Основные методы изготовления деталей из карбона
Качество деталей из карбона в первую очередь зависит от правильного выбора и качества смолы и углеродного полотна. При ошибках в выборе плотности полотна карбона и смолы для карбона вы не сможете аккуратно выложить заготовку в форме, плотно прижать и полностью удалить пузырьки воздуха.
Основные методы изготовления деталей из карбонаК основным методам изготовления можно отнести:
- формование из препрегов, то есть полуфабрикатов,
- метод аппликации,
- формование непосредственно в форме с вакуумом,
- формование давлением (ручная прикатка).
Изготовление карбона дома не требует сложного оборудования, и при определенных навыках можно получить детали достойного качества. Поэтому сделать углепластик удовлетворительного качества самому вполне реально.
Карбон для автотюнингаВнимание! Так называемый 3D-карбон, автовинил или пленка “под карбон” никакого отношения к карбону не имеет, кроме отличной имитации поверхности карбона.
Это разноцветные виниловые и ПВХ-пленки с визуальными эффектами только для декоративной отделки поверхности, но не для упрочнения.
А вот для изготовления некоторых облегченных элементов, где требуется высокая прочность, например, для бамперов, капотов, мелких деталей кузова, может использоваться дорогостоящий настоящий карбон. Можно попробовать даже сделать обтяжку карбоном своими руками некрупных элементов.Но необходимо помнить, что этот материал очень чувствителен к точечным ударам и есть риск повреждения мелкими камнями и щебнем из-под колес.
И здесь определяющую роль играет мастерство автомастера, насколько совершенно он владеет навыками подбора полотна, смолы и толщины слоев. А ремонт карбоновых деталей – тоже дорогостоящий процесс.
Если же для вас главную роль играют эстетические параметры, а не облегчение веса автомобиля или мотоцикла, то присмотритесь к ПВХ-пленкам “под карбон”, аква-печати или аэрографии.
Изготовление деталей из карбона методом препреговПромышленный процесс формования изделия из препрега (заготовок для формования) в автоклаве представляет собой одновременное протекание сложных процессов:
- полимеризацию компаунда,
- вакуумное удаление воздуха и излишков смолы,
- высокое давление ( до 20 атм) прижимает все слои к матрице, уплотняя и выравнивая их.
Это дорогостоящий процесс, поэтому для мелкосерийного тюнинга в домашних условиях малопригодный.
Но разделение этих процессов удешевляет и удлиняет всю процедуру самостоятельного получения карбона. Изменения при этом вносятся в технологию подготовки препрега, поэтому всегда нужно обращать внимание, для какой технологии предназначена заготовка.
В этом случае препрег готовится в виде сэндвича. После нанесения смолы заготовка с обеих сторон покрывается полиэтиленовой пленкой и пропускается между двух валов. При этом лишняя смола и нежелательный воздух удаляются.
Препрег вдавливается в матрицу пуансоном, и вся конструкция помещается в термошкаф. То есть в данном случае препрег представляет полностью готовую к формованию заготовку, с обжатыми слоями и удаленным воздухом.
Этот метод чаще всего и используют автомастерские, покупая заготовки карбона, а матрицы изготавливаются из алебастра или гипса, иногда вытачиваются из металла или в качестве модели используется сама деталь. которую вы хотите повторить из карбона. Иногда модели вырезаются из пенопласта и остаются внутри готовой детали.
Углепластик своими руками проще всего сделать методом «обтяжки» или аппликации углеполотна на заготовку.
Метод аппликации (ручная оклейка)Сделать карбон своими руками можно методом оклейки, который включает пять основных этапов:
- Тщательная подготовка оклеиваемой поверхности: зашкуривание, обезжиривание, скругление углов.
- Нанесение адгезива.
- Приклеивание углеткани с пропитыванием эпоксидной смолой с отвердителем.
- Сушка.
- Покрытие защитным лаком или краской.
Наполнители для смолы используют как для придания декоративности, так и для предотвращения стекания смолы с вертикальных поверхностей.
Необходимые материалы
- Адгезив для фиксации углеткани на поверхности.
- Ткань из углеволокна, которую укладывают на смолу послойно, с прикатыванием твердым валиком.
- Эпоксидная смола средней вязкости с отвердителем (иногда она используется в качестве адгезива).
- Защитный лак. Лучше всего для защиты от царапин подходит полиуретановый. Нужно выбирать водостойкий и светостойкий. Он не помутнеет. Для высокого блеска в качестве финишного покрытия можно использовать акриловый лак.
Смолу наносят 2-3 раза с промежуточной сушкой и шлифовкой.
Этот метод отличается от традиционного изготовления карбоновых изделий по моделям нанесением адгезива, а не разделителя для легкого съема получившегося полуфабриката.
Компания 3М предлагает даже самоклеющееся углеполотно, но работа с ним требует хороших навыков.
И карбон остается на оклеиваемой детали, упрочняя ее. Такое производство карбона чаще всего используется для оклеивания бампера, приборной панели и пр.
Метод формования карбона в форме с вакуумомДля этого метода требуется специальное оборудование и хорошие навыки.
- Нанесение разделительного состава на поверхность модели. Для матовых и полуглянцевых поверхностей обычно применяется разделительный воск, а для глянцевых поверхностей(пластик и металл) — разделитель типа WOLO и растворы для грунтования, которые используются при мелкосерийном призводстве.
- Выкладывание углеткани в матрицу, без морщин и пузырей.
- Пропитка углеткани смолой.
- Слоев может быть несколько. В некоторых случаях углеткань можно чередовать со стеклотканью.
- Наложение перфорированной пленки для отжима излишков смолы и выхода воздуха. Желательно укладывать внахлест.
- Прокладка впитывающего слоя.
- Установка вакуумной трубки и порта для подключения вакуумного насоса.
- Помещение всей конструкции в прочную вакуумную пленку, приклеивание герметизирующим жгутом к оснастке.
Вся процедура напоминает помещение какого-либо предмета в вакуумный пакет, которые продаются в магазинах для хранения вещей, с последующей откачкой из него воздуха. Можно поэкспериментировать с такими вакуумными пакетами. Они очень прочные и продаются разных размеров. А вакуумный насос для домашнего использования обойдется в среднем в 150-200$.
Еще один вариант вакуумной технологии – процесс формования включает в себя наложение слоев углеродного волокна на пресс-форму, упаковывание в мешки всей сборки и удаление лишнего воздуха с помощью вакуумной системы. Смоляная смесь затем подается с одного конца и затем всасывается в пакетированный узел под действием вакуума внутри. После периода охлаждения формованная деталь отделяется от пресс-формы, а избыток материала обрезается.
Применяется для самостоятельного изготовления деталей из карбона и аналогичен методу формования вакуумом, но без использования дорогостоящей оснастки. Наборы включают кисти для нанесения смолы и валики для выдавливания воздуха и прикатки слоев.
Для простого тюнинга автомобиля понадобятся:
- углеполотно плотностью 200-300 г/м,
- эпоксидная смола,
- отвердитель,
- жесткий валик и кисть.
На Alibaba.com углеполотно плотностью 200 г/м.кв. плетения twill предлагается по цене от 10 до 25 долларов за квадратный метр. Правда, и покупать нужно от 10 метров. Но можно договориться о получении образцов, которые позволят самостоятельно изготовить небольшие изделия из карбона.
В общих чертах процесс изготовления углепластика своими руками выглядит так:
- На поверхность формы наносится разделительный воск, гелькоат для формирования защитно-декоративного слоя на поверхности готового изделия.
- После его высыхания наносится тонкий слой смолы, на который прикатывается или прижимается углеткань, для выхода пузырьков воздуха.
- Затем наносится еще один слой смолы для пропитки. Можно нанести несколько слоев ткани и смолы, в зависимости от требуемых параметров изделия.
- Смола может полимеризироваться на воздухе. Это происходит обычно в течение 5 дней. Можно поместить заготовку в термошкаф, нагретый до температуры 140 – 180 ◦С, что значительно ускорит процесс полимеризации.
Затем изделие извлекаем из формы, шлифуем, полируем, покрываем лаком, гелькоутом или красим.
Каждый слой прокатывается валиком для удаления пузырьков воздуха и получения максимального сцепления.
При таком методе получается высокий расход смолы (в три раза выше плотности углеполотна), но зато именно таким способом можно изготовить любую деталь из карбона своими руками.
Автор Ирина Химич
Как сделать карбон своими руками
Автомобиль сегодня становится чем-то большим, чем просто средством передвижения. Владельцы машин любят их, пытаются выделить из толпы, добавив что-то особенное внешнему виду. Такой вид модернизации называется стайлинг и включает огромное количество различных способов добавления красоты. Это и бампера, и обвесы, и фары замысловатых форм, и тонировка, и различные способы покраски деталей. Очень распространёнными среди автолюбителей являются детали из карбона (или углепластика), которые пользуются огромной популярностью, причём, скорее, из-за необычного внешнего вида, а не из-за своих аэродинамических свойств. В этой статье мы расскажем, как сделать углепластик своими руками.
Характеристики карбона
Углепластик обладает рядом выдающихся качеств, таких как очень высокая прочность при малом весе. Зачастую детали из карбона прочнее даже, чем стальные аналоги, а весят при этом гораздо меньше.
Эти же характеристики стали причиной того, что детали из карбона стали широко применяться при подготовке гоночных автомобилей, а благодаря их своеобразному внешнему виду, этот материал стал пользоваться немалой популярностью среди обычных автолюбителей. Поэтому изготовление деталей из карбона является очень распространённой задачей многих водителей, которые мечтают добавить изюминку во внешность своей машины.
Способы изготовления карбона
Для того чтобы изготовить деталь автомобиля из углепластика, совсем необязательно идти в специализированный автосервис, ведь запросто можно сделать карбон своими руками. Есть несколько способов изготовления карбона. Ниже мы разберём только те способы, которые подойдут для применения в домашних условиях.
Изготовление деталей с помощью ручного давления
Этот способ отлично подойдёт для самостоятельного изготовления деталей из углепластика. Отличается он тем, что для его реализации не потребуется дорогостоящее оборудование, а значит, вы сможете изготовить себе карбоновые детали без ощутимых затрат.
Для проведения работ вам потребуется ряд инструментов: карбоновый лист, отвердитель, эпоксидная смола, валик для выдавливания пузырей и кисть для нанесения смолы.
Также вам потребуется форма, по которой вы будете изготавливать деталь.
После того как заготовка полностью высохнет, можно достать деталь, почистить её и покрыть лаком для обеспечения защиты покрытия.
Изготовление формы с использованием вакуума
Первые шаги в изготовлении этим способом похожи на предыдущий. Изменения присутствуют в самой форме и в порядке действий, после того как все слои углепластика выложены на форму. После этого необходимо поместить всю конструкцию в вакуумную плёнку и подключить к ней вакуумный насос. Насос откачает весь воздух и создаст давление для лучшего приставания детали к форме.
Этот способ очень хорош и позволит получать качественные детали. Однако обойдётся он довольно дорого, особенно по сравнению со способом ручного формирования: вакуумный насос стоит порядка 200 долларов.
Способ обклейки
Заключается этот способ в том, чтобы готовые детали автомобиля обклеить карбоновым материалом, а не изготавливать новые. Это не облегчит конструкцию автомобиля, зато позволит повысить прочность деталей. Например, можно обклеить капот автомобиля, бампера или приборную панель.
Порядок действий для этого способа следующий:
- Сначала необходимо подготовить ту поверхность, которую вы собираетесь обклеивать. Для этого необходимо её тщательно очистить, избавиться от резких углов и обезжирить. Далее, следует нанести клей на поверхность, а материал пропитать эпоксидной смолой и отвердителем.
Карбоновые листы нужно приклеить к поверхности, избегая образования пузырей, после чего высушить её и покрыть лаком.
- Не путайте обклейку углепластиком и обклейку карбоновой плёнкой. В этом случае карбоновая плёнка представляет собой обычный автовинил с рисунком, похожим на покрытие из углепластика. Он применяется исключительно в декоративных целях и не несёт цели сделать детали прочнее или легче. Тем не менее, если вам важна только внешность, этот способ может вам подойти — осуществить его легче и дешевле всего. Однако делать этого мы не советуем, так как такие плёнки окажут не самое лучшее влияние на покрытие кузова вашего автомобиля.
Таким образом, вы теперь знаете, как сделать карбон самостоятельно. Для этого потребуется лишь наличие материала, умение обращаться с инструментами и некоторое терпение. Если эта статья оказалась для вас полезной, напишите нам.
Страница не найдена
Вы можете перейти на главную страницу сайта или воспользоваться простым или визуальным поиском.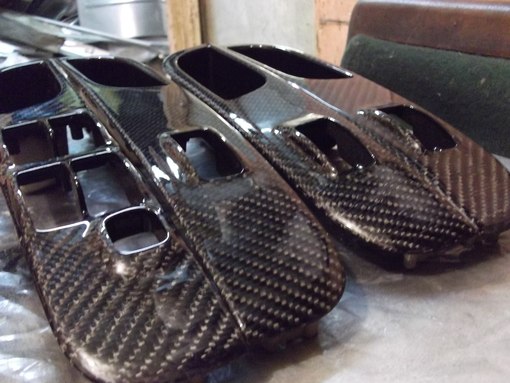
Возможно Вас заинтересует
Пред След Страница:
Перетяжка маски приборов ВАЗ 2110
Просмотров:14239
Считается, что обтянуть козырек панели приборов автомобиля задача не из легких, сложная форма детали не позволяет перетянуть…
Перетяжка ручки КПП кожей
Все хотят ощущать приятные чувства от того, к чему прикасаешься очень часто. Обтянув ручку КПП…
Рамка для навигатора своими руками
Просмотров:12041
Рынок электронных авто аксессуаров быстро расширяется, поэтому вопрос, как самостоятельно установить монитор в панель автомобиля все…
Шумоизоляция локеров
Просмотров:42170
Шумоизоляция автомобиля — это комплекс мероприятий по изоляции шумов, как извне (шумоизоляция двигателя, изоляция шума дороги. ..
Установка номеров в задний катафот автомобиля
Все знают, что задние номера ВАЗ 2110 и ВАЗ 2112 закреплены на бампере, а между фонарями длинный катафот. В этом фотоотчете покажем, каким образом можно перенести номерные знаки с бампера в…
Лучшие диски для автомобиля
Эффективный способ сделать автомобиль индивидуальным — заменить стальные диски на литые. Но определится с выбором не так просто, как кажется на первый взгляд. Различают несколько классов автодисков, каждый из которых…
Популярные ключевые слова (ТОП 50)
Интересный сайт? Поделись с друзьями
Оборудование для производства карбона, изготовление карбоновых деталей
Для производства карбона, кевлара и других композитов на основе углепластика, применяется несколько распространенных технологий.
Основные компоненты:
1. оснастка
2. ламинат (армирующий материал)
3. жертвенный слой (Pill Play)
4. перфорированная плёнка
5. впитывающий слой (Braizer)
6. вакуумная пленка
Также понадобятся: герметизирующий жгут, вакуумная трубка, вакуумный насос.
Суть: В оснастку обработанную разделительным составом наносится гелькоут, после доведения до состояния «на отлип» укладывается армирующий материал (карбон) и пропитывается связующим (эпоксидной смолой) кистью или валиком. После, укладывается жертвенный слой, перфорированный слой, впитывающий (распределяющий вакуум) слой.
Далее делается вакуумный мешок: накрываем вакуумной пленкой оснастку, пленка крепится к оснастке с помощью герметизирующего жгута. Герметизируем форму. Откачиваем воздух вакуумным насосом.
Особенности: при использовании духового шкафа можно получать более качественные компоненты за более короткое время.
Плюс технологии: Используя эту технологию можно делать качественные и достаточно недорогие компоненты малых и средних размеров.
Минус технологии: в том, что процесс пропитки армирующего материала (карбона) является открытым (идут испарения летучих веществ из связующего), а следовательно не безопасным для персонала. Обязательно использование защитной маски и перчаток при работе.
II. Технология Вакуумной инфузии (Vacuum infusion) – технология пропитки армирующего материала с помощью разрежения.Основные компоненты:
1. оснастка
2. ламинат (армирующий материал)
3. жертвенный слой (Pill Play)
4. проводящая сетка
5. вакуумная пленка
Также понадобятся: герметизирующий жгут, вакуумная трубка, спиральная трубка, вакуумный насос, ловушка для смолы (обязательное условие), т-образные переходники, спрей-клей Aerofix2 временной фиксации, зажим прерывания подачи.
