с канцерогенными хроматами, были наиболее эффективными. Технология AnCatt может остановить непреодолимую естественную силу коррозии и без использования токсичных тяжелых металлов приведет человечество в совершенно новую эпоху беспрецедентной устойчивости, ресурсов и возможностей. Таким образом, прорыв в области антикоррозионного покрытия AnCatt может решить некоторые из величайших проблем, с которыми сегодня сталкивается человечество: глобальное потепление, кризис бюджета инфраструктуры, отходы, сокращение природных ресурсов и загрязнение окружающей среды, особенно загрязнение тяжелыми металлами из металлических покрытий.Технология AnCatt может высвободить огромное количество ресурсов, которые в настоящее время тратятся впустую в бесконечной борьбе с коррозией, чтобы улучшить качество жизни и обеспечить мир во всем мире, в том числе на металлических поверхностях. На последний проект перекраски моста Verrazano Narrow было вложено четверть миллиарда. Если краска прослужит в шесть раз дольше, прямая экономия на перекраске составит 4,5 миллиарда долларов в течение следующих 60 лет, если я буду считать только 3,2% годовых, не считая темпов роста.
Или наша краска стоимостью один миллион долларов может сэкономить 180 миллионов долларов на прямых расходах на перекраску моста.Косвенные затраты на перекраску, такие как покраска моста, вызванные пробками, в десять (10 раз) превышают затраты на покраску самого моста. Конечно, огромная экономия приведет к огромному сокращению выбросов углерода, но, что более важно, она включает два наиболее интенсивных антропогенных источника выбросов CO2: производство стали и производство цемента, которые производят 3,5 и 2 гигатонны выбросов CO2 в год. 40% стали, производимой в год, используется для замены корродированной стали, которая производит 1,4 (3,5 * 0,4)) гигатонны выбросов CO2 в год. Если краска может сделать сталь долговечной в шесть раз дольше, это уменьшит примерно.Выбросы СО2 5 гиготонн в год, которых достаточно, чтобы остановить глобальное потепление. Кроме того, 90% разрушения бетона произошли из-за коррозии арматуры внутри, цемент является основным ингредиентом бетона. Использование краски AnCatt, не содержащей тяжелых металлов, также может снизить затраты на смягчение воздействия на окружающую среду, связанные с использованием тяжелых металлов в антикоррозионных красках, загрязняющих воду и почву во время нанесения краски, технического обслуживания и после окончания срока службы.
Шестивалентный хромат — ядовитый враг №1 военной и авиационной промышленности.Свинец уже вызвал кризис воды, связанной со свинцом. Экологически совместимый цинк составляет более 85% рынка, но он по-прежнему является загрязнителем морской среды и неэффективен при ограниченном сроке службы. Антикоррозийная краска следующего поколения AnCatt обеспечивает отличную адгезию к металлической поверхности с использованием химического связывания, а не физического соединения, поэтому можно избежать нынешнего дорогостоящего и токсичного процесса подготовки поверхности для увеличения площади поверхности с целью улучшения физического связывания краски и металлической поверхности.Технология AnCatt устранила дорогостоящую подготовку поверхности, что позволило сократить время перекраски, стоимость и загрязнение почти вдвое. Краска AnCatt намного тоньше и не содержит тяжелых металлов, поэтому она делает покрытие намного легче, что может помочь снизить вес инфраструктуры и сэкономить энергию, необходимую для движения защищенных металлических конструкций, таких как корабль.
Краска AnCatt может защитить все виды металлов, поэтому уменьшает количество красок, которые необходимо поддерживать для защиты различных металлов.
Антикоррозийные пигменты Grace — SHIELDEX®
SHIELDEX ® нефосфатные, не содержащие хрома антикоррозионные пигменты защищают металл при использовании в грунтовках для рулонных покрытий общего промышленного назначения грунтовки и грунтовки для автомобильных и морских покрытий.Этот высокоэффективный ингибитор коррозии с последующим добавлением отвечает самым строгим экологическим стандартам и требованиям, обеспечивая нетоксичную альтернативу соединениям фосфата хрома (VI) и цинка для производства экологически чистых красок и покрытий, отверждаемых излучением. Эффективность ингибирования ржавчины пигмента SHIELDEX ® была тщательно проверена в различных условиях и подтверждена ускоренной инновационной технологией естественного атмосферного воздействия.
Покупатель Сервис и поддержка
В 1949 году компания Grace впервые применила синтетический диоксид кремния в высокоэффективных промышленных покрытиях. Наш опыт в области добавок к покрытиям проявляется в улучшении характеристик, которое вы можете измерить. Фундаментальное понимание Грейс инженерии частиц позволяет нам настраивать свойства поверхности, пор и частиц для конкретных приложений и помогает предлагать решения, специально разработанные для вашего приложения. А всестороннее понимание отраслевых процессов и проблем нашими преданными командами НИОКР и технической поддержки гарантирует, что вы получите максимальную отдачу от наших продуктов.
Для получения дополнительной информации о SHIELDEX ® Anti-Corrosion Pigments загрузите следующие брошюры:
Внешний вид | Белый порошок без запаха | |||
Средний размер частиц (мкм) | 5 | 3 | 3 | 3 |
pH | 9 | 9 | 9 | 8 .7 |
Плотность (г / см3) | 1,8 | 1,8 | 1,8 | 1,8 |
Маслоопоглощение (г / 100 г) | 60 | 60 | 80 | 80 |
SHIELDEX® AC 5 Пигмент | Стандартный класс:
1-4 вес. Системы на основе растворителей: 3-7 мас.% от состава |
SHIELDEX® AC 3 Пигмент | Тонкопленочные системы:
3-5 мас.% От состава Двухкомпонентные системы: 5- 7 мас.% От состава |
SHIELDEX® C 303 Пигмент | Специальная марка для реактивных грунтовок :
6-9 мас.-% от состава Порошковые покрытия: ≈10% масс. от состава |
SHIELDEX® CS 311 Пигмент | Грунтовки, катушки, GI, автомобильная; специально для систем кислотного отверждения Покрытия рулонов: 6-9 мас. Порошковые покрытия: ≈10 мас.% По рецептуре |
Как Для защиты оборудования от коррозии
На промышленных предприятиях коррозия является самой большой причиной поломки машин и оборудования, включая машины, сосуды, конструкции, опоры и трубопроводы.Хотя атмосферная коррозия в виде воздуха (кислород) и воды (влага, влажность, пар и т. Д.) Является основной причиной, факторы окружающей среды, включая высокие температуры и давления, а также агрессивные вещества, химические вещества и газы, также могут ускорить коррозию. из углеродистой стали и других металлов.