Суть: Эта технология позволяет производить качественные и относительно недорогие компоненты средних и больших размеров с отличным качеством внешнего вида.
В оснастку обработанную разделительным составом наносится гелькоут, после доведения до состояния «на отлип» укладывается сухой армирующий материал (карбон, кевлар, базальт) . После, укладывается жертвенный слой, укладывается проводящая сетка и форма закрывается вакуумной пленкой. Пленка крепится к оснастке с помощью герметизирующего жгута. Устанавливаем трубку подачи связующего (эпоксидной смолы низкой вязкости). Герметизируем форму. Откачиваем воздух вакуумным насосом. После проверки на герметичность (отсутствие утечек) производим пуск смолы.
Смола под разряжением входит в форму и занимает доступный объем пропитывая армирующий материал уложенный в оснастку. После окончания пропитки армирующего материала (визуальный контроль) перекрываем трубку подачи смолы.
Особенности: для пропитки используется связующее низкой вязкости.
Плюс технологии: главное положительное качество технологии вакуумной инфузии в том, что при выкладке армирующего материала (карбона, арамида) в форму он остается сухим, а следовательно, это не ограничивает время работы. Кроме того процесс является «чистым». Т.е. не происходит активного испарения летучих компонентов связующего, следовательно более безопасным для рабочего по сравнению с вакуум бэгингом.
Из минусов: можно отметить повышенные требования к квалификации рабочего, его внимательности и аккуратности. Также то, что компоненты могут получаться с большим содержанием связующего по сравнению с вакуум бэгингом.
Основные компоненты:
1. оснастка (стойкая к температуре)
2. препрег (армирующий материал пропитанный «горячим» связующим на специальном оборудовании)
3. жертвенный слой (Pill Play)
4. перфорированная плёнка
5. впитывающий слой (Braizer)
6. вакуумная пленка
7. * автоклав
* – специальное профессиональное оборудование (мощный герметичный сосуд) для создания, удержания и контроля повышенного давления воздуха (6-8 атмосфер) и температуры (80-160°C).
Также понадобятся: высокотемпературный герметизирующий жгут, высокотемпературная вакуумная трубка, вакуумный насос.
Суть: процесс работы с препрегом похож на Технологию вакуумбэгинга. В оснастку обработанную «горячим» разделительным составом (высокотемпературные разделительные составы) укладывается армирующий материал (карбоновый препрег). Хорошенько прожимается пальцами, тефлоновой палочкой. После, укладывается жертвенный слой, перфорированный слой, впитывающий (распределяющий вакуум) слой.
Далее делается вакуумный мешок: накрываем высокотемпературной вакуумной пленкой оснастку, пленка крепится к оснастке с помощью высокотемпературного герметизирующего жгута. Герметизируем форму. Откачиваем воздух вакуумным насосом.
Использование автоклава при переработке препрегов не является обязательным (достаточно вакуумного мешка и печи), но при использовании, позволяет получать изделия высочайшего качества (характеристика прочность-вес).
Используется при производстве высокопрочных композиционных деталей: монококи, детали подвески и кузова Формулы1, суперкаров, детали самолетов, аэрокосмические компоненты, протезы, профессиональное спортивное оборудование.
Стоит отметить, что данная технология является наиболее дорогой при производстве композитов на основе карбона. Это связанно не только со стоимостью самого автоклава но и расходами на электроэнергию.
Плюс технологии: низкая сложность укладки ламината, чистый процесс, высокое качество композита.
Минус технологии: гораздо более дорогой процесс (по сравнению с вакуум бэгингом, вакуумной инфузией). Также необходимо отметить повышенные требования к оснастке (высокая температура полимеризации).
Необходима холодильная камера для хранения препрега. Но даже при правильном хранении (-18С) срок годности материала не превышает 12 месяцев.
Из вышесказанного можно сделать вывод, что именно сложность в технологии изготовления и высокий уровень квалификации рабочих обуславливает достаточно высокую цену компонентов из карбона. Наша компания за 7 лет работы накопила опыт и знания позволяющие решать любые задачи при производстве изделий из композитов. Имеется необходимое оборудование для производства любых изделий из карбона, в том числе, различных сложных, оригинальных конструкций для авиационной и космической отрасли, профессионального спорта, медицины, тюнинга автомобилей и мотоциклов.
Карбон как делают
Основные методы изготовления деталей из карбона
Качество деталей из карбона в первую очередь зависит от правильного выбора и качества смолы и углеродного полотна. При ошибках в выборе плотности полотна карбона и смолы для карбона вы не сможете аккуратно выложить заготовку в форме, плотно прижать и полностью удалить пузырьки воздуха.
Основные методы изготовления деталей из карбонаК основным методам изготовления можно отнести:
- формование из препрегов, то есть полуфабрикатов,
- метод аппликации,
- формование непосредственно в форме с вакуумом,
- формование давлением (ручная прикатка).
Изготовление карбона дома не требует сложного оборудования, и при определенных навыках можно получить детали достойного качества. Поэтому сделать углепластик удовлетворительного качества самому вполне реально.
Карбон для автотюнингаВнимание! Так называемый 3D-карбон, автовинил или пленка “под карбон” никакого отношения к карбону не имеет, кроме отличной имитации поверхности карбона.
Это разноцветные виниловые и ПВХ-пленки с визуальными эффектами только для декоративной отделки поверхности, но не для упрочнения.
А вот для изготовления некоторых облегченных элементов, где требуется высокая прочность, например, для бамперов, капотов, мелких деталей кузова, может использоваться дорогостоящий настоящий карбон. Можно попробовать даже сделать обтяжку карбоном своими руками некрупных элементов.Но необходимо помнить, что этот материал очень чувствителен к точечным ударам и есть риск повреждения мелкими камнями и щебнем из-под колес.
И здесь определяющую роль играет мастерство автомастера, насколько совершенно он владеет навыками подбора полотна, смолы и толщины слоев. А ремонт карбоновых деталей – тоже дорогостоящий процесс.
Если же для вас главную роль играют эстетические параметры, а не облегчение веса автомобиля или мотоцикла, то присмотритесь к ПВХ-пленкам “под карбон”, аква-печати или аэрографии.
Изготовление деталей из карбона методом препреговПромышленный процесс формования изделия из препрега (заготовок для формования) в автоклаве представляет собой одновременное протекание сложных процессов:
- полимеризацию компаунда,
- вакуумное удаление воздуха и излишков смолы,
- высокое давление ( до 20 атм) прижимает все слои к матрице, уплотняя и выравнивая их.
Это дорогостоящий процесс, поэтому для мелкосерийного тюнинга в домашних условиях малопригодный.
Но разделение этих процессов удешевляет и удлиняет всю процедуру самостоятельного получения карбона. Изменения при этом вносятся в технологию подготовки препрега, поэтому всегда нужно обращать внимание, для какой технологии предназначена заготовка.
В этом случае препрег готовится в виде сэндвича. После нанесения смолы заготовка с обеих сторон покрывается полиэтиленовой пленкой и пропускается между двух валов. При этом лишняя смола и нежелательный воздух удаляются.
Препрег вдавливается в матрицу пуансоном, и вся конструкция помещается в термошкаф. То есть в данном случае препрег представляет полностью готовую к формованию заготовку, с обжатыми слоями и удаленным воздухом.
Этот метод чаще всего и используют автомастерские, покупая заготовки карбона, а матрицы изготавливаются из алебастра или гипса, иногда вытачиваются из металла или в качестве модели используется сама деталь. которую вы хотите повторить из карбона. Иногда модели вырезаются из пенопласта и остаются внутри готовой детали.
Углепластик своими руками проще всего сделать методом «обтяжки» или аппликации углеполотна на заготовку.
Метод аппликации (ручная оклейка)Сделать карбон своими руками можно методом оклейки, который включает пять основных этапов:
- Тщательная подготовка оклеиваемой поверхности: зашкуривание, обезжиривание, скругление углов.
- Нанесение адгезива.
- Приклеивание углеткани с пропитыванием эпоксидной смолой с отвердителем.
- Сушка.
- Покрытие защитным лаком или краской.
Наполнители для смолы используют как для придания декоративности, так и для предотвращения стекания смолы с вертикальных поверхностей.
Необходимые материалы
- Адгезив для фиксации углеткани на поверхности.
- Ткань из углеволокна, которую укладывают на смолу послойно, с прикатыванием твердым валиком.
- Эпоксидная смола средней вязкости с отвердителем (иногда она используется в качестве адгезива).
- Защитный лак. Лучше всего для защиты от царапин подходит полиуретановый. Нужно выбирать водостойкий и светостойкий. Он не помутнеет. Для высокого блеска в качестве финишного покрытия можно использовать акриловый лак.
Смолу наносят 2-3 раза с промежуточной сушкой и шлифовкой.
Этот метод отличается от традиционного изготовления карбоновых изделий по моделям нанесением адгезива, а не разделителя для легкого съема получившегося полуфабриката.
Компания 3М предлагает даже самоклеющееся углеполотно, но работа с ним требует хороших навыков.
И карбон остается на оклеиваемой детали, упрочняя ее. Такое производство карбона чаще всего используется для оклеивания бампера, приборной панели и пр.
Метод формования карбона в форме с вакуумомДля этого метода требуется специальное оборудование и хорошие навыки.
- Нанесение разделительного состава на поверхность модели. Для матовых и полуглянцевых поверхностей обычно применяется разделительный воск, а для глянцевых поверхностей(пластик и металл) — разделитель типа WOLO и растворы для грунтования, которые используются при мелкосерийном призводстве.
- Выкладывание углеткани в матрицу, без морщин и пузырей.
- Пропитка углеткани смолой.
- Слоев может быть несколько. В некоторых случаях углеткань можно чередовать со стеклотканью.
- Наложение перфорированной пленки для отжима излишков смолы и выхода воздуха. Желательно укладывать внахлест.
- Прокладка впитывающего слоя.
- Установка вакуумной трубки и порта для подключения вакуумного насоса.
- Помещение всей конструкции в прочную вакуумную пленку, приклеивание герметизирующим жгутом к оснастке.
Вся процедура напоминает помещение какого-либо предмета в вакуумный пакет, которые продаются в магазинах для хранения вещей, с последующей откачкой из него воздуха. Можно поэкспериментировать с такими вакуумными пакетами. Они очень прочные и продаются разных размеров. А вакуумный насос для домашнего использования обойдется в среднем в 150-200$.
Еще один вариант вакуумной технологии – процесс формования включает в себя наложение слоев углеродного волокна на пресс-форму, упаковывание в мешки всей сборки и удаление лишнего воздуха с помощью вакуумной системы. Смоляная смесь затем подается с одного конца и затем всасывается в пакетированный узел под действием вакуума внутри. После периода охлаждения формованная деталь отделяется от пресс-формы, а избыток материала обрезается.
Применяется для самостоятельного изготовления деталей из карбона и аналогичен методу формования вакуумом, но без использования дорогостоящей оснастки. Наборы включают кисти для нанесения смолы и валики для выдавливания воздуха и прикатки слоев.
Для простого тюнинга автомобиля понадобятся:
- углеполотно плотностью 200-300 г/м,
- эпоксидная смола,
- отвердитель,
- жесткий валик и кисть.
На Alibaba.com углеполотно плотностью 200 г/м.кв. плетения twill предлагается по цене от 10 до 25 долларов за квадратный метр. Правда, и покупать нужно от 10 метров. Но можно договориться о получении образцов, которые позволят самостоятельно изготовить небольшие изделия из карбона.
В общих чертах процесс изготовления углепластика своими руками выглядит так:
- На поверхность формы наносится разделительный воск, гелькоат для формирования защитно-декоративного слоя на поверхности готового изделия.
- После его высыхания наносится тонкий слой смолы, на который прикатывается или прижимается углеткань, для выхода пузырьков воздуха.
- Затем наносится еще один слой смолы для пропитки. Можно нанести несколько слоев ткани и смолы, в зависимости от требуемых параметров изделия.
- Смола может полимеризироваться на воздухе. Это происходит обычно в течение 5 дней. Можно поместить заготовку в термошкаф, нагретый до температуры 140 – 180 ◦С, что значительно ускорит процесс полимеризации.
Затем изделие извлекаем из формы, шлифуем, полируем, покрываем лаком, гелькоутом или красим.
Каждый слой прокатывается валиком для удаления пузырьков воздуха и получения максимального сцепления.
При таком методе получается высокий расход смолы (в три раза выше плотности углеполотна), но зато именно таким способом можно изготовить любую деталь из карбона своими руками.
Автор Ирина Химич
engitime.ru
Как сделать карбон своими руками
Автомобиль сегодня становится чем-то большим, чем просто средством передвижения. Владельцы машин любят их, пытаются выделить из толпы, добавив что-то особенное внешнему виду. Такой вид модернизации называется стайлинг и включает огромное количество различных способов добавления красоты. Это и бампера, и обвесы, и фары замысловатых форм, и тонировка, и различные способы покраски деталей. Очень распространёнными среди автолюбителей являются детали из карбона (или углепластика), которые пользуются огромной популярностью, причём, скорее, из-за необычного внешнего вида, а не из-за своих аэродинамических свойств. В этой статье мы расскажем, как сделать углепластик своими руками.
Характеристики карбона
Углепластик обладает рядом выдающихся качеств, таких как очень высокая прочность при малом весе. Зачастую детали из карбона прочнее даже, чем стальные аналоги, а весят при этом гораздо меньше. Благодаря таким характеристикам, детали из этого материала находят широкое применение во многих сферах промышленности. В основном это ракетостроение, самолётостроение и судостроение, так как в этих областях такие параметры материалов нужны больше всего. При этом производство углепластика связано с рядом технических сложностей, таких как необходимость постоянного контроля условий изготовления с применением очень дорогостоящих и энергозатратных методов. Если же отказаться от подобного контроля, то существует огромный риск того, что характеристики материала получатся гораздо хуже ожидаемых. Причиной этому может послужить малейшее отклонение от рекомендуемых параметров производства. Также настоящий материал плохо выдерживает удары, в результате чего даже незначительная деформация может повредить деталь из углепластика.
Эти же характеристики стали причиной того, что детали из карбона стали широко применяться при подготовке гоночных автомобилей, а благодаря их своеобразному внешнему виду, этот материал стал пользоваться немалой популярностью среди обычных автолюбителей. Поэтому изготовление деталей из карбона является очень распространённой задачей многих водителей, которые мечтают добавить изюминку во внешность своей машины.
Способы изготовления карбона
Для того чтобы изготовить деталь автомобиля из углепластика, совсем необязательно идти в специализированный автосервис, ведь запросто можно сделать карбон своими руками. Есть несколько способов изготовления карбона. Ниже мы разберём только те способы, которые подойдут для применения в домашних условиях.
Изготовление деталей с помощью ручного давления
Этот способ отлично подойдёт для самостоятельного изготовления деталей из углепластика. Отличается он тем, что для его реализации не потребуется дорогостоящее оборудование, а значит, вы сможете изготовить себе карбоновые детали без ощутимых затрат.
Для проведения работ вам потребуется ряд инструментов: карбоновый лист, отвердитель, эпоксидная смола, валик для выдавливания пузырей и кисть для нанесения смолы.
Также вам потребуется форма, по которой вы будете изготавливать деталь. В первую очередь необходимо нанести на форму разделительный воск и дождаться его высыхания. После этого следует нанести эпоксидную смолу, на которой начать формировать слой углепластика. Следите за тем, чтобы под слоями карбона не оставалось пузырей, а его сцепление с формой было максимальным. Для этого следует воспользоваться валиком.
После того как заготовка полностью высохнет, можно достать деталь, почистить её и покрыть лаком для обеспечения защиты покрытия.
Изготовление формы с использованием вакуума
Первые шаги в изготовлении этим способом похожи на предыдущий. Изменения присутствуют в самой форме и в порядке действий, после того как все слои углепластика выложены на форму. После этого необходимо поместить всю конструкцию в вакуумную плёнку и подключить к ней вакуумный насос. Насос откачает весь воздух и создаст давление для лучшего приставания детали к форме.
Этот способ очень хорош и позволит получать качественные детали. Однако обойдётся он довольно дорого, особенно по сравнению со способом ручного формирования: вакуумный насос стоит порядка 200 долларов.
Способ обклейки
Заключается этот способ в том, чтобы готовые детали автомобиля обклеить карбоновым материалом, а не изготавливать новые. Это не облегчит конструкцию автомобиля, зато позволит повысить прочность деталей. Например, можно обклеить капот автомобиля, бампера или приборную панель.
Порядок действий для этого способа следующий:
- Сначала необходимо подготовить ту поверхность, которую вы собираетесь обклеивать. Для этого необходимо её тщательно очистить, избавиться от резких углов и обезжирить. Далее, следует нанести клей на поверхность, а материал пропитать эпоксидной смолой и отвердителем.
Карбоновые листы нужно приклеить к поверхности, избегая образования пузырей, после чего высушить её и покрыть лаком.
- Не путайте обклейку углепластиком и обклейку карбоновой плёнкой. В этом случае карбоновая плёнка представляет собой обычный автовинил с рисунком, похожим на покрытие из углепластика. Он применяется исключительно в декоративных целях и не несёт цели сделать детали прочнее или легче. Тем не менее, если вам важна только внешность, этот способ может вам подойти — осуществить его легче и дешевле всего. Однако делать этого мы не советуем, так как такие плёнки окажут не самое лучшее влияние на покрытие кузова вашего автомобиля.
Таким образом, вы теперь знаете, как сделать карбон самостоятельно. Для этого потребуется лишь наличие материала, умение обращаться с инструментами и некоторое терпение. Если эта статья оказалась для вас полезной, напишите нам.
carextra.ru
Как делают карбоновые детали — Как это сделано, как это работает, как это устроено — LiveJournal
Оригинал можно посмотреть здесь.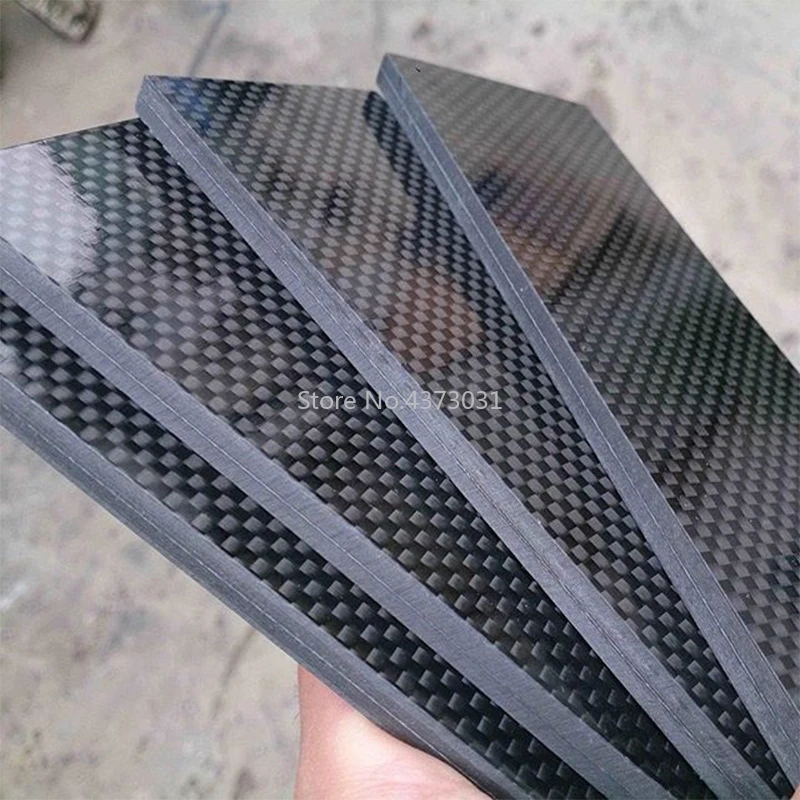
Был у одного нашего заказчика такой проект: сделать линейку техники с корпусами из углеродного волокна. Лёгкие, прочные, красивые — сплошные плюсы. Только цена кусается. Вот и командировали меня на разведку: узнать как бы сделать то же самое, но подешевле.
Честно говоря, я ни разу до этого не видел, как производятся подобные вещи, и даже не представлял себе всю технологию. Поэтому сразу и с удовольствием взялся за задачу.
Но оказалось, что попасть на завод не так просто. Два производителя под разными предлогами отказались встречаться на производстве и настойчиво звали к себе в офис. У третьего офис и производство были в одном здании, и я недолго думая поехал к нему.
Завод выглядит вполне прилично, меня проводят в переговорную-шоурум.
От разнообразия образцов разбегаются глаза: карбоновый велосипед, детали для авто и мототюнинга, всякие штуковины непонятного назначения.
Целиковый капот для BMW — мечта пацанов с раёна.
Иногда в карбоновую ткань вплетают цветные нити: красные или синие, выглядит очень необычно.
Детали, покрашенные целиком, сразу и не отличишь от обычных. Обычно спортсмены так делают: им нужен низкий вес, а не понты 🙂
Мотошлем.
И нечто, неизвестно для чего нужное.
Но главной целью моего визита, было вот это:
Чехол для iPad. Меня интересовал не сам чехол, конечно, а похожие на него штуки: детали для корпусов телефонов, ноутбуков, планшетов. Было важно разобраться в технологии произодства, понимать, как правильно их проектировать, чтобы это было максимально дешево и технологично. Поэтому после долгих переговоров и уговоров я всё-таки напросился на экскурсию по цеху.
Производство занимает один этаж здания, тут чисто, но довольно пустынно.
Карбоновое полотно с нанесенным клеящим слоем поступает в рулонах. Оно бывает разной толщины, с разным рисунком плетения. Хранится в специальных холодильниках.
Ткань нарезается на куски по выкройке, и наклеиваются в несколько слоёв на матрицу. Матрицы бывают лёгкими, из чего-то типа пластика и с увеличенным ресурсом, из алюминия.
Матрицы, идущие в работу раскладываются прямо на полу, каждая в своём секторе.
Сам процесс наклейки карбона был расположен за стеклянными дверьми, но мне наотрез отказались его показывать, мол страшная коммерческая тайна. Но я не думаю, что там есть что-то секретное, просто вырезают ножницами, и укладывают лоскутки в форму.
После этого каждую деталь упаковывают в вакуумные пакеты.
Откачивают из пакетов воздух и загружают в одну из двух печей, побольше или поменьше.
Готовые детали извлекают из матриц. Если деталь сложной формы, то и матрица для неё будет сложносоставной, из нескольких частей.
Контроль качества перед сдачей на склад.
Как вы догадываетесь, это не весь процесс. Теперь у деталей нужно обрезать края и покрасить их лаком. Но это делается на другой площадке, у субподрядчика. Предлагали поехать посмотреть, но я отказался — вот там уж точно ничего нового.
Ой, вом же наверное интересно узнать про цены? Так вот, карбоновый чехольчик на iPad стоит с завода 25 долларов. А велосипед — несколько тысяч. Улыбаться перестанешь, как говорит один мой знакомый. И вариантов снижения особо не видать, слишком мелкосерийное производство, слишком много ручного труда.
kak-eto-sdelano.livejournal.com
Honda Civic «г у т а л и н» › Бортжурнал › По просьбам трудящихся! Карбон своими руками без особых проблем. Много буков 8)
В связи с тем, что много драйверов пишет в личку по поводу карбона, решил осилить написание данного поста.
крышка ля мпски
крышка для сивика
И так все началось с того, что мне очень захотелось чего-нибудь закарбонить в своей тачке, и я начал долго и упорно набивая шишки воплощать эту затею в жизнь.
Сначала, как и множество самозакарбонвателей я купил погонный метр карбоновой ткани и сняв лючок бензобака со своего «сивика» решил отделать его карбоном и тут началось.
Первой проблемой стало выкладывание ткани, которая при натягивании изменяла рисунок, то есть квадратики становились не ровными, а что бы их выровнять приходилось двигать их пальцами, решение данной проблемы: предварительно обклеить ткань малярным скотчем и не отрывать до окончания работ.
Следующей преградой на пути к мечте стала смола, так как покупать американскую смолу я счел не целесообразным, пришлось подбирать достойный вариант от Российского производителя. И вариант был найден, им оказалась очень жидкая двух компонентная оптическая смола. Ее преимущество состоит в том, что воздух из нее выходит практически полностью уже при простом нагревании по средствам установки стаканчика на батарею в квартире при этом смола долго остается жидкой, что позволяет ей хорошо пропитать материал.
И вот настал момент, когда лючок был, обтянут тканью, и я начал поливать эту конструкцию смолой. Вылив на все это примерно 30 граммов смолы, я с досадой обнаружил, что большая ее часть стекла на заблаговременно подложенный снизу журнал «Топ гир». Так, что советую смолы брать столько, чтобы пролить ткань и не более того, а иначе выльете всю смолу в пустую.
И так поняв, что смола у меня стекла и благополучно закончилась, я оставил все сохнуть до утра и пошел спать. Утром я обнаружил, что смола уже не течет, но еще и не застыла, расстроенный положил крышку на место и отправился на работу. Придя вечером, я обнаружил, что смола высохла и превратилась в очень жесткий полностью прозрачный материал, в который была заключена карбоновая ткань единственное, чем я был раздосадован это бугристость получившегося покрытия. Взяв в руки шкурку начал шкурить поверхность шкурил, шкурил и дошкурил прям до ткани блин.( Вся фигня в том, если пошкурить ткань на ней остаются светлые пятна. Короче все пришлось переделывать. В итоге; учитывая ошибки прошлого, все было переделано и в принципе получилось хорошо, но нам, то надо идеально. И тут я вспомнил про передачу всем известного научного телеканала, в котором рассказывалось про создание корабельных мачт из карбона. И тут я вспомнил о карбоновом препреге с помощью которого можно создать еще более идеальную поверхность.
сравниваем линии волокна на капоте от сейбон и нашей крышке
Жмакаем кнопку ниже. Об этом в сл. части заходите.
www.drive2.ru
Toyota Supra Последняя из Могикан › Бортжурнал › Карбон Handmade или как сделать карбоновые детали в гаражных условиях
Идея делать и ремонтировать карбоновые детали возникла после траблов с капотом. В итоге как обычно увлёкся…решил сделать подкапотку и салон в америкосовском стиле…пример на стойке…
Сезон закончился, началось очередное зимнее вбухивание денег. Я не сторонник корчевания, извращенства и прочего. Поэтому сторонник эстетической красоты авто и ввиду необходимости решил дозакупиться остальными датчиками, столкнувшись с проблемой их размещения. Подиум под три датчика у меня уже был…
Накладка
надо разместить куда-нибудь ещё два необходимых для буду. Побороздив простор инета ничего нормально не нашёл, разные фирмы предлагаю всякие колхозные накладки или вообще кто-то впихивает на такие комплектные крепления
датчик
Так что решил сделать всё в гараже. Место выбрано на стойке, под 2 датчика, колхозный перетянутый или крашенный вариант меня не устраивал, поэтому решил сделать из карбона. Выбрал как будет удобно, подобрал место их расположения так чтобы, циверблат был развёрнут точно на меня и не выходили за рамки самой стойки, чтобы не загораживать обзорность.
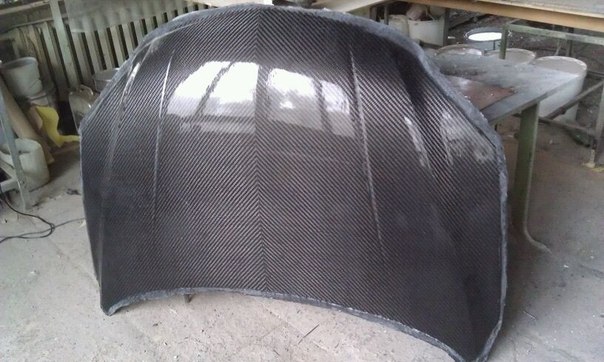
экскиз
Матрица
Формочка
Результат
Стойка
Стойка
Стойка
Также ещё некоторые детали из подкапотки. Извиняюсь за телефонное качество.
Стойка
Цена вопроса: 100 500 ₽ Пробег: 0 км
www.drive2.ru
Как делают детали из карбона?
Был у одного нашего заказчика такой проект: сделать линейку техники с корпусами из углеродного волокна. Лёгкие, прочные, красивые — сплошные плюсы. Только цена кусается. Вот и командировали меня на разведку: узнать как бы сделать то же самое, но подешевле.
Честно говоря, я ни разу до этого не видел, как производятся подобные вещи, и даже не представлял себе всю технологию. Поэтому сразу и с удовольствием взялся за задачу.
Но оказалось, что попасть на завод не так просто. Два производителя под разными предлогами отказались встречаться на производстве и настойчиво звали к себе в офис. У третьего офис и производство были в одном здании, и я недолго думая поехал к нему.
Завод выглядит вполне прилично, меня проводят в переговорную-шоурум.
От разнообразия образцов разбегаются глаза: карбоновый велосипед, детали для авто и мототюнинга, всякие штуковины непонятного назначения.
Целиковый капот для BMW — мечта пацанов с раёна.
Иногда в карбоновую ткань вплетают цветные нити: красные или синие, выглядит очень необычно.
Детали, покрашенные целиком, сразу и не отличишь от обычных. Обычно спортсмены так делают: им нужен низкий вес, а не понты 🙂
Мотошлем.
И нечто, неизвестно для чего нужное.
Но главной целью моего визита, было вот это:
Чехол для iPad. Меня интересовал не сам чехол, конечно, а похожие на него штуки: детали для корпусов телефонов, ноутбуков, планшетов. Было важно разобраться в технологии произодства, понимать, как правильно их проектировать, чтобы это было максимально дешево и технологично. Поэтому после долгих переговоров и уговоров я всё-таки напросился на экскурсию по цеху.
Производство занимает один этаж здания, тут чисто, но довольно пустынно.
Карбоновое полотно с нанесенным клеящим слоем поступает в рулонах. Оно бывает разной толщины, с разным рисунком плетения. Хранится в специальных холодильниках.
Ткань нарезается на куски по выкройке, и наклеиваются в несколько слоёв на матрицу. Матрицы бывают лёгкими, из чего-то типа пластика и с увеличенным ресурсом, из алюминия.
Матрицы, идущие в работу раскладываются прямо на полу, каждая в своём секторе.
Сам процесс наклейки карбона был расположен за стеклянными дверьми, но мне наотрез отказались его показывать, мол страшная коммерческая тайна. Но я не думаю, что там есть что-то секретное, просто вырезают ножницами, и укладывают лоскутки в форму.
После этого каждую деталь упаковывают в вакуумные пакеты.
Откачивают из пакетов воздух и загружают в одну из двух печей, побольше или поменьше.
Готовые детали извлекают из матриц. Если деталь сложной формы, то и матрица для неё будет сложносоставной, из нескольких частей.
Контроль качества перед сдачей на склад.
Как вы догадываетесь, это не весь процесс. Теперь у деталей нужно обрезать края и покрасить их лаком. Но это делается на другой площадке, у субподрядчика. Предлагали поехать посмотреть, но я отказался — вот там уж точно ничего нового.
Ой, вом же наверное интересно узнать про цены? Так вот, карбоновый чехольчик на iPad стоит с завода 25 долларов. А велосипед — несколько тысяч. Улыбаться перестанешь, как говорит один мой знакомый. И вариантов снижения особо не видать, слишком мелкосерийное производство, слишком много ручного труда.
Но вы всё же улыбнитесь. Вот вам напоследок картинка обычной китайской жизни, которую я снял перед воротами этого завода.
Источник
kak-eto-sdelano.ru
Карбон, как способ облегчить авто и кошелёк — Nissan 200SX, 2.0 л., 1989 года на DRIVE2
Да… Давненько я тут небыл. Не знаю как вам, а мне пришлось перечитать бортовик, чтобы вспомнить чего тут вообще к чему =) стыдно говорить, но машина с ноября или декабря стояла без движения. Приезжал к ней редко и не очень продуктивно. Причин несколько: свет в гараже был отключен 4 месяца, а с фонариком особо нихрена и не сделаешь; времени небыло, а то что было я тратил на вторую любимую (девушку) или тупо на сон; на работе произошли изменения и на мне повисло слишком много и на слишком большой срок, потому стало мне не до моей любимой красавицы. Итог, пропущенный сезон, но я смирился и решил что наспех абы как делать не буду, лучше долго чем хреного. Итого машина строиться ммм… Почти 2 года уже)) жееееесть! Есть правда одна оговорочка, другой проект таки был закончен и дарит удовольствие и радость. EAT SLEEP RACE почитайте, зацените!