За пределами морской среды, подверженной воздействию солевого тумана или соединений, вызывающих коррозию, обычные газообразные промышленные загрязнители воздуха, такие как диоксид серы, озон и диоксид азота, могут вызывать коррозию.Так же может подвергаться воздействию промышленных химикатов, таких как хлориды, уксусная кислота и формальдегид. «Существует огромная потребность в антикоррозийном покрытии, которое может наноситься на участки, где обычные покрытия имеют тенденцию к разрушению», — говорит Джои Тейлор, президент IPI, американского подрядчика по окраске / нанесению покрытий для коммерческого и промышленного строительства. «В некоторых проектах необходимо удалить хлориды для достижения максимальной производительности. Но в большинстве случаев это может быть непомерно дорого ».
Покрытия на основе химически связанной фосфатной керамики (CBPC)
К счастью, для промышленных предприятий с активами, подверженными экологической коррозии, новая категория прочных, химически связанных фосфатно-керамических покрытий (CBPC) помогает остановить коррозию, упростить нанесение и сократить время простоя производства .
При переработке алюминия его плавят, чтобы отделить чистый металл от примесей. В результате этого процесса образуются отходы, называемые соляной лепешкой, которые содержат соединения, способствующие коррозии. В результате обычные антикоррозионные покрытия барьерного типа, такие как полимерные краски, могут преждевременно выйти из строя. Это особенно верно, когда краска поцарапана, потрескалась или потрескалась, а промоторы коррозии попадают в зазор между основой и покрытием. Тогда покрытие может действовать как теплица, улавливая стимуляторы коррозии, что позволяет коррозии распространяться под покрытием.
Итак, когда заводу по переработке алюминия в Западной Вирджинии потребовалась защита от коррозии для своей работы, он искал долгосрочное решение, которое не потребовало бы частого повторного покрытия, по словам Тейлора, участвовавшего в проекте. «Заводу по переработке не повезло с обычными антикоррозийными покрытиями, которые прослужили всего около трех или четырех лет», — говорит он. «На самом деле, любой, кто пытается защитить свое имущество от коррозии, хочет, чтобы его покрытие прослужило намного дольше.”
Что такое EonCoat?
Для обеспечения долговременной защиты от коррозии в суровых условиях завод и Тейлор обратились к EonCoat, неорганическому покрытию, наносимому распылением, от одноименной компании. EonCoat представляет новую категорию прочных CBPC с уникальными свойствами.
В отличие от традиционных полимерных покрытий, которые наносятся поверх подложки, коррозионно-стойкое покрытие CBPC связывается с подложкой посредством химической реакции. Покрытие можно наносить даже на ржавую влажную сталь.Образуется слой сплава. Это делает невозможным проникновение активаторов коррозии, таких как кислород и влажность, за покрытие, как это происходит с обычными красками.
Хотя традиционные полимерные покрытия механически связываются с основами, которые были тщательно подготовлены, при выдолблении влага и кислород будут мигрировать под пленку покрытия со всех сторон канавки. Напротив, такое же повреждение подложки с керамическим покрытием не приведет к распространению коррозии в промышленной инфраструктуре, поскольку поверхность углеродистой стали превращена в сплав стабильных оксидов.Как только поверхность стали становится стабильной (как стабильны благородные металлы, такие как золото и серебро), она больше не вступает в реакцию с окружающей средой и не может подвергаться коррозии.
Преимущества EonCoat
EonCoat, видимый на фотографиях, сделанных с помощью сканирующего электронного микроскопа, не оставляет зазора между сталью и покрытием, поскольку связь является химической, а не механической. Поскольку зазора нет, даже если влага должна проникнуть к стали из-за зазубрины, влаге некуда перемещаться, что эффективно предотвращает коррозию в промышленных применениях.
Барьер от коррозии также покрыт керамическим слоем, который устойчив к коррозии, воде, ударам, истиранию и химическим веществам, а также огню и температурам до 450 ° C. По словам Тейлора, для такой долговечной защиты от коррозии компания IPI успешно нанесла EonCoat на два промышленных пылесборника (один 60 000 кубических футов в минуту и один 40 000 кубических футов в минуту), включая четыре резервуара высотой до 40 футов и связанные с ними воздуховоды. «Антикоррозийное покрытие CBPC рассчитано на значительно более длительный срок службы, чем традиционные покрытия, поэтому частое повторное покрытие не должно быть проблемой», — говорит он.
Руководители промышленных предприятий или инженеры по коррозии, стремящиеся сократить расходы, также находят дополнительные преимущества у покрытий CBPC помимо коррозионной стойкости. Такие покрытия состоят из двух безопасных компонентов, которые не взаимодействуют друг с другом, пока не будут нанесены с помощью стандартной промышленной системы множественного распыления, подобной тем, которые обычно используются для нанесения покрытий из пенополиуретана или полимочевины. Поскольку покрытия CBPC неорганические и нетоксичные, они не содержат летучих органических соединений, HAP и запаха. Это означает, что водорастворимые негорючие покрытия можно безопасно наносить даже в ограниченном пространстве или когда соседние части установки продолжают работать.
Однако одним из самых больших преимуществ является быстрое возвращение к работе, сводящее к минимуму время простоя оборудования. Экономия времени на проектах по антикоррозийному покрытию достигается как за счет упрощенной подготовки поверхности, так и за счет ускоренного времени отверждения. При использовании типичного промышленного покрытия для подготовки поверхности требуется струйная очистка почти белого металла (NACE 2 / SSPC-SP 10). Но с керамическим покрытием обычно требуется только промышленная струйная очистка NACE 3 / SSPC-SP 6.