Отсюда сделаны выводы, которые обошлись очень дорого) ВНИМАНИЕ!
— если хочешь давать угла, покупай готовый проект, это значительно выгоднее. Да пусть машина будет немного не такая как в твоих ванильных мечтах, но она реально будет дарить радость и адреналин + опыт дрифта который ты будешь получать в это время, а не опыт вращения гаек и работой болгарки. За 400-500 тыщ проектов море. Реально проще поработать побольше и перетерпеть, купить корыто и сразу начать давать угла! Дешево, продуктивно и адреналинисто. Те кто будет говорить что за 400-500 можно посторить охренеть какой космолет для дрифта – ребята, вы заблуждаетесь. Я сам также все расписывал на листочке и у меня все срасталось. Их я уже сжег, а подсчеты стоимости вообще перестал вести.
— если хочешь много дури под капотом ставь изначально более мощный мотор. 1-GZ, 2-GZ на левый руль самое то! На правый руль RB25det. (почему 25det ? потому что запчасти на него стоят в 3-4! Раза дешевле чем на 26). В мотор лучше ваще не лазить. Масло поменял, буст подключил, обеспечение есть? Тогда в путь! Сделать из SR мотор похожий по характеристикам на RB26 в 2 раза дороже чем сам RB26.
— Тюнинг на мотор (помимо обеспечения в виде маслокулеров, радиаторов и т.п. – дроч), рецепт настоящего дрифтера, ХОРОШИЙ стоковый мотор + очко буста! (моно и переплатить, если он действительно хороший, поверьте это будет выгоднее чем взять полумертвый и с ним возиться – это потеря времени и денег). Посмострите на машины япошек, облегченные, стоковые ведра на бустапе, блоке и стойках. Всё – так и надо.
— Любишь строить, тогда покупай кузов и начинай все с нуля. Разбирай, все выкидывай, вари, переваривай, усиливай, грунтуй, крась. И собирай на всем новом, соберешь на старом — получишь тоже корыто, тока с нормальной внешностью, таких немало.
Вобщем вот такая инфа для размышления )) Надеюсь поможет кому-нить)
Возвращаемся к зелененькой.
Как говорят ралисты (люди кстати ваще веселые), «Лучше 1000кг, чем 1000 лошадей». Вот и я так думаю. Решил облегчить ведерко, долго думал что к чему и с чего начать. Решил с дверей. Вырезать их ( внутренности все, оставив только внешний лист с ручкой), как-то руки не поднялись, много раз выдел на корчах такой метод, при открывании они гуляют как лист бумаги, не закрываются нихрена, стекла облегченные не держаться, вощем жесть. С такими дверьми ниокаких стеклоподъемниках можно и не мечтать.
Решил что карбон мой вариант.
Стал заморачиваться на эту тему и понял что настоящего карбона то толком никто и не производит! Все то что можно заказать из Америки или Японии в большинстве случаев видовой карбон для понтов, и веса толком не скидывает, и не прочный ниразу (я б сказал хрупкий), чуть какой камушек или удар, сразу идет паутина по нему. Все что продается это: только ВЕРХНИЙ слой карбона, а снизу стекловолокно, пластик и ли все что угодно но уже не карбон. Карбон имеет разную плотность, прочность, вид. Так вот есть просто для вида, он тонкий и никакой конструкционной нагрузки не несет. А есть настоящий конструкционный, который применяется при изготовлении настоящих гоночных болидов. Плотный и прочный, он действительно может соперничать при правильном использовании и при соблюдении технологического процесса со сталью. По удельным характеристикам превосходит высокопрочную сталь, например 25ХГСА. Основная составляющая часть углепластика — это нити углерода. Такие нити очень тонкие (примерно 0.005-0.010 мм в диаметре), сломать их очень просто, а вот порвать достаточно трудно. Из этих нитей сплетаются ткани. Они могут иметь разный рисунок плетения. Для придания прочности, изделие делают из нескольких слоев углеткани(5-8), каждый раз меняя угол направления плетения. Таким образом на разрыв изделие получает высоченную прочность в направлении 360 градусов.
Слои скрепляются с помощью эпоксидных смол. Эти смолы вовсе не те, которые используют при работе со стеклотканью и требуют совсем других навыков и оборудования. Чтобы придать прочность изделию их карбоновых тканей нужно высокое давление и температура одновременно. Все слои должны продавиться относительно друг-друга и относительно самого себя. Т.е.сама ткань должна натянуться и спрессоваться, каждый слой. Очень легко отличить настоящий карбон прожатый под давлением от простого видового изготовленного не по технологии. Ткань имеет плетение, так вот каждое плетение в разрез имеет вот такую форму « ) ». А у прожатого оно уже не дугообразное и плоское « ] ». И ткань кажется плоской. Т.е. она прожалась под давлением и между собой все слои и сама спрессовалась. Это очень важно для веса и для прочности, т.к. выдавливается лишние смолы и материал становиться более плотным.
Гляньте, отчетливо видно что просто положили ткань и залили ее смолой. О какой прочности тут можно говорить?
А теперь о главном: есть два вида карбона мокрый и сухой карбон.
Все производители, которые занимаются выпуском карбоновых деталей типа SEBON на большой рынок, пользуются исключительно технологией мокрого карбона . Во первых, они используют карбон красивый, но не конструкционный, во вторых что более важно они используют полиэфирные смолы, которые значительно уступают по своим прочностным характеристикам эпоксидным. Плюс они значительно дешевле, нежели эпоксидные. Карбон по мокрой технологии даже не прожимают и соотношение смола/ армирующий материал (карбон) идет в пользу смолы со значительным перевесом.Примерно 70 смолы и 30 карбона. Плюс они экономят на слоях и не укладывают углеткань в нескольких направлениях, обычно ограничиваясь 1-2 слоями, которые видны глазу. Такие изделия реально тяжелее по сравнению с их сухими аналогами в 3-4 раза! Еще к минусам можно отнести то что они на солнце желтеют а при деформации мутнеют в местах изгиба, часто трескаясь (трескаются смолы и лаки, т.к. они декоративные а не прочностные.) Смолы в идеале должны быть только между волокнами самого полотна и между полотнами. Особого умения, как и дорогостоящего оборудования не нужно для изготовления такого карбона. Да и от карбона у таких изделий лишь одно название. Жаль, но это так. Я на самом деле и не удивлен, т.к. людей реально занимающихся спортом единицы и обычных понторезов миллионы. Потому в нашем коммерческом мире понятно на кого направлены взгляды производителей.
Сухой карбон, божественный материал, который применяется как основной конструкционный в таких суперкарах как Ламборгини, Макларен, Феррари, на автомобилях F1. Как вы думаете имеет ли он что-то общее с ширпотребом на рынке? На автосалоне в Париже компания Lamborghini представла экспериментальный автомобиль, получивший название Sesto Elemento (шестой элемент). Эта машина имеет полностью карбоновый кузов, карбоновые колесные диски и карбоновый интерьер, и поэтому весит всего 999 килограммов. С мотором V10 мощностью 570 сил новинка способна разогнаться до сотни за 2,5 секунды. Из карбона у концепта выполнены монокок кузова, детали подвески и карданный вал, а выпускная система изготовлена из смеси карбона и ст
www. drive2.ru
BMW 3 series 335i Навести&уничтожить › Бортжурнал › Карбоновые детали интерьера и экстерьера своими руками.
Итак, душа требует чего-то нового, утонченного, а машина требует новые аксессуары, хочется попробовать что-то новое, слишком много свободного времени, слова 3д-корбон вызывают рвотный рефлекс. Если есть все перечисленное и очень много терпения, тогда эта тема для Тебя 8)
Прежде всего попрошу не упоминать слово пленка в этой теме. Вообще слова пленка и карбон находятся на разных уровнях мироздания. Итак, поехали. Для начала приобретаем ткань, эпоксидку и затвердитель, клей, валерьянку. Их можно заказать в моем интернет-магазине Streetpower.com.ua или даже не знаю, мало где еще по такой цене выйдет, судя по статистике.
Итак, имеем:
1. Около 4 ярдов ткани(3.6м), рулон шириной 1.52м. Этого хватит на интерьер и накладку багажника.
2. 1 галлон эпоксидки (около 4л) . 80 мл затвердителя MEKP(Methyl ethyl ketone peroxide).
3. Клей 3М супер 77 в аэрозоле или любой другой. Одного баллона вполне хватит.
Итак, первый этап — подготавливаем поверхности, зачищаем, рекомендую снять слой дерева до металла, если это элементы интерьера, которые туго входят даже в родном состоянии, не говоря уже о том, что слой карбона, эпоксидки, лака будет достаточно значительным.
Моя крышка багажника была ярко-оранжевой, я прокрасил поверхность черным с аэрозоля и покрыл лаком для того, чтобы клей не смыл краску при накладывании ткани.
Далее кропотливый и очень тонкий процесс приклеивания ткани. Углеволоконная ткань достаточно хрупкая, легко расплетается, не тянется и в отличии от виниловых продуктов — не захочет просто отлипнуть и «попробовать еще разок с феном» 😉
Моя любимая помощница:
Самая сложная по форме деталька. Подиум для компьютерного экрана:
После того как ткань приклеена, замешиваем эпоксидку, запах которой без респиратора постепенно превращается из неприятного в сладкий и манящий аромат 8)
Покрываем кисточкой детали, не слишком толстый первый слой, покрывающий запчасть. Обращаем внимания на то, чтоб не осталось «сухих» мест. Подогреваем феном пузырьки, они выходят наружу. Оставляем сохнуть.
Приходим на следующий день, следующую неделю снимаем шкуркой пузырьки, сильные неровности и явные проблемы 8) Не забываем есть, пить и девушек)
Здесь лучшая подруга — лучшая подруга или любимая. и 100ая наждачка =)
Процесс начинает нам уже надоедать, а мы переходим к основным слоям эпоксидки. Делаем слой эпоксидки, ждем с пол часа, делаем следующий слой, в общей сумме около 4х слоев на каждой детали. оставляем сохнуть и предвкушаем обалденный результат:
Думаем, что все закончилось, но оказывается — самый трудный бой впереди. Начинаем счищать волны, 100ая наждачка, дремель на невидных местах, режем руки, режем дремелем, обрезаем на невидимых плоскостях лишнее, вычищаем с обратной стороны лишнее, если не маскировали(скорее всего будет до одного места, но лучше клипсы и болтики и подобные места все же постараться отмаскировать — лучше обычный, а не малярный скотч. После 100ой, 200ая, 400ая, 800ая наждачки
и вот, потеряв немало нервов, пальцев и спустя литры алкоголя — получаем результат, который теперь необходимо или наполировать полиролью или вскрыть лаком, как сделал я. Получаем результат, который с гордостью можно назвать эксклюзивным.
Фото результата чутка позже.
www.drive2.ru
Углеродное волокно. Карбон. — DRIVE2
Сегодня мы поможем разобраться в одном из самых интересных материалов 21 века. Начнем с военных технологий, закончим тюнингом.
Углеродное волокно — материал, состоящий из тонких нитей диаметром от 3 до 15 микрон, образованных преимущественно атомами углерода. Атомы углерода объединены в микроскопические кристаллы, выровненные параллельно друг другу. Выравнивание кристаллов придает волокну большую прочность на растяжение. Углеродные волокна характеризуются высокой силой натяжения, низким удельным весом, низким коэффициентом температурного расширения и химической инертностью.
Углеродное волокно является основой для производства углепластиков (или карбона, карбонопластиков, от «carbon», «carbone» — углерод). Углепластики — полимерные композиционные материалы из переплетенных нитей углеродного волокна, расположенных в матрице из полимерных (чаще эпоксидных) смол.
Углеродные композиционные материалы отличаются высокой прочностью, жесткостью и малой массой, часто прочнее стали, но гораздо легче.
Что такое карбон?
Слово «карбон» — своего рода профессиональный жаргонизм, точнее сокращение от английского Carbon Fiber (углеродное волокно), под эгидой которого, в общем понимании, объединилось огромное количество самых разных материалов. Примерно, как тысячи различных веществ с отличающимися физическими, химическими и техническими свойствами носят название «пластмасса». В случае с карбоном, общим для материалов стал углеволоконный наполнитель, но не связующее вещество, которое может быть разным. Даже полиэтиленовая пленка с впаянными в нее угольными нитями с полным правом может носить это гордое имя. Просто сложившейся классификации углепластиков еще нет.
Большинство современных материалов, применяемых в технике и, особенно, в автомобильной области, доходят до рядового потребителя по схожему сценарию. Новшества появляются в научных лабораториях обычно для нужд «оборонки». Затем, исполнив почетную обязанность по защите Отечества, они прокладывают себе дорогу через спорт и, как следствие, тюнинг к конвейеру. Так произошло и в случае с углеродными материалами.
Какое применение для карбона?
В последние годы проникновение карбона в конструкцию затюнингованных энтузиастами «аппаратов» приняло лавинообразный характер. Кроме того, углепластик все чаще и чаще упоминается в описаниях серийных машин. Этот материал, имеющий военно-космическую и спортивную предысторию, становится все популярнее. Прочность и легкость материалов ценятся конструкторами автомобилей уже давно, примерно с 50-х годов прошлого века. Сегодняшний прогресс технологий производства увеличивает соблазн применять больше композитов в новых разработках. Для владельца машины подобные детали ценны не только декоративностью рисунка углеродной ткани и завораживающей «переливчатостью» отраженного волокнами света, но и сохраняющейся аурой эксклюзивности. Со стороны производителя предложение карбоновых элементов в отделке — показатель технологической «продвинутости» фирмы.
Краткий курс истории.
Не нарушая сложившихся традиций, после «службы в армии» углепластик «занялся» спортом. Лыжники, велосипедисты, гребцы, хоккеисты и многие другие спортсмены по достоинству оценили легкий и прочный инвентарь. В автоспорте карбоновая эра началась в 1976 году. Сначала на машинах McLaren появились отдельные детали из диковинного черно-переливчатого материала, а в 1981 на трассу вышел McLaren MP4 с монококом, полностью изготовленным из углеволоконного композита. Так идея главного конструктора команды Lotus Колина Чепмена, создавшего в 1960-х несущую основу гоночного кузова, получила качественное развитие. Однако в то время новый материал был еще неведом технологам от автоспорта, потому неразрушаемую капсулу для McLaren изготовила американская компания Hercules Aerospace, обладающая опытом военно-космических разработок. Сейчас же в активе практически всех ведущих команд Формулы-1 есть собственное оборудование для выпуска карбоновых монококов, рычагов подвески, антикрыльев, спойлеров, сидений пилотов, рулей и даже тормозных дисков.
Что же такое КАРБОН или углеродное волокно?
Углеродное волокно состоит из множества тончайших нитей углерода. Прочность нитей на разрыв, сравнимая с прочностью легированной стали, при массе, меньшей, чем у алюминия, обуславливает высокие механические характеристики карбонов. Интересно, что наиболее распространенная технология получения столь прочного материала основана на методе «обугливания» волокон, по изначальным свойствам близким к шерсти. Исходный полимер белого цвета с мудреным названием полиакрилонитрил подвергается нескольким циклам нагрева в среде инертных газов. Сначала под воздействием высокой температуры (около 260 C) на молекулярном уровне изменяется внутренняя структура вещества. Затем при температурах повыше (около 700 C) атомы углерода «сбрасывают» водород. После нескольких «поджариваний» водород удаляется полностью. Теперь удерживавшие его силы направлены на упрочнение связей между оставшимися элементами. На шерсть материал уже не похож, однако его прочность еще далека от идеала. И процесс под названием графитизация продолжается. Повторяющиеся операции нагрева до 1300 C «очищают» почерневшее волокно уже от азота. Полностью избавиться от последнего не удается, однако его количество уменьшается. Каждый «шаг» делает содержание в веществе атомов углерода все больше, а их связь все крепче. Механизм упрочнения такой же, как и при «изгнании» водорода. Самая прочная продукция проходит несколько ступеней графитизации при температуре до 3000 C и обозначается аббревиатурой UHM.
Почему так дорого?
Большие затраты энергии — основная причина высокой себестоимости углеродного волокна. Впрочем, это с лихвой компенсируется впечатляющим результатом. Даже не верится, что все начиналось с «мягкого и пушистого» материала, содержащегося в довольно прозаических вещах и известных не только сотрудникам химических лабораторий. Белые волокна — так называемые сополимеры полиакрилонитрила — широко используются в текстильной промышленности. Они входят в состав плательных, костюмных и трикотажных тканей, ковров, брезента, обивочных и фильтрующих материалов. Иными словами, сополимеры полиакрилонитрила присутствуют везде, где на прилагающейся этикетке упомянуто акриловое волокно. Некоторые из них «несут службу» в качестве пластмасс. Наиболее распространенный среди таковых — АБС-пластик. Вот и получается, что «двоюродных родственников» у карбона полным-полно.
Угольная нить имеет впечатляющие показатели по усилию на разрыв, но ее способность «держать удар» на изгиб «подкачала». Поэтому, для равной прочности изделий, предпочтительнее использовать ткань. Организованные в определенном порядке волокна «помогают» друг другу справиться с нагрузкой. Однонаправленные ленты лишены такого преимущества. Однако, задавая различную ориентацию слоев, можно добиться искомой прочности в нужном направлении, значительно сэкономить на массе детали и излишне не усиливать непринципиальные места.
Что такое карбоновая ткань?
plain
Для изготовления карбоновых деталей применяется как просто углеродное волокно с хаотично расположенными и заполняющими весь объем материала нитями, так и ткань (Carbon Fabric). Существуют десятки видов плетений. Наиболее распространены Plain, Twill, Satin. Иногда плетение условно — лента из продольно расположенных волокон «прихвачена» редкими поперечными стежками только для того, чтобы не рассыпаться.
Плотность ткани, или удельная масса, выраженная в г/м2, помимо типа плетения зависит от толщины волокна, которая определяется количеством угленитей. Данная характеристика кратна тысячи. Так, аббревиатура 1К означает тысячу нитей в волокне. Чаще всего в автоспорте и тюнинге применяются ткани плетения Plain и Twill плотностью 150–600 г/м2, с толщиной волокон 1K, 2.5K, 3К, 6K, 12K и 24К. Ткань 12К широко используется и в изделиях военного назначения (корпуса и головки баллистических ракет, лопасти винтов вертолетов и подводных лодок, и пр.), то есть там, где детали испытывают колоссальные нагрузки.
satin
Бывает ли цветной карбон? Желтый карбон бывает?
Часто от производителей тюнинговых деталей и, как следствие, от заказчиков можно услышать про «серебристый» или «цветной» карбон. «Серебряный» или «алюминиевый» цвет — всего лишь краска или металлизированное покрытие на стеклоткани. И называть карбоном такой материал неуместно — это стеклопластик. Отрадно, что и в данной области продолжают появляться новые идеи, но по характеристикам стеклу с углем углеродным никак не сравниться. Цветные же ткани чаще всего выполнены из кевлара. Хотя некоторые производители и здесь применяют стекловолокно; встречается даже окрашенные вискоза и полиэтилен. При попытке сэкономить, заменив кевлар на упомянутые полимерные нити, ухудшается адгезия такого продукта со смолами. Ни о какой прочности изделий с такими тканями не может быть и речи.
Отметим, что «Кевлар», «Номекс» и «Тварон» — патентованные американские марки полимеров. Их научное название «арамиды». Это родственники нейлонов и капронов. В России есть собственные аналоги — СВМ, «Русар», «Терлон» СБ и «Армос». Но, как часто бывает, наиболее «раскрученное» название — «Кевлар» — стало именем нарицательным для всех материалов.
twill2/2
Что такое кевлар и какие у него свойства?
По весовым, прочностным и температурным свойствам кевлар уступает углеволокну. Способность же кевлара воспринимать изгибающие нагрузки существенно выше. Именно с этим связано появление гибридных тканей, в которых карбон и кевлар содержатся примерно поровну. Детали с угольно-арамидными волокнами воспринимают упругую деформацию лучше, чем карбоновые изделия. Однако есть у них и минусы. Карбон-кевларовый композит менее проче
www.drive2.ru
Как покрыть деталь карбоном самому
В этой статье хочу поговорить и рассказать вам, как можно самому покрыть карбоном зеркала или другие детали кузова автомобиля. Сам процесс мне показался не очень трудоёмким, главное соблюдать последовательность и не спешить..
Какие материалы нам понадобятся для этой процедуры.
- Наждачная бумага — мне нужна была наждачная бумага с липучкой, вам может быть понадобится простая, в зависимости с каким инструментом вы работаете.
Бумага нужна градации: 180, 150, 120 и 80. Также для мокрой чистки нам понадобиться наждачка. 320, 400 и 600.
- для обрезания углеткани, понадобится болгарка или дремель.
- простой автомобильный лак.
- сама угля ткань, 1 квадратный метр.
- полиэфирная или эпоксидная смола с отвердителем.
- малярный скотч и растворитель 646 или 647.
- и кисточка, шириной приблизительно 5 см.
Вот это все материалы, которые нам потребуются для нашего процесса.
Теперь начинаем сам процесс.
Берем зеркало и аккуратно со всех сторон зашкуриваем 80 наждачкой.
Далее наносим тонкий слой смолы на всю поверхность зеркала и ждем приблизительно 20 минут, чтобы она подсохла.
Далее, отрезаем кусок углеткани такого размера, чтобы как раз хватило на зеркало и аккуратно приклеиваем углеткань на зеркало, всё аккуратно разглаживает, чтобы углеткань хорошо прилегала по всей поверхности и оставляем так на 24 часа.
После того, как прошли сутки, нужно слоями наносить смолу прямо на поверхность карбона. Наносим 3 слоя с промежутком в 1 час, не забываем при этом добавить к смоле отвердитель. Опять всё оставляем сохнуть на 24 часа.
Далее, берём наши зеркала и начинаем обрезать, и удалять лишние части углеткани.
После того, как всё выровняли и удалили лишнее, начинаем зачищать смолу по всему зеркалу. Порядок наждачки такой 120,150,180, потом с водой чистим 320.
Затем как все будет гладенько, подготавливаем зеркало к покрытию лаком. Протираем зеркала обезжиривателем, разводим лак и наносим 2-3 слоя с промежутком в 10-15 минут.
На этом вроде бы стоило и остановиться, но я всё таки ещё раз, через сутки, зачистил весь лак и покрыл ещё 3 слоями, чтобы получился глубокий, насыщенный цвет.
Вот на этом данную процедуру я считаю законченной.
Автор; Макс, г.Воронеж
xn--100—j4dau4ec0ao.xn--p1ai
Карбон под капот своими руками — Mitsubishi Lancer Evolution, 2.0 л., 2005 года на DRIVE2
Давно лежат оставшиеся углеволокно, смола и остальные материалы с того времени, когда я ламинировал салон в Импрезе. Зачесались руки, появилось немного свободного времени, и я снова начал процесс тренировок по ламинации. Под раздачу попали две крышки предохранителей, что находятся под капотом.
Все, что понадобится для ламинации-это углеволокно, эпоксидная смола с затвердителем, черный праймер для стекол, лак, кисточки, тара, кухонные весы, фен, канцелярский нож, наждачная бумага, малярный скотч и ножницы.
Зачищаем деталь крупной наждачкой
Закрываем не включенную в работу часть детали малярным скотчем
Покрываем деталь праймером
Когда праймер высохнет, наносим на деталь слой смолы и ждем, пока она станет липкой
После этого прикладываем уже вырезанный по размеру (с запасом) кусок углеткани и разглаживаем. Наносим слой смолы.
Ждем, пока она подсохнет (при прикладывании пальца к смоле, она должна быть липкой, но следов на пальце не должно оставаться), и наносим последующие слои по такому же принципу, пока под ней не скроется весь рельеф ткани и будет видно, что смолы достаточно для того, чтобы при вышкуривании не дойти до ткани и не испортить деталь.

Обрезаем лишнюю ткань по бокам, выравниваем деталь, придаем ей форму и вышлифовываем наждачкой от крупной 80 до 1500. Покрываем лаком, а если где-то подтекла смола, либо часть детали повреждена наждачкой, то можно подкрасить, либо как-то скрыть, на ваше усмотрение.
На выходе получаем что-то подобное
Скажу сразу, получилось так себе. Делал все в домашних условиях, от пыли не спрятаться при нанесении лака, да и сам лак автомобильный дает сильную усадку. Да и ткань не идеально легла. Еще набираю опыт и изучаю нюансы.
В идеале-иметь вакуумный насос, помещение, шлифовальную машинку, хороший лак, и тогда из углеволокна, кевлара и другой декоративной ткани, которые представлены в огромном ассортименте, можно творить чудеса :).
www.drive2.ru
Изготовление карбона. Карбон на авто
Карбон или углепластик – сокращенное название от английского Carbon Fiber (углеродное волокно), под маркой которого, объединилось большое количество различных композитных материалов (также, как например, сотни органических материалов с определенными физическими свойствами, называют пластмассами). Карбон получают из углеродного волокна и используют, как армирующий наполнитель для производства различных высокопрочных композитных материалов. Самое удивительное, что карбон или углепластик, делают из жидкости. Точнее, из жидкого полимера – полиакрилонитрила. Для этого, из полиакрилонитрила, сначала получают полиакрилонитрильное волокно, которое получают, путем продавливания исходного полимера – полиакрилонитрила, через специальную фильеру с сотнями тончайших отверстий, диаметром около 50 микрон. Под давлением, в горячей воде, через крохотные отверстия фильеры, непрерывным потоком, «выходят» тонкие белые ниточки, которые и являются исходным сырьем для дальнейшего изготовления карбона. После прохождения через несколько ванн со специальными растворами, полученные полиакрилонитриловые волокна становятся в несколько раз тоньше, а их молекулы выстраиваются таким образом, что волокна становится еще прочнее. После этого, полиакрилонитрильное волокно проходит многоэтапный процесс обработки, который изменяет внутреннюю структуру вещества на молекулярном уровне.
Данный процесс включает в себя высокотемпературную обработку, окисление и «карбонизацию» (насыщение углеродом) в инертной среде, в результате чего получается конечный продукт – материал карбон или углеродное волокно.
Наиболее важное свойство карбона или углеволокна – это уникальное соотношение низкого веса и исключительной прочности. Модуль упругости отдельных «сортов» карбона может превышать 60 ГПа, а разрывная нагрузка может достигать 5 гПа, при этом карбон в полтора раза легче стали и на четверть легче алюминия. Для придания большей прочности, карбоновые волокна переплетают между собой особым образом, с разным углом направления плетения и затем, шьют из них специальные высокопрочные карбоновые ткани, способные выдерживать колоссальные механические нагрузки. Композитные армирующие материалы на основе карбона стали использовать для создания монококов спортивных и гоночных автомобилей, корпусов скоростных катеров, мачт океанских яхт, винтов вертолетов, корабельных тросов, для изготовления специальной экипировки и многого другого. Благодаря выдающихся технико-эксплуатационных характеристик и декоративных свойств, карбон стал широко использоваться и в автотюнинге, для отделки кузовных элементов автомобилей. И если раньше, натуральный карбон можно было увидеть только на дорогих спортивных или представительских автомобилях, то уже сейчас продаются автомобили, в которых покрытие карбоном входит в базовую комплектацию, при этом, при покупке у дилера нового автомобиля, можно выбрать нужный цвет карбона или заказать понравившийся вид карбона, например, матовый карбон или карбон под лаком. Помимо этого, сейчас уже почти в каждом тюнинговом ателье вам могут полностью обтянуть карбоном машину, обклеить салон карбоном или обклеить машину карбоновой пленкой, или даже, предложат купить карбоновую пленку, для оклейки карбоном своими руками.
Материал – кевлар: кевларовая ткань
Кевларовая ткань представляет собой паpа-аpамидное синтетическое волокно, которое производят из синтетического полимера — полипарафинилин терафталамида. Кевларовые волокна обладают исключительной прочностью (разрывная прочность может доходить 600 кг/мм2), и высоким сопротивлением к ударам и динамическим нагрузкам. Кевларовые волокна обладают высокой термической стойкостью (разлагается при температуре, более 4500 С) и сохраняют прочность, и эластичность (и даже становятся чуть прочнее) при крайне низких, криогенных температурах, до — 2000 С. Из кевларовых волокон плетут армирующие нити, из которых, также, как и из карбона, делают специальные высокопрочные кевларовые ткани, используемые затем, для производства различных армирующих материалов. В отличие от карбона, кевларовый материал может легко деформироваться и имеет наилучшее показатели по скорости поглощения энергии, и длительности взаимодействия с ударником, обеспечивая высокую противопульную и противоосколочную стойкость, благодаря чему, кевларовая ткань является основным армирующим компонентом при производстве бронежилетов и различных средств безопасности.
В качестве армирующего материала, кевларовая ткань широко используется при производстве самолетных шин, пуленепробиваемых покрышек, корабельных канатов, специальной защитной одежды и многого другого. Перчатки, сшитые из кевлара защищают руки от ожогов, порезов, в них можно смело хвататься за лезвие ножа без риска порезаться. Для получения эластичного армирующего материала на основе кевлара, несколько слоев кевларовой ткани сшивают вместе и затем спекают с резиновой основой. Тем не менее, у кевлара, как и у любого другого композитного материала, есть свои недостатки. Кевлар разрушается от ультрафиолетового излучения, а в смоле, в виде формованного материала, при длительном воздействии уф-лучей, кевларовая ткань также значительно ухудшает свои свойства. Помимо этого, кевлар сохраняет высокое сопротивление на разрыв и стойкость к порезам только в «сухом» виде. С конца прошлого века началось производство комбинированных армирующих материалов или гибридных тканей, сотканных из равного количества кевларовых и карбоновых нитей, обладающих лучшими эксплуатационными показателями, чем материалы, сделанные из натурального карбона или кевлара.
Из карбон-кевларовых нитей плетут тонкие и прочные корабельные канаты, изготавливают корды в автомобильных шинах, делают автомобильные ремни безопасности, приводные ремни и мн. др.
Виниловые «карбоновые» пленки. Иммерсионные пленки под карбон.
Среди недостатков карбоновых, кевларовых или гибридных армирующих материалов можно отнести высокую стоимость исходного сырья и длительное время изготовления конечного продукта. Но, если в исключительных физических свойствах карбона или кевлара нет необходимости, можно использовать внешнюю отделку: покрытие карбоном или перетяжка карбоном. Для отделки карбоном идеально подходят два типа покрытий: самоклеющиеся виниловые карбоновые пленки «3D carbon» и «4D carbon», и иммерсионные пленки под карбон, наносимые методом аквапечати или аквапринта.
Наличие в карбоновых пленках воздушных «каналов», значительно упрощает процесс обтяжки карбоном кузовных элементов и позволяет наклеивать карбоновые пленки на различные сложно профилированные поверхности. Карбоновые пленки стоят дешевле карбоновой ткани и не требуют какой-то специальной подготовки поверхности. После оклейки изделия карбоновой пленкой, покрытие ничем не отличается от формованного покрытия из натурального карбона. Обтяжка карбоном (виниловыми пленками «3D carbon» и «4D carbon»), это простой и экономичный способ имитации карбонового покрытия, не требующий использования для этого, дорогостоящих натуральных карбоновых тканей или материалов.
Другой вид отделки карбоном – использование wtp-пленок под карбон, наносимые методом иммерсионной (аква) печати. Wtp-пленки под карбон позволяют имитировать плетения различных карбоновых или кевларовых тканей и после проведения процесса аква-печати и нанесения на поверхность карбоновой пленки, изделие ничем не отличается от изделия, сделанного от натурального карбона или покрытого натуральной карбоновой тканью. К дополнительным преимуществам использования wtp-пленок, можно отнести большой выбор вариантов «плетений», под карбон или кевлар. При этом, благодаря большому выбору пленок «под карбон», можно выбрать не только понравившийся «рисунок» плетения карбоновых нитей, но и цвет карбонового покрытия, и текстуру карбона.