При использовании традиционных покрытий требуется обширная подготовка поверхности, которая проводится постепенно, чтобы избежать окисления поверхности, широко известного как «мгновенная ржавчина», которая может потребовать повторной струйной обработки.Однако с покрытием CBPC мгновенная ржавчина не является проблемой. Нет необходимости «сдерживать взрыв». Причина этой уникальной характеристики CBPC связана с присутствием железа в ржавчине, которое помогает создать слой сплава фосфата магния и железа. Именно этот слой сплава позволяет CBPC столь эффективно защищать углеродистую сталь от коррозии.
«Обычные покрытия требуют, чтобы вы загрунтовали основу каждый день, чтобы не потерять струю», — говорит Тейлор. «Вы должны прекратить пескоструйную очистку рано утром, а затем прогрунтовать [основание] до конца дня. Это требует трудоемких ежедневных операций по демонтажу и настройке окрасочного оборудования.
«Однако с EonCoat, если у вас будет чистая поверхность основы, без прокатной окалины и покрытия, она не повредит, если на ней появится ржавчина. Таким образом, вы можете продолжить нанесение покрытия [на следующий день] без необходимости повторной пескоструйной обработки основания, повторной грунтовки или установки и демонтажа оборудования для покраски каждый день. Вы можете продолжать работать всю 12-часовую смену. Это сэкономило нам около 50 часов рабочей недели над проектом ».
Для традиционных покрытий «трехкомпонентной системы» с использованием полиуретанов или эпоксидных смол время отверждения может также составлять дни или недели до нанесения следующего слоя, в зависимости от продукта.Напротив, антикоррозийное покрытие для углеродистой стали с использованием керамического покрытия в один слой почти не требует времени отверждения.
«Мы смогли завершить проект от начала до конца за девять недель, включая подготовку основания, распыление и нанесение высокопроизводительного верхнего покрытия с минимальным нарушением работы завода», — говорит Тейлор.
Руководители промышленных предприятий, которым требуется более надежная и долговременная защита от коррозии в суровых условиях, обнаружат, что покрытия CBPC значительно повышают безопасность, производство и прибыль.
Антикоррозионные покрытия — Антикоррозийные покрытия
Crossroads Coatings широко известна в отрасли благодаря нашему обширному перечню рецептур коррозионно-стойких покрытий. Эти покрытия защищают металлические компоненты от разрушения из-за влаги, солевого тумана, окисления и воздействия УФ-лучей и различных экологических или промышленных химикатов. Наши антикоррозийные покрытия весьма разнообразны в применении, но мы обычно продаем их клиентам в нефтяной, автомобильной и горной промышленности.Также к покрытию металлических дверей, декоративного железа и другого металлического оборудования.
МЫ — ФОРМУЛЯТОР ПОКРЫТИЙ НА ЗАКАЗ
Мы разрабатываем и формулируем высококачественные антикоррозийные покрытия для применения во всех отраслях промышленности. Запросите расценки на поставку покрытий по индивидуальному заказу сегодня!
Типы коррозионно-стойких покрытий
Высококачественные антикоррозионные покрытия, производимые Crossroads, позволяют защитить металлические поверхности, выступая в качестве барьера для окисления.У нас уже есть широкий спектр антикоррозионных покрытий, и их можно настроить для любого применения. Мы поставляем:
- Фторполимер — смеси смолы и смазки, обеспечивающие отличную защиту от коррозии
- Эпоксидная смола, воздушная сушка — экономичное антикоррозийное покрытие
- Эпоксидная смола, термоотверждаемая — отличная ударопрочность, а также устойчивость к коррозии и истиранию
- Фенольный — идеально подходит для сред с низким pH и высокой температурой
- Фосфат — покрытие из черных металлов для защиты от истирания и незначительной коррозии
- Полиуретан — глянцевое верхнее покрытие для эпоксидной смолы и неорганического цинка
- Цинк неорганический — защита стали от коррозии и атмосферных воздействий
- PTFE — оригинальное антипригарное покрытие, выдерживающее высокие температуры
- FEP — ПТФЭ с повышенной стойкостью к истиранию
Многие из этих антикоррозионных защитных покрытий также обеспечивают стойкость к истиранию, антипригарные свойства и химическую защиту.
Применение антикоррозионного покрытия
Мы создаем индивидуальные покрытия для различных областей применения в различных отраслях промышленности:
С помощью нашего современного испытательного оборудования каждая партия наших антикоррозионных покрытий проверяется на качество и подтверждает их соответствие любым установленным стандартам. Свяжитесь с нами сегодня, и мы будем рады помочь вам правильно начать свой проект по нанесению покрытий, предоставив покрытие, идеально соответствующее вашим требованиям.
Нажмите здесь, чтобы запросить ценовое предложение, или позвоните нам по телефону 1.833.724.6816Высокоэффективные антикоррозионные полиэфирные покрытия для мягкой стали в средах со смешанными кислотами
Образец мягкой стали был выбран из резервуаров для хранения кислоты, используемых в промышленности в качестве подложки, и были разработаны два передовых технологических покрытия на основе полимерных смол, обозначенные как LAM-P на основе смолы, которая представляет собой покрытие LAM-P / FR, и на основе смолы LAM-V, которое представляет собой покрытие LAM-V / FR. Эти покрытия были нанесены на стальные образцы с использованием ручного способа укладки. Тест FTIR был проведен для подтверждения полного отверждения, а SEM-анализы использовались для исследования морфологии поверхности.Серия электрохимических испытаний была проведена в кислой среде (смешанный раствор кислоты 56% H 2 SO 4 + 26% HNO 3 + 18% H 2 O по весу). Результаты показали успешное развитие LAM-P / FR и LAM-V / FR для получения покрытий с желательными характеристиками, такими как антикоррозийное покрытие, толщина, адгезия, стабильность, накопление заряда и повышенная устойчивость к кислой среде. Данные EIS для смешанных кислотных накопителей показали, что покрытие LAM-V / FR имеет более высокую прочность в смешанном кислотном растворе, более высокие значения импеданса и фазового сдвига, более высокое значение R , поры и низкое значение C c ; Процент снижения скорости коррозии составляет 96% для LAM-P / FR и 99.
96% LAM-V / FR по сравнению с образцом из мягкой стали без покрытия. Результаты этого исследования могут помочь в разработке руководящих принципов для антикоррозионных покрытий для промышленного применения.