Как делают карбоновые детали — Как это сделано, как это работает, как это устроено — LiveJournal
Оригинал можно посмотреть здесь.Был у одного нашего заказчика такой проект: сделать линейку техники с корпусами из углеродного волокна. Лёгкие, прочные, красивые — сплошные плюсы. Только цена кусается. Вот и командировали меня на разведку: узнать как бы сделать то же самое, но подешевле.
Честно говоря, я ни разу до этого не видел, как производятся подобные вещи, и даже не представлял себе всю технологию. Поэтому сразу и с удовольствием взялся за задачу.
Но оказалось, что попасть на завод не так просто. Два производителя под разными предлогами отказались встречаться на производстве и настойчиво звали к себе в офис. У третьего офис и производство были в одном здании, и я недолго думая поехал к нему.
Завод выглядит вполне прилично, меня проводят в переговорную-шоурум.
От разнообразия образцов разбегаются глаза: карбоновый велосипед, детали для авто и мототюнинга, всякие штуковины непонятного назначения.
Целиковый капот для BMW — мечта пацанов с раёна.
Иногда в карбоновую ткань вплетают цветные нити: красные или синие, выглядит очень необычно.
Детали, покрашенные целиком, сразу и не отличишь от обычных. Обычно спортсмены так делают: им нужен низкий вес, а не понты 🙂
Мотошлем.
И нечто, неизвестно для чего нужное.
Но главной целью моего визита, было вот это:
Чехол для iPad. Меня интересовал не сам чехол, конечно, а похожие на него штуки: детали для корпусов телефонов, ноутбуков, планшетов. Было важно разобраться в технологии произодства, понимать, как правильно их проектировать, чтобы это было максимально дешево и технологично. Поэтому после долгих переговоров и уговоров я всё-таки напросился на экскурсию по цеху.
Производство занимает один этаж здания, тут чисто, но довольно пустынно.
Карбоновое полотно с нанесенным клеящим слоем поступает в рулонах. Оно бывает разной толщины, с разным рисунком плетения. Хранится в специальных холодильниках.
Ткань нарезается на куски по выкройке, и наклеиваются в несколько слоёв на матрицу. Матрицы бывают лёгкими, из чего-то типа пластика и с увеличенным ресурсом, из алюминия.
Матрицы, идущие в работу раскладываются прямо на полу, каждая в своём секторе.
Сам процесс наклейки карбона был расположен за стеклянными дверьми, но мне наотрез отказались его показывать, мол страшная коммерческая тайна. Но я не думаю, что там есть что-то секретное, просто вырезают ножницами, и укладывают лоскутки в форму.
После этого каждую деталь упаковывают в вакуумные пакеты.
Откачивают из пакетов воздух и загружают в одну из двух печей, побольше или поменьше.
Готовые детали извлекают из матриц. Если деталь сложной формы, то и матрица для неё будет сложносоставной, из нескольких частей.
Контроль качества перед сдачей на склад.
Как вы догадываетесь, это не весь процесс. Теперь у деталей нужно обрезать края и покрасить их лаком. Но это делается на другой площадке, у субподрядчика. Предлагали поехать посмотреть, но я отказался — вот там уж точно ничего нового.
Ой, вом же наверное интересно узнать про цены? Так вот, карбоновый чехольчик на iPad стоит с завода 25 долларов. А велосипед — несколько тысяч. Улыбаться перестанешь, как говорит один мой знакомый. И вариантов снижения особо не видать, слишком мелкосерийное производство, слишком много ручного труда.
Сделай сам Углеродное волокно — Усиление композитных материалов HJ3 Composite Technologies
Как домовладелец, у вас есть список всех вещей, которые потенциально могут пойти не так с вашим домом, длиной в 10 миль. У вас, вероятно, также есть очень длинный список вариантов ремонта для всех этих потенциальных проблем. Но если вы похожи на меня, ваш бюджет далеко не такой большой, как любой из этих списков, поэтому вы задаетесь вопросом, как оплачивать ремонт. Возможно, вы также осознали, что существует несколько вариантов «Сделай сам», которые позволяют взять дело в свои руки, позволяя сразу же сэкономить деньги.Но так ли надежны все эти варианты DIY, как найм эксперта? Как узнать, достаточно ли ваших собственных навыков для самостоятельного выполнения поставленной задачи? Что, если вы начнете проект и только тогда поймете, что заблуждаетесь и все равно заставляете вас вызывать подрядчика? К счастью, в хаосе всех этих страшных вопросов появляется один твердый ответ. И хотя это не применимо для всех проблем, с которыми вы столкнетесь в своем доме, наборы DIY из углеродного волокна дают вам возможность структурно укрепить свой собственный дом за считанные часы.
Не уверены в своих силах? Вы сильнее, чем думаете! Установка систем из углеродного волокна StrongHold ™, вероятно, — один из самых простых проектов по благоустройству дома, за который вы можете взяться. Как выразился один из клиентов StrongHold ™, «это проще, чем наклеивать обои». Люди из всех слоев общества, без опыта в ремонте домов или каких-либо других ремонтных работ, менее чем за один день структурно укрепляли свои изогнутые и потрескавшиеся стены и полы.На сегодняшний день StrongHold ™ используется в более чем 10 000 домов без единого обратного вызова.
1. Удалите всю краску и отслоившийся бетон.
(Вы можете арендовать шлифовальный станок в большинстве хозяйственных магазинов, если у вас его нет)
2. Пропылесосьте или смахните щеткой всю пыль.
3. Протрите стену ацетоном.
4.Загрунтуйте стену эпоксидной смолой StrongHold ™.
5. Пропитайте обе стороны углеродного волокна.
6. Прижмите углеродную ткань к стене.
7. Нанесите еще один слой эпоксидной смолы.
Вот и все! После установки комплекта StrongHold ™ вы можете закрасить его прямо поверх , чтобы уменьшить вероятность ремонта. Если вы решили красить стену, делайте это, пока эпоксидная смола еще липкая (примерно через час после установки).Если система уже затвердела и вы хотите ее покрасить, слегка отшлифуйте поверхность, чтобы отшлифовать ее перед покраской.
Хотите узнать больше о системах StrongHold ™ из углеродного волокна? Свяжитесь с нами сегодня по [email protected]!
Пять советов по работе с углеродным волокном
Итак, вы решили заняться проектом из углеродного волокна? Вот несколько советов, которые следует учитывать при работе с углеродным волокном:
1. Резка ламината из углеродного волокна
Листы из углеродного волокна можно разрезать с помощью стандартных инструментов, от ножниц и бритвенных ножей для более тонких листов до абразивных отрезных кругов и инструментов dremel. Для резки многих листов шпона из углеродного волокна мы рекомендуем использовать твердосплавные инструменты, абразивные фрезы или инструменты с алмазной коркой. Обычные стальные инструменты отлично режут углеродные листы, но из-за абразивной природы всех углеродных листов стандартные инструменты быстро изнашиваются при интенсивной резке. Панели затем легко шлифуются по краям, что позволяет обрезать и шлифовать до окончательных размеров для получения гладких и чистых краев. См. Нашу сводку стандартных толщин для получения более подробной информации о режущих инструментах для каждой толщины.
2. Соображения, касающиеся здоровья и безопасности
Углеродная пыль не токсична, однако она вызывает легкое раздражение кожи, глаз и легких, как и стекловолокно. Мы настоятельно рекомендуем вам носить респиратор, чтобы свести к минимуму зуд или раздражение, особенно при резке или шлифовании в большом количестве. Края могут быть очень острыми, поэтому перчатки также важны, чтобы избежать порезов и порезов.
3. Клей
См. Нашу страницу «Варианты клея» для получения дополнительной информации о лучших альтернативах углеродному волокну.
4. Углеродное волокно
Панели из углеродного волокна, изготовленные из эпоксидных смол, не являются термопластичными (термоформованными) — готовый лист нельзя нагревать и сгибать для сохранения искривленной формы. Ламинат из углеродного волокна не растягивается, как пластик. Вы можете получить очень ограниченное количество постоянной кривизны в одном направлении с помощью высокой температуры (более 200 o F), но из-за трудностей, связанных с этим, мы не рекомендуем это. Можно изготавливать формованные детали, но ткань из углеродного волокна должна быть помещена в форму и пропитана эпоксидной смолой перед процессом нагрева / отверждения.
Имейте в виду, что гибкий лист из углеродного волокна будет изгибаться по простой кривой, например, вокруг трубы, но не по сложной кривой, как при накрытии мяча.
Несколько пользователей сообщили об успешной установке наших облицовок из углеродного волокна с клейкой пленкой на глушители и выхлопные патрубки, однако мы не можем дать каких-либо конкретных рекомендаций для областей применения с температурой более 200 o F. Вы можете поэкспериментировать с теплом, но имейте в виду, это полностью на ваш страх и риск.
5. Возможности обработки
Многие люди используют станки с ЧПУ для резки панелей из углеродного волокна, но иногда бывает трудно удержать листы из углеродного волокна в станке.Вырубка также возможна. Обязательно найдите слесаря или высекального станка, имеющего опыт работы с углеродным волокном, или оставьте обработку нам. Наши опытные сотрудники с ЧПУ справятся даже с самыми сложными операциями по резке.
Водоструйные резаки используются для изготовления деталей сложной, сложной формы или больших объемов. Наш высокоэффективный клей 3M можно наносить ПЕРЕД водоструйной обработкой деталей из углеродного волокна, так как вода не повредит клей, оставляя красивый чистый край как на листе из углеродного волокна, так и на клее.
Имеете в виду проект?
Мы рады предоставить бесплатную консультацию без обязательств.
BBC — Путешествия — Может ли технология удаления углерода сделать путешествия более экологичными?
Если ваши планы поездок на 2020 год были отменены из-за коронавируса, компенсация выбросов углерода, вероятно, станет последней вещью, о которой вы думаете. По данным Международной ассоциации воздушного транспорта (ИАТА), всего 1% авиапассажиров участвовали в добровольной компенсации выбросов углерода до того, как вступили в силу ограничения на поездки, вызванные вирусом. Компенсация выбросов, связанных с поездкой, скорее всего, изначально не входила в ваш список приоритетов.
Мы знаем, что путешественники хотят взять меры по борьбе с изменением климата в свои руки
Тем не менее, на фоне прогнозов, что снижение глобальных выбросов, зафиксированных во время отключений коронавируса, может быть недолгим, и что экономические последствия вируса могут замедлить усилия по сокращению авиационных выбросов В долгосрочной перспективе добровольное сокращение выбросов углекислого газа, вероятно, будет более важным, чем когда-либо, когда международная туристическая индустрия снова включит все двигатели.
Может ли новая форма компенсации выбросов углерода помочь увеличить участие путешественников?
Рост технологий удаления углерода
Возникшая в результате переговоров по климату в Киото в 1997 году, компенсация выбросов углерода уже давно борется с проблемой имиджа. Компенсационные схемы позволяют людям инвестировать в экологические проекты, предназначенные для изоляции выбросов углерода (например, посадка деревьев) или предотвращения выбросов (например, в проекты возобновляемых источников энергии), но отсутствие регулирования и подотчетности в первые дни подпитывало широко распространенное недоверие к их эффективности .
Совсем недавно лесные пожары, охватившие Австралию, Калифорнию и Амазонку, усугубили проблемы, связанные со схемами компенсации, основанными на лесном хозяйстве (когда дерево горит, оно высвобождает весь свой запас углерода обратно в атмосферу).
Сложность точной количественной оценки большинства программ компенсации выбросов углерода (трудно измерить, например, объем выбросов, которые вы компенсируете, внося свой вклад в проект чистой кухонной плиты, инициатива по энергоэффективности, обычно финансируемая компенсирующими организациями) помогло.
Затем появился Climeworks, швейцарский стартап, который первым разработал технологию, которая высасывает углерод из воздуха и превращает его в камень, эффективно удаляя выбросы углерода из атмосферы мгновенно, безопасно и навсегда.
Вас также может заинтересовать:
• Будет ли путешествие безопаснее к 2022 году?
• Как Исландия навсегда ликвидирует выбросы углерода
• Будущее путешествий под водой?
Расположенная на покрытых мхом склонах действующего вулкана на юго-западе Исландии, первая установка по удалению углерода с постоянным хранилищем Climeworks была запущена в 2017 году. Работая на отходящем тепле геотермальной электростанции, она использует технологию прямого улавливания воздуха (DAC). ) для втягивания окружающего воздуха в гигантские пылесосы, называемые сборщиками СО2.Затем углерод отделяется от захваченного воздуха, объединяется с водой и закачивается на 700 м под землю. В результате естественной минерализации углекислый газ реагирует с базальтовой породой и через несколько лет превращается в камень, а оставшийся воздух просто возвращается в атмосферу.
Подобно посадке деревьев и удобрению океана, DAC — это то, что известно как средство для удаления углекислого газа или технология отрицательных выбросов. Эти решения обычно составляют основу проектов по компенсации выбросов углерода, поддерживаемых такими авиакомпаниями, как Qantas и Delta, при этом большинство перевозчиков теперь согласовано с проектами, подтвержденными такими организациями, как Gold Standard и Verified Carbon Standard.Когда дело доходит до смягчения последствий изменения климата, когда-то считавшиеся гораздо менее важными, чем сокращение выбросов с самого начала, решения по удалению углекислого газа получили значительную научную поддержку в 2018 году, когда публикация отчета МГЭИК о сдерживании повышения глобальной температуры до 1,5 ° C в этом столетии показала, что эти технологии будут иметь важное значение для достижения климатических целей «с ограниченным превышением или без него».
Хотя большинство климатологов согласны с тем, что для того, чтобы повернуть вспять время глобального потепления, необходим портфель решений по удалению углекислого газа, эффективность и измеримость DAC с постоянным хранилищем в сочетании с его минимальным физическим воздействием и незначительным воздействием на окружающую среду (сторона Climeworks) выбросы составляют менее 10% CO2, который он высасывает из атмосферы), эта технология стала особенно многообещающим подходом.
«С точки зрения эффективности, одно дерево удаляет примерно 25 кг CO2 в год, что делает один коллектор CO2 Climeworks в 2000 раз более эффективным на площади, чем дерево», — сказал Ян Вурцбахер, соучредитель и содиректор Climeworks, которая в Июнь был назван Всемирным экономическим форумом среди 100 пионеров технологий 2020 года.
«За последнее десятилетие мы доказали, что прямой захват воздуха не только возможен, но и коммерчески жизнеспособен в больших масштабах».
Действительно, хотя первая постоянная установка для удаления углерода Climeworks способна превращать всего 50 тонн углерода в камень в год — капля в море по сравнению с 36 миллиардами тонн углерода, выброшенными во всем мире в 2019 году, — компания быстро расширяется, с новым производством в Исландии, способным постоянно удалять несколько тысяч тонн углерода в год, который должен открыться к концу 2020 года.
Climeworks также имеет более десятка других заводов в Европе, которые улавливают углерод для продажи на коммерческой основе для использования во всем, от газированных напитков до синтетического топлива, что помогает финансировать постоянное удаление углерода в бизнесе.
Мобилизация путешественников
В июне 2019 года Climeworks стала первой компанией в мире, которая запустила персональную систему удаления углерода с помощью службы DAC для общественности, с подпиской на 7 евро в месяц с финансированием 85 кг углерода в год. в камень.
Теперь новая платформа постоянного удаления углерода, предназначенная для путешественников и запущенная в партнерстве с Ассоциацией торговли приключенческими поездками (ATTA), присоединилась к движению, чтобы помочь компенсировать колоссальные 8% глобальных выбросов, за которые несет ответственность международная туристическая индустрия.
«Выводы отчета IPCC, особенно срочность, необходимая для оказания воздействия, глубоко повлияли на меня», — сказала Кристина Бекманн, вице-президент по глобальной стратегии ATTA.
После участия в саммите по климату, призванном помочь делегатам принять меры по борьбе с изменением климата в пределах их собственных сфер влияния, Бекманн основала образовательную платформу по удалению углерода Tomorrow’s Air on Earth Day 2020 (22 апреля). Два месяца спустя, в июне, Tomorrow’s Air запустила собственную онлайн-службу удаления углерода в партнерстве с Climeworks.
Пока мы не придумаем действительно экологически безопасный способ полета людей вокруг планеты, нам нужно будет летать меньше
В то время как углеродные кредиты, продаваемые Climeworks и Tomorrow’s Air, направлены на превращение углерода в камень (при этом Tomorrow’s Air сохраняет 2 доллара США. от ежемесячной подписки в размере 10 долларов на финансирование повышения осведомленности), Бекманн уверен, что запуск платформы по удалению углерода, инкубированной ATTA, которая охватывает более шести миллионов путешественников с приключениями, поможет мотивировать больше путешественников подписаться.Путевые льготы для подписчиков уровня «Clean Up Champion» (которые обещают 75 долларов США в месяц за удаление 600 кг углерода в год), в том числе скидки на туристическое снаряжение и эксклюзивные советы и контакты, делают сделку еще более приятной.
Однако если вы только что посчитали, вы бы поняли, что годовая подписка на Clean Up Champion (стоимостью 900 долларов США) едва ли компенсирует перелет эконом-класса в одну сторону из Лос-Анджелеса в Нью-Йорк. Город, что делает превращение углерода в камень очень дорогим по сравнению с традиционными схемами компенсации выбросов углерода.Чтобы увидеть разницу в ценах, компенсация тонны углерода через немецкую некоммерческую организацию Atmosfair, которая поддерживает проекты устойчивого развития, сертифицированные золотым стандартом, стоит всего 23 евро (20,80 фунтов стерлингов). Но поскольку Climeworks прогнозирует, что в течение трех лет она сократит свои затраты на две трети, разрыв в ценах сокращается.
«В конечном итоге Tomorrow’s Air будет успешным благодаря тому уровню осведомленности, который он создает, а также удаляет углерод», — сказал Бекманн, который недавно запустил виртуальные туры по заводу Climeworks в Швейцарии через Airbnb Experiences, чтобы потребители могли сами увидеть, как DAC технология работает. «Мы знаем, что путешественники хотят взять меры по борьбе с изменением климата в свои руки, и Tomorrow’s Air предлагает простой и интересный способ оказать немедленное воздействие, помогая снизить затраты на постоянное удаление углерода».
Может ли это быть новая компенсация выбросов углерода?
Поскольку постоянное удаление углерода становится более доступным для путешественников с помощью этих двух схем, социолог-эколог и научный сотрудник Саутгемптонского университета доктор Роджер Тайерс, который изучал компенсацию выбросов углерода в своей докторской диссертации, говорит, что это может помочь поддержать индустрию компенсации.
«Более измеримые компенсации, такие как прямое улавливание воздуха (либо для постоянного удаления, либо для создания альтернативы ископаемому топливу), могут поднять стандарты на всем рынке офсетных материалов», — сказал он. «Они также могут помочь пролить свет на более дешевые и менее эффективные схемы компенсации, которые доминировали на рынке до сих пор и которые часто слишком хороши или дешевы, чтобы быть правдой».
До тех пор, пока удаление углерода с помощью постоянного хранилища не станет более финансово выгодным для путешественников, другим поставщикам компенсационных услуг, возможно, не следует слишком беспокоиться о потере клиентов.Но основатели Climeworks и Tomorrow’s Air надеются, что необходимость принятия срочных мер по борьбе с изменением климата побудит путешественников раньше, чем позже, включить постоянное удаление углерода в свои стратегии компенсации выбросов углерода.
«Путешественникам не следует отказываться от других экологически безопасных решений — они все нам нужны», — сказал Бекманн. «Но, вкладывая часть своего компенсирующего бюджета на удаление углерода с помощью постоянного хранилища, путешественники могут продемонстрировать свою поддержку этого более быстрого и надежного решения.
Однако, поскольку международные границы начинают медленно открываться после блокировки коронавируса, Тайерс советует, что удаление углекислого газа путем превращения углерода в камень, как и любую другую форму компенсации выбросов углерода, не должно рассматриваться как оправдание для бронирования длительного периода Тащим отпуск с чистой совестью.
«Пока мы не разработаем действительно экологически безопасный способ полета людей по планете, нам нужно будет меньше летать», — сказал он. «Это так просто».
Future of Travel — это серия сериалов от BBC Travel, в которой исследуется, как мир может выглядеть для путешественников в ближайшие годы, и рассказывается о людях, живущих на переднем крае перемен.
Присоединяйтесь к более чем трем миллионам поклонников BBC Travel, поставив нам лайк на Facebook или подписавшись на нас в Twitter и Instagram .
Если вам понравилась эта история, подпишитесь на еженедельную рассылку новостей bbc.com под названием «The Essential List». Специально подобранная подборка историй из BBC Future, Culture, Worklife и Travel, которые доставляются вам на почту каждую пятницу.
Английская деревня стремится к углеродной нейтральности | Окружающая среда | Все темы от изменения климата до сохранения | DW
К югу от Манчестера, Ashton Hayes представляет собой совокупность твидовых коттеджей и красивых домов, расположенных между зелеными полями и деревьями. Но последние 10 лет эта маленькая деревня показывала мировым лидерам, как спасти планету.
«Я выключила вещи, надела больше перемычек, изменила способ использования электричества — например, я никогда после этого не использовала его для нагрева воды», — говорит местная Кейт Харрисон, чтобы объяснить, как ей удалось сократить потребление энергии. на колоссальные 60 процентов за короткий период времени.
«В конце концов, я заменил свой котел на более эффективный — и, по правде говоря, просто погрузился в проект.«
Солнечные батареи возникли в самых неожиданных местах, например, в этом поле.
Первая деревня с нулевым выбросом углерода
Кейт, как и многие другие местные жители, вдохновилась 10 лет назад, когда другой сельский житель предложил уже близкий — сплочите сообщество, чтобы попытаться стать первым городом в Англии с нейтральным выбросом углерода.
«Я пришла на первое собрание, мне понравилось то, что я услышал, и я решила пойти домой, чтобы что-то с этим поделать», — говорит она. может быть так просто, но за десятилетие, прошедшее с момента начала реализации проекта углеродной нейтральности, было сделано гораздо больше.
«Недавно мы полностью покрыли крышу начальной школы панелями, и это фактически с мая сделало школу отрицательной по выбросам углерода», — объясняет Гарри Чарнок, бывший журналист, который впервые представил идею углеродно-нейтрального баланса группе друзей во время паб викторины.
«Школа экспортирует больше энергии, чем использует. И школа рада, потому что это экономит им небольшое состояние».
Создание энергии
В деревне теперь есть коммунальная компания по возобновляемым источникам энергии, которая арендует крышу у нескольких других общественных зданий.Предприятие использует солнечную энергию и получает прибыль для реинвестирования в проекты, направленные на то, чтобы сделать деревню еще более устойчивой.
В других местах люди установили собственные солнечные батареи, сократили количество рейсов, сменили автомобили и перестали пользоваться сушильными барабанами. И оказывается, каждая мелочь действительно помогает.
Приведены данные за 2012 год, самый последний доступный
«Мы сократили внутренние выбросы углерода примерно на 20 процентов в первый год и немного увеличили это», — объясняет местный житель Рой Александер.«Если мы посмотрим на отдельные дома, которые участвовали в опросе как в 2006, так и в 2015 году, то в среднем их будет не менее 33 процентов — больше, чем если мы включим компенсацию выбросов углерода за перелеты», — добавляет он.
Александр — профессор экологической устойчивости в соседнем Честерском университете. Он отвечал за несколько подробных исследований энергопотребления в деревне за 10 лет реализации проекта углеродной нейтральности. Он убежден, что необходимы местные действия, чтобы реально изменить мировые климатические проблемы.
Рой Александер, профессор экологической устойчивости, Честерский университет
«То, что планируют правительства, не соответствует обязательствам, взятым на Парижском саммите по климату», — говорит он. «Но если мы сможем заставить все население внести эти небольшие изменения в свой образ жизни, тогда мы сможем помочь заполнить этот разрыв между тем, что мы взяли на себя, и тем, что нам нужно делать».
Никаких политиков
Проект вызвал большой политический интерес и несколько визитов лондонских правительственных чиновников.Тем не менее, жители деревни стремились полностью исключить политику партии. Бездействие или неадекватная реакция правительств на вызовы изменения климата отчасти стали причиной того, что они решили действовать в одиночку.
«У нас было довольно много политиков, которым разрешили прийти, послушать и узнать больше, но им никогда не разрешали обращаться к нам», — говорит Гарри Чарнок.
«Мы хотели, чтобы здесь не было боевых действий. Просто чтобы побудить людей не показывать пальцем, а говорить:« Что мы можем сделать в нашей сфере влияния ».'»
Местные продукты
Деревенский магазин, также принадлежащий общине, является еще одним свидетельством стремления сократить выбросы углерода. Местные продукты изобилуют, от меда и овощей до сыра и мяса.
Кейт Харрисон (слева) ), и Деб Дейнем покупает местные продукты
«У нас здесь есть прекрасные пирожные, они сделаны Хизер, которая тоже работает в магазине», — говорит менеджер магазина Деб Дейнем. Когда магазину угрожали закрытием, сообщество собрались и купили, — объясняет она.
«Если бы мы не спасли магазин, нам пришлось бы проехать 3 мили [около 5 километров] до ближайшего магазина, что опять же вредно для окружающей среды», — добавляет она.
Ashton Hayes все еще далек от своей цели — стать полностью углеродно-нейтральным — но это не имеет особого значения, говорят местные жители. Что отличает этот проект, так это то, как люди взяли вопрос об изменении климата в свои руки и фактически что-то с этим сделали — в отличие от правительств многих стран, которые продолжают дискутировать, не предпринимая конкретных действий.
И их послание распространяется: около 200 городов со всего мира связались, чтобы извлечь уроки из опыта этой деревни.
Ваш двор — незаметный пожиратель ископаемого топлива — измените его климат
Примечание редактора: Хотите экологически чистый дом? Ваш двор — хорошее место для начала. Это первое из пяти руководств по уходу за газоном на открытом воздухе для уменьшения выбросов углекислого газа и создания благоприятной для птиц среды обитания.Прочтите части вторую, третью, четвертую и пятую.
Представьте себе эту знакомую сцену в городах и пригородах по всей Америке: ландшафтные бригады выпрыгивают из гигантских восьмицилиндровых грузовиков и запускают различные косилки, воздуходувки и другие двигатели, потребляющие много газа, — и все это во имя сохранения наших зеленых дворов. С точки зрения выбросов углекислого газа, «было бы лучше просто вымостить ландшафт», — полушутя говорит эксперт по садоводству Дуг Кент, когда мы гуляем по одному из его садов с низким содержанием углерода в Манхэттен-Бич, Калифорния.
Многие садовники считают, что их деятельность благоприятна для климата, потому что дворы полны растений, которые поглощают углекислый газ, ведущий парниковый газ. Но уход за типичным садом «невероятно зависит от ископаемого топлива», — говорит Кент, автор A New Era of Gardens (2001), первой книги по низкоуглеродному садоводству, опубликованной в Соединенных Штатах. На самом деле, отмечает он, многие сады выделяют больше CO2, чем поглощают, а зачастую и намного больше.
Хорошая новость в том, что если вы возьмете на себя заботу о своем дворе, вы сможете уменьшить его воздействие на климат, сохраняя воду и ресурсы и создавая среду обитания.Ниже приведены наиболее важные шаги, которые вы можете предпринять, чтобы сократить выбросы парниковых газов в вашем ландшафте.
Выбираю People Power
Потрясающий ассортимент электроинструментов используется в ландшафтах — не только косилки и воздуходувки, но также кромкообрезные машины, кусторезы, измельчители сорняков, измельчители, измельчители, мотокультиваторы и многое другое. По данным Калифорнийского совета по воздушным ресурсам, эти «маленькие внедорожные двигатели», или SORES, значительно превосходят по численности легковые автомобили в «Золотом штате», довольном транспортными средствами. Исследование Агентства по охране окружающей среды подсчитало, что на долю SORES приходится 4 процента выбросов CO2 по всей стране. Они также являются основными компонентами смога и выделяют ряд загрязняющих веществ, вызывающих рак.
Если вы не можете положиться на свой сорняк, чтобы держать ландшафт под контролем, что вы должны делать? Кент, преподающий экологический ландшафтный дизайн и менеджмент в Калифорнийском государственном политехническом университете в Помоне, восхваляет власть людей. По его словам, чтобы уменьшить влияние вашего ландшафта на изменение климата, «лучшее, что вы можете сделать, — это уменьшить количество используемой техники.«А использование ручных инструментов, таких как барабанные косилки и грабли, — отличное упражнение, — добавляет он. Такой подход к ландшафтному дизайну, ориентированный на людей, вполне выполним, если вы уменьшите размер лужайки и избегаете таких сложных функций, как ухоженные изгороди.
Некоторые люди поменяли свои газовые садовые инструменты на более энергоэффективные и бесшумные электрические. Но если ваша электроэнергия не поступает из солнечной, ветровой или других возобновляемых источников, они все равно вносят вклад в общие выбросы углерода. Power Profiler EPA дает вам подробную информацию о том, откуда поступает ваша электроэнергия, чтобы помочь вам оценить углеродный след вашего SORES.
Избавьтесь от привычки удобрять
Большинство садоводов удивлены, узнав, что одним из основных источников выбросов парниковых газов в результате ухода за газонами является использование азотных удобрений.
«Большинство садоводов удивлены, узнав, что одним из основных источников выбросов парниковых газов в результате домашнего садоводства и ухода за газонами является использование азотных удобрений», — говорит Дэвид Вулф, профессор экологии растений и почвы Корнельского университета. По словам Вулфа, производство синтетических удобрений чрезвычайно энергоемко: на каждую тонну произведенного азота обычно попадает от четырех до шести тонн углерода.Более того, большинство удобрений содержат больше азота, чем растения могут усвоить, а почвенные микробы превращают избыток азота в газообразную закись азота, которая в 300 раз больше улавливает тепло, чем CO2.
При использовании синтетических или органических удобрений выделяется закись азота. Но органические удобрения лучше синтетических, потому что огромные выбросы CO2, связанные с производством, в основном устраняются. А если в качестве основного источника питания растений использовать дворовые обрезки, компостированные на собственном заднем дворе, вы также избавитесь от выбросов парниковых газов, связанных с упаковкой и транспортировкой покупных товаров.В качестве бонуса это уберегает садовый мусор от свалок, где он разрушается и выделяет метан, еще один мощный парниковый газ.
Хватит тратить воду
По данным EPA, садоводство поглощает в среднем более 30 процентов воды, потребляемой домохозяйствами, и до 60 процентов в засушливых регионах. Почти половина теряется из-за ветра, испарения и стока из-за неэффективных ирригационных систем. Если бы этого было недостаточно, на перекачку, очистку и распределение воды приходилось от 3 до 4 процентов национального потребления электроэнергии, а это означает, что орошение является причиной значительного количества выбросов CO2.
Самый эффективный способ перестать тратить воду впустую — это выращивать растения, подходящие к условиям вашей собственности и количеству осадков в вашем регионе. Ручной полив — это наиболее безопасный для климата способ увлажнить их при необходимости. Если вам необходимо поливать, убедитесь, что профессионал, которого вы нанимаете для установки и обслуживания вашей системы, сертифицирован программой EPA WaterSense, которая помогает потребителям определять продукты и услуги, обеспечивающие экономию воды.
Терять лужайку
Неудивительно, что бесконечное кошение, обдув, внесение удобрений и орошение при уходе за газоном приводит к значительному влиянию на климат.Что еще хуже, 40 миллионов гектаров газонов в стране, которые являются нашей крупнейшей орошаемой культурой, мало что предлагают птицам и другим животным. Замена лужайки местными деревьями, кустарниками и почвопокровным покровом не только сократит выбросы парниковых газов в вашем ландшафте, но и привлечет птиц обратно в ваш сад, и они тоже будут отлично выглядеть.
Сад на Манхэттен-Бич — хороший тому пример. «Здесь не используются никакие электроинструменты, — говорит Кент. — Сад полностью поливается вручную». Впечатляющий калифорнийский платан бросает прохладную тень на большую часть заднего двора.Спереди низкорослые цветы придают больше цвета и сезонного интереса, чем типичный газон. Лучше всего то, что цветущий фуксией крыжовник, цветок золотой обезьяны, калифорнийский фланелевый куст и другие местные полевые цветы привлекают очаровательное множество птиц, пчел и бабочек.