1. Введение
Коррозия — это электрохимический распад материалов, который вызывается реакцией между материалами и агрессивными или коррозионными средами. Металлы наиболее восприимчивы к такому типу ударов, потому что они содержат свободные электроны и могут образовывать электрохимические ячейки в своей структуре [1].Коррозия приводит к значительным экономическим потерям и замедляет экономический рост всех стран. Ежегодные затраты на коррозию во всем мире оцениваются в 2,2 триллиона долларов США. Национальная ассоциация инженеров по коррозии (NACE) подсчитала, что прямая причина коррозии в США составила 276 миллиардов долларов в 2014 году, что составляет примерно 3,1% валового внутреннего продукта (ВВП). Однако, с учетом косвенных потерь от коррозии, это было оценено превысить 1 триллион долларов США.
При смешивании серной кислоты (H 2 SO 4 ) и разбавленной азотной кислоты (HNO 3 ) они становятся очень коррозионными.Коррозия в резервуаре для хранения кислоты зависит от нескольких факторов, таких как температура, концентрация коррозионных компонентов, условия эксплуатации и чистота используемых кислот [2]. Скорость коррозии низкоуглеродистой стали в 95% H 2 SO 4 составляет 5–20 мм / год при температуре ниже 25 ° C. Это зависит от материала, из которого изготовлен резервуар, и чистоты получаемой кислоты [3].
Коррозия, вероятно, является одной из наиболее серьезных проблем, с которыми сталкиваются в практических приложениях, поэтому по всему миру добавляются различные исследовательские стратегии с единственной целью защиты различных материалов от коррозии в различных областях применения.Многие методы используются для защиты конструкций от коррозии путем добавления ингибиторов коррозии [4, 5], применения катодной и анодной защиты [6, 7], модификации конструкции, изменения окружающей среды и, что наиболее важно, изменения материала, который больше подвержен коррозии. стойкая, например нержавеющая сталь [8]. Еще одним популярным методом защиты металлов от агрессивных коррозионных реакций является нанесение различных видов защитных покрытий [9, 10]. Исследователи постоянно ищут новые инновационные покрытия, которые улучшат защиту активов от коррозии в обычных средах [11].
Ананда Кумар и др. [12] в 2008 г. изучали коррозионное поведение низкоуглеродистой стали с полимерным и полимерно-металлическим двухслойным покрытием. Для синтеза покрытий использовалась методика циклической вольтамперометрии, а для исследования — методы EIS и потенциодинамических испытаний на коррозию. Защитный механизм покрытия на основе ПАНИ выполнял роль защитного барьера; однако существуют ограничения из-за пористости покрытий на основе ПАНИ. В двухслойных покрытиях из полианилина (PANI) металлические наночастицы заполняли пористые участки PANI, и защита была лучше, чем на основе PANI, из-за двойного действия барьерных и жертвенных свойств.Кроме того, покрытие на основе ПАНИ-Zn обеспечивает лучшую защиту, чем ПАНИ-Ni.
Shittu et al. [13] использовали метод потери веса для изучения коррозионного поведения мягкой стали с полистирольным покрытием, HCl и H 2 SO 4 испытательных сред. Подавление коррозии мягкой стали увеличивается при высокой концентрации полистирола, но уменьшается с увеличением времени.
Syed et al. [14] исследовали защиту от коррозии нержавеющей стали 316L с помощью полимерного многослойного покрытия; Композитное покрытие полианилин полиакриловая кислота / полиэтиленовый рудник (PANI / PAA / PEI) было приготовлено и нанесено на подложку методом центрифугирования.Исследование показало, что комбинация покрытий обеспечивает необходимую коррозионную стойкость, когда подложка помещается в среду 3,5% NaCl, как это наблюдалось во время электрохимических измерений. Повышение коррозионной стойкости можно объяснить тем, что путь диффузии ионов коррозии увеличился за счет многослойной структуры.
Амин Уддин Аммар и др. [15] в своем исследовании выбрали два покрытия на основе нанокомпозитов: одно на полимерной основе — ПВС / ПАНИ / ФЛГ, а другое — на керамической основе — TiO 2 / GO. Оба покрытия были нанесены на образцы методом погружения. Электрохимические испытания проводились в морской воде и в среде сырой нефти. Исследование EIS показало, что покрытие на керамической основе демонстрирует высокие значения импеданса и фазового сдвига на графике Боде, в то время как, с другой стороны, результаты Найквиста показали, что покрытие TiO 2 / GO удовлетворяет высоким значениям импеданса и имеет повышенную долговечность до разрушения. по сравнению с покрытиями ПВА / ПАНИ / ФЛГ. Кроме того, в случае сырой нефти результаты были другими по сравнению с морской водой.В сырой нефти образцы, покрытые PVA / PANI / FLG, обеспечивали большую защиту по сравнению с образцами, покрытыми TiO 2 / GO.
В представленной работе поверхность низкоуглеродистой стали покрыта защитными полимерными покрытиями. Были изготовлены резервуары для хранения из мягкой стали по индивидуальному заказу, на которые были нанесены антикоррозионные покрытия LAM-V / FR и LAM-P / FR. Исследован состав различных покрытий, включая сложноэфирные составляющие. Аналитические методы EIS и тафел-сканирования применялись с использованием потенциостата Gamry, а SEM использовался для определения морфологии поверхности.
Композитные покрытия на основе полимеров обсуждаются с точки зрения их коррозионной стойкости как с точки зрения условий покрытия, так и с точки зрения снижения скорости коррозии. Процент снижения скорости коррозии LAM-P / FR составил 96%, а LAM-V / FR — 99,96% по сравнению с образцами из чистой мягкой стали.
2. Методология
Изучены и сравнены антикоррозионные свойства двух типов композитных покрытий на основе полиэфира, ламинатного покрытия, армированного виниловым волокном, и ламинатного покрытия, армированного небными волокнами (LAM-V / FR и LAM-P / FR). когда они находились в кислой среде.Антикоррозионное поведение мягкой стали в кислой среде было использовано в качестве эталона.
На рисунке 1 показаны материалы и химические реакции, участвующие в приготовлении покрытий LAM-V / FR и LAM-P / FR. В первом покрытии ненасыщенная и неотвержденная полимерная V-смола использовалась для покрытия резервуаров из мягкой стали. Это произошло, когда он вступил в реакцию с мономером стиролом в присутствии МЕКП и образовал затвердевший композит. Во втором покрытии для покрытия использовалась ненасыщенная смола P-4, которая реагирует со стиролом в присутствии MEKP и образует покрытие на мягкой стали в соответствии с химическими реакциями, показанными на рисунке 1.
Два типа покрытий (LAM-V / FR и LAM-P / FR) были исследованы в кислой коррозионной среде, в которой образцы обоих покрытий вместе с оголенным металлом испытываются и сравниваются. Порядок тестирования можно увидеть на рисунке 2. Первый шаг включает подготовку образцов; затем покрытие было синтезировано на мягкой стали для подтверждения отверждения, и был проведен анализ FTIR. Для изучения эффективности покрытия был проведен анализ EIS. Наконец, было проведено сравнение результатов для мягкой стали с покрытием и без покрытия, и был сделан вывод, что покрытие предотвращает коррозию мягкой стали и увеличивает срок службы резервуаров для кислоты.
2.1. Подготовка проб
2.1.1. Подготовка образца мягкой стали.
Стальные пластиныBS436043A использовались для изготовления различных типов стальных болтов, стальных сварных швов, резервуаров для хранения и других конструктивных элементов со следующими составами [3]. Таблица 1 демонстрирует состав мягкой стали; то есть он состоит из 0,25% углерода (C), 0,50% диоксида кремния (Si), 1,6% марганца (Mn), 0,05% фосфора (P), 0,05% серы (S) и 0,20–0,35 % меди (Cu).
|
2.1.2.Приготовление покрытия LAM-V / FR
LAM-V / FR представляет собой двухкомпонентную систему покрытия на основе полиэфирной смолы, армированную волокном, наносимую шпателем и кистью. Благодаря наличию нескольких слоев перекрывающегося волокна достигается чрезвычайно низкая проницаемость водяного пара. Отличная стойкость к проникновению — особенность этого покрытия, обеспечивающая долгий срок службы. Эта система покрытия / футеровки состоит из желейного покрытия и двух слоев смолы LAM-V, наносимых шпателем и кистью с заданной толщиной 40 мм. Для определенных условий эксплуатации могут быть рекомендованы более толстые и дополнительные слои.В таблице 2 представлена толщина покрытия. Выявлено, что первичное покрытие связующего имеет толщину 2–5 мм, в то время как смола ЛАМ-В вместе с волокнистым материалом имеет толщину 60–80 мм.
|
Сначала поверхностные загрязнения были удалены с помощью ацетона для подтверждения адгезии новой системы покрытий LAM-V / FR. Смолы ЛАМ-В содержат 30–50 мас.% Мономеров [16, 17]. Смолы LAM-V вступили в реакцию радикальной сополимеризации с катализатором. На рис. 3 показан механизм сети, образованной радикальной реакцией сшивания. Перекись (катализатор) и ускоритель добавляются к смоле LAM-V, которая уже была растворена в мономере / растворителе (действует как сшивающий агент) в различных соотношениях смешивания. Кроме того, раствор пигмента P1 был добавлен либо к смоле базового покрытия, либо к смоле верхнего покрытия. Это обеспечит чередование цветных слоев, что обеспечит полное покрытие.В качестве армирующего материала использовался волокнистый мат. Компоненты грунтовки и облицовки были рассчитаны, и добавленные количества были наилучшими для отверждения этих заранее измеренных количеств, включая полимерную смолу и отвердитель, как схема слоев, показанная на рисунке 3.
2.1.3. Приготовление покрытия LAM-P / FR
Смола LAM-P представляет собой ненасыщенный полимер, который уже растворен в растворителе, чтобы уменьшить его вязкость и принять участие в реакции полимеризации с поперечными связями. Используемая здесь смола имеет среднюю реакционную способность и среднюю вязкость [18].Это связано с тем, что P-смола растворяется в стироле и действует как мономер, а также как растворитель; поэтому вязкость снижается до средней. В таблице 3 представлена толщина покрытия. Выявлено, что первичное покрытие связующего имеет толщину 2–5 мм, тогда как смола ЛАМ-П-4 вместе с армированным волокном материалом имеет толщину 60–80 мм.
|
2.2. Методика коррозионных испытаний
После синтеза и нанесения покрытий на образец было проведено электрохимическое испытание. Была проведена спектроскопия электрохимического импеданса (EIS). EIS для металлической основы с покрытием измеряет два явления, которые показывают ухудшение органического полимерного покрытия при контакте с электролитом, а также увеличение скорости коррозии основы из-за разрушения покрытия и ударного воздействия электролита [19].
На рисунке 4 показана схема испытательной установки EIS.Для исследования использовалась трехэлектродная система потенциостата [20, 21].
В приведенной выше установке низкоуглеродистая сталь используется в качестве рабочего электрода, графит — в качестве противоэлектрода, а серебро-хлорид серебра — в качестве электрода сравнения. Смешанная кислота используется в качестве электролита и имеет массовый процентный состав 56% H 2 SO 4 , 26% HNO 3 и 18% H 2 O. LAM-V / FR и LAM-P / Покрытия FR были разработаны для мягкой стали и использовались в качестве барьера между мягкой сталью и электролитом.Стеклянная ячейка закреплялась поверх образца из мягкой стали с покрытием с помощью герметика [22].
Данные EIS дополнительно анализируются с использованием подгоночных моделей; эти модели используются в зависимости от типа покрытия и окружающей среды. Создается следующая информация об испытуемом материале (металлах, покрытиях) и окружающей среде; (i) сопротивление электролита, (ii) емкость двойного слоя, (iii) сопротивление поляризации, (iv) сопротивление переносу заряда и (v) емкость покрытия.
Для этого исследования использовалась кислая среда / электролит.Кислотный состав, для которого были получены данные EIS, представлен в Таблице 4. Он показывает состав смешанной кислоты, которая хранилась в резервуарах из мягкой стали, и кислотный состав составляет 56% H 2 SO 4 , 26% HNO 3 , 0,60% HNO 2 и 17,40% H 2 O. Этот состав был взят в качестве электролита в электрохимической ячейке.
|
После ввода данных в программное обеспечение Gamry, показанное на рисунке 5, в котором начальная частота была установлена на 100000 Гц, конечная частота составляла 0,2 Гц, а напряжение переменного тока было установлено на 20 мВ. Последовательность сбора данных представлена в виде (i) потенциала холостого хода (OCP), (ii) графика Боде и (iii) графика Найквиста. Соответствующая подгоночная модель была применена после испытания и когда были получены все три графика, чтобы предоставить информацию о таких свойствах, как сопротивление нескомпенсированного раствора ( R и ), сопротивление покрытия ( R , покрытие ), емкость покрытия ( C c ), сопротивление пор ( R пор ), сопротивление поляризации ( R p ) и емкость двойного слоя ( C dl ).