9 прыгающих шариков углерода: открытие и обещание фуллеренсов | Позитрон по имени Присцилла: научное открытие на границе
при осмотре вмятины в бывшей орбитальной установке для длительной экспозиции (LDEF), которая была возвращена на Землю космическим шаттлом.По всей видимости, крошечный богатый углеродом метеорит врезался в спутник и оставил после себя осколок в образовавшейся вмятине. Ученым удалось продемонстрировать, что фуллерены образовались не в результате столкновения с LDEF, а были действительно космическими — оставленными метеоритом.
БИБЛИОГРАФИЯБаум Р. М. 1991. Систематическая химия C 60 начинает появляться. Новости химии и машиностроения 69 (50): 17–20.
Бетюн, Д.S., G. Meijer, W. C. Tang и H. J. Rosen. 1990. Колебательные спектры комбинационного рассеяния очищенных твердых пленок C 60 и C 70 . Chemistry and Physics Letters 174: 219–222.
Дагани Р. 1992. Наноструктурированные материалы обещают продвинуть вперед целый ряд технологий. Новости химии и машиностроения 70 (47): 18–24.
Хокинс, Дж. М., А. Мейер, Т. А. Льюис, С. Лорен и Ф. Дж. Холландер. 1991. Кристаллическая структура осмилированного C 60 : Подтверждение каркаса футбольного мяча.Science 252 (12 апреля): 312–313.
Хебард А. Ф. 1992. Сверхпроводимость в легированных фуллеренах. Физика сегодня 45 (11): 26–32.
Holczer, K., O. Klein, S.-M. Хуанг, Р. Б. Канер, К.-Дж. Фу, Р. Л. Веттен и Ф. Дидерих. 1991. Щелочно-фуллеридные сверхпроводники: синтез, состав, диамагнитная защита. Science 252 (24 мая): 1154–1157.
Джонсон Р. Д., Г. Мейер и Д. С. Бетюн. 1990. C 60 имеет икосагредральную симметрию. Журнал Американского химического общества 112: 8983-8984.
Джонсон Р. Д., Дж. Мейер, Дж. Р. Салем и Д. С. Бетюн. 1991. 2D ядерно-магнитно-резонансное исследование структуры фуллерена C 70 . Журнал Американского химического общества 113: 3619.
Джонсон, Р. Д., М. С. де Фриз, К. С. Яннони, Д. С. Бетюн и Дж. Р. Салем. 1992. Исследования электронного парамагнитного резонанса лантансодержащего C 82 . Nature 355: 239–240.
Джонсон Р. Д., К. С. Яннони, Х. К. Дорн, Дж. Р. Салем и Д.С. Бетюн. 1992. C 60 вращение в твердом состоянии: динамика граненого сферического волчка. Наука 255: 1235–1238.
Джонс, Д. Э. Х. 1966. Ариадна. New Scientist 245 (3 ноября): 245.
Кретчмер, В., Л. Д. Лэмб, К. Фостиропулос и Д. Р. Хаффман. 1990. Solid C 60 : новая форма углерода. Nature 347 (27 сентября): 354–358.
Крото, Х. У., Дж. Р. Хит, С. К. О’Брайен, Р. Ф. Керл и Р. Э. Смолли. 1985. C 60 : Бакминстерфуллерен.Nature 318 (6042): 162–163.
Meijer, G., and D. S. Bethune. 1990. Лазерное осаждение кластеров углерода на поверхности: новый подход к изучению фуллеренов. Журнал химической физики 93: 7800–7802.
Meijer, G., and D. S. Bethune. 1990. Масс-спектроскопическое подтверждение присутствия C 60 в углеродной пыли, произведенной в лаборатории. Письма по химии и физике 175: 1–2.
О углеродном волокне — Schmolke Carbon
О углероде
Что такое углерод?
Когда говорят о углероде, обычно имеют в виду композиты из углеродного волокна.Эти углеродные волокна заключены в матрицу из пластика. Углеродные волокна — это промышленно производимые волокна, изготовленные из сырья, содержащего углерод, которое с помощью термических процессов превращается в графитоподобный порядок. Углеродные волокна чрезвычайно легкие и обладают огромной прочностью на разрыв. Чтобы технически использовать только тонкие волокна толщиной 5-8 мкм в качестве ровинга (мотка) или однонаправленных тканей, их включают в пластиковую матрицу.
Первые детали из пластика, армированного углеродным волокном (crp), появились примерно в конце 80-х годов, тогда они были сделаны из «сухих» тканей из углеродного волокна, которые затем пропитывались жидкой смолой.
Спустя некоторое время стали популярными так называемые «препрег», а «препрег» — это сокращение от «пропитанный». Эти препреги были погружены во все еще влажную пластиковую матрицу, что обеспечивает лучшее качество ламината с более равномерным распределением смолы.
Schmolke Carbon присутствовал с самого начала. Мы уже извлекли первые уроки из «сухих» карбоновых тканей. Наше понимание качества заставило нас перейти к препрегам уже на ранней стадии, хотя в то время препреги были настолько редки (читай: дорогими), что использовались только в аэрокосмической отрасли.С годами качество сырья, в частности волокна, улучшилось, как и качество продукции Schmolke. Например, эволюция волокон с 2000 года означает увеличение предела прочности на разрыв в два раза. Компания Schmolke всегда придерживалась политики использования лучших материалов, которые можно купить за деньги, поэтому наше преимущество превратилось в постоянно растущее лидерство в области технологий.
Что делает углеродные волокна такими особенными?
Углеродные волокна и изделия из них отличаются исключительной прочностью и жесткостью, но в то же время чрезвычайно легкими. Углеродные волокна также отличаются своей «анизотропией». Так что это значит? Например, металлы выдерживают нагрузки независимо от их направления. Это свойство дает им право на «изотропию». В отличие от этого пластики, армированные углеродными волокнами, намного лучше выдерживают нагрузки в направлении волокон, чем нагрузки, перпендикулярные направлению прядей. Они превосходны, когда дело доходит до растягивающих нагрузок, но для давлений они не так хороши. Такое изменение характеристик называется «анизотропией».
Анизотропный характер материала можно использовать с пользой. Если проанализировать нагрузки, преобладающие в конкретной ситуации, можно укладывать волокна только в тех направлениях, где они действительно необходимы, что позволяет сэкономить как материал, так и вес. Это требует тщательного и глубокого понимания нагрузок и напряжений, которые должна выдержать конкретная деталь, и компоновки волокон с учетом этих факторов. Многолетний опыт конструирования и производства деталей из углеродного волокна просто незаменим, когда дело доходит до изготовления деталей, которые являются эталоном качества и производительности в своей области.
Как подогнать детали?
Растягивающие нагрузки — сильная сторона углеродных волокон. Изгибающие нагрузки всегда включают растягивающие нагрузки; следовательно, они также не представляют серьезной проблемы для углерода. Преимущество углеродных волокон менее очевидно при многоосных нагрузках (то есть нагрузках с разными направлениями). Такие ситуации давления обычно типичны в местах, где детали сжаты, например, в зонах зажима. Мы анализируем характер этих напряжений и укрепляем свои части в соответствующих местах.Поскольку мы не хотим добавлять лишний вес, важно определить пределы для этих локальных нагрузок. Следуйте рекомендуемым настройкам максимального крутящего момента и не зажимайте детали за пределами отмеченной усиленной области. Какими бы прочными ни были детали из углеродного волокна, сила зажима — их ахиллесова пята!
Чем отличается продукция Schmolke?
Как обычно, качество имеет свою цену. Schmolke Carbon поставил перед собой цель создать одновременно легкую и интеллектуальную конструкцию. Это означает, что мы разрабатываем наши продукты в соответствии с вашими требованиями и условиями использования. Вес и стиль езды гонщика так же важны, как и пробег. Детали, изготавливаемые по индивидуальному заказу, определяются не только своими размерами и диаметром, в первую очередь это наслоение волокон, которое делает каждую деталь уникальной. Каждый руль и подседельный штырь изготавливаются вручную, тщательно следуя определенной схеме. Такое расположение волокон снижает вес деталей, оставляя при этом достаточный запас прочности, чтобы выжить даже в нестандартных ситуациях.
Чтобы гарантировать максимально возможное качество, мы разрабатываем и производим все наши детали в Германии.
Еще одним фактором, который отличает нас от других и, возможно, более дешевых производителей, является то, что мы используем только лучшее качество волокна, которое Toray, лидер рынка и технологий из Японии, может поставлять.
Как показано на диаграмме ниже, волокна T1000, которые мы используем в нашей линейке TLO, имеют предел прочности на разрыв примерно на 30% выше, чем предел прочности волокон T700, более широко используемых в велосипедной промышленности. Волокна T1000 стоят вдвое дороже.
Не меньший вклад в доказанное качество Schmolke — это наше внимание к деталям. Мы используем множество тонких слоев, потому что это необходимо для точного моделирования соответствующих нагрузок. В качестве побочного эффекта многослойные конструкции также повышают усталостную прочность, то есть срок службы детали. Вдобавок к этому большее количество слоев делает менее внезапным и непредсказуемым отказом, если части должны сломаться. В отличие от простых конструкций с несколькими слоями из многих тонких слоев, деталь не становится «хрупкой» с тенденцией к внезапному разрушению; они надежнее и безопаснее.
K-фактор — что такое 1K, 3K и 12K?
За последние пару лет маркетологи использовали такие термины, как 1K или 3K, когда писали о углероде. Он определяет количество мельчайших волокон (нитей), используемых в одном ровинге. 1K означает 1000 нитей, 3K — 3000 и так далее.
Эти ровницы затем переплетаются по двум осям, образуя углеродную ткань. Различия между тканями в основном заключаются во внешнем виде.
UD — что за история?
UD — это сокращение от однонаправленного.Это означает, что все волокна лежат параллельно в одном направлении, без перекрестных волокон или переплетения. Поэтому такие вещи, как 1K, 3K или 12K, не имеют никакого значения. Единственное, что имеет значение, — это общее количество используемых волокон, то есть вес слоев по отношению к площади. Это то, о чем обычно не упоминают маркетологи.
UD отличается от ткани не только своим внешним видом, но и его механические свойства: в ткани волокна слегка изогнуты из-за плетения.Это приводит к небольшому снижению прочности на разрыв; волокна не такие прямые, как хотелось бы. Однако ткани с сеткой из нитей лучше предотвращают образование трещин в случае разрушения. Поэтому волокна UD
могут быть неплохой идеей для рам, где более чем одна ванна выдерживает вес всадника. Выход из строя одной трубки не обязательно приводит к поломке. Что касается наших деталей, мы не довольны трендом UD. При желании мы сделаем рули и подседельные штыри с поверхностным слоем UD, мы всегда будем использовать ткань под ним из соображений безопасности, это помогает предотвратить «хрупкие» изломы и быстрое расширение трещин.
Увеличенный размер по сравнению с диаметром 26 / 25,4 мм
Тенденцию увеличения размера руля диаметром 31,8 мм необходимо оценивать с разных точек зрения. В общем, правда, что большие диаметры с уменьшенной толщиной стенок делают часть излишне жесткой при неизменном весе. Имея это в виду, было бы неплохо увеличить диаметр и соответственно уменьшить толщину стенки.
Но этому есть предел.Чем тоньше стена, тем более хрупкой она становится против давления и — учитывая хорошо известный эффект банки из-под кока-колы — легко вмятина. Поскольку углеродное волокно намного лучше выдерживает растягивающие нагрузки, чем давление, оно не поддается тенденции увеличения размеров. При наличии сил давления, характерных для зажима стержней штоком, эту область необходимо укрепить.
Наш негабаритный дорожный брус, самый легкий в мире, весит на 5 г больше, чем его аналог стандартного размера с диаметром 26 мм.Тем не менее, он имеет эргономичную опору для рук и более жесткий, поскольку больший диаметр сохраняется по всей средней части руля.
Предоставляет ли Schmolke Carbon гарантию на свою продукцию?
Соответствующий гарантийный срок составляет 24 месяца. Мы идем на один лучше и покрываем все продукты трехлетней гарантией. Помимо стандартной гарантии, мы также предлагаем пожизненную замену после аварии. Замена при сбое определяется в каждом конкретном случае в зависимости от возраста продукта.Если вам нужна аварийная замена, отправьте копию счета, краткое описание повреждений и фотографии по адресу [email protected], и мы свяжемся с вами в течение 48 часов.
Что означает «SL»?
«SL» означает «сверхлегкий». Для наших подседельных штырей и рулей мы используем волокна качества T800 для этой линейки продуктов, в то время как детали из углеродного волокна других производителей обычно подходят для чего угодно от T300 до T700. В дополнение к тому, что мы знаем, как создавать детали из углеродного волокна, сочетание этих двух факторов приводит к сочетанию низкого веса и надежности, за которые мы выступаем.
Что означает «TLO»?
«ТЛО» — «самый легкий». Для этой линии подседельных штырей и рулей мы просто используем лучшее, что можно купить за деньги, это волокна T1000. Их прочность на разрыв еще на 16% выше, чем у T800. В дополнение к этому наши ламинаты TLO используют еще более сложную структуру слоев. Комбинация приводит к множеству мировых рекордов веса; еще легче, чем SL, без ущерба для надежности и жесткости.
Насколько безопасны продукты Schmolke Carbon?
Перед началом производства мы тестируем наши детали на испытательном стенде специально для этой работы.Наши процедуры испытаний соответствуют стандартам, определенным новыми нормами DIN EN 14781 и 14766. Как только мы с этим закончим, мы идем на один лучше и начинаем наши собственные, гораздо более сложные последовательности испытаний. При нагрузке до 150 кг штанги прогибаются до 30 мм!
После начала производства мы постоянно тестируем образцы, чтобы улучшить наши подседельные штыри и рули.
Но мы все еще не удовлетворены. Тестовый стенд — это всего лишь тестовый стенд, поэтому мы каждый день вывозим наши вещи на дороги и тропы. Есть две команды MTB Pro, которые катаются на наших запчастях TLO.
Почему вы не красите поверхности деталей?
Поверхности наших деталей не такие блестящие и полированные, как поверхности деталей китайского производства. На это есть причина: мы не красим наши детали.
Краска не делает детали прочнее, но утяжеляет их. В большинстве случаев глянец и так не держится так долго, краска часто бывает довольно чувствительна к царапинам и воздействию химикатов. Наша поверхность из эпоксидной смолы обычно намного прочнее.
Тем не менее, нам нравится, чтобы наши детали выглядели так же красиво, как и окрашенные, благодаря нашему чрезвычайно многолетнему опыту и нашим оптимизированным производственным процессам с использованием зеркально-полированных форм.
Можно ли отремонтировать детали из углеродного волокна?
Как и большинство других высококачественных деталей из алюминия или титана, ремонт обычно неэкономичен. Нам придется сделать рентгеновский снимок детали и проверить ее ультразвуком, что очень дорого и не дает полностью надежного результата.
Нужно ли заменять детали из углеродного волокна после каждой аварии?
В общем, любая авария — серьезный инцидент для вашего руля.Это может окончательно повредить его внутреннюю структуру. В этом отношении углеродные волокна ничем не отличаются от других легких материалов, таких как алюминиевые сплавы.
Для вашей безопасности после аварии следует тщательно проверить все компоненты. В случае сомнений не используйте их, а замените или обратитесь к производителю.
Если на вашем руле наблюдается одно или несколько из следующих признаков, значит, он поврежден:
- Тщательный визуальный осмотр: видимые трещины на руле.
- Приложение нагрузки: тянуть, толкать и поворачивать в разные стороны, закрепив руль на выносе руля.
Если одна сторона заметно слабее другой, значит, она повреждена.
- Приложение нагрузки: Руль издает странный звук под нагрузкой, когда он закреплен на выносе.
Если ваш подседельный штырь выполняет одно или несколько из следующих действий, он наверняка поврежден:
- Тщательный визуальный осмотр: видимые трещины в подседельном штыре.
- Приложение нагрузки: Подседельный штырь можно согнуть в одном направлении больше, чем в другом.
- Приложение нагрузки: Подседельный штырь издает странные звуки.
Имейте в виду, что вышесказанное является рекомендацией, основанной на многолетнем опыте. Тем не менее, мы не можем гарантировать деталь после аварии, даже если ничего из вышеперечисленного не является очевидным. В случае сомнений замените деталь. Ваша безопасность должна быть наивысшим приоритетом!
Будьте осторожны с бывшими в употреблении деталями из углеродного волокна! На самом деле нет возможности проверить, что происходило в его жизни до того, как вы его купили.