3. Результаты и обсуждение
3.
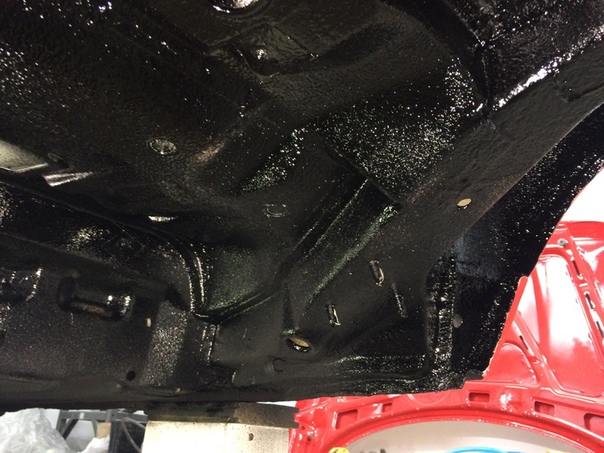
На рисунке 6 показаны пики пропускания FTIR-спектров смолы. Сильный и слабый пик при 776 см -1 и 1004 см -1 возникает из-за связи C-H, присутствующей в 1 и 3 положениях бензольного кольца, соответственно, в ненасыщенной полиэфирной смоле. С другой стороны, пик при 1306 см -1 появляется из-за группы -C = C- полиэфира.
Линия пропускания с широким спектром при 1119 см -1 показывает присутствие связи сложного эфира C-O-C, в то время как пик при 1719 см -1 является характерным пиком -C = O, который подтверждает присутствие сложноэфирная группа в полиэфирной смоле.
3.2. Спектральный анализ армированного волокном композита
Спектральные пики отвержденной смолы показаны на рисунке 7. Пики при примерно 2,985 × 10 3 см -1 демонстрируют более резкие тенденции и пики, которые обусловлены -CH = CH- группы исчезают в армированном полимером композите. При 1,408 × 10 3 см -1 в армированном полимерном композите становится видимым вновь возникший острый пик, как видно в спектре FTIR. Это показывает присутствие алкенов и подтверждает участие алкенов -CH = CH- в группе алканов.Это указывает на то, что двойные связи в ненасыщенной смоле являются реактивными центрами, которые исчезают и появляется пик одинарной связи. Это происходит в процессе отверждения, и происходит превращение этой группы в алканы в процессе сшивания. Это происходит из-за поперечно-сшивающей полимеризации ненасыщенной смолы в насыщенный основной композит.
3.3. SEM образца мягкой стали без покрытия / без покрытия
На рис. 8 показаны микрофотографии пузырей в мягкой стали, образовавшихся в результате реакции коррозии, с помощью SEM.Эти пузыри являются результатом проникновения водорода на поверхность из низкоуглеродистой стали. Когда низкоуглеродистая сталь подвергается коррозии в присутствии смешанной кислоты (H 2 SO 4 + HNO 3 + H 2 O), образуется атомарный и молекулярный водород. Если есть пустоты и пространства, то этот атомарный водород собирается в этих пустых отверстиях, поэтому постепенно давление увеличивается, а затем происходит образование пузырей. Это также показывает, что имела место реакция между ионами, присутствующими в смешанном растворе кислоты, и материалом из мягкой стали.Эта реакция вызвала образование продуктов коррозии, которые показаны в виде характерной текстуры на посткоррозионных микрофотографиях SEM, и ясно, что поверхность мягкой стали была повреждена, когда ее погрузили в смешанный кислотный электролит.
3.4. Графики Найквиста для низкоуглеродистой стали с покрытием LAM-P / FR, с покрытием LAM-V / FR и без покрытия
Все три графика EIS обсуждаются в этом разделе для целей сравнения и более подробного анализа. Таким образом, все три графика EIS для металла без покрытия / без покрытия, для покрытия LAM-P / FR и для покрытия LAM-V / FR были нанесены на один и тот же график.На рисунке 9 показан график Найквиста для всех трех случаев, и, как обсуждалось ранее, это наблюдение также предполагает, что LAM-V / FR обеспечивает наивысшую прочность покрытия до начала разрушения по сравнению с двумя другими графиками, в то время как LAM-P / FR показывает улучшенные свойства по сравнению с образцами без покрытия и более высокий импеданс, но меньший, чем покрытие LAM-V / FR.
График Найквиста показывает прямую линию, идущую под углом 90 градусов от действительной оси с непрерывным увеличением. Это показывает, что импеданс постоянно увеличивается и покрытие не разрушается; в случае деградации образуется небольшой полукруг.
3.5. График Боде для мягкой стали с покрытием LAM-P / FR, с покрытием LAM-V / FR и мягкой стали без покрытия
На рис. 10 показаны графики Боде для образца без покрытия, покрытия LAM-P / FR и покрытия LAM-V / FR. Разница четко видна в том, что, как и ожидалось, неизолированный металл демонстрирует наименьшее сопротивление и фазовый сдвиг, что, в свою очередь, показывает, что он более подвержен коррозии, и в этом случае удар будет серьезным из-за отсутствия защиты.
Среди двух покрытий покрытия LAM-V / FR демонстрируют относительно большую прочность в кислой среде по сравнению с покрытием LAM-P / FR, и это видно из высокого значения импеданса этого покрытия и разницы в фазах. смещение тоже хорошо видно.
График здесь показывает, что в кислой среде покрытия LAM-V / FR демонстрируют большую устойчивость к коррозионным ионам и выдерживают большее количество зарядов до того, как они разложатся. LAM-P / FR, однако, проявляет стойкость к коррозии и в некоторой степени обеспечивает защиту, о чем свидетельствует разница на графике с образцом из чистого металла; однако это покрытие ухудшилось раньше, чем покрытие LAM-V / FR.
3,6. Сравнение сканирования по тафелю
На рис. 11 показаны результаты по тафелю для мягкой стали с покрытием LAM-V / FR и мягкой стали с небным покрытием LAM-P / FR.Разница хорошо видна на графике сравнения; как и ожидалось, металл без покрытия показывает более высокую скорость коррозии 28,93 млн / год, и в этом случае показано, что удар будет серьезным из-за отсутствия защитных покрытий [23]. В таблице 5 бета-значения образцов с покрытием LAM-V / FR, с покрытием LAM-P / FR и без покрытия составляют 156,9e −3 В / декаду, 147,4e −3 В / декаду и 166,5e. −3 В / декада соответственно. Также существуют значения E corr и I corr , которые равны -378.3 мВ и 24,98 нА для покрытия LAM-V / FR, −770,7 мВ и 207,8 нА для покрытия LAM-P / FR; с другой стороны, значения для образца без покрытия составляли -545,9 мВ и 63,30 мк А. Среди двух нанесенных покрытий покрытие LAM-V / FR относительно обеспечивало большую прочность в кислой среде по сравнению с покрытием LAM-P / FR, что очевидно. от значений скорости коррозии. Металл с покрытием LAM-P / FR имеет скорость коррозии 2,471e −3 миль в год, а металл с покрытием LAM-V / FR имеет скорость 297,1e −6 миль в год показывает большую устойчивость к смешанной кислоте.
| |||||||||||||||||||||||||||||||||||||
Сравнение скорости коррозии MS с LAM-P / FR-покрытием, LAM-V / FR-покрытием без покрытия в кислой среде 26% HNO 3 + 56% H 2 SO 4 + 18% H 2 O. |
3,7. Сравнение скорости коррозии (смешанная кислота)
Скорость коррозии показана на рисунке 12, которая наблюдалась при сканировании Тафеля с использованием подгоночной модели E log I. В этой модели металл с покрытием LAM-V / FR имеет самую низкую скорость коррозии 297,1e −6 миль в год, металл с покрытием LAM-P / FR имеет скорость коррозии 2,471e −3 миль в год, а чистый металл имеет скорость коррозии. скорость коррозии 28,93 млн / год. Эти результаты подтверждают все предыдущие результаты.
3.8. Сравнение моделирования цепей
На рисунке 13 показана эквивалентная модель цепи для металла с покрытием (LAM-V / FR, LAM-P / FR), которая объясняет различные части электрохимической ячейки и их поведение в реакции.В таблице 6 показано сравнение сопротивления между двумя покрытиями с использованием модели подгоночных значений EIS REAP2CPE в кислотном растворе. Значения C c , R cor , R po , C cor и R soln для покрытия LAM-P / FR равны 27,43e — 9 F, 2.073e −6 F, 4.887e −3 Ом, 4.369e 3 Ом и 1.157e 3 Ом соответственно. С другой стороны, значения покрытия LAM-V / FR C c , R cor , R po , C cor и R soln 757. 4e −15 F, 1.498e −9 F, 155,6 Ом, 1,923e 3 Ом и 48,21 Ом соответственно.
|
Более высокое значение сопротивления пор для покрытия LAM-V / FR по сравнению с другими объясняет тот факт, почему это покрытие имеет лучшую стабильность. Это связано с более высокими значениями сопротивления пор, это объясняется меньшим процентом пор, которые образовывались при взаимодействии с электролитом в растворе [24].
3.9. Сравнение значений модели EIS Fit (смешанная кислота)
Результаты по сопротивлению пор и емкости покрытия представлены на рисунке 14; данные были взяты из модели подгонки схемы REAP2CPE [25]. Высокое сопротивление пористости означает высокую стабильность покрытия и означает, что поры не образуются при контакте со смешанным кислотным электролитом. С другой стороны, емкость покрытия обратно пропорциональна общему сопротивлению покрытия в соответствии с уравнением, приведенным ниже [19].
где сопротивление, частота и емкость. Низкая фракционная площадь металлического образца подвергается воздействию кислого электролита из-за низкого импеданса. Следовательно, в этом случае реакция коррозии подавляется, а в случае полимерного композиционного покрытия произошло обратное. Поры играют жизненно важную роль в увеличении или уменьшении реакции коррозии. Сопротивление пор покрытия играет важную роль в повышении стабильности покрытий LAM-V / FR.
Для случая C c можно заметить, что покрытие LAM-P / FR показывает большую емкость покрытия по сравнению с покрытием LAM-V / FR, что объясняет причины показа покрытия LAM-P / FR. меньшее сопротивление согласно уравнению (1).По мере увеличения значения емкости значение импеданса будет уменьшаться. Таким образом, образец покрытия LAM-P / FR имеет большую емкость, что означает, что он не может хранить больше зарядов. Таким образом, увеличение скорости заряда приводило к более быстрому разрушению этого покрытия по сравнению с покрытием LAM-V / FR, которое показывает меньшее значение емкости покрытия [26].
3.10. Испытание на внешний вид покрытия LAM-V / FR, погруженного в смешанную кислоту
На рис. 15 показан ход экспериментов за 5 месяцев в зависимости от времени.Покрытия LAM-V / FR были погружены в смесь кислоты с 56% H 2 SO 4 , 26% HNO 3 и 18% H 2 O композиции по весу на 1 месяц, 3 месяца и 5 месяцев. . Разрушения покрытия не наблюдалось и наблюдалась потеря веса 0,33%; через 5 мес.
3.11. Морфологический анализ поверхности покрытий LAM-P / FR и VE / FR
Морфология поверхности покрытий LAM-P / FR и LAM-V / FR, показанная на рисунке 16, была изучена с помощью сканирующей электронной микроскопии до и после погружения в раствор смешанной кислоты. .Результаты показали, что поверхность покрытия LAM-P / FR была слегка повреждена, в то время как поверхность покрытия LAM-V / FR, гладкая без царапин, наблюдалась при погружении в смешанную кислоту; Значит, он эффективнее первого. Испытание внешнего вида также проводилось по краям обоих покрытий; это также подтверждает превосходство покрытия LAM-V / FR.
4. Выводы
Были разработаны антикоррозионные композитные покрытия на основе полиэфира, которые были применены на резервуарах для хранения смешанных кислот из мягкой стали, содержащих различные составы серной и азотной кислоты, для создания антикоррозионных растворов.Это современные технологические полимерные покрытия, которые способны ингибировать окислительно-восстановительные реакции с целью предотвращения коррозии резервуаров для хранения смешанной кислоты за счет нанесения соответствующих полиэфирных покрытий на их поверхность и структуры, которые широко используются в химической промышленности, где хранятся эти кислоты. хранится. Поверхность низкоуглеродистой стали покрыта защитными полимерными покрытиями. Изготовленные на заказ резервуары из мягкой стали были покрыты антикоррозийным покрытием из ламината, армированного виниловыми волокнами, и ламината, армированного небными волокнами р-4.Исследованы различные составы покрытий на основе сложных эфиров. Для исследования морфологии поверхности этих покрытий использовали инструменты спектроскопии электрохимического импеданса (EIS) и потенциостата Gamry Tafel, а также сканирующую электронную микроскопию (SEM). Нанесенные композитные покрытия на полимерной основе обеспечивали превосходную коррозионную стойкость как ламинатных покрытий, армированных небными волокнами (LAM-P / FR), так и ламинатных покрытий, армированных виниловыми волокнами (LAM-V / FR), и снижали скорость коррозии.Исследование предполагает, что значительный контроль коррозии может быть достигнут за счет использования этих антикоррозионных покрытий.
Доступность данных
Наборы данных, созданные в ходе и / или проанализированные в ходе текущего исследования, доступны у соответствующего автора по разумному запросу.
Конфликт интересов
Авторы заявляют об отсутствии конфликта интересов относительно публикации этой статьи.
Благодарности
Авторы выражают признательность Дирекции исследований НИТУ за поддержку в проведении данного исследования. Поддержка и закупка оборудования через Комиссию по высшему образованию (HEC) Пакистана, грант программы NRPU № 3526 и грант № 6020.
Inline Filling представляет линию по производству антикоррозионных разливочных машин
КомпанияInline Filling Systems со штаб-квартирой в США представила новую линию противокоррозионных разливочных машин, устойчивую к химическим веществам, таким как сильные кислоты, отбеливатель, рассол и сахар.
В наполнителе используется стекловолокно для защиты от коррозии, а его компоненты имеют порошковое покрытие для той же цели.
Компоненты тракта прохождения жидкости изготовлены из кинара и тефлона, которые обладают агрессивными свойствами сопротивления. Все электронные компоненты проходят антикоррозионную обработку, а корпуса постоянно продуваются чистым системным воздухом.
Эта машина удовлетворяет потребность в разливочных машинах, которые требуют меньшего обслуживания, чем разливочные машины из нержавеющей стали, заявляет компания.
Inline Filling Systems Сэм Любус сказал, что новая конструкция продлевает срок службы типичной разливочной машины на семь-девять лет.
Машины могут быть интегрированы с модифицированными разборщиками бутылок, укупорочными машинами, конвейерами и накопителями, что дает клиентам полную систему розлива.
Связанные компании
NWB
Решения для упаковки напитков Bag-in-Box
28 августа 2020
Uflex
Крупнейшая в Индии многонациональная компания по производству гибких упаковочных материалов и решений
28 августа 2020
Флексографская промывка
Технология очистки для флексографской, глубокой и офсетной печати упаковки
28 августа 2020
Активные решения для защиты от коррозии и загрязнений
TM198 — Как это работает?
TM198 плавится из твердой смолы (в блоке подачи) и наносится с помощью нагретого шланга и пистолета. Он обеспечивает органическое гибкое барьерное покрытие из термопласта, которое защищает все типы металлических компонентов от гальванической точечной коррозии и атмосферной коррозии, а также защищает от проникновения воды и пыли.
Ключевой особенностью инкапсулирующей системы TM198 является отсутствие прилипания к подложке наряду с самосмазывающимися свойствами, что позволяет любым компонентам, которые должны перемещаться, делать это.
Материал можно легко разрезать и удалить для доступа и обслуживания, затем область удаленного материала может быть повторно заполнена, поскольку вновь нанесенный материал будет сцепляться с существующим TM198.В качестве альтернативы защищенный субстрат можно проверить через УЗИ непосредственно через материал.
Нет простоев во время применения, и защита обеспечивается немедленно, что позволяет снизить как капитальные, так и операционные затраты. Доказано, что TM198 продлевает срок службы компонентов и снижает затраты на техническое обслуживание. Посмотреть, как работает TM198, можно здесь 📹.
Отлично подходит для широкого спектра применений, требующих защиты от коррозии, в том числе; фланцы, клапаны, подшипники, трубопроводы, опоры труб, стыки стали и бетона, болты, изоляция электрических проводов и долгосрочное хранение оборудования в нормальных атмосферных условиях.
Наши аппликационные машины прошли обширную разработку и тестирование и представлены в двух размерах: 12 фунтов / 5,5 кг и 50 фунтов / 22 кг, чтобы удовлетворить широкий диапазон критериев применения. Также доступна машина большего размера, сертифицированная IECEx.
Тестирование:
МатериалOxifree прошел тщательные испытания в течение 11 688 часов «отраслевого стандарта» испытания солевым туманом, что соответствует испытаниям на коррозию ASTM B117, что эквивалентно более чем 50 годам «в полевых условиях».Oxifree также прошел испытания ASTM G56 UV / Weathering и снова с легкостью превысил требуемую долговечность. :
- ASTM B117 — Испытание в солевом тумане — успешно протестировано на 4-кратном промышленном эталоне
- ASTM G154 UV — атмосферные испытания успешно превзошли стандарты
- GOL492 / 09 Испытание на летучие органические соединения (<0,05%)
- Boeing BSS 7239 — Успешный тест дымовой токсичности
- ASTM E662 — Успешный тест дымообразования
- ASTM G85-94 — Испытание на стойкость по Приложению A5 — успешно одобрено 1000 часов испытаний
- BS EN 13823 — Испытание на единичное горение предмета — Завершено и прошло в рамках стандартов
- ASTM D790 — Гибкость при криогенном изгибе
- ASTM D149 — Испытания на электрическую прочность
- BS2782 Pt